The case examples presented here show that proper planning, communication and execution of tasks can add value and reduce unintended negative consequences for many capital-intensive projects
Materials management means something different to different groups of people. For the engineering and construction (E&C) industry, the Construction Industry Institute (CII; Austin, Tex.; www.construction-institute.org) [ 1 ] defines materials management as “a complex and comprehensive process involving people, organizations, technologies, and processes that manage the definition, source planning, quantification, supplier qualification, purchasing, supplier quality assurance and quality control (QA/QC), expediting, transportation, logistics and control of materials and associated information across the life cycle of a capital project” (Ref. 1, p. v).
In the 30 years since the E&C industry first began focusing on materials management as a concept, the practice has evolved and continues to evolve. As E&C contractors face challenges to remain competitive in a dynamic marketplace, a lightly structured materials-management organization that functions as a coordinating resource provides a vehicle to facilitate the delivery of lowest possible total-installed-cost (TIC) facilities. And — if thoughtfully structured within the overall E&C organization — a thoughtful materials-management framework can be the most effective tool that the E&C project management has to support all business objectives.
Discussed below is one example of how a materials-management organization should be structured to optimize materials-related work processes in an evolving environment. The discussion shows how proper materials-management effort can help an organization to add value and defray unintended negative consequences (Figures 1 and 2).
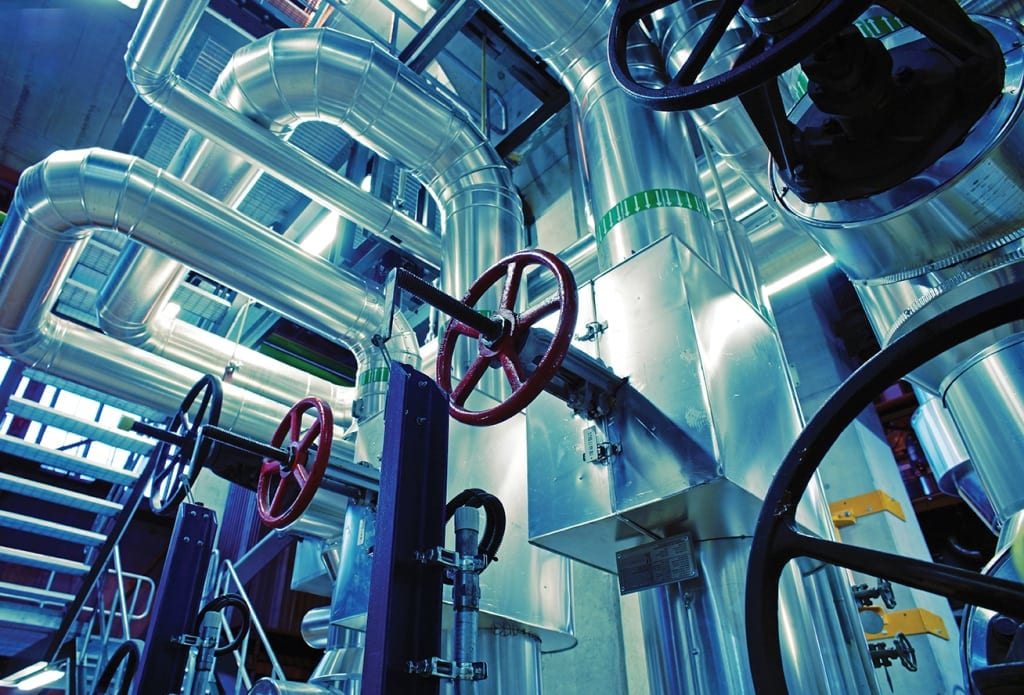
Figure 1. By establishing a well-developed materials-management organization to coordinate the management of resources involved in capital-intensive engineering projects, chemical process industries (CPI) facilities can both reduce the facility’s total installed cost and support all business objectives
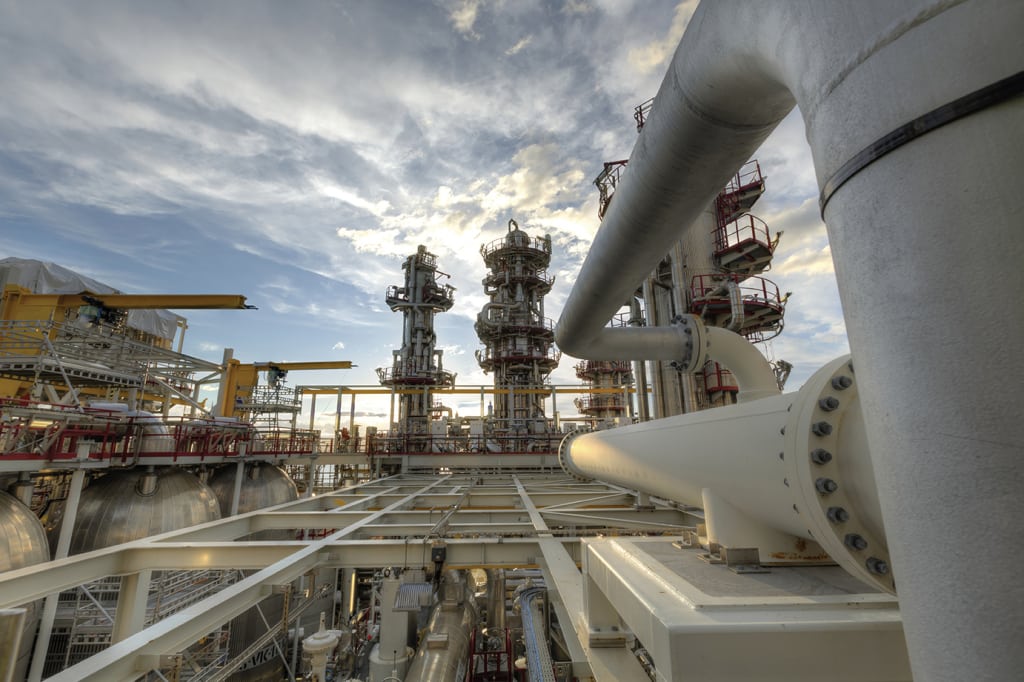
Figure 2. To be most effective, the materials-management framework should strive to break down silos and function independently of the procurement department, to ensure that the efforts remain focused on the overall objectives and not simply focused on material transactions
Key activities
In Ref. 1, p. 17, CII articulates the key materials-management activities as the following:
- Materials-related requirements planning
- Project-acquisition strategies
- Purchasing and subcontracting activities
- Expediting activities
- Supplier-quality management
- Transportation and logistics actvities
- Site-materials management
- Planning for operations and maintenance turnover
Further details can be found in in additional CII publications [ 1–5 ].
Scope and breadth
