As benefits become apparent, the acceptance of modular process systems grows and the concept finds new opportunities
While providers of modular process systems and facilities will tell you modular builds were once a hard sell, modularization is now sought after for both traditional process systems, as well as new and novel applications. What is the reason? Aside from its many inherent benefits, including reduced costs and significant schedule reductions, the modular concept lends itself to a variety of applications across many processes (Figure 1).
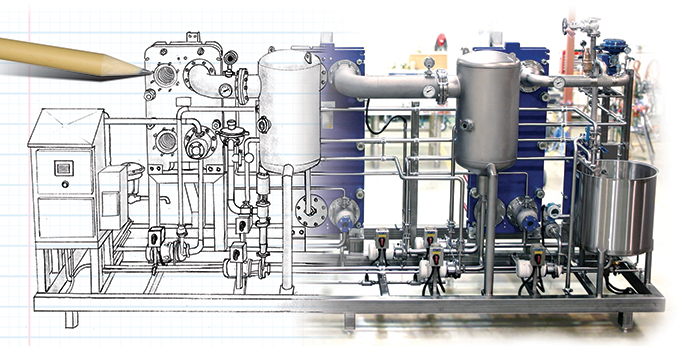
Figure 1. Modularization is now sought after for both traditional process systems, as well as new applications because the modular concept easily lends itself to a variety of applications across many processes. Shown here is a caustic soda evaporator skid Barnum Mechanical
“The acceptance of modular construction continues to expand,” says Thomas Schafer, vice president of Koch Modular Process Systems (Paramus, N.J.; www.kochmodular.com). “When we first got into the modular business, we had to overcome objections that modular construction was different and potentially would be crowded and difficult to maintain. But now we’re finding that most of our clients don’t have to be convinced about the benefits and quality of modular construction, as it has been widely proven, which is expanding modular opportunities.”
Not only are previously conservative companies embracing modular builds, but the scope of projects is growing as well. “In more recent projects, the scope has expanded so that instead of supplying only distillation equipment, we are supplying reactors, as well as filters, compressors and other equipment modularized,” Schafer continues. “So, the trend is that we are expanding the unit operations going into these systems” (Figure 2).
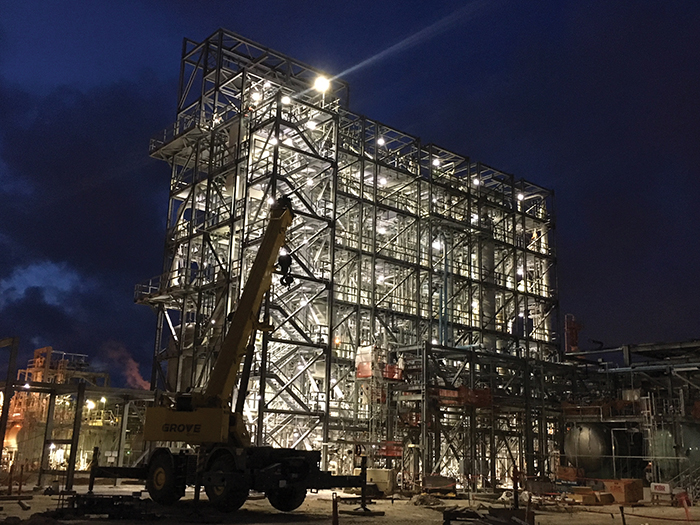
Koch Modular Process Figure 2. This complete modular constructed process plant was designed and built for a southern U.S. specialty chemicals producer. It was a late addition to a larger project that was field constructed and the schedule was critical to catch up to the balance of plant
The big drivers for the increased interest in modular construction, according to David Funderburg, global technology manager with ABB (Cary, N.C.; www.abb.com), are the reduction of costs, schedules and risks. “Costs are reduced because you can build off site, and risk is reduced because you can pre-test and pre-document the systems, which in turn improves schedules because late changes can be managed due to the Lego-like approach of modular construction versus having a big project where any change has a ripple effect on the schedule for the entire project,” explains Funderburg.
Modularization benefits
Modular construction is known to reduce costs due to the assembly-line-like building concept. In addition, the controlled workshop environment also reduces schedules, improves quality of the finished product and increases safety, which directly lead to additional benefits for owners of modular process skids (Figure 3).
