Precious and rare-earth metals are used in countless consumer products, and advanced processes to efficiently recover these materials from waste present promising alternative sources
Metal is all around us — we drink out of aluminum cans and eat with stainless-steel (or perhaps even silver) silverware. But we may not give much thought to the platinum stored within our vehicles or the europium contained in our smartphone screens. We also may not consider what happens to these materials when they reach the end of their useful life. Potentially valuable product streams can be obtained if the precious and rare-earth metals contained in these products are efficiently recovered. This article will examine some advanced techniques for recycling a variety of consumer products to recover precious metals, as well as the more elusive rare-earth metals.
Treating unique precious metals
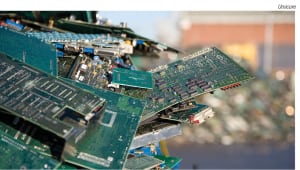
FIGURE 1. Electronics waste — including discarded circuit boards and mobile phones — can contain many valuable materials
Precious metals are crucial in many diverse products and applications, and determining the most efficient recycling processes for each material presents challenges. Umicore N.V. (Brussels, Belgium; www.umicore.com) operates a complex metals-recycling facility in Hoboken, Belgium, that treats approximately 350,000 metric tons per year (m.t./yr) of industrial residues and other recyclable materials, including electronics waste (Figure 1), such as mobile phones and printed circuit boards (PCBs), and automotive and industrial catalysts. The recycling process is unique, says Umicore communications and general services manager Marjolein Scheers, because of the variety of materials handled and recovered — the process recovers 17 different metals, including precious metals, such as gold, silver and the platinum-group metals (PGMs) platinum, palladium and rhodium.
“The operation is designed so that raw materials enter the process at the most optimal step,” explains Scheers. This is determined by the individual material’s physical properties, analytical fingerprint and recovered value. The process begins with a smelter, where precious metals are separated from other metals. The smelter furnace applies a submerged-lance-combustion technology, which involves the injection of oxygen-enriched air into a molten-metal bath. Says Scheers: “Umicore is the only company to apply this technology on such a large scale with such a variety of materials.” Following the smelter are copper-leaching and electrowinning steps, after which the precious metals are collected in a residue that is further processed at an in-house refinery. According to the company, on average, over 95% of the metals contained in the feed can be recovered.
Umicore understands the complexity of recycling waste electrical and electronic equipment (WEEE), and in February of this year, received compliance certification by two European trade organizations (Eurometaux and the European Electronics Recyclers Association) for WEEE recycling. “As the recycling of WEEE wastes consists of various steps, such as collection, pre-processing and end-processing, it is logical that the efficiency and performance of the entire chain is monitored and evaluated,” says Scheers.
PGMs from autocatalysts
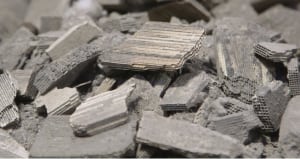
FIGURE 2. Spent automotive catalysts contain valuable precious metals, such as palladium, platinum and rhodium
BASF
One major application for precious PGMs is in the catalytic converters in automobiles. When an automobile has reached the end of its useful life, the PGMs contained within the catalytic converter can be recycled. BASF SE (Ludwigshafen, Germany; www.basf.com) operates three facilities worldwide that recover PGMs (platinum, palladium and rhodium) from spent automobile catalysts (Figure 2) in either ceramic or metallic converter systems. BASF’s process for recovering PGMs from ceramic converter systems is shown in Figure 3. Ceramics represent a larger-volume market than metallic converters, and a recent expansion project at the company’s Cinderford, U.K. site more than doubled the site’s processing capacity for ceramic converters. The upgrades at Cinderford, which went onstream in February of this year, involved the installation of new milling and de-canning equipment.
A variety of factors drives demand for recovered PGMs. The recovered metals are used to supply BASF’s Mobile Emissions Catalysts business, which, says the company, means that they are then used in a new generation of emissions-reduction catalysts. According to BASF, demand for these catalysts has increased in line with automotive production, along with “new and more restrictive automotive emissions regulations around the world.” In addition to the Cinderford location, BASF operates two autocatalyst-recycling facilities in the U.S.The benefits of large-scale PGM recycling are evident, says the company, citing “the lower cost of recycling processes versus other metal sources (mining or open-market purchase), as well as the sustainability and environmental benefits of recovering metals from end-of-life materials that would otherwise end up in landfills.”
