Milling active ingredients combines equipment selection, material characterization, and process characterization, with the aim of improving and controlling the properties of the solid crystalline drug substance. These topics are discussed here
Milling is a common technique used for the reduction and control of particle-size distribution (PSD) for active pharmaceutical ingredients (APIs), many of which are crystalline solids. Regulatory expectations require APIs of high purity, and consistent well understood physical properties [1]. Particle characteristics of APIs, such as solubility and surface area, and important powder characteristics, such as flowability and compressibility, impact bioavailability (BA) parameters when formulated into drug products (DPs), such as tablets, capsules, suspensions and inhalation products [2, 3].
Overview of milling
Mills are useful tools to generate API particle properties with desired and consistent properties, through size reduction and surface modification mechanisms. The use of mills in the pharmaceutical industry remains prevalent, due to their modular nature, predictable performance and wide range of equipment availability. The choice of mill for a specific application is dependent on the performance capabilities relative to the properties of the feed material, as well as any constraints particular to the mill that is being considered for the function. The comparatively low-volume nature of pharmaceutical products means there are fewer concerns about energy utilization in milling than in mining and commodity chemicals.
Particles can be conveniently characterized by a characteristic size, L (m), of the particle [4]. The distribution of size for a population of particles is then communicated through the normalized frequency distribution f(L), and cumulative distribution F(L), often measured by a light-scattering technique [4]. The feed and the milled product are characterized in terms of these, and often specifications are placed on the product cumulative distribution F(L), which is the fraction of particles less than or equal to L. Although statistics are used extensively to characterize size distributions and their specifications, there is no adequate substitute for imaging particles, because their shapes and surfaces are not completely described by statistical metrics.
Milling results in particle size reduction, the creation of new surface, and surface modifications — roughness, for example. This transformation is achieved by the comminution mechanism, whereby the solid particles are fractured by mechanical force delivered to particles, achieved in a myriad of ways depending on the mill type. Surfaces of milled products are modified through the fracture mechanism and by abrasion.
Broadly, mills can be separated into wet and dry mills, and these two categories are each further subdivided by how comminution is achieved, such as rotor-stator mills, jet mills, pin mills, hammer mills, media (ball) mills and cavitation mills. Wet mills use liquid as their working fluid, whereas dry mills use gas.
Common mill types and their characteristics are provided in Table 1. Each type of mill is characterized by an energy input mechanism and a particle-breakage mechanism. As a rough guide, the mill type is selected against the product size range when milling solids. In turn, the size range of the product is informed by formulation development, modeling, and the Biopharmaceutics Classification System (BCS) class of the compound. Scaling up the milling operations is specific to each type of mill, and revolves around the normalized energy input to the particles. Consistency of mill supplier is helpful in maintaining control of processing at various stages of development.
What size range is needed?
The required size range for a pharmaceutical compound formulated as a solid is arrived at through experimental human and animal tests, along with modeling of the absorption behavior of the formulation. The BCS classification system provides a guideline for solid oral products through their solubility and permeability [8]. BCS Class III products, having high solubility and low permeability, are dissolution-limited in their absorption, and hence, can be very sensitive to particle size distribution. BCS Class I products may not require as tight control of distribution due to their rapid uptake. BCS Class II and IV may require additional formulation work to improve absorption through additives. Inhalation products will have extreme requirements based on the physics of deposition in the lung [9], with specifications of 1–2µm being common.
How milling impacts PSD
Milling changes the size distribution and is intended to provide normalization; that is, a similar size distribution of product is obtained for various size distributions of feeds. Theoretically, a milled product is predicted to have a log-normal or Weibull distribution [ 10], related to the probability of a particle fracturing and the nature of the fragment as a function of its original size. Practically speaking, this means that milling does not typically give symmetrical Gaussian distributions, and instead skewness and tails are common depending on the type of mill. Figure 1 provides examples of size distributions before and after milling for a couple of the common techniques.
