Online monitoring of steam and water chemistry in a steam system is important for safe and reliable operation of steam generators
High-pressure, high-temperature steam is a critical commodity at power plants and at many chemical process industries (CPI) facilities. Examples abound in heavy industry, where co-generation facilities are common. In these plants, a portion of the steam generated is utilized to drive power-generating turbines, while the remainder is used for other turbine applications or for process heating needs. For instance, in the steel-manufacturing industry, steam-driven turbines serve as the prime mover for the air feed to blast furnaces.
In facilities where steam is generated, it is not uncommon for the control and monitoring of water and steam chemistry to be neglected because intense attention is focused on process operations. Only when a failure occurs is action taken in the area of water/steam chemistry.
In decades past, when conventional coal-fired power generation was the norm, numerous lessons were learned that emphasized the criticality of water- and steam-chemistry monitoring. Many of these lessons were quite dramatic, and, when ignored, underlined the possibility of not only lost production and equipment repair at the facility, but sometimes injuries and fatalities. To avoid such negative occurances, continuous online chemistry monitoring became commonplace at most plants. Now, for both power and industrial-plant steam production, heat recovery steam generators (HRSGs) are a common choice. Unfortunately, a large number of these plants are minimally staffed, often with few, if any, employees that have a strong background in water and steam chemistry. Often, lessons of the past are not considered, leading to a twist on the old saying, “Those who do not understand history are condemned to repeat it.” This article reviews the importance of water and steam chemistry for reliable and safe operation in industrial steam systems, and outlines recommended water-monitoring parameters.
HRSG design: a brief review
High-purity water requirements and water/steam chemistry control and monitoring for HRSGs are similar to those for older, conventional steam generators. However, as compared to coal-fired units, there are some obvious major differences in HRSG design and operation, the most important of which include the following:
- The various waterwall tube and superheat/reheat panels (also known as harps) are aligned in sections along the fluegas path. The waterwall tubes in a coal unit basically form the walls (hence the name waterwall) of a box that surrounds the combustion chamber
- Essentially no ash-fouling potential exists unless the combustion turbine is fired with oil, which is not common
- HRSGs are typically of multi-pressure design, with the most popular having three steam-generating networks (that is, evaporators)
- The common term for the boilers in an HRSG is “evaporator,” which will appear throughout the remainder of this article
Sampling points and monitoring
Within a steam-generating network, the samples that are of primary importance for online monitoring of the water/steam chemistry include the following:
- Makeup treatment system
- Condensate pump discharge
- Condensate return (when applicable)
- Feedwater or economizer inlet
- Boiler water
- Saturated steam
- Main and reheat steam
Makeup treatment system. No system is completely closed, and even in the tightest steam generators, a small amount of process water/steam continually escapes. These losses must be made up with high-purity water. The makeup water volume can be quite large if condensate from steam utilized for process heating is not returned to the unit(s). The most common core process is reverse osmosis (RO), followed by either mixed-bed ion exchange (MBIX) or electrodeionization (EDI) to “polish” the RO effluent, especially for high-pressure steam generators. RO units typically include a number of instruments to monitor system performance, including pressure, temperature, flow and specific conductivity. This section focuses upon the recommended analyses of the final effluent from either the MBIX or EDI polisher.
In this and the following sections, the normal upper limit, or a range, for each parameter is included.
- Specific conductivity: ≤0.1µS/cm
- Silica content: ≤10 parts per billion (ppb)
- Sodium concentration: ≤2 ppb
These measurements ensure that high-purity water is being distributed to the steam generators. A rise in any of the values indicates that either the MBIX resin has reached exhaustion or that a problem has occurred in the EDI unit. Prompt corrective action is necessary in this case.
Condensate pump discharge (CPD). In stand-alone steam-generation power units, the primary location for potential contaminant ingress is the condenser, and particularly water-cooled condensers where a tube leak(s) allows cooling water to infiltrate the high-purity condensate. A tube leak will introduce a variety of impurities, including the hardness ions (Mg2+ and Ca2+), chloride and sulfate, and silica, which when subjected to the harsh environment in the steam generator, can cause serious problems. This will be examined in a later section. A condensate polisher will provide a buffer against contaminant ingress, but polishers are often not considered for drum units, in large measure to reduce project capital cost.
