Advances in membrane technologies allow processors to delve into gas- and water-separation applications more effectively and efficiently
Conventional membranes have a reputation for being “finicky” and “high maintenance” because they don’t operate well under high pressures or temperatures, are subject to fouling and consume significant amounts of energy. However, growth in gas- and water-separation applications has led to the development of more robust membranes with higher fouling resistance and enhanced selectivity, both solving problems and opening avenues for new applications driven by sustainability trends, including a green gas economy and water conservation.
“Membrane systems get a bad reputation for being picky or needy with the water quality they are able to accept, as well as for fouling and scaling that leads to increased cleaning, frequent membrane replacement and, ultimately, unplanned downtime,” says Jared Galligan, director of engineering with Kurita America, Inc. (Minneapolis, Minn.; www.kuritaamerica.com). “But, as water conservation and reuse and other sustainability practices become standard operating procedure, membranes will be playing a bigger role, so current users are demanding more robust and reliable operation from their membrane systems, and providers of membranes and membrane systems are working on developments to support these needs” (Figure 1).
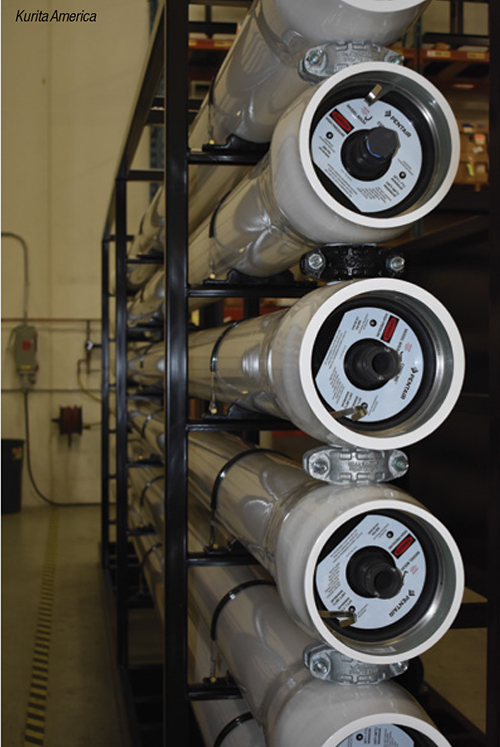
FIGURE 1. As water conservation and other sustainability practices become standard, membranes will be playing a bigger role. Providers of membranes and membrane systems are developing more robust and reliable components and systems
Innovating for robustness
“In many applications, especially in gas separations, the membrane requires an enormous robustness,” explains Goetz Baumgarten, vice president of membranes at Evonik Industries AG (Essen, Germany; www.evonik.com). “Membranes for these types of applications are made of high-performance polymers, which offer fantastic gas-separation abilities. But if you have separation of natural gas where conditions of high temperatures, high pressures and organic liquids are present, you need membranes that can operate under these harsh conditions.”
Baumgarten says more robust membranes are becoming essential as we move toward a sustainable gas economy because they are needed for applications in hydrogen extraction and other green-gas processes. And, Evonik, he says, is developing membranes for these types of applications (Figure 2). “For example, we identified the need to extract hydrogen from natural gas grids because as the world heads towards a hydrogen economy, we need the ability to transport hydrogen in its own pipeline systems in the future,” says Baumgarten. “However, currently, most of the globe uses natural gas pipeline grid infrastructure. To take advantage of the existing infrastructure, we partnered with Linde Engineering [Pullach, Germany; www.engineering.linde.com] to develop hydrogen-extraction technology, which enables existing infrastructure to transport hydrogen next to natural gas and extract the hydrogen where it is needed at a grade that is required by the customer.”
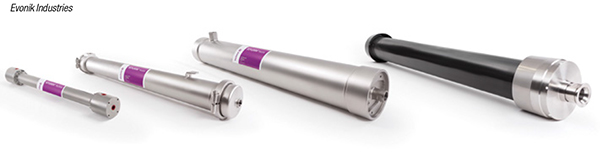
FIGURE 2. More robust membranes are becoming essential as we move toward a sustainable gas economy because they are needed for applications in hydrogen extraction and other green gas processes. Evonik is developing membranes for these types of applications
This technology is a combination of Evonik’s membrane technology and Linde’s pressure-swing adsorption (PSA) technology. Linde recently launched a full-scale pilot plant in Dormagen, Germany, to demonstrate how hydrogen can be separated from natural gas streams. The process is a key enabler for scenarios in which H2 is blended with natural gas and transported via natural gas pipelines. The blended gas can consist of between 5 and 60% H2. Membranes are then used to extract H2 from these natural gas streams at the point of consumption. The resulting hydrogen has a concentration of up to 90%. When further processed with Linde’s PSA technology, a purity of up to 99.9999% can be achieved.