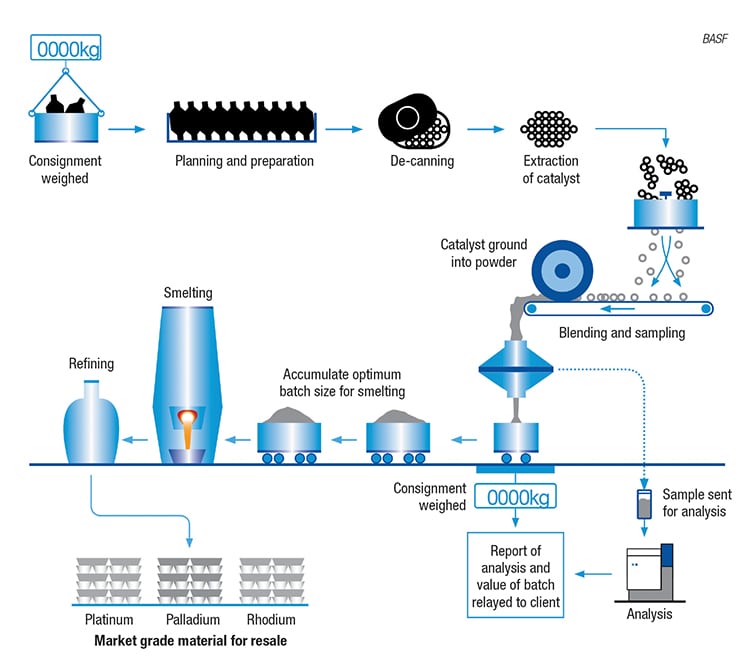
FIGURE 3. Recently expanded at BASF’s Cinderford site, this process recycles platinum-group metals from automotive catalysts for use in new mobile-emissions catalysts
Safer stripping
Electronics components, specifically PCBs, represent a very promising area for the recovery of precious metals, as gold can be stripped from PCBs and recycled. Typical industrial gold-stripping processes utilize cyanide or aqua regia (nitro-hydrochloric acid) solutions. UWin Nanotech Co. (New Taipei City, Taiwan; www.uwin-nano.com) has recently patented what is said to be more environmentally friendly, less toxic gold-stripping chemicals — UW-700 (sulfide solution) and UW-860 (citrate solution). “Aqua regia is a highly corrosive solution, and cyanide is a very toxic solution,” UWin managing director Kenny Hsu explains, “whereas UW-700 is a neutral gold-stripping solution, and is also highly selective.” For UW-860, Hsu elaborates, saying that the solution “is different from aqua regia because it doesn’t damage the plastic, ceramic, silicon, titanium or stainless-steel substrate.”
After treatment with UW-700, the gold is completely stripped from the PCB, while the remaining materials are left intact (Figure 4). The recovered gold is isolated and can be re-sold for use in optical-electrical, plating and decorative applications. According to the company, applying this technology to 1 m.t. of PCB waste from cellular phones can result in the extraction of 400 g of gold.
Using these chemicals, the company has developed modular, automatic gold-stripping machines (Figure 5), which have deployed commercially worldwide, including locations in Taiwan and Texas. The company is also collaborating with a mechanical manufacturer to develop new types of stripping machines. UWin has also developed technologies for selective stripping of other precious metals, including silver, palladium and indium. In January 2015, the company released UW-195, a cyanide-free platinum-stripping agent that is compatible with stainless-steel, plastic or ceramic substrates.
Rare-earth metals
Compared to their precious-metal counterparts, and despite a growing demand, commercial recycling and recovery techniques remain elusive for the 17 rare-earth metals (REMs). China, in recent years, has become the world’s most significant source of REMs, but recent regulatory changes may lead to a global shortage, forcing manufacturers to seek new methods to obtain REMs, including recycling.