Recommended continuous CPD analyses results are as follows:
- Cation conductivity (CACE): ≤0.2µS/cm
- Specific conductivity: Consistent with pH
- Sodium concentration: ≤2 ppb
- Dissolved oxygen: ≤20 ppb
- pH: 9.6 to 10.0 (This is the pH range for the HRSG design in Figure 1. The range may be a bit lower for other HRSG designs.)
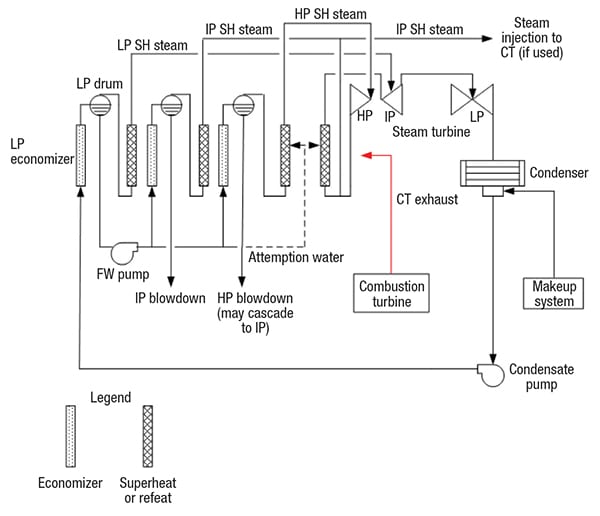
Figure 1. The diagram shows the basic flow path of the most common type of HRSG — the design known as the “feed forward low-pressure (FFLP)”
Sodium monitoring is very effective for detecting condenser tube leaks or perhaps issues related to contaminated condensate return from heating processes. With a tight condenser, sodium ion levels in the condensate are normally very low (
Cation conductivity is now often referred to as “conductivity after cation exchange (CACE)” to represent the fact that the sample is routed through a cation exchange column to replace all cations (for example, ammonium, sodium, calcium, and so on) with hydrogen ions. This creates a very dilute acid solution of primarily trace amounts of chloride and sulfate ions, whose conductivity is then measured. As with sodium, a rise in CACE indicates impurity in-leakage, although this measurement is also influenced by carbon dioxide ingression, say from increased air in-leakage at the condenser. Thus, becoming increasingly popular is degasified CACE, which utilizes either a re-boiler or nitrogen sparging compartment to remove CO2. A low CACE value is a requirement for proper control of all-volatile oxidizing treatment [AVT(O)] chemistry (an offshoot of oxygenated treatment), which is recommended for condensate/feedwater treatment to minimize flow-accelerated corrosion (FAC), and whose details are outlined shortly.
Dissolved oxygen analyses are important for monitoring condenser air in-leakage. A sudden increase in dissolved oxygen may indicate a mechanical failure at or near the condenser, which allows excess air to enter the system. However, with modern AVT(O) chemistry, some dissolved oxygen is required for the chemistry to be effective.
With regard to specific conductivity and pH, ammonia (or sometimes an amine or ammonia/amine blend) is the pH-conditioning agent for condensate/feedwater. However, direct pH measurement of high-purity water can be tricky, and algorithms have been developed to calculate pH based on conductivity measurements to provide more accurate results. Specific conductivity (S.C.) in high-purity water is directly correlated to the ammonia concentration, and thus S.C. measurements offer better control of ammonia feed than pH.
A parameter not typically monitored continuously, but which can be of major importance, is total organic carbon (TOC), as discussed in the next section. For utility steam generators, the normal TOC limit in this sample is 100 ppb.
Condensate return. Steam recovered as condensate from process heat exchangers represents a potentially large source of impurities, which, depending upon the processes and products of the facility, can be inorganic or organic in nature, or may be of particulate form, such as iron oxides. Contaminant ingress from condensate return can be very problematic. For example, the author once visited an organic chemical production plant where substantial organic transport in the condensate return caused drum foaming and subsequent reoccurring failures of the superheat sections of four, 550-psig steam boilers. Tests by the company’s water-treatment vendor at the time indicated TOC excursions above 100 parts per million (ppm). The recommended TOC limit for boilers of this pressure is 0.5 ppm. The plant had no condensate polisher on the return line, and no one on staff who understood this chemistry.