The high-performance membrane package unit is based on a robust polymer developed by Evonik. It consists of highly selective hollow fibers that efficiently separate the H2 in the blended natural-gas stream from the main components of methane and higher hydrocarbons. The membrane material is particularly robust, as natural gas contains a host of other substances that can influence the separation performance of membranes.
Evonik is also working on innovative polymer membranes for water electrolysis that can help make green H2 more affordable. Green H2, which is critical for use as a carbon-free fuel for industry and transportation and as a raw material for the chemical industry, is produced from water by electrolysis using electricity generated from renewable resources. It is still much more expensive than conventional H2, which is generally obtained from steam-methane reforming, a process that releases CO2. In addition to sufficient low-cost energy generated from renewables, investment in an electrolyzer is a key factor in cost-efficient production of green H2.
Evonik has developed a new anion-exchange membrane (AEM), which should contribute to the breakthrough of electrolytic production of H2. “Electrolysis featuring anion-exchange membranes has benefits over other electrolytic processes such as conventional alkaline electrolysis using diaphragms (AEL) or the more recent method of proton exchange membrane electrolysis (PEM), which is dependent on raw materials such as precious metals. “Because the anion-conducting membranes work in a caustic versus acidic environment, standard 316 stainless steel can be used in the electrolyzer,” says Baumgarten. “In PEM electrolyzers, precious metal-plated and rare-earth metals are needed, the expense of which could limit the future of a H2 economy. This development featuring our anion conducting membrane systems will be launched next year and move us closer to a H2 economy.”
Likewise, the trend toward sustainability regarding water conservation and reuse is driving the need for membranes that can withstand higher temperatures and pressures. “As chemical and other processors try to conserve water, they are wanting to reuse water that traditionally would have been sent to treatment facilities,” says Erik Hanson, director of global product management and strategy, with SUEZ Water Technology & Solutions (Trevose, Pa.; www.suezwatertechnologies.com). “Traditionally reverse osmosis (RO) and nanofiltration (NF) have been used for many years for treating water coming into plants and existing membranes worked well for those applications. But when you are using water that has gone through one or more industrial processes, it has things in it that are perhaps less predictable than what you find in intake water, so in reuse and zero-liquid-discharge (ZLD) applications, we are seeing more innovation in membrane technologies to enable these separation processes.
“This type of water might have more extreme pH or the temperature might be higher than what you would start with in a typical RO treatment, so today’s parameters are taking us beyond what the RO elements of a decade ago would be able to handle,” continues Hanson. “There is a lot of innovation for spiral-wound elements that are making them more resistant to high temperatures, pH levels and higher pressures” (Figure 3).
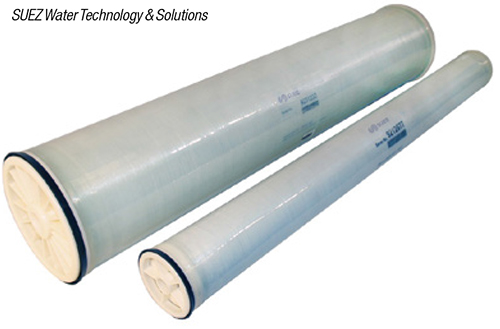
FIGURE 3. SUEZ is developing spiral-wound elements that are more resistant to high temperatures, pH levels and higher pressures
For example, as salt concentrations get higher and processors need to operate at higher pressures to recover those salts, SUEZ’s Industrial RO5, RO6 and RO7 elements can be used. “These elements are made with special membranes and special element construction to provide high rejection of salt at higher-than-average brine concentrations and pressures,” says Hanson.
In other cases, industrial processes may make water acidic. Purifying or concentrating those acids requires a membrane element that can be continuously operated at low pH. “Our Duracid membrane element can continually operate in the 2 to 3 pH range, helping processors reuse water without having to do a lot of pH adjustment prior to treatment,” Hanson continues. “If you didn’t have an element like this and you wanted to purify an acid stream to enable water reuse, you would first have to neutralize it, which means adding a lot of caustic at a significant expense. The development of a membrane that can operate at low pH avoids that neutralization, saving time and expense.”