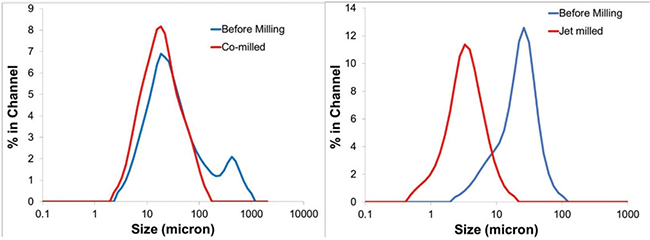
Figure 1. Shown here is the particle-size distribution before and after co-milling (left) and before and after jet milling (right)
Milling also impacts the shape, or morphology, of API crystals, particularly for high aspect ratio “needle” or “rod” type particles. The comminution fracture mechanism is often along the length of these crystals, effectively chopping them along the length scale into lower-aspect-ratio shapes, with consequent change in the physical attributes, such as bulk density, as well as formulation behavior, such as flow properties — in a slurry as well as in a solid DP mixture. The practical manifestations of aspect-ratio reduction include less plugging inside a syringe for an injectable drug and improved flow properties for better mixing and DP content uniformity (CU) parameters, such as RSD (relative standard deviation) for solid dosages, including inhalants or implants. Reducing aspect ratio can also lead to better compressibility/compactability for tablet formulations and achieve a higher dosage in a solid capsule without resorting to granulation methods (wet or dry) to help densify the drug product intermediate.
Properties of crystals
While milling energy has a direct correlation to particle-size reduction, the physical properties specific to the crystalline API particles also have an important effect as well. The mechanical strength of a crystalline organic compound can now be modeled and calculated by computer models once the crystalline lattice is determined by assay methods like single-crystal X-ray diffraction (XRD). The lattice energy is sometimes presented as attachment energy, meaning the amount of energy required to pull apart adjacent crystalline planes. Additional mechanical properties, such as the Young’s modulus and tensile strength, can also be estimated from the theoretical attachment energy.
Empirically, we can use a lower energy “weaker” mill, such as a rotor-stator wet mill at a lower tip speed (25 m/s) to assess and rank the relative friability of API crystalline forms in a semiquantitative manner. Running in batch mode, we can reach the steady state PSD in about 90 s for a 3-g test batch and then analyze the milled particle size. Less friable crystals only reach d50 (mass median diameter) particle size in the 40- to 50-µm range, while moderately friable crystals are reduced to 20–30 µm and the most friable crystals can go down to 10-µm size. In addition, we have observed that when exposed to more mild milling methods, the milled PSD of stronger crystals show a dependence on the starting particle size, while for weaker and friable APIs, the milled PSD is often independent on the initial size.
The crystal shape and morphology can also have an effect on the milling performance, and here again higher-aspect-ratio particles have more unique properties. For example, needle-shaped crystals are often challenging to fracture in rotor-stator wet mills, because the long thin particles tend to follow the flow patterns of the suspension liquid and therefore result in glancing collisions that are significantly less effective at breakage, so a needle could at most be chopped once along the length axis. For dry milling, where the carrier media is gaseous, this effect is much less pronounced, and a needle may be broken into many more low-aspect-ratio particles. Crystal morphology also impacts the orientation of the particle fracture and the surface area changes from particle size reduction. Again, higher-aspect-ratio crystals, such as needles or rods, are more likely to break along the length axis, even if the attachment energy of the cleavage plane is higher than other potential cleavage planes, due to the angle of impact and mechanical moments experienced during collisions and other factors. When broken along the length axis, the increase in surface area may only be 10%, even though the particle size drops by 50%. On the other hand, breakage along any axis of a more isotropic 3D cube-shaped crystal that causes the same 50% reduction in particle size will also generate twice the number of particles and twice the surface area.
Mills for dispersion and sieving
Comills or hammer mills (Figure 2)disperse agglomerates or aggregates of crystalline APIs, instead of particle size reduction via the comminution mechanism. Aggregates are particles that are fused together from solid bridges of precipitated API out of the evaporated interstitial mother liquor or cake-wash solvents, or through a contact bridge. These aggregates/agglomerates are often formed after the filtration and drying operations, when solvent-wet particles clump together due to surface-energy effects between the crystalline solids and solvents, as well as potential exacerbating effects from mechanical agitation of the drying cake, of from compression during storage due to normal force. Smaller-sized crystals are often more liable to form aggregates or agglomerates because of their increased surface area and improved packing capabilities. Aggregate/agglomerate sizes can range from a few fine- (micron) sized particles stuck together to a 10-µm range agglomerate, up to multi-centimeter-sized granules (lumps) that are easily visible to the eye without any optical magnification. For most crystalline APIs, agglomeration is undesirable because of the inherently lower reproducibility and control over API physical properties and formulation behavior that often leads to lower content uniformity or compactability of the DP.