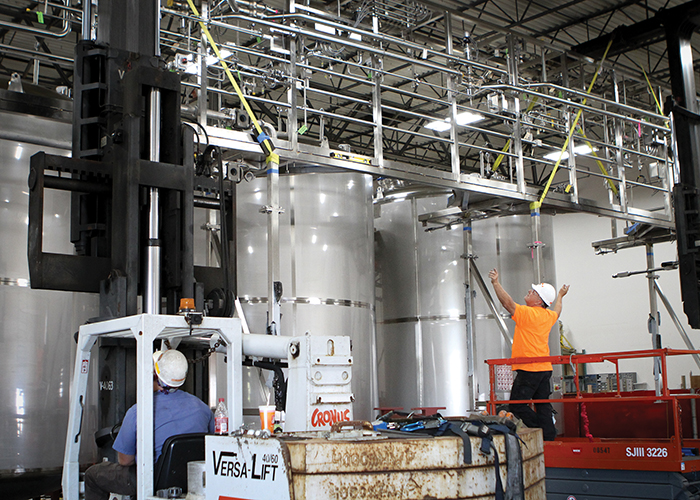
Figure 3. The controlled workshop environment reduces schedules, improves quality of the finished product and increases safety, which directly lead to additional benefits for owners of modular process skids EPIC Modular Process Systems
Costs savings often result from labor savings, according to Ken Sipes, director of engineering for the process and mechanical group with EPIC Modular Process Systems (St. Louis, Mo.; www.epicmodularprocess.com). “Especially on large projects in an area where construction is usually performed by union craftsmen, modular projects often provide an opportunity to realize labor savings while still providing quality work performed by talented craftsmen who build to the same specifications as unionized labor forces, just under a different labor agreement.”
Additional savings can be found on very large jobs where “a massive labor force would be required,” Sipes adds. “In some geographical locations, a labor force of this size might be almost impossible to deliver,” he says. “When labor is a limiting factor, you’re left with the same amount of work to be done with a smaller crew. That crew has to work more, which means paying premium overtime wages, as well as per diems and travel expenses. However, taking a modular approach can spread the work out geographically to where the workforce is readily available, lessening the impact of those costs.”
Elizabeth Manning, manager of sales with Koch Modular, says savings are also discovered because project owners don’t have to employ a large project engineering staff to oversee the project. “They can issue a single purchase order and, ultimately, we are responsible for all of the vendors’ building equipment, fabricating piping and doing electrical work. This allows the project owner to run a leaner staff than if they had to manage a field-erected plant.”
The workshop environment also lends itself to reduced project schedules, as craftsmen can work indoors in a controlled environment without weather or other interference while site permits are obtained and the site is prepped. And, since skids are always pre-tested prior to delivery, it reduces installation time. “We pretest the systems and ensure that all instruments are wired correctly, calibrated and configured, all motors turn on and off and all valves are actuated to verify functionality,” says Doug Cornwell, controls engineering manager, with Barnum Mechanical, Inc. (Loomis, Calif.; www.barnummech.com). “More often than not, customers request modifications or additional features during installation. This means that the installation may require more time than anticipated, but the owner’s startup date isn’t going to move. However, because we do testing in our shop, we are able to reduce I/O check out, commissioning and validation time during installation and often can reduce the on-site commissioning portion of the project from two weeks to ten days. Pre-testing allows us to absorb some of the schedule hits that sometimes occur during installation.”
Experts estimate that the controlled workshop environment, concurrent building and pre-testing associated with modular construction can shave anywhere from a quarter to half the time from schedules when compared to the same project when traditionally fabricated.
As a side benefit, compressed schedules help companies get their products to market faster, says Schafer. “Some clients come to us because they are in a time crunch and need to save time in order to get to market faster and satisfy offtake contracts,” he says. “They know that if they build the plant modularly, in some cases, they can be up and running six months to a year earlier than they would be if they had a large engineering company site construct the same facility.”
This is important even where customer contracts aren’t an issue, he adds. “Once the owners have made the decision to spend the capital, they don’t want to wait any longer than necessary for a project to be completed. The faster the project is done, the faster they realize profits from it,” explains Schafer.
And, in existing facilities, the modular concept helps reduce downtime, says Gregory Sandell, senior process engineer with Barnum. “We do a lot of work in existing facilities and because they’re currently operating, downtime is lost revenue,” he says. “Many customers in this situation find that if they go modular when they need to replace an older system with a better performing one or one that meets current standards, it can reduce the financial impact on their production schedules.”