“Rare-earth elements really are not scarce in the world. You may find some of them in your own backyard,” explains Eric Peterson of the Idaho National Laboratory (INL; Idaho Falls, Idaho; www.inl.gov). “However, it is rare to find them in locations where they occur in reasonably high concentrations that allow for economical mining of the materials.”
INL is part of the Critical Materials Institute (CMI; www.cmi.ameslab.gov), an Energy Innovation Hub sponsored by the U.S. Dept. of Energy through the Advanced Manufacturing Office. Comprised of national laboratories, universities and companies at the forefront of REM research, CMI brings a four-tiered approach to tackling advanced rare-earth projects, focusing on the development of more efficient separations, recovery and recycling processes, and alternative materials that can potentially serve as REM substitutes, as well as bringing end-of-life awareness to manufacturers whose products utilize rare-earth metals.
While commercial technologies do exist for recovering REMs, these processes have some shortcomings. “There are many technological approaches that may make it possible to recover and recycle the elements,” says Peterson. “However, due to the specific chemistries of each of the rare-earth elements, it is necessary to develop approaches to recycle the elements independently.” Current commercial technologies may result in complex mixtures, which require further purification before yielding a usable product. The economy of these technologies is also highly dependent on the market value for the recovered metals, as in the case of recycling cerium from automotive catalysts or fluidized catalytic cracking (FCC) catalysts.
CMI is developing a number of processes for recovering REMs from various sources, including electronics waste, phosphor powders from fluorescent lighting and LEDs and permanent magnets from computer disc drives and wind turbines. “Phosphors are moving very quickly to the commercial scale,” says Peterson of CMI’s phosphor-recovery projects, which target fluorescent lamps as the source of phosphor powder. Phosphor powder can contain 5–25% by weight rare-earth elements, such as europium or terbium, in a cerium-, yttrium- or lanthanum-phosphate matrix.
In one CMI project, a supercritical-fluids process selectively extracts rare-earth metals from the phosphor powders, which also contain mercury. “The economics of the process are aided by the recovery and isolation of the mercury that is also contained in the phosphor powder, plus the recovery of the glass, aluminum and steel,” INL’s Peterson explains. In another project, CMI’s main focus is concentrating the rare-earth oxides (REOs) in phosphor dust and separating out the non-REO materials via hydrometallurgical methods.
Perhaps the most promising REM-recovery process CMI has developed involves membrane solvent extraction. CMI has demonstrated and is licensing the process, and expects to see full-scale realization of the project in 2.5 years. This extraction process sets itself apart from other rare-earth recovery techniques in that a more dilute stream can be used for extraction. A dispersion-free, supported, liquid-membrane solvent-extraction process separates and recovers REMs, such as yttrium, europium, praseodymium and neodymium, from permanent magnets and halophosphate phosphors. Operating under non-equilibrium conditions, the extraction process overcomes the stability issues arising due to the gradual loss of extractant in normal solvent-extraction processes. Other REM-recovery projects in development at CMI include recovery of indium and REOs from thin-film plasma display panels, recovery of overspray from coating processes, bioleaching using microorganisms and biosorption in an aqueous solution.
Since most of their processes utilize components of discarded consumer products, CMI recognizes that the ability to readily recover and recycle REMs begins with the initial manufacture of the product. Involving manufacturers, and emphasizing the importance of end-of-life considerations in manufacturing processes, eases the complexities of recycling these materials. For instance, if disc drives are manufactured so that the magnets are easily removable, recycling the REMs contained within becomes a much less labor-intensive task. This will benefit the manufacturers, as well, through the increased availability of recycled REMs, while decreasing the dependence on virgin materials.