Overcoming fouling
Since fouling and scaling have long been a major challenge with membranes, several manufacturers are working on improvements that will help processors reduce their environmental footprint and often enable the use of membranes in applications where it may not have been previously possible.
“Fouling is one of the most common and severe problems in the operation of RO systems. Unchecked, it causes significant operational problems such as frequent interruption, damage to the membranes, intense chemical and energy use and regular cleaning-in-place of the RO and the pressure exchangers,” says Tina Arrowood, principal research scientist with DuPont Water Solutions (Edina, Minn.; www.dupontwatersolutions.com). “The bottom line is far less water produced for the money operators spend on capital assets and operations.”
The company is currently producing its fourth-generation fouling-resistant membrane technology, which reduces the need for cleaning by as much as 50% for wastewater reuse applications for industries including petrochemical, coal-to-chemical, paper and pulp, microelectronics and textiles.
Kurita is also working to reduce fouling in cooling-tower water treatment, helping reduce water use and expenses, via its Cooling Tower Blow Down Recovery System (CTBR). The technology recovers a higher rate of tower blowdown water, conditioning it and returning it to the cooling tower system, minimizing the operating costs of acquiring fresh water and discharging blowdown as wastewater. The approach combines chemicals, equipment and service. While many other systems face continued fouling issues of the filter media and membranes, decreasing the total recovery rate of the system and increasing water use, Kurita’s CTBR solution effectively removes suspended solids in cooling water, inhibiting fouling, decreasing water use and maximizing the recovery rate of tower blowdown for a more reliable operation.
Also interested in reducing fouling and striving for energy conservation, Aqua Membranes (Albuquerque, N.M.; www.aquamembranes.com) has developed a new manufacturing method for the production of RO and UF membrane elements. “Membranes require frequent cleaning due to their construction,” says CEO Craig Beckman. “The layers separating the membrane where fluid flows are separated by a net material constructed of extruded polypropylene. While that net creates turbulence in the membrane that is designed for the feed flow to come through, it is also the part that scales after separation has taken place, necessitating cleaning. What many people don’t realize is that the energy associated with cleaning the membrane is a significant percentage of the energy required to run it.”
He continues to say that Aqua Membranes constructed a membrane element using printed spacer technology that does not include the netting element, reducing fouling and pressure drop, thus providing energy savings. The Aqua Membranes product features a customized 3D-printed pattern on the membrane to reduce fouling and wasted pressure (Figure 4). “We use flat sheet membrane purchased from a supplier as our printing substrate and run it through our patented printing process. We end up with brail-like dot and line patterns on the membrane surface. This pattern covers only 2 to 3% of the membrane, but it’s enough to create the flow channels and customize the flow through the system, resisting fouling and providing energy savings because less cleaning is needed,” he says.

FIGURE 4. The Aqua Membranes product features a customized 3D-printed pattern on the membrane to reduce fouling and wasted pressure
Dynamic membrane systems that reduce fouling can also be an enabling technology for many applications, says Greg Johnson, CEO and co-founder of New Logic Research (Minden, Nev.; www.vsep.com). “Conventional spiral-wound membranes have a very tight space between the membranes and use high laminar cross flow to pump liquid through a filter at a high rate of speed to create shear at the membrane surface. But as the membrane allows water to pass, the solids are left behind and congregate at the membrane surface, causing scaling and fouling. This is known as concentration polarization,” Johnson explains. “Using our Vibratory Shear Enhanced Processing (VSEP), we developed a fouling-resistant membrane filtration system that vibrates the membrane using resonance, which creates high shear at the membrane surface, improving fouling resistance by preventing congregation of the salts at the membrane surface” (Figure 5).
