There are many technologies used in industry to protect workers from toxic gases. Here are some guidelines for selecting one that will match your application
The dual threat of toxicity and combustibility applies to a number of industrial gas hazards. When such gases go undetected, they can lead to catastrophic accidents with the potential to injure or kill employees and damage or destroy plant equipment. Ammonia is one of those potentially double-trouble hazards, especially in its most common usages as a refrigerant or fertilizer product. It can be found as a chiller or refrigerant in the food and beverage industry, pharmaceutical production, in air-conditioning equipment, in electric power generation plants and, of course, fertilizer production. Understanding the proper precautions to take with ammonia provides a highly useful model or example of what is required when protecting people, equipment and plants against the threats of many other toxic and combustible gases. In general, those responsible for plant processes and safety need to understand the health threat and symptoms of exposure to any toxic gas, the nature of any toxic or combustible gas (how it behaves in a plant setting) and the gas detection sensing technologies available. The article explains the advantages and limitations of gas detection technologies, as well as their maintenance requirements.
Understanding the gas
According to the U.S. Occupational Safety & Health Administration (OSHA; Washington, D.C.; www.osha.gov): “Ammonia is considered a high health hazard because it is corrosive to the skin, eyes and lungs. Exposure to 300 parts per million (ppm) is immediately dangerous to life and health. Ammonia is also flammable at concentrations of approximately 15 to 28% by volume in air.”
OSHA also correctly points out that when ammonia is mixed with lubricating oils, its flammable concentration range increases. It can explode if released in an enclosed space with a source of ignition present, or if a vessel containing anhydrous ammonia is exposed to fire. Fortunately, ammonia has a low odor threshold of 5 ppm, so most people will seek relief at much lower concentrations.
How gas behaves in the plant
Toxic gases, including ammonia, can be difficult to detect, depending on the specific gas and the plant layout. For example, fertilizer plants are typically crowded with equipment where ammonia can be present. The same can be said for many other materials-processing or other industrial plants where ammonia is present as a refrigerant gas for chilling or refrigeration. Layered, redundant monitoring gas-detection sensing technologies provide an added degree of safety against toxic and combustible gases, such as ammonia.
Leaking ammonia also tends to form clouds outside plant buildings that are affected by temperature and weather. These clouds also have the potential to travel beyond the plant perimeter, potentially endangering other nearby facilities or the community at large. For these reasons, plant safety teams typically rely on a mix of portable detectors worn by employees and plant fixed-gas detection systems,including perimeter monitoring.
Gas detection and sensing
There are several types of fixed-gas detectors that are appropriate for protecting plants from toxic gases. Point detectors relying on infrared (IR), electrochemical cell or other contact sensing technologies are typically placed throughout the plant near equipment in production areas, on pumps, valves, pipelines and tanks for loading and unloading. Along plant exterior boundary fence lines, perimeter detectors are placed. These detectors rely on open-path detection technologies.
Many types of fixed-gas sensors are available to detect ammonia vapor and other toxic or combustible gases within industrial applications. The following sections look at the operating principles behind these technologies with an eye toward understanding their strengths and potential weaknesses.
Optical infrared technologies
Optical infrared (IR) sensors have been used for decades to monitor combustible and toxic gas leaks, including ammonia (Figure 1). The key benefits of IR sensors are their high specificity to ammonia and reduced (or even eliminated) need for calibration adjustment. IR detectors have a wide dynamic range and are not degraded or consumed by exposure to high concentrations of ammonia. Their main limitations are the physical size of the detector assembly, the need to protect the detector against the potential effects of fluctuating temperature and humidity and higher cost compared to other detectors.
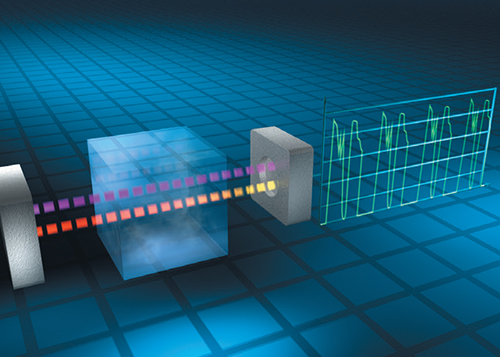
FIGURE 1. Optical infrared sensors offer a high specificity for ammonia without degradation when exposed to high concentrations
Differential infrared. Differential IR sensors measure gas as a function of the absorbance of infrared light. Molecules consist of atoms that are held together by chemical bonds. The bonds in a particular type of molecule (such as ammonia) absorb energy at selected wavelengths. When a chemical bond absorbs infrared light, it continues to vibrate at the same frequency, but with greater amplitude after the transfer of energy. In other words, molecules that can absorb energy at that wavelength are heated to a higher temperature than molecules that are not able to absorb light at that wavelength.