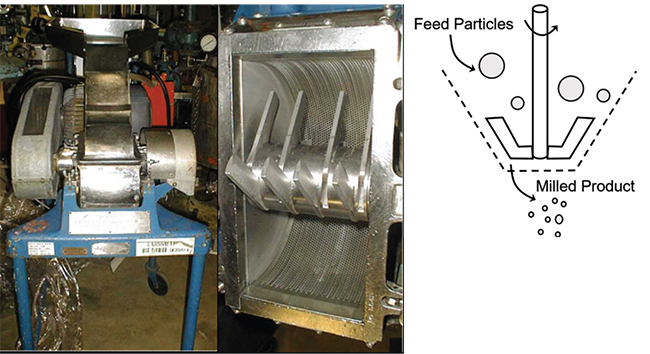
Figure 2. The photos show a hammer mill motor (left) and a a cutaway showing the hammer mill screen and hammers (middle). The comill schematic (right) shows the rotating element, the screen, the feed particles and the milled product
Comills and hammer mills can operate with significantly lower mechanical energy compared to a jet mill, resulting in dispersing of the aggregates or breaking only the weaker solid bridges connecting the agglomerate particles together [11]. The effect is similar to forcing the granules or agglomerates through a mesh screen, usually with no reduction in the primary particle size of the API. On the other hand, these type of degranulation “mills” usually lack sufficient mechanical energy to fracture crystalline agglomerates generated by high supersaturation-related nucleation and agglomeration-driven macrostructures, such as “starburst-” shaped agglomerates (Figure 3, left); or spherical crystals composed of submicron- to micron-scaled fine particles (Figure 3, right) — unless perhaps operated at very high tip speeds in the 100 m/s range. Higher energy jet- or pin-milling equipment will disperse all but the smaller diameter agglomerates, but sometimes will also fracture the primary particles as well, resulting in lower than desired API PSD.
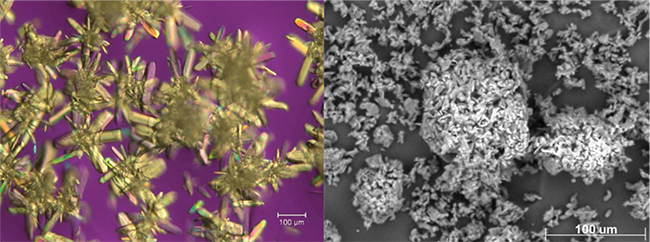
Figure 3. These micrographs show “starburst” (left) and spherical agglomerated crystals (right)
The comill is essentially a screen with controlled sieve size and a rotating element that pushes the powder through the screen. The spacing of the element from the screen, the rotational rate, and the screen size are the important parameters. This type of mill is sometimes called a de-lumper because the primary purpose is to remove lumps and loosely bound aggregates over large size ranges.
The hammer mill (Figure 2) is a dry mill that is more unique in that it can act to either disperse agglomerates or fracture particles (albeit usually larger sized ones) depending on the operating conditions. The “hammers” are arrays for rotating fin-like blades, with one side being a flat contact surface (the “hammer”), the opposite side a tapered sharp blade geometry. Depending on the direction of rotation, this mill can use either a blunt impact mechanism or a sharper cutting action to effect particle fracture or agglomerate dispersion. The tip speed (and consequent mechanical energy conferred from the blades to the particles) is the primary deciding factor on whether de-granulation or comminution occurs.
Wet milling
Most APIs are crystallized in water or organic solvents, which are Newtonian fluids and incompressible. In wet milling, the slurry containing crystals is directly milled in a rotor-stator device prior to filtration and isolation of the product. The wet mill rotors and stators are composed of walled disks with gaps, called “slots” or “teeth,” on the walls (rotor/stator pairs are shown in Figure 4). When spinning at a high tip speed, the rotor acts like a centrifugal pump, which moves the API in solvent slurry through the mill and forces flow through the narrow slots, creating transient highly turbulent eddies that constitute the mechanical energy source for particle breakage, likely due to force moments transferred from the liquid media to the particles.
