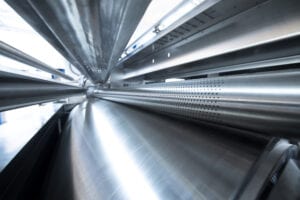
Source: IPCO
Chemical processing and handling equipment manufacturer IPCO Germany GmbH (Fellbach, Germany) is celebrating 40 years continuous production of its market-leading Rotoform granulation system. The development of this innovative rotary dropforming technology in 1980 brought new levels of quality and productivity to the market and changed the face of chemical granulation. A premium quality formed product — one with consistent specifications — enables safer, easier handling during storage and transportation. Such is the quality and reliability of granulation delivered by Rotoform that it has gone on to sell more than 2000 systems to date.
“We had been supplying flaking systems since the early 1950s,” says Johan Sjögren, managing director of IPCO’s Equipment division, “and our ranges now encompass storage and handling solutions, too; but the introduction of Rotoform was a defining moment in our company’s history. It put us on the map in this respect and the system remains the market leader to this day.”
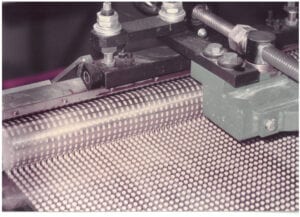
Rotoform in 1983 (Source: IPCO)
While the core principle — direct-from-the-melt solidification on a steel belt cooler — remains unchanged, Rotoform technology has undergone significant advances over the years.
In 2013 the company introduced the 4G (4th Generation) Rotoform, the foundation of an entire family of models designed to meet specific process requirements. These include the granulation of abrasive and sedimenting materials (for example, catalysts and suspensions), melts requiring a high feed temperature (such as bitumen and resins), the pastillation of subcooling melts in supercooling plants (for instance, photo chemicals) and the handling of high viscosity products (such as chocolate, hot melts and resin).
“Rotoform has been a cornerstone of our portfolio for forty years,” says Sjögren. “By continuing to focus on how we can make it better, faster and even easier to maintain, we are confident that it will carry on playing a central role in chemical processing for another 40 years and more.”
The Rotoform consists of a heated cylindrical stator, supplied with molten product via heated pipes and filter, and a perforated rotating shell that turns concentrically around the stator. Drops of the product are deposited by the nozzle bar across the whole operating width of a continuously running stainless steel belt. A system of baffles and internal nozzles built into the stator provides uniform pressure across the whole belt width, providing an even flow through all holes of the perforated rotary shell. This ensures that all granules are of uniform size, from one edge of the belt to the other.
The rotation speed of the Rotoform is synchronized with the speed of the steel cooling belt to allow gentle deposition of the liquid droplets onto the moving belt. Heat released during cooling and solidification is transferred via the steel belt to cooling water sprayed underneath. This water is collected in tanks and returned to the water recooling system; at no stage does it come into contact with the product.
After the drop has been deposited onto the steel belt, any product residue on the outer shell is returned to the Rotoform via a heated refeed bar which keeps the outer shell clean. The product droplets are then discharged as solid, hemispherical granules at the end of the cooling system. To eliminate the possibility of product damage during discharge, a thin film of silicon-based release agent is sprayed onto the steel belt.
This process offers a number of environmental advantages. As the cooling water never comes into direct contact with the chemical, there is no risk of cross contamination. Secondly, solidification takes less than ten seconds, resulting in very low emission values. And low levels of dust levels mean no need for exhaust air treatment.