When IR radiation passes through a sensing chamber containing a specific gas, the only wavelengths that are absorbed are the wavelengths that match the chemical bonds in that gas. The rest of the light is transmitted through the chamber without hindrance. As most chemical compounds absorb at several different frequencies, IR absorbance can be used for measuring the gas concentration.
TDL absorption spectroscopy
Alternatively, for some molecules, it can be possible to find an absorbance peak at a specific wavelength that is not shared by other molecules that may be present. In this case, absorbance at a particular wavelength can be used to provide a substance-specific measurement for a specific molecule. This is possible for some molecules, including ammonia, which has a usable absorbance peak at a wavelength of about 1,512.2 nm using laser-based IR detection technology. Absorbance at this wavelength is proportional to the concentration of ammonia.
Tunable diode laser (TDL) absorption spectroscopy technology is used by open-path gas detectors operating similarly to point IR gas detectors. The difference between the two technologies is the distance between the light source and the receiver, which for open-path gas detectors can be more than 330 ft (100 m). The system cannot determine the size of the cloud or its concentration, so it calculates the total amount of the specific wavelength being absorbed by the gas. This calculation then determines the concentration of gas between the source and the receiver and is represented in the measurement range of ppm meters.
PAIR sensing technology
Photoacoustic infrared (PAIR) analysis extends beyond simply measuring the amount of infrared light that is absorbed, which is the case for the nondispersive infrared (NDIR) monitors described earlier. This technology actually detects what occurs after the gas is absorbed. Photoacoustic sensor technology is ideal for detecting ammonia at very low concentrations (as low as 10 ppm). It offers zero stability, eliminating the need for zero drift adjustment. A direct gas reading is obtained because there is no need for a reference point, ensuring continuous monitoring. No zero point is involved, providing the most accurate and reliable readings.
When using a PAIR instrument (Figure 2), a gas sample is introduced into the monitor’s measurement chamber and the sample is exposed to a specific wavelength of infrared light. If the sample contains the gas of interest, that sample will absorb an amount of infrared light proportional to the gas concentration that is present in the sample. Gas molecules are always in motion and move around the inside of the measurement chamber, generating pressure. When gases absorb infrared light, the temperature of the molecules rises, and they begin to move more rapidly. As a result, the measurement chamber pressure increases, creating an audible pulse that can be detected.
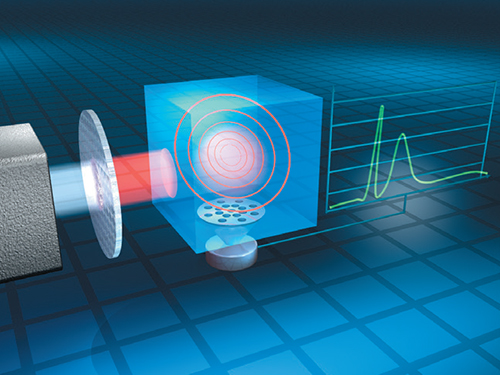
FIGURE 2. Photoacoustic infrared sensors can continuously detect ammonia at very low concentrations without the need for a reference point
A highly sensitive microphone is located inside the photoacoustic infrared monitor to detect even the smallest of pressure pulses, enabling detection of very low levels of gas. As the optical filter will only pass the particular wavelength of light for the gas in question, a pressure pulse indicates that the gas is present. The premise is simple; if no pressure pulse occurs, then no gas is present. The magnitude of the pressure pulse indicates the gas concentration present. The stronger the pressure pulse, the more gas that exists.
ELDS technology
Another technology using the effect of absorption of specific optical light by ammonia is laser-based open-path gas detectors. This sensor technology utilizes enhanced laser diode spectroscopy (ELDS). Unlike point NDIR or other point gas detectors that simply measure the gas concentration at a particular (fixed) location, ELDS gas detectors measure the concentration (in ppm per m or ppm-m) over the full distance between the transmitter unit and receiver unit.
ELDS open-path detectors analyze the signal using a technique called Fourier transform, which breaks the signal into several component parts that can be analyzed against a predetermined pattern that is similar to a harmonic fingerprint (Figure 3). This means there are no false alarms from interference gases, the detectors are less prone to water-vapor interference, and they provide greater reliability and performance in rain or fog.