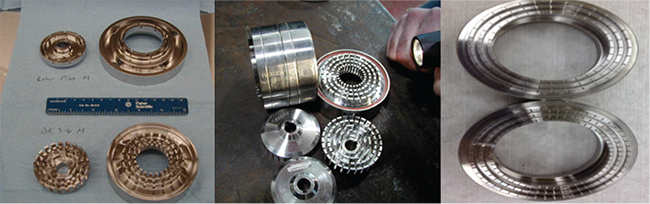
Figure 4. Shown here are various rotor/stator pairs for wet mills
Historically, rotor-stator wet mills were used to form emulsions via the shear forces attained from the high turbulence zones within the teeth/slots that the oil-water mixtures were forced through, with the droplet size determined by the tip speed and the fluid properties of the two immiscible liquids. In milling applications, force transfer occurs directly through the media to the target particles, so the mechanism of action is often shear forces due to highly turbulent flow being transferred from the liquid to the solid, which is the cause of the massive fracture events that produce the particle breakage along defects in the particles due to crack tip propagation.
Organic crystals are relatively brittle and don’t possess ductile healing properties. On the other hand, the liquid viscosity can act as a lubricating layer that dampens the force in particle-particle or particle-wall collisions, making this fracture mechanism less effective. The higher viscosity of liquids also makes for much lower energy usage efficiency, since the majority is dissipated in the form of heat generated by viscous friction forces [12].
Rotor-stator wet mills have historically been used as emulsifiers for water-oil blends, such as for the food or cosmetic industry, but recently have been also utilized for API particle-size reduction. The term colloid mill is sometimes used for these devices and is a technology dating from the early 1900s [13]. In addition to terminal milling of the API slurry prior to filtration, the wet mill can also be used to normalize a seeded slurry for a co-feed or reverse addition crystallization process to indirectly control the crystallized API particle size. In addition, rotor-stator wet mills operating at high tip speeds can be used for amorphous precipitation or direct crystallization (fast mixing and potentially shear-induced nucleation effects), where the precipitated particles are often smaller in size due to the high shear environment. In these cases, the mill is used as a high-shear mixing device.
For rotor-stator wet mills, the extent of particle-size reduction can be correlated to a suitable parameter for milling intensity and to the exposure of the slurry to the mill. The simplest parameter for milling intensity is the tip speed (in m/s) at maximum diameter. Holding tip speed constant is useful when scaling up and down to maintain similar conditions. More detailed considerations include accounting for the mill geometry through slot events [14], shear frequency [15], and a cumulative normalized energy input [16]. Exposure to the milling event relates to details of equipment and recycling through the mill, and is managed by monitoring the process versus time either in batch or recycle mode.
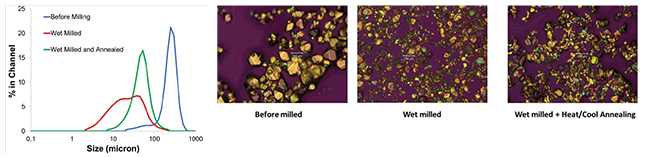
Figure 5. The graph (left) shows the particle-size distribution before wet milling, after wet milling and after heat/cool annealing. The micrographs (above) show the corresponding micrographs of the powders
Rotor-stator wet mills often generate fine particles via attrition, with consequent potential negative impact on the filtration rate, broadening of the PSD for less consistent BA performance, and formulation issues like tablets partially sticking to the presses (an elegance problem that could impact the dose if severe enough). We can add a post-milling heat/cool annealing of the API slurry, which utilizes the increased solubility of API at elevated temperature with Ostwald ripening (where smaller particles are preferentially dissolved and precipitated back out onto the remaining larger particles) to improve the PSD, by shifting the mean particle size upwards and narrowing the distribution and eliminating shoulders or other modes to create a monomodal Gaussian type PSD. Heat/cool annealing can result in more consistent PSD profiles and eliminate the troublesome fine particles (see Figure 5).
At high-tip-speed operations, the batch slurry can receive enough heat input from the wet mill to raise the exiting stream temperature significantly, followed by cooling once the batch stream returns to the feed vessel and is blended back with the bulk slurry. This results in a sort of real-time annealing effect that can sometimes eliminate fines right after formation, negating the need for a separate annealing step.
On the other hand, the temperature increase from high-tip-speed rotor-stator wet milling could cause too much annealing and partially offset the size reduction of the mill, so that the PSD does not reach the fullest possible reduction that the mill is capable of producing. Therefore, when wet milling at high tip speeds appropriate temperature control is an important consideration. Annealing can also smooth out the particle surface and “heal” defects caused by collisions or other mechanical impacts, resulting in surface areas that are significantly lower compared to dry-milled particles in the same size range and morphology.