To facilitate the lowest TIC, materials-management planning and activities need to be “cradle-to-grave,” “cross-functional” and assertively proactive. In terms of cradle-to-grave, this means the materials-management team engages at the earliest phases of project planning, and continues, actively engaged, until all materials-related issues on a project have been addressed, resolved and dispositioned.
In this context, cross-functional means that the materials-management team addresses every function within project execution that involves project materials, specifically the following:
All engineering disciplines
- — This includes activities related to civil, structural and mechanical engineering, piping, electrical, instruments and architectural considerations
Procurement activities (as organized by the E&C company)
- — This involves purchasing, expediting, ensuring supplier quality, and managing traffic and logistics
Construction activities
- — This involves field engineering, receiving, warehousing and withdrawal
Startup and turnover
- — This includes the materials that are “permanent plant” (meaning they will become part of the physical plant); those that are temporary (those that are used and scrapped during construction); and spares that are used in installing, commissioning or operating the facility
Most important is the need for the materials-management organization to be assertively proactive — not just proactive, but assertively so; this is discussed in detail below.
Organization and reporting
Within the E&C industry, some organizations have chosen to simply re-describe or re-characterize their procurement organization as materials management. But historically, materials-requirements planning and project-acquisition strategies typically involve a substantial amount of engineering. Site-materials management and planning for operations and maintenance turnover typically involve the construction, startup and turnover organizations. The act of simply re-describing the “procurement function” as “materials management” subverts this broad process and underestimates the contributions that both the engineering and construction infrastructure have to offer. Accordingly, the most effective materials-management organizations are operated independently of the engineering, procurement, or construction organizations, and operate as a non-transactional organizing resource, reporting directly to project management.
Similarly, we need to emphasize the need for the materials-management organization to be non-transactional and silo-free. The engineering, procurement and construction organizations are often described as silos, as are many of the individual disciplines or sub-functions. These silos are typically individual cost centers within the E&C organization and execute transactions. For instance, engineering disciplines produce drawings and data sheets; the purchasing group produces purchase orders (POs); the traffic and logistics organizations execute orders for transportation.