EPIC Modular Process Systems’ Sipes agrees: “Think of installing processes within existing chemical plants like open-heart surgery. The heart and soul of that plant is running and has wires, power, communication and utilities connected to it and it’s making product. The moment you turn off the flow to the process and start tearing it apart is the moment you stop making money,” he explains. “With modular, you can do 75 to 90% of the work in the shop, bring it to the site, turn off the existing equipment, remove it, drop in the new skid, reconnect it faster because it’s been pre-tested and be up and running again relatively quickly.”
Additional perks of modular construction include increased safety and consistency, according to the experts. “Safety is the number one priority with our customers and this remains true when they are executing projects,” says Sipes. “Modular construction lessens the amount of work done at a customer’s property so their exposure goes down. Additionally, when a system is built in a controlled environment on a shop floor, it’s inherently safer than doing this work on a job site where they are climbing and weather and elements are a factor. It creates a safer project execution strategy” (Figure 4).
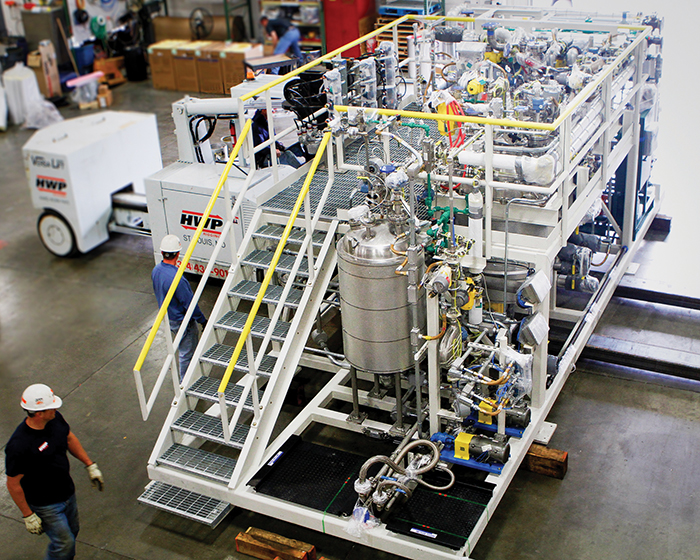
Figure 4. When a system is built in a controlled environment on a shop floor, it is inherently safer than doing this work on a job site where workers are climbing and weather and elements are a factor. It creates a safer project execution strategy EPIC Modular Process Systems
And, for processors for whom consistency across locations is key, modular builds often provide the solution. “Some customers have facilities throughout the U.S. or globally and they want to deploy new technologies within multiple plants, but they require the same technology and the same equipment not only to provide consistent quality of the finished product, but also so that inventory and training, operations and maintenance are the same at each of those plants,” says Sipes. “This can only happen when the same equipment is built to the proper codes, using consistent craftsmanship, workmanship, techniques and equipment and delivered to each of those plants in a modular fashion.” For these and other reasons, modular technologies are being employed in new applications.
A Word About Controls
Currently, control of modular process skids is handled in one of two ways, depending upon the needs of the owner. According to Doug Cornwell with Barnum, the skids can be designed with the programmable logic controller (PLC) onboard and a self-contained program. This is often the route selected when the end user doesn’t have a main PLC in the plant or when they don’t want to integrate the process skid into the main control system. The skid operates via its own control panel and operator interface terminal.
The second method of control is usually employed when the end user has a PLC and they want to control the skid via the main control method. “In these cases, we supply the instrumentation and input/output (I/O) hardware according to their specifications. We put a panel on the skid with distributed I/O modules that match the brand of the PLC in the plant,” he explains. “We pre-wire the skid to that distributed I/O panel, do all the pre-testing, etc., so that when we install the skid in the plant, we just bring power to the distributed I/O panel and a communication network cable and integrate our program from the skid into the owner’s existing PLC program.”
For companies that are building from the grassroots, skid builders often help them select appropriate instrumentation and PLCs to meet their needs and integrate the skids in the same way.
While skid manufacturers are very flexible in how their skids are controlled, the control and automation industry is looking forward to potential integration standards, says ABB’s David Funderburg. “The NAMUR-led Modular Automation Initiative addresses the need to achieve an open standard interface to skid equipment,” he says. “This means that end users would not be forced to use one skid vendor or one automation supplier, thus achieving true interoperability.”
He suggests thinking about standardizing skid automation like a printer driver, defined by NAMUR Modular Automation as an Module Type Package (MTP). “You buy a skid that has a controller or PLC on it, as well as an interface driver (that is, MTP) that you just import into your automation system. The brand won’t matter because the MTP includes pre-configured data connections, including process graphics and services, which makes it easy to import” (Figure 5).