Although the geometry and rotation of a rotor-stator wet mill imbues it with a pumping capacity akin to a centrifugal pump (has an almost linear pump curve and will “slip” instead of “dead head” and pressurize like a positive displacement pump), the inlet feed line to the mill can still be clogged if the pre-milling API particles size is too large, has high aspect ratio, high slurry concentration, poor mixing in the container vessel, or some combination thereof. One simple way to resolve potential feed-line blockage by API is to install a positive-displacement pump, such as a diaphragm pump, upstream of the wet mill, to force batch slurry to flow into the mill where it can be properly digested.
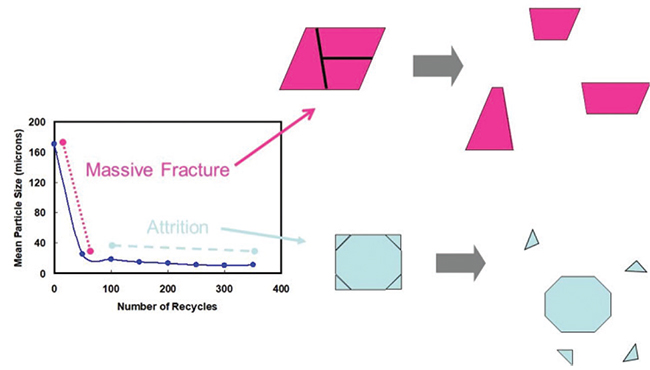
Figure 6. In wet milling, there are typically two different mechanisms at play, the massive-fracture regime and attribution regime, which are illustrated here
Another differentiation is the recycle versus single-pass movement of the API solids through the mill. Most wet milling, whether rotor-stator or media, is conducted in recycle mode, where the batch slurry is recirculated from the holding vessel through the mill, often for multiple batch turnovers, until the PSD reaches a pseudo steady-state minimum. At this minimum, there is a very slow decrease in the size, because particle fracture has stopped (likely due to the smaller particles now lacking sufficient inertia for effective force transfer to cause massive fracture). Then, the only remaining breakage due to weaker attrition related chipping and consequent fines generation (Figure 6) for a classic two-stage particle size versus batch-turnover plot, where initial steep drop in size in the “massive fracture” regime transitions to an shallow, almost flat regime driven mostly by the “attrition” mechanism.
The reason why multiple passes are required to complete wet milling is because particle breakage is dependent on the product of number of (breakage inducing) “events” and the breakage efficiency. Residence time considerations in the tank imply that recirculation is useful to ensure that all particles are exposed to a similar milling environment and time. Whether run in batch mode (in the laboratory) or a recycle mode (at scale), the general characteristics of the milling curve are retained with energy input versus particle size being a reliable method.
Other examples of wet mills with different mechanism of action are media mills, which use spherical beads made from ceramics, such as zirconia oxide, or polystyrene (PS), to reduce API particle size, often to one or two orders of magnitude smaller than the milling media. This mechanism involves a sort of grinding, polishing attrition type action, where again the dense and viscous liquid acts to lubricate the beads, as well as help to dissipate the frictional heat generated from the grinding mechanism. Cavitation mills, rarely deployed for API comminution, utilize yet another mechanism for generating mechanical energy, via dramatic pressure drop that causes cavitation. Extremely rapid evaporation generates transient gas bubbles, which then collapse violently to cause shock waves to propagate through the adjacent liquid phase to fracture the suspended particles.
As mentioned above, media mills utilize a grinding media made up of materials such as ZrO2 (often stabilized and hardened by yttrium) or PS to reduce the API PSD significantly, similar to the performance of jet mills. However, there are some practical issues with using media mills for API processing. The beads can still shed, especially in the presence of more abrasive API compounds. For Zr-based beads, elemental analysis can detect and quantify the amount of shedding in the milled API, but for “transparent” beads, such as PS, we lack a reliable method to detect any shedding contaminants, which poses a quality and safety issue, especially if the API is going to be an injectable or inhalant. Also, the milled API still needs to be isolated via filtration, where the very small particles with high surface area often form agglomerates during drying, causing a loss of effective PSD and surface area that defeats the purpose of milling.