For high-pressure steam generators, the condensate return system should have water purity equivalent to the parameters outlined above for the CPD.
Low-pressure (LP) economizer inlet/boiler feed pump discharge.The dominant issue with regard to chemistry control in the HRSG feedwater system (and LP evaporator, as will be discussed) is the minimization of flow-accelerated corrosion (FAC). When the author began his utility career in 1981, conventional wisdom said that any dissolved oxygen that entered the condensate/feedwater system of utility boilers was harmful. At that time, over 50% of the electric power produced in the U.S. came from coal. Coal units typically have complex condensate/feedwater networks with numerous feedwater heaters. A common material for feedwater heater tubes was some type of copper alloy, usually either Admiralty brass or 90%/10% copper-nickel. The prevalent thinking was that any trace of dissolved oxygen (DO) would cause corrosion, and indeed DO can be very corrosive to copper, and to carbon steel in uncontrolled conditions. Therefore, virtually all feedwater systems for high-pressure steam generators were equipped with a deaerator for dissolved gas removal. A properly operating deaerator can lower DO concentrations to 7 ppb.
However, even this residual DO concentration was still considered harmful, so chemical deaeration was also employed at most plants. The chemical of choice for many years was hydrazine (N2H4), a reducing agent (also known as an oxygen scavenger), which reacts with oxygen as follows:
N2H4 + O2 —> 2H2O + N2 (gas)
Hydrazine proved advantageous because it does not add any dissolved solids to the feedwater, it reacts with oxygen in a one-to-one weight ratio, and it is supplied in liquid form at 35% concentration. The primary benefit of hydrazine is that it will passivate oxidized areas of piping and tube materials.
Hydrazine residuals of 20 to perhaps 100 ppb were common. Reducing agent treatment was coupled with feed of ammonia or an amine to maintain feedwater pH within a mildly alkaline range, 8.8 to 9.1 for mixed-metallurgy feedwater systems and a bit higher for all-ferrous (carbon-steel- and stainless-steel-only) systems.
NH3 + H2O —> NH4+ + OH–
The use of ammonia (or a neutralizing amine) combined with a reducing agent/oxygen scavenger is the basis of the program known as all-volatile treatment reducing [AVT(R)].
Due to the suspected carcinogenic nature of hydrazine, alternative reducing agents, such as carbohydrazide, methyl ethyl ketoxime, and others, gained popularity. All still had the same purpose — to establish a reducing environment in the feedwater circuit, thus inhibiting oxidation of metal. AVT(R) became a standard in the industry.
“This changed in 1986. On December 9 of that year, an elbow in the condensate system ruptured at the Surry Nuclear Power Station [near Rushmere, Va.]. The failure caused four fatalities and tens of millions of dollars in repair costs and lost revenues” [1]. Researchers learned from this accident and others that the reducing environment produced by oxygen scavenger feed results in single-phase flow-accelerated corrosion (FAC). The attack occurs at flow disturbances, such as at elbows in feedwater piping and economizers, feedwater heater drains, locations downstream of valves and reducing fittings, attemperator piping, and, most notably for the combined-cycle industry, in low-pressure economizers and evaporators, and to a lesser (but still important) extent, in intermediate-pressure circuits.
The effect of single-phase FAC is shown in Figure 2. Wall thinning occurs gradually until the remaining material at the affected location can no longer withstand the process pressure, whereupon catastrophic failure occurs (Figure 3).