These cost centers are driven by project management to optimize individual work processes. However, while each needs to be as efficient as possible, they often optimize their processes to the detriment of inter-related disciplines or functions. This negative activity often leads to the formation of silos that isolate individual groups or functions. As discussed below, materials-management organizations that take on transactions or constitute a silo are at risk of becoming part of the problem instead of part of the solution; specifically, if the materials-management organization starts to do work (such as carrying out transactions) that should be done by an engineering or procurement discipline, they tend to become an entity unto themselves — instead of simply coordinating the effort and seeing that the responsible disciplines execute their duties.
Automation: An optimizing tool
The CII definition of materials management [ 1 ] incorporates concepts such as “technologies…processes… and control of… information.” Today, the same evolving automation landscape that is transforming how E&C contractors design and construct CPI facilities has the potential to play a pivotal role in how materials are managed. Materials-management staff must not only be conversant with specific materials-related processes across the engineering, procurement and construction functions, but also conversant in automation-related tools and technologies. This knowledge must not be limited to automation-related tools and technologies that are utilized specifically within the particular E&C enterprise — whether internally developed or commercially purchased. Ideally, this should also extend to a working knowledge of automation tools used by partners, suppliers and clients, as well as trends and emerging automation-related technology developments. Such broad-based knowledge allows the materials-management organization to identify nascent opportunities for optimization, and to coordinate project-specific work process improvements early in project execution — while the potential to capture the benefits still exists.
Project landscape
So why is all of this important? Despite the best efforts of all E&C contractors, clients and manufacturers to standardize facilities, work processes and products, the project landscape is constantly evolving. Underlying facility processes evolve or incorporate new technology; manufacturers improve and change products; project sites differ; logistical challenges vary site by site, depending on available infrastructure; brownfield projects differ from greenfield projects; new suppliers appear from emerging-economy countries; and many minor parameters change from project to project.
While E&C contractors strive to maximize the use of standardized off-the-shelf materials, the nature of most facilities requires an extensive amount of customized equipment and materials (Figure 3). As such, the design process is often described as a series of successive approximations, changing as the engineering disciplines and suppliers interact and react to finalize design. So every individual project presents new and varying challenges, each of which, if addressed in a timely manner, offers opportunities to lower TIC, or conversely, can negatively impact TIC if not properly managed.
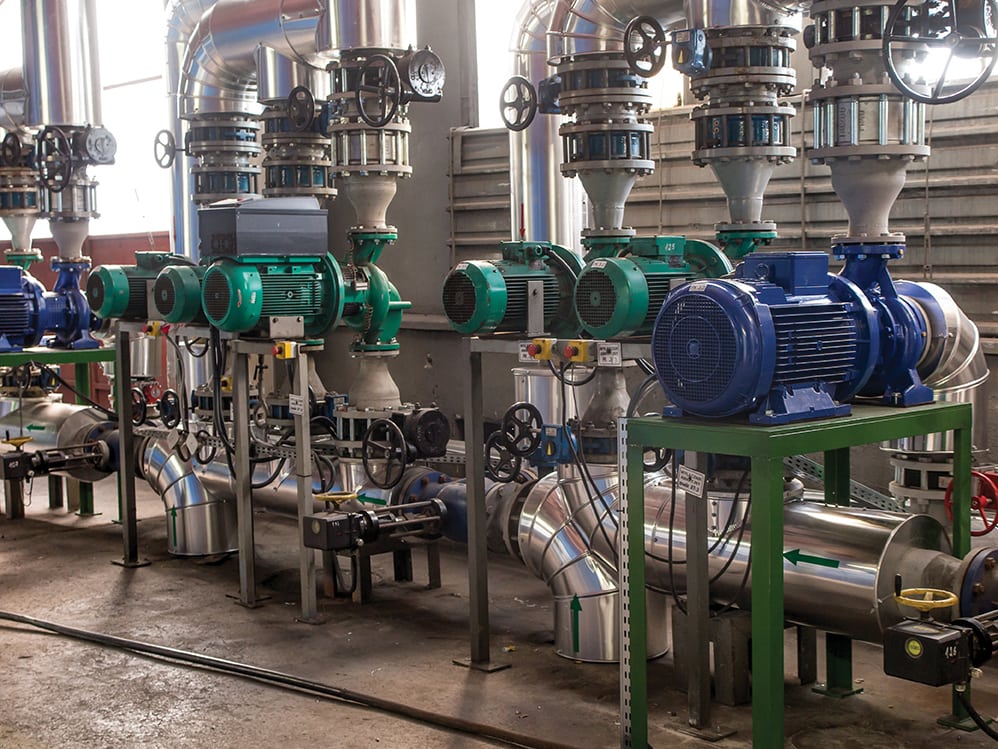
Figure 3. Capital-intensive CPI projects typically involve a mix of off-the-shelf and customized equipment components and systems, which adds complexity to the overall materials-management process
Materials-management skillset
The scope and scale of major projects these days require E&C contractor organizations to be highly specialized. Design engineers often struggle to comprehend how many of the facilities on the project they design will be erected. Construction engineers and superintendents often lack knowledge of many design parameters that impact and complicate the design. Purchasing and expediting staff often lack the ability to fully visualize or comprehend the complexity of the materials they order and expedite. And automation support staff often understand data flows among interacting automation tools, but do not fully understand the underlying work processes.