A possible solution is to use media mills on the DP side for a suspension-type formulation. Another possibility is testing some variation of thin-film or wiped-film evaporation to drive off the solvents, while hopefully keeping the fine particles from clumping up and aggregating in the process (often the first step into formation of harder fused agglomerates upon drying). However, the agglomeration issue and bead-shedding issue tend to make media milling less attractive of an option for API size reduction.
Dry milling
“Dry” mills operate in a gaseous environment, usually an inert gas like nitrogen being either a carrier stream for the pin mill, or also providing the mechanical energy for the particle collisions, as in the case of jet mills. In the milling conditions, these gases are at significantly lower density compared to liquids and are also compressible, so there are much less viscous dissipation and dampening forces, allowing particle collisions — with other particles or the mill walls — to become the major particle-fracture mechanism. While this allows for more efficient energy usage, the particles also absorb most of the heat generated by the collisions, which could be problematic for crystals that either have a low glass-transition temperature ( Tg) (and thus could lose crystallinity or even turn amorphous), or desolvate, or convert to a different crystal form due to the temperature increase. Milling in a dry environment can also result in more static buildup on the particles, since inert gas isn’t an effective conductor or carrier of electrostatic charges that are created by the mechanical energy from the numerous collisions. Although most dry mills are constructed from relatively conducting metallic materials, some residual charge on the milled API particles could make them cling to the walls or clump together and become difficult to handle or collect.
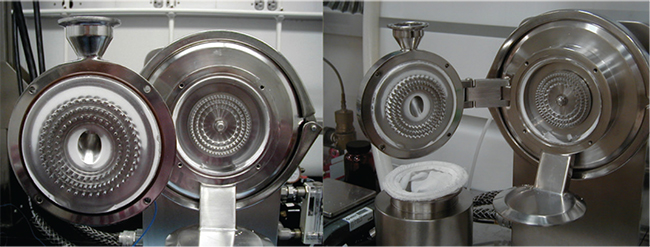
Figure 7. Two different views of a rotor-stator pin mill are shown here
The pin mill has metal pins on both the rotor and stator (Figure 7). And while the rotor spinning at high tip speeds will also cause a vacuum draw and pumping effect that, combined with centrifugal force, transport the particles suspended in nitrogen through the array of pins, the primary mechanism of action is particle collision with the pins, along with particles being imparted with mechanical energy from the pin and subsequently colliding with another particle in its path [17].
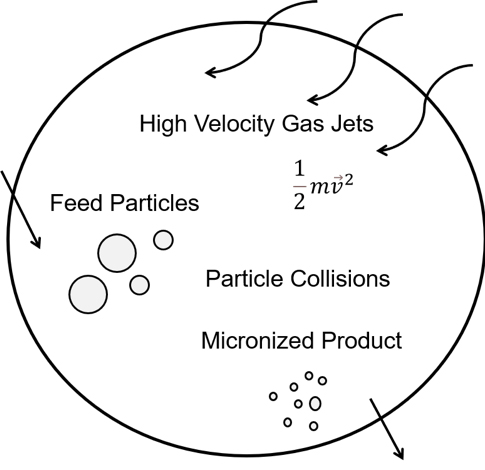
Figure 8. Inside a spiral jet mill chamber, feed particles are micronized by high-velocity collisions created by gas jets. The gas enters through nozzles at a pressure as high as 10 bars and with sonic velocities
In the dry mill category, jet mills utilize high-pressure gas streams to suspend and accelerate the API particles to cause particle-particle and particle-wall collisions (the latter evidenced by abrasive API crystals causing erosion and metals shedding from the product contacting internal mill surfaces) [18]. Although jet mill “raceways” are sometimes of different geometries (common examples are circular tracks for “spiral” mills (Figure 8); or an oval/bean shaped raceway for a “loop” mill, which, when scaled up, turns into a cylindrical tube formed into a “D” shape). Although the mill internal geometries, as well as the flow pattern and direction of the gas jets of the mill namesake differ, jet mills generally share the same mechanism of action. The particles in the jet mill continue to impact the raceway until they are small enough to traverse the path without wall collisions and then leave the mill.
The milling setup is dependent on the mill mechanism of action and the API suspension media. From an operational viewpoint, the largest discrepancy clearly lies between wet milling and dry milling. Wet milling is usually (but not always) conducted “terminally” — that is, after crystallization is complete, but in the post-crystallization API slurry (after which the milled API is usually isolated via filtration and then dried), like a conventional unmilled API batch. Thus, wet milling is a separate operation, but not a separate step. Dry milling is conducted on the filtered and dried API and therefore is considered a separate and discrete step from the crystallization step. It has a distinct product loss (mostly due to fines entrainment into dust bags and physical losses to the equipment internal surfaces and charging devices like hoppers) of about 5–10%, which is a significant yield-reduction that is hard to ignore.