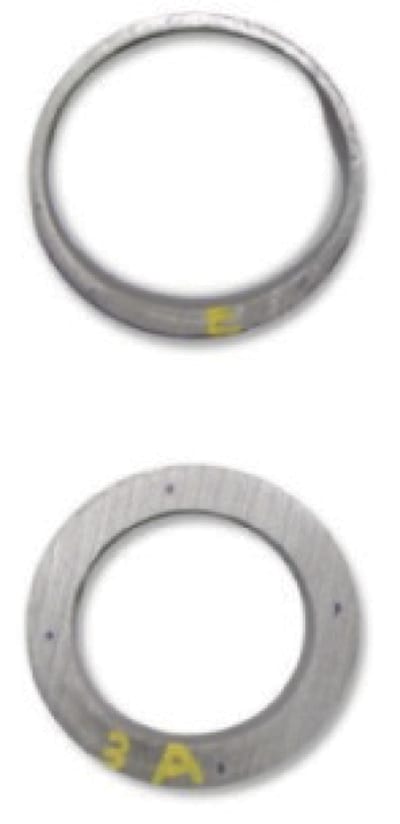
Figure 2. Tube-wall thinning is caused by single-phase flow-accelerated corrosion
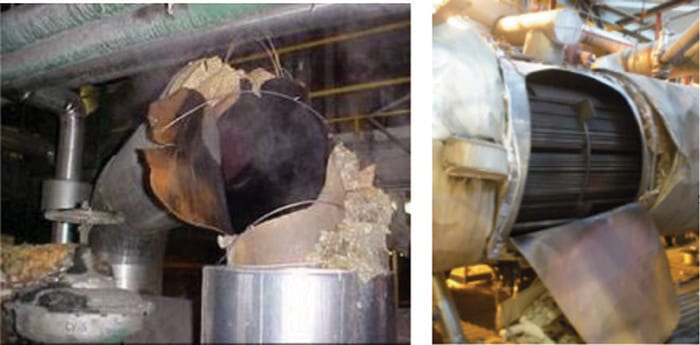
Figure 3. The photos show two examples of catastrophic failures induced by flow-accelerated corrosion (source: Ref. 2)
Two additional factors, pH and temperature, also strongly influence single-phase FAC (Figure 4). As this figure illustrates, corrosion reaches a maximum at 300˚F. Thus, feedwater systems, attemperator lines, HRSG LP economizers and evaporators, and to some extent HRSG intermediate pressure (IP) circuits are particularly susceptible locations. Also note the substantial influence of pH on the corrosion characteristics.
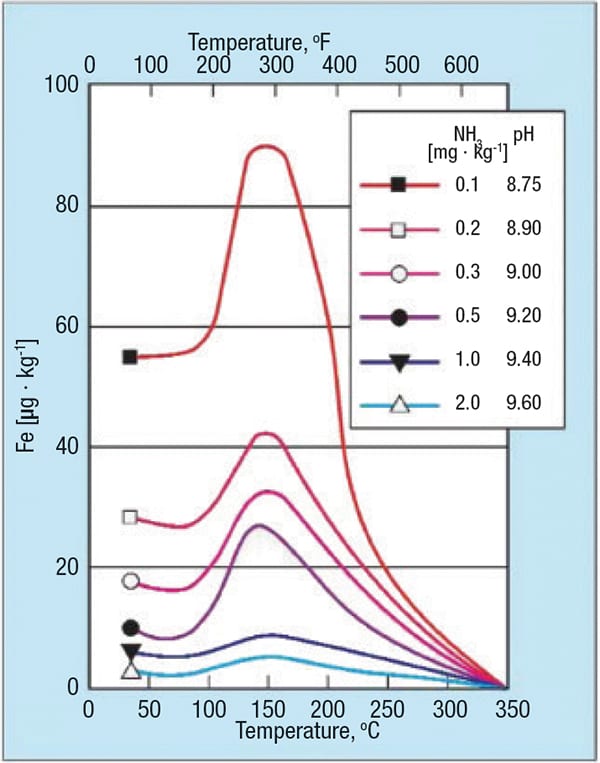
Figure 4. The graph shows carbon-steel matrix dissolution as a function of pH and temperature (source: Ref. 2)
An important point highlighted by the graph (and which is a key point of later discussion), is that with proper chemistry, feedwater iron concentrations can be maintained at levels below 2 ppb. Higher concentrations indicate that FAC is in progress somewhere in the system. HRSGs, by their very nature, typically have many short-radius economizer and evaporator elbows, and thus offer many locations for single-phase FAC.