Standardization, when achieved, will benefit skid builders, as well. “OEM skid suppliers can supply the skid with their own intellectual property in their preferred platform and the interface to it will be an open standard. This means they aren’t forced to change their software or architecture to meet that of a project-specific solution,” says Funderburg.
Currently, specialty chemical and pharmaceutical processors are seeking this type of standardization because it provides flexibility, allowing them to buy skid equipment to make one product, then rearrange the skids to make a different product in a plug-and-produce fashion without worrying about control and interface compatibility, he says.
Standardization would also benefit traditional oil, gas and chemical plants that have a lot of integrated skid equipment, as well, says Funderburg. “Usually there’s a lot of I/O and engineering involved on projects of large magnitude,” he says. “But standardization would reduce the engineering and allow users to plug in a skid and have data right away without the extra overhead of customizing interfaces to get the data from the vendor’s PLC.”
While it will make modularization more convenient, standardization is still a work in progress due to the conservative nature and complexity of our industry, notes Funderburg. “The standards have been released and there are pilots taking place in Europe, but there is a lag between the pilots being complete and wide-scale adoption. We are in between the technologies being proven at pilot scale and larger facilities before we can start seeing it as a standard specification for skid integration.”
New opportunities
One of the newest trends is using modular skids for sustainable initiatives that reduce waste or environmental impact. “One of the hottest markets for modular skids right now is water recovery or water harvesting,” says Tony Salemi, product manager with Chicago Plastic Systems (Crystal Lake, Ill.; www.cpsfab.com). “The skids recover gray or runoff water and treat and recycle it for use in flushing toilets or for irrigating landscaping. The skids include the filtration mechanisms, ultraviolet (UV) or chlorine-treatment equipment, pumps and other necessary components.”
While the process is not new, modularizing it onto a skid makes it convenient to go green. “If a company wants to do this, they just order the equipment. It’s delivered as a skid and installed in about a day. Then they simply collect the water and turn it on. It makes it very easy and convenient for a manufacturer to reduce their environmental impact by not using potable water to flush toilets or irrigate landscaping,” he says.
Solvent recovery is another process employing modular skids with more frequency. “Everyone who manufacturers paint, adhesives or resins uses solvents and most of them want to recover these solvents at the end of the process and recycle them back to the front of the process,” says Rocky Costello, president of R.C. Costello & Associates, Inc. (Redondo Beach, Calif.; www.rccostello.com). “This is being accomplished with modular batch or modular continuous distillation equipment.”
Creating fertilizer from wastewater treatment is another new application for modular skids. Barnum worked with a large municipality to help develop a modular, low-temperature, commercial-scale, skid-mounted thermal hydrolysis processing unit. The mobile process was developed in response to increasing demand for practical resource-recovery solutions, particularly from smaller-scale solid-waste treatment plant operators, allowing end users to create Class A bio-fertilizer product during the waste treatment process.
Another new area for modularization is in specialty and pharmaceutical processing, where the switch is being made from batch processing to continuous flow chemistry, because they are starting to realize that cost benefits can be achieved by moving from batch to continuous processing, says Costello. Often, when making the switch, these processors take a modular approach. “The cost and size of the plant is much smaller when employing continuous processing in these types of facilities and when you have smaller plants, as compared to batch processing, it’s very amenable to do so in a modular fashion.”
Besides reducing cost and size, it increases their flexibility. “If possible, we build the plant with modules that can move around. You may have a reactor here, a crystallizer there, a filter under a crystallizer, and so on. And, if modules are built correctly, owners can move them around into a new configuration if products change,” explains Costello.
Another new market includes bio-derived chemicals and fuels, says Koch’s Schafer. “Many of these products are being created by start-up companies with a great idea for a new route to a product, but who need to hire a company with chemical process engineering expertise to get them to a full-plant-constructed solution that is economical, flexible and safe. As a result, we’ve gotten involved in assisting several such companies with the development of these processes. And, because they want to get this new product to market as quickly as possible, modular construction makes sense as it is inherently faster.”
Case in point, Koch Modular recently worked with New Jersey-based start up Primus Green Energy on its natural gas-to-liquids technology, specifically their processes for converting natural gas to drop-in gasoline and methanol via reforming, reaction and distillation unit operations. Koch assisted Primus with engineering services supporting the process conceptualization and pilot-testing phase and, later, the development of the process design package and the forthcoming detailed engineering and construction of its first commercial-scale system.