Dry milling is often conducted in single-pass mode regardless of mill type, even if the different mill types are divergent in milling energy. It is difficult for dry mills to set up a recycle-type loop like that for wet mills, while conducting multiple single passes is operationally burdensome. Instead, the preferred strategy is to select a higher-energy dry mill like a pin mill or jet mill when a smaller size is required.
High-energy dry milling operations are routinely screened for metal leaching into the milled product, abrasion of the mill surfaces, and crystallinity of the resulting product. It is usually desired to retain crystallinity and a reduction in crystallinity on milling is unfavorable from a product property control point of view. Wet-milling techniques usually do not have these same considerations, a practical reason for why the wet-mill can be favored.
Concluding remarks
Milling active ingredients combines equipment selection, material characterization, and process characterization, with the aim of improving and controlling the properties of the solid crystalline drug substance. The basis for mill selection and operational conditions is typically a target size range defined by the biophysical properties, or a size range defined by processing considerations (for example, content uniformity) in blending downstream (or both). Various conditions are screened including variation in feed to define conditions, followed by larger-scale trials. Particle-size distributions and mill-energy input are the key metrics. The milling techniques are well described by their working fluid, energy input mechanism, and fluid mechanics design. Rotating mills can be scaled at a crude level using the tip speed at the maximum diameter, with more refinements depending on mill specifics. Non-rotating mills are described by the specific energy input relative to the solids feed, for example of the kinetic energy of the feed gas divided by solids feedrate.
Acknowledgment
All photos courtesy of Merck & Co., Inc.
References
1. U.S. Food and Drug Admin. (FDA), Guidance for Industry #169 – Drug Substance, www.fda.gov/media/69923/download.
2. Byrn, S. R., “Solid State Chemistry of Drugs,” Academic Press, New York, N.Y., 1982.
3. Powder Technology and Pharmaceutical Processes, Chulia, D., Deleuil, M., Pourcelot, Y., Eds., “Handbook of Powder Technology,” Elsevier, Amsterdam and New York, 1994.
4. Litster, J. “Design and Processing of Particulate Products,” Cambridge series in chemical engineering, Cambridge University Press, Cambridge, U.K., 2016.
5. Basset, D., Matteazzi, P., and Miani, F., Measuring the Impact Velocities of Balls in High Energy Mills, Materials Science and Engineering: A, 174 (1), pp. 71–74, 1994, https://doi.org/10.1016/0921-5093(94)91113-4.
6. Bonakdar, T. and Ghadiri, M., Analysis of Pin Milling of Pharmaceutical Materials, International Journal of Pharmaceutics, 552 (1–2), pp. 394–400, 2018, https://doi.org/10.1016/j.ijpharm.2018.09.068.
7. Vanarase, A., Aslam, R., Oka, S., and Muzzio, F., Effects of Mill Design and Process Parameters in Milling Dry Extrudates, Powder Technology, 278, 84–93, 2015, https://doi.org/10.1016/j.powtec.2015.02.021.
8. U.S. FDA, “The Biopharmaceutics Classification System (BCS) Guidance,” December 2017, www.fda.gov/about-fda/center-drug-evaluation-and-research-cder/biopharmaceutics-classification-system-bcs-guidance (accessed 2022-07-23).
9. Colombo, P., Traini, D., and Buttini, F., “Inhalation Drug Delivery: Techniques and Products,” Wiley-Blackwell, Chichester, U.K., 2012.
10. Tenchov, B. G., Yanev, T., and Weibull, K., Distribution of Particle Sizes Obtained by Uniform Random Fragmentation, J. of Colloid and Interface Science, 111 (1), pp. 1–7, 1086, https://doi.org/10.1016/0021-9797(86)90002-0.
11. Metta, N., Ramachandran, R., and Ierapetritou, M., A Computationally Efficient Surrogate-Based Reduction of a Multiscale Comill Process Model, J. Pharm. Innov., 15 (3), pp. 424–444, 2020, https://doi.org/10.1007/s12247-019-09388-2.