Solutions to single-phase FAC
Nearly a half century ago, researchers and chemists in Germany and Russia began using a program known as oxygenated treatment (OT) to minimize carbon-steel corrosion and iron dissolution in supercritical steam generators. The key component of the program was, and still is, deliberate injection of pure oxygen into the condensate/feedwater network to establish oxygen residuals of up to 300 ppb. What the chemists discovered is that in very pure feedwater (cation conductivity ≤ 0.15µS), the oxygen will intersperse and overlay magnetite to generate a tenacious and very insoluble film of ferric oxide hydrate (FeOOH). OT typically lowered feedwater iron concentrations to 1 ppb or less, and greatly minimized single-phase FAC. Now, OT is the preferred feedwater treatment for most once-through utility steam generators around the world, unless the feedwater heaters have copper alloy tubes.
Although OT has been successfully applied to drum boilers, the Electric Power Research Institute (EPRI) developed what is known as the all-volatile treatment oxidizing [AVT(O)] program, which is the most common treatment for condensate/feedwater in drum units. AVT(O) relies on the oxygen that enters condensate via condenser air in-leakage, although supplementary oxygen feed may be necessary. When researchers developed AVT(O), they took into account the pH effect on carbon-steel dissolution. Depending upon the HRSG design, the recommended feedwater pH may range from 9.2 to 10.0. Other AVT(O) guidelines are as follows:
- Feedwater DO: 5–10 ppb
- Feedwater cation conductivity limit: ≤ 0.2µS/cm.
High-purity water is a requirement, because otherwise, substantial oxygen corrosion would result. When properly applied, the initial gray-black magnetite (Fe3O4) layer becomes interspersed and overlayed with more protective FeOOH, which produces the “rugged red” color shown in Figure 5.
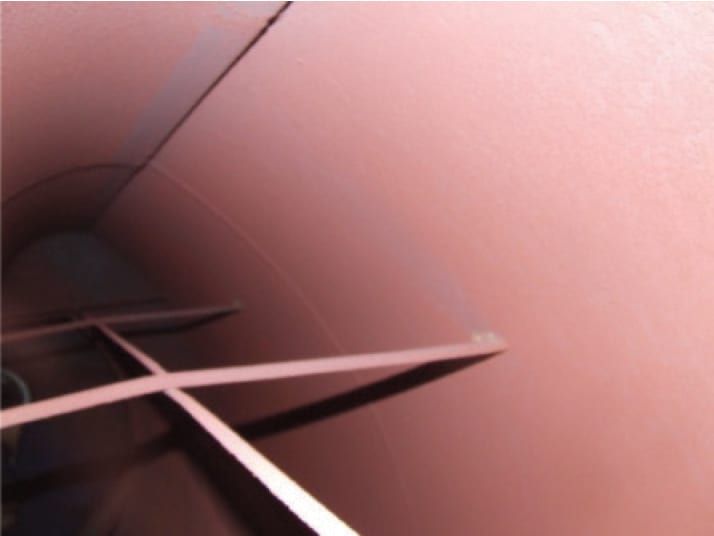
Figure 5. The photo shows the red coloration of a properly applied AVT(O) program (photo courtesy of Dan Dixon, Lincoln Electric System)
A critical idea that combined-cycle owners, operators and technical personnel must be aware of is that very rarely, if ever, do the condensate/feedwater systems of HRSGs have any copper alloys within the network. (Copper-alloy condenser tubes are a non-issue with regard to this discussion.) Therefore, no reason exists to employ AVT(R) chemistry; rather AVT(O) should be the choice.
The following parameters are recommended for feedwater chemistry to high-pressure steam generators:
- CACE: ≤0.2µS/cm
- S.C.: Consistent with pH
- Sodium: ≤2 ppb
- Dissolved oxygen: 5–10 ppb
- pH: 9.6 to 10.0 (This is the pH range for the HRSG design shown in Figure 1. The range may be a bit lower for other HRSG designs.)
- Iron: ≤2 ppb
The discussion for CACE, S.C., pH, and sodium mirrors that for the condensate pump discharge. These measurements, along with dissolved oxygen, are critical for proper AVT(O) chemistry.
The reader will note the inclusion of iron in this list. Iron monitoring provides a direct measurement of FAC (or hopefully lack thereof) and the effectiveness of the feedwater chemistry program. Typically, 90% or greater of iron corrosion products generated by FAC are particulate in nature. Several methods exist to monitor carbon-steel corrosion, and include the following:
- Continuous particulate-matter monitoring
- Corrosion product sampling
- Grab sample analysis
With regard to the latter, improved grab sampling techniques are available, in which, with proper sample treatment, iron measurements down to 1 ppb are possible. This method can provide near-realtime data for corrosion rates, although on a “snapshot” basis (Figure 6).