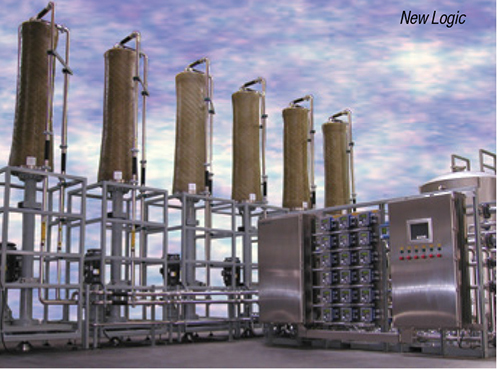
FIGURE 5. Using Vibratory Shear Enhanced Processing (VSEP), New Logic developed a fouling-resistant membrane filtration system that vibrates the membrane using resonance, which creates high shear at the membrane surface, improving fouling resistance by preventing congregation of the salts at the membrane surface
This unique method has allowed the use of membrane systems in many viscous or other applications where it may not have been possible to use membranes or other separation technologies in a cost-effective way, notes Johnson. “Often in challenging separations, our equipment is the enabling technology that can allow separations or purification that would not otherwise be possible,” he says. “While some of our applications are in the chemical processing or purification industry or the industrial wastewater industry, we have a lot of projects installed treating biogas effluent. In these applications, processors take organic material like manure or food waste and digest that in an anaerobic digester where methane is extracted and sold as a gas, but they are left with effluent that must be treated and our membranes can help with that. We also treat leachate from landfills and help other companies achieve zero- or minimal-liquid discharge.”
Increased selectivity
“One of the biggest challenges in membrane-separation technology is to break through the trade-off between rejection (selectivity) and permeability. In other words, achieving a process that enables the required water quality to be obtained with lower energy consumption and cost,” says Tatsuya Tamura, general manager of the water treatment division, RO membrane products department, with Toray Industries (Tokyo, Japan; www.toray.com). “The performance of water treatment membranes depends on the separation target-size sieve, the membrane surface charge and the interaction with the substance to be separated.”
One recent development is the improved performance of membranes for the removal of both small neutral molecules and ionic substances, such as dissolved organic matter and silica while maintaining water permeability. Toray has achieved this performance improvement by precisely controlling the size of micropores, such as molecular gaps in RO membranes and by improving the structure of the folds on the surface of separation membranes with its TBW-HR series of ultra-low-pressure RO membrane elements. Impurity rejection with these membranes exceeds that of existing ultra-low pressure RO membrane elements (Figure 6).
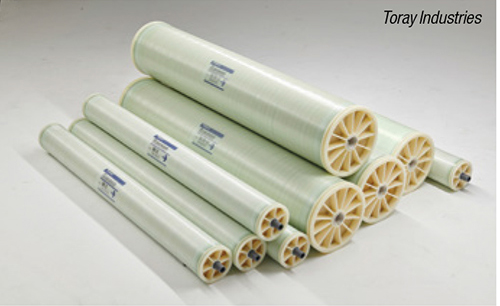
FIGURE 6. Toray achieved performance improvement by precisely controlling the size of micro pores, such as molecular gaps in RO membranes, and by improving the structure of the folds on the surface of separation membranes with its TBW-HR series of ultralow-pressure RO membrane elements
As demand for purer water has risen in the electronics industry, a key prospective benefit of these new membranes is purification of higher-quality and higher-purity water, enabling the production of semiconductors with finer wires as increasingly compact and complex semiconductors are needed for new applications.
In addition to meeting a demand for new applications, innovations in RO element selectivity are also helping with sustainability efforts. DuPont recently launched a new portfolio of RO elements, FilmTec Prime RO, for the treatment of brackish water in industrial applications (Figure 7). These elements require up to 20% less energy while improving permeate quality by up to 60%. “Analysis using U.S. Environmental Protection Agency tools indicates that the positive sustainability impact of FilmTec Prime RO, which has the potential to reduce global CO2 emissions by approximately 85,000 metric tons each year (based on global adoption), is equivalent to the emissions generated by an average car driving 211 million miles,” says DuPont’s Arrowood. “This global sustainability impact is delivered while retaining compatibility with existing brackish-water RO treatment systems, allowing operators to upgrade easily and secure the benefits of the technology,” she continues.

FIGURE 7. DuPont’s FilmTec Prime RO membranes for the treatment of brackish water in industrial applications require up to 20% less energy while improving permeate quality by up to 60%
“As water conservation and reuse and other sustainability-based applications continue to grow, flexibility and new features in membrane technologies, as well as the ability to tailor membranes to remove a specific contaminant or operate under unusual pressures or temperatures, will enable us to push them harder to meet the needs of processors. These advancements will be key for those looking to improve their water or energy footprint,” says Kurita’s Galligan.