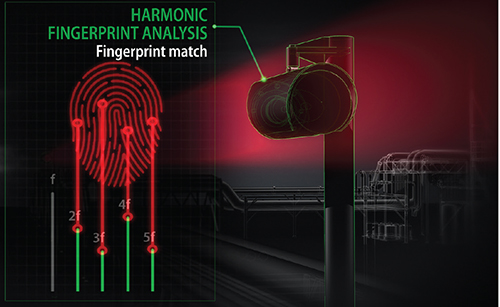
FIGURE 3. Enhanced laser diode spectroscopy can be used to detect specific gases without false alarms from interference gases or water vapor
The ELDS transmitter/receiver configuration is failsafe, which improves the level of safety. It also does not require calibration or any other routine maintenance and has no consumable parts, resulting in a low cost of ownership. With a built-in automatic self-testing function, an ELDS sensor offers end users a solution to the problem of costly and time-consuming testing of gas detectors.
MOS sensors
Metal-oxide semiconductor (MOS) sensors, also known as chemisorption sensors, consist of a metal-oxide semiconductor, such as tin dioxide (SnO2) on a sintered alumina ceramic bead contained within a flame arrestor (Figure 4). In clean air, the electrical conductivity is low. Oxidation of the measured gas on the sensing element increases conductivity. An electrical circuit is used to convert the change in conductivity to an output signal which corresponds to the gas concentration. Sensitivity to a particular gas is measured by changing the temperature of the sensing element.
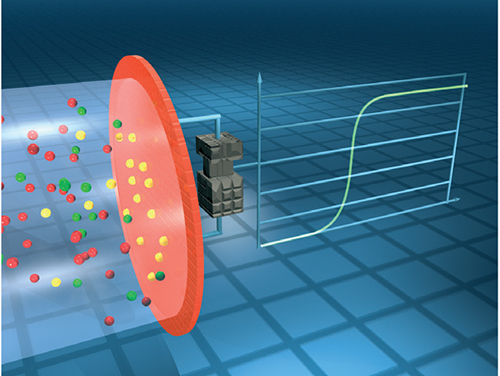
FIGURE 4. The detection mechanism of metal-oxide semiconductor sensors involves the measurement of conductivity as the target gas is oxidized on the sensing element
MOS sensors are designed to respond to the widest possible range of toxic and flammable gases and vapors. The idea is to provide a “broad range” response to the presence of contaminants. MOS sensors can detect chlorofluorocarbon refrigerants, as well as other gases that are difficult to detect by other means, as well as ammonia, carbon monoxide, hydrogen, alcohols and many other gases and vapors.
Their non-specificity is advantageous where unknown toxic gases are present, and a simple go/no-go determination is sufficient. As the sensors are not specific to ammonia, however, this can lead to false alarms if the sensors are installed where interfering contaminants are present. The benefits of MOS sensors are their long operational life and low cost. MOS sensors can be used to detect ammonia concentrations as low as 30 ppm, up to concentrations in the flammable range.
Electrochemical sensors
Target-gas-specific electrochemical (EC) sensors are available for many of the most common toxic gases. Electrochemical sensors are compact, require very little power, exhibit excellent linearity and repeatability, and are comparatively inexpensive. The detection technique is very straightforward in concept.
Electrochemical sensors function on principles similar to those found in batteries. The target gas enters the sensor through an inlet, and then generates a chemical reaction with a catalyst that is in contact with an electrode. When the target gas encounters an electrolyte solution on the working electrode, a reaction occurs (Figure 5).
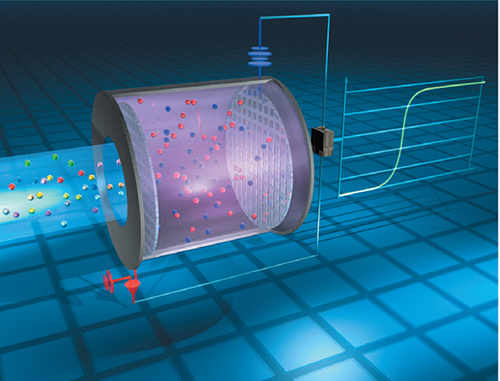
FIGURE 5. In an electrochemical sensor, the target gas contacts a catalytic electrode site and an electrolytic solution, and electrons are released. By measuring this current, the presence of the target gas can be determined by the sensor
This reaction causes a release of electrons, whereby the flow of the electrons is measured as current within the sensor. Consequently, the current is proportional to the gas concentration and the reaction is measured in ppm of the gas. In the case of ammonia sensors, the electrolyte includes an active ingredient that is consumed in the electrochemical reaction used to detect the ammonia. Thus, the lifespan of the sensor is directly related to its amount of exposure to ammonia.