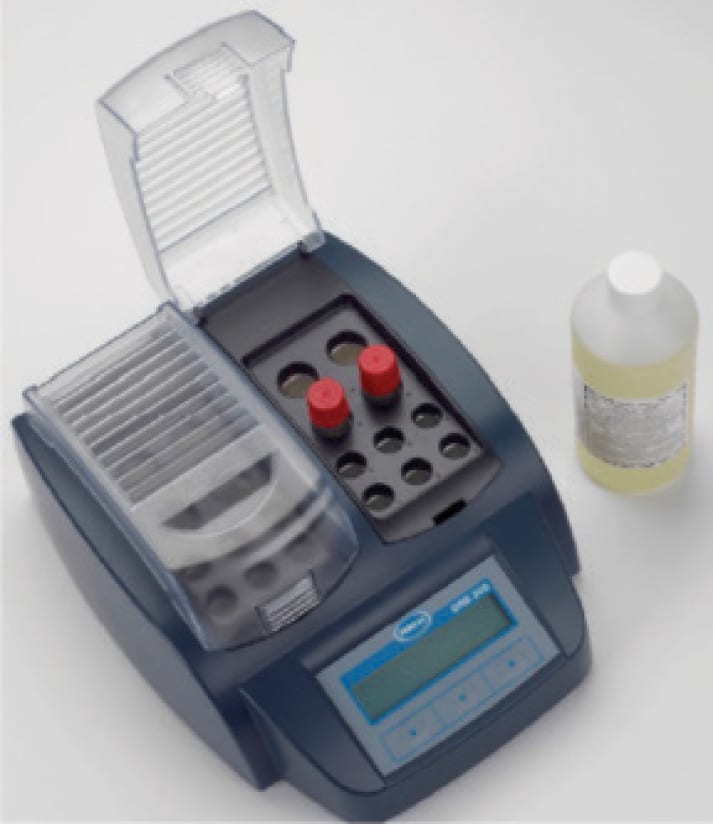
Figure 6. This instrument is a iron digestion unit and spectrophotometer (photo courtesy of Hach)
Evaporator water
Evaporator water sampling is critical for two primary reasons. First, poor chemistry control or poor monitoring (or both) can allow unacceptable carryover of excess impurities to the steam. The second reason is that the highest heat fluxes occur within the evaporators (as is the same with conventional units) and particularly the HP evaporator of HRSGs. Thus, the effects of impurity ingress or poor chemistry are magnified by the high temperatures and pressures in these circuits. Consider the classic, longstanding issue of hydrogen damage, which has plagued high-pressure units for decades.
In this mechanism, the most serious corrosive agent (chloride) that enters during a cooling leak can concentrate under waterwall tube deposits and generate acid. The following equation outlines a common mechanism for this process:
MgCl2 + 2H2O + heat —> Mg(OH)2 (solid) + 2HCl
Acid generation is problematic in its own right, but the very small hydrogen atoms will penetrate the steel matrix and then react with carbon in the steel.
4H + C —> CH4
Formation of voluminous methane molecules induces cracking, which can then induce failures with very little metal loss (Figure 7).
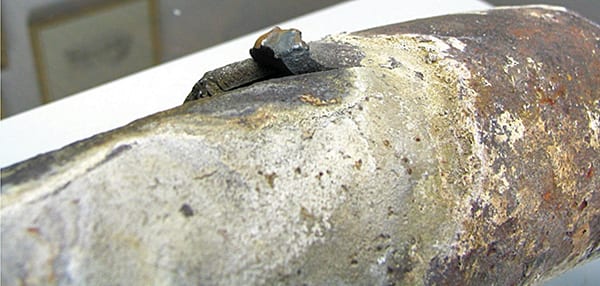
Figure 7. The photo shows a pipe with hydrogen damage. Notice the thick-lipped failure, showing little metal loss
The author once observed the after-effects of severe hydrogen damage on a 1,250 psig boiler, which required complete replacement of the waterwall tubes. Hydrogen damage remains one of the leading corrosion mechanisms in modern steam generators, and is why, as the guidelines below indicate, immediate unit shutdown is required if the boiler water pH drops below 8.0.