12. Kwade, A. A., Stressing Model for the Description and Optimization of Grinding Processes, Chemical Engineering & Technology, 26 (2), pp. 199–205, 2003, https://doi.org/10.1002/ceat.200390029.
13. Travis, P. M., Mechanochemistry and the Colloid Mill, Including the Practical Applications of Fine Dispersion, Chemical Catalog Co., New York, N.Y., 1928.
14. Harter, A., Schenck, L., Lee, I., and Cote, A., High-Shear Rotor–Stator Wet Milling for Drug Substances: Expanding Capability with Improved Scalability, Org. Process Res. Dev., 17 (10), pp. 1,335–1,344, 2013, https://doi.org/10.1021/op4001143.
15. Luciani, C. V., Conder, E. W., and Seibert, K. D., Modeling-Aided Scale-Up of High-Shear Rotor–Stator Wet Milling for Pharmaceutical Applications, Org. Process Res. Dev., 19 (5), pp. 582–589, 2015, https://doi.org/10.1021/acs.oprd.5b00066.
16. Engstrom, J., Wang, C., Lai, C., and Sweeney, J., Introduction of a New Scaling Approach for Particle Size Reduction in Toothed Rotor-Stator Wet Mills, International J.of Pharmaceuticals, 456 (2), pp. 261–268, 2013, https://doi.org/10.1016/j.ijpharm.2013.08.084.
17. Bonakdar, T. and Ghadiri, M., Analysis of Pin Milling of Pharmaceutical Materials, International J. of Pharmaceutics, 552 (1), pp. 394–400, 2018, https://doi.org/10.1016/j.ijpharm.2018.09.068.
18. Chamayou, A. and Dodds, J. A., Chapter 8: Air Jet Milling, “Handbook of Powder Technology,” Salman, A. D., Ghadiri, M., Hounslow, M. J., Eds., Particle Breakage, Elsevier Science B.V., Vol. 12, pp. 421–435, 2007, https://doi.org/10.1016/S0167-3785(07)12011-X.
Authors
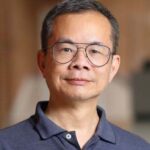
Ivan Lee
Ivan Lee is an associate principal scientist in the Process Research & Development division at Merck & Co., Inc. (126 E. Lincoln Ave, Rahway, NJ, 07065; Email: [email protected]). Lee has been in the Chemical Engineering Research and Development group since 2001. He has focused on API process development and clinical trial delivery support, in project teams as well as in specialty laboratories, such as the Crystallization Lab and Particle Engineering Lab. Lee is currently the head of the Unit Operations Lab and is a subject matter expert on kilogram-scale operations, such as wet and dry milling, crystallization, filtration and drying. Lee has worked on 1st GMP deliveries and crystallization process development for Merck projects, such as Sitagliptin, Doravirine, Ceftolozane, Gepaxipant and Molnupravir. He is the inventor of three patents, and the recipient of four Green Chemistry awards. He holds a Ph.D. in chemical engineering from the Massachusetts Institute of Technology (MIT), and a B.A.Sc. in chemical engineering from the University of California, Berkeley.
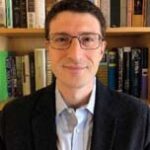
Eric Sirota
Eric Sirota is a senior principal scientist in the Process Research & Development division at Merck (same address as above; Email: [email protected]). Sirota has 19 years of experience at Merck developing chemical processes in the laboratory for pilot scale manufacture and commercial validation. He is the head of Merck’s Crystallization Lab, a group that designs crystallization processes with an emphasis on particle size and polymorph control, as well as impurity rejection. Sirota holds a B.S.Ch.E. degree from the University of Michigan.
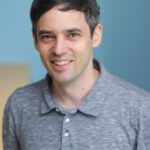
Aaron Moment
Aaron Moment is a professor of Practice in Chemical Engineering at Columbia University (500 W 120th St. New York, N.Y. 10027; Email: [email protected]). He maintains an active research program in sustainable and green manufacturing routes to fine chemicals and intermediates using molecular design principles. Moment currently chairs the N.Y. ACS Employment and Professional Relations Committee, and is an executive member of the AIChE (American Institute of Chemical Engineers) Particle Technology Forum. Moment’s previous experience includes process and development roles within the pharmaceutical industry, including with Merck & Co., and DuPont Pharmaceuticals. He has a Ph.D. in chemical engineering from MIT, and a B.S.Ch.E. degree from Rensselar Polytechnic Institute.