The sensor is filled with an organic gel electrolyte mixture in which the reaction occurs (Figure 6). Active ingredients in the electrolyte are incrementally consumed as the sensor is exposed to ammonia. Once the exposure life of the sensor is exceeded, it is no longer capable of detecting gas, and will need to be replaced. Next-generation technology utilizing ionic-liquid electrolytes have an extremely low vapor pressure, and they do not evaporate in extreme environments, even with long periods of low humidity. The positive benefits for this type of sensor include good resolution in the low-ppm range and acceptable cold-temperature performance.
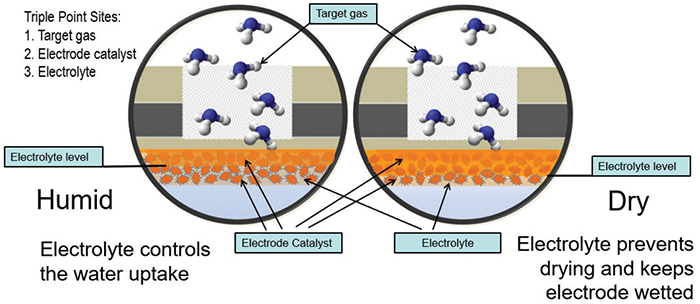
FIGURE 6. The electrolytic solution in an electrochemical sensor is consumed as the sensor is exposed to the target gas
Catalytic bead sensors
These sensors use a catalytic bead to oxidize mainly combustible gases, but also higher-volume-percentage concentrations of ammonia (Figure 7). A bead is represented by wire coil coated with a catalyst-coated glass or ceramic material and is electrically heated to a temperature that allows it to burn the gas being monitored, releasing heat and increasing the temperature of the wire. As the temperature of the wire increases, so does its electrical resistance. This resistance is measured by a Wheatstone bridge circuit, and the resulting measurement is converted to an electrical signal used by gas detectors. Usually a second sensor, the reference bead, is used to compensate for temperature, pressure and humidity. These sensors have a long life and are less sensitive to temperature, humidity, condensation and pressure changes. However, they are also subject to sensor poisoning and shortened life with frequent or continuous exposure to high measured-gas concentrations. Another limitation is that they monitor a wide range of combustible gases and vapors in air, and therefore are not specific to ammonia gas.
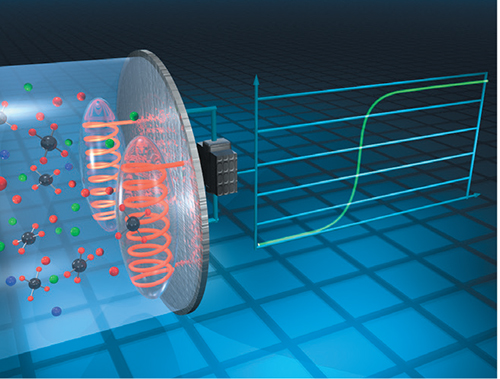
FIGURE 7. Catalytic bead sensors are mainly used to oxidize combustible gases, but they can also be used in high-volume ammonia applications
Keys to success
It is important to understand that no single type of toxic or combustible gas sensor is perfect or foolproof in all industries and applications. The keys to gas monitoring that drive success are understanding the following:
- The human gas exposure symptoms and health issues
- The physical properties of the gas hazard
- The plant’s geographic location and the plant physical site environment
- The potential gas leak sources and location where detectors must be placed
- The applicable choices of sensor technologies and their advantages and limitations
- The chosen detector’s calibration and installation requirements
- The detector’s maintenance requirements and its lifecycle
Many of the mature and the newer sensing technologies have improved through evolving designs, materials advances and better construction technologies. In addition, sensors are now highly intelligent compared to 20 to 30 years ago with benefits that include diagnostics, self-regulation and network communication with other process safety systems in the cloud for remote monitoring.
Author
Sarah Rajasekera is a segment marketing manager at MSA Safety (Email: [email protected]; Website: us.msasafety.com), where she develops go-to-market strategies that increase revenue and drive demand for the Fixed Gas and Flame Detection product group. She has a B.S. degree in chemistry from Carnegie Mellon University. Prior to joining MSA, she was in sales and marketing roles related to industrial manufacturing.