Recommended boiler water analyses results include:
- pH (
- CACE
- Specific conductivity
- Chloride
- Silica
- Phosphate (for those units on phosphate treatment)
- Iron:
The reader will notice no direct limits for most parameters, with the exception of a “drop-dead” lower limit for pH. This is due to the fact that the limits are variable based on boiler pressure. EPRI has published detailed charts for these parameters, but they are only directly available to EPRI members. Other guidelines are available from the International Association of the Properties of Water and Steam (IAPWS; www.iapws.org) at no charge.
Also notice the limit for iron. The LP circuits and some intermediate-pressure (IP) locations in an HRSG can suffer from a phenomenon known as two-phase FAC. Space limitations prevent a discussion of this mechanism here, but iron monitoring is important to ensure that proper chemistry is being maintained in these circuits.
Comment is necessary regarding phosphate. For decades, tri-sodium phosphate (Na3PO4) has been a core boiler-water-treatment chemical in many drum units. However, control of the phosphate concentration is difficult due to the compound’s reverse solubility above 300˚F. Some plant personnel, especially in the power industry, have switched to a caustic (NaOH) feed to eliminate phosphate “hideout,” but great care is required with these programs to prevent caustic gouging of waterwall tubes. Similar in some respects to the acid corrosion described earlier, caustic can concentrate under porous deposits (usually iron oxide corrosion products that carry over from feedwater or condensate return systems) to directly attack the metal. Inclusion of a condensate polisher in the system design offers the opportunity to eliminate phosphate or caustic from the boiler-water-treatment program.
Steam purity
Steam-purity measurements are very important, and particularly if the steam drives a turbine or turbines. Contaminant deposition on turbine blades can lead to corrosion and possible blade failures, which represent a potentially catastrophic situation with the turbine spinning at several thousand revolutions per minute. Core monitoring parameters include the following:
- CACE: ≤0.2µS/cm
- Sodium: ≤2 ppb
- Silica: ≤10 ppb
Sodium provides a direct indication of salt or sodium hydroxide carryover with the steam. Salts, and particularly chloride salts, will settle in the last rows of the low-pressure turbine, where they can cause pitting and subsequent stress corrosion cracking (SCC) and corrosion fatigue (CF) of turbine blades and rotors. Sodium hydroxide carryover is a very serious issue, because caustic can quickly induce SCC of turbine components.
CACE provides a surrogate measurement of chloride and sulfate carryover, and has been a long-time guideline for turbine manufacturers. However, the accuracy of CACE is suspect, especially given that the limit for both impurities is 2 ppb, similar to sodium. A new instrument has emerged on the market that allows analyses of these two impurities down to a 0.1 ppb level (Figure 8).
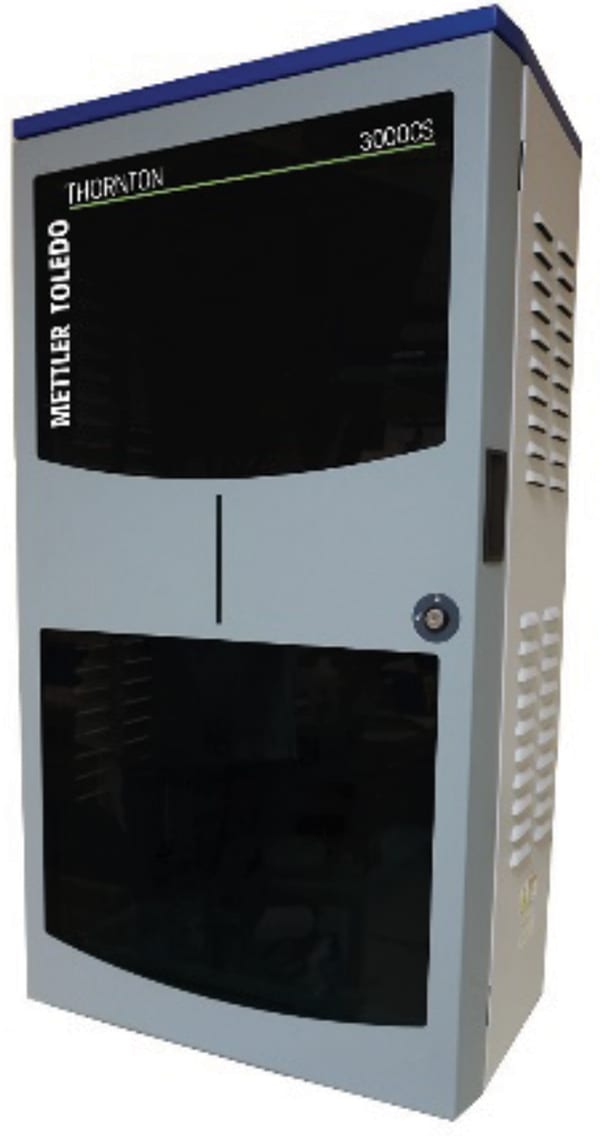
Figure 8. Chloride/sulfate analyzer separates ions in the sample via capillary electrophoresis
It has long been known that silica in steam will precipitate on turbine blades. While the compound is not corrosive, it can influence turbine aerodynamics and reduce efficiency. Thus, the 10-ppb recommended limit.