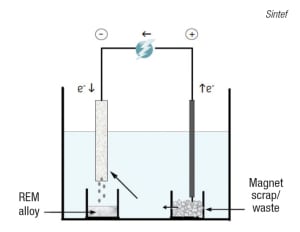
FIGURE 6. Rare-earth metals contained in permanent magnets can be recovered via high-temperature electrolysis
Another group working to develop recycling processes for REMs is Sintef (Trondheim, Norway; www.sintef.no), as part of the “Value from Waste” consortium formed by various European research and technology organizations. Sintef’s work has targeted two main sources for REM recovery — nickel metal-hydride (NiMH) batteries and permanent magnets that contain neodymium (Nd) — focusing mainly on the use of high-temperature electrolysis for the direct extraction of REM alloys from magnets. Says Sintef senior research scientist Ana Maria Martinez, “This can be considered a direct electro-refining process, as it allows the extraction of a rare-earth alloy that can be used in the manufacture of new permanent magnets directly from the waste material.” Figure 6 shows a simplified model of the magnet-recycling process, which begins with the scrap material being placed into an anode compartment. Here, the REMs present in the magnets (typically Nd, but also dysprosium, praseodymium or terbium) are anodically dissolved in the form of rare-earth ions, which will deposit at the cathode as rare-earth alloys. Other elements present (such as transition metals) will remain at the anode as sludge.
“At the moment, the high-temperature electrolysis approach has only been applied in the case of Nd-based permanent magnets,” comments Martinez, “but the method could be suited to any conductive rare-earth-containing material.” The technology was recently submitted to the European Commission to receive economic support for demonstration in industrial environments. In addition to end-of-life Nd-containing magnets, the recycling process can be supplemented with the use of scrap from the manufacture of new magnets. According to Martinez, “This is seen as the most practical solution to start operating recycling plants effectively.”
Sintef’s process for recovering REMs from NiMH batteries involves pyrometallurgical refining. “This high-temperature approach is able to completely separate the valuable nickel-based alloys and REO concentrates from the negative electrodes of NiMH batteries,” says Martinez. The output material is subsequently fed into a high-temperature electrolysis process to produce a mixture of REMs, which can be used in new battery electrodes. As with Sintef’s magnet-recycling process, the next steps will be to extrapolate these technologies to other REM-containing waste streams.
Like CMI, Sintef recognizes the challenges associated with rare-earth recycling, emphasizing the importance of implementing efficient systems for obtaining usable REM-containing scrap. “The process of separating and collecting the magnets safely from end-of-life products not only requires a great deal of time and effort, but also uses acids and other chemicals,” says Martinez. “This results in toxic liquid wastes, the disposal of which creates environmental and cost issues.” Once again, attention is brought to the limitations that initial manufacturing considerations can put on recycling.
Commercial future
On the commercial front, some companies are developing REM-recycling processes. In France, Solvay S.A. (Brussels, Belgium; www.solvay.com) has demonstrated a process for recycling phosphor powders (containing lanthanum, cerium, terbium, yttrium, europium and gadolinium) from fluorescent light bulbs and lamps. At the company’s St. Fons site, the phosphor powders are separated from glass and other components and suspended in an aqueous solution. In solution, the phosphor powders undergo a chemical reaction, further concentrating the REMs. After separating out the liquid and drying, the remaining REM-concentrate powder is then sent to another site, La Rochelle, which specializes in rare-earth purification.
At the 2014 Minerals, Metals and Materials Society Annual Meeting & Exhibition, Hitachi Ltd., (Tokyo, Japan; www.hitachi.com), through the company’s Yokohama Research Laboratory, announced a recycling process for permanent magnets that includes steps for the disassembly of scrap products, followed by pyrometallurgical recovery of neodymium and dysprosium using molten magnesium as an extraction medium. It was reported that the company can process several kilograms of magnets per day using this technology.
Mining companies, as well, are acknowledging the importance of REM conservation, and are looking into technologies to recover and recycle REMs from mining waste. In March of this year, Ucore Rare Metals Inc. (Bedford, Nova Scotia, Canada; www.ucore.com) secured exclusive rights to advanced molecular-recognition technology that can be used for REM separation and recycling. According to the company, this technology can recover more than 99% of the REM content in a stream. In February, Pele Mountain Resources (Toronto, Ont., Canada; www.pelemountain.com) announced a plan for the dedicated recycling of the REM-containing mineral monazite, from which neodymium and praseodymium, along with smaller amounts of other REMs, can be produced.
It seems that across the board, from miners to electronics manufacturers to consumers, the importance of conserving rare-earth materials, as well as precious metals, is clear. Although recycling processes for REMs have not yet reached the level of efficiency and commercial feasibility of other metals-recycling techniques, the great deal of development work in the area is certainly promising. ■
Mary Page Bailey