Several steam sampling points are available in power generating units. These include saturated, main and reheat steam samples. Main and reheat steam are the most important, as they provide data on impurities directly entering the turbine, which can also come from contaminated steam attemperation water. Measurement of saturated steam is less important, but can be valuable on a periodic basis to check for mechanical carryover issues from steam drums. Failed or damaged steam separators are a common cause of mechanical carryover.
Smart systems
Organizations such as EPRI have been performing much work in the development of “smart systems” that integrate instrument data into outputs that provide information on overall steam-generation chemistry. For example, if an HRSG is equipped with both CPD and feedwater sodium and CACE analyzers, and only one is giving high readings, instrument error is the likely culprit. However, if all four are out of normal range, contamination from a condenser tube leak or makeup system upset is the likely cause. This can be narrowed further by comparing CPD readings with makeup system effluent values. Numerous other integrated evaluations are possible, and use of a program that examines all data and provides intelligent outputs to plant operators and technical personnel can be extremely valuable in identifying specific upsets before they become major problems. For instance, the makeup water system at a CPI facility may be fine, and all turbine condensers are in good order, but a leak in a process heat exchanger may be fouling the condensate return. With the proper instrumentation in place, a smart system will quickly analyze the issue and alert the plant staff. This article has outlined fundamental guidelines, but each system is different and therefore, consultation with a water treatment expert is recommended to address the details of your system.
Edited by Scott Jenkins
References
1. Cycle Chemistry Guidelines for Combined-Cycle/Heat Recovery Steam Generators (HRSGs), EPRI, Palo Alto, Calif.: 2006. 1010438. Note: EPRI published an updated version of this document in 2013.
2. Buecker, B. and Shulder, S., “Power Plant Cycle Chemistry Fundamentals”; pre-conference seminar to the 35th Annual Electric Utility Chemistry Workshop, June 2, 2015, Champaign, Ill.
Author
Brad Buecker is the senior technical publicist with ChemTreat, Inc. (5460 Cox Road, Glen Allen, VA 23060; Phone: 1-804-935-2000; Email: [email protected]). He has 36 years of experience in or affiliated with the power industry, much of it in steam generation chemistry, water treatment, air quality control, and results-engineering positions with City Water, Light & Power (Springfield, Illinois) and Kansas City Power & Light Company’s La Cygne, Kansas station. He also spent two years as acting water/wastewater supervisor at a chemical plant. Most recently, he was a technical specialist with Kiewit Engineering Group Inc. Buecker has a bachelor’s degree in chemistry from Iowa State University, with additional course work in fluid mechanics, energy and materials balances, and advanced inorganic chemistry. He is a member of the American Chemical Society, American Institute of Chemical Engineers, American Society of Mechanical Engineers, Association of Iron and Steel Technology, Cooling Technology Institute (via corporate membership), National Association of Corrosion Engineers, the Electric Utility Chemistry Workshop planning committee, the Advisory Council for the International Water Conference, the EPRI-sponsored Power Plant & Environmental Chemistry Committee, and the Power-Gen International planning committee. Buecker has authored many articles and three books on power plant and water/steam chemistry topics.