The best materials-management organizations employ personnel who have a range or general knowledge of all processes and automation tools but are not specialists in any, except by chance. Staffing levels needs to be consistent with the ability to identify opportunities for materials-related, work-process enhancement, in order to coordinate work-process modifications where justified, to monitor work-process execution, and to identify negative trends. Personnel can be drawn from all disciplines — including engineering personnel, such as design engineers; procurement experts (such as buyers, expeditors and inspectors), construction (staff such as field engineers), warehouse staff, and more. But most important is that the materials-management organization is managed by a materials manager who is conversant in all processes, including the design office, construction site and supplier processes.
The benefits of being proactive
Individual disciplines or functions (silos) will, by nature, work to optimize their individual processes, often unaware that internal process modifications related to materials work may negatively impact other disciplines or functions. Also, opportunities may exist within an individual discipline or function that offer noteworthy savings in other disciplines or functions, and the owning discipline may not be aware.
A knowledgeable, involved materials-management organization that is proactively monitoring project development will recognize, capture and implement materials-related process enhancements. Conversely, it will also work to deflect and defray downstream costs in cases where an upstream discipline or function is about to modify an internal process that is unaware of downstream materials impact and costs. And since most work-process modifications tend to be in some way related to automation, this emphasizes the need for the materials-management organization to be knowledgeable of discipline/function functionality (in terms of what activity a set of software executes) within the E&C, as well as supplier functionality, and evolving automation trends. Often an upstream discipline or function will possess information within an automation tool or system, or have the ability to enhance upstream information at relatively minor impact; if passed to downstream disciplines or functions, such advances often provide opportunities for significant downstream cost savings.
Gap removal versus gap filling
In an evolving environment, materials-management work processes evolve and gaps develop. An assertive, proactive materials-management organization will work to close or eliminate those gaps within existing disciplines or functions, as far upstream as possible. Those disciplines and functions will, by nature, tend to resist adding additional duties and transactions, particularly when project management refuses to provide the additional resources needed to do so.
Reactive and passive materials-management organizations tend to close those gaps by “filling” the gap — that is, by taking on the additional transactions themselves. While there may be limited cases that justify this, they need to be exceptions, and not be undertaken in a way that creates an independent structure or silo within the E&C organization. A gap that is filled as opposed to closed organizationally tends to add overhead and unnecessary cost, particularly, in cases where an upstream work-process modification may offer an opportunity to close the gap altogether.
Consider some specific examples. We’ll take a look at three different situations, each exhibiting a different class of materials-related issue that can develop on a project where less-than-optimal materials management was executed. Then we’ll look at how an assertive, proactive materials-management team could have added value.
Example 1. Minor protocol variations delay construction. For many process plants, piping systems constitute a major portion of the plant, and the piping design, supply, fabricate and erect process is not only almost always on the critical path, but constitutes one of the most complex work processes the E&C contractor faces (Figure 4). Unique pipe, fitting, and valve combinations (in terms of type, metallurgy, pressure rating and size combinations, or individual products) can involve quantities in the thousands, with the actual item count in the hundreds of thousands, spread over tens of thousands of construction drawings. Fortunately, experienced E&C contractors have developed sophisticated protocols and procedures to address this complex process. Even minor deviations can have a serious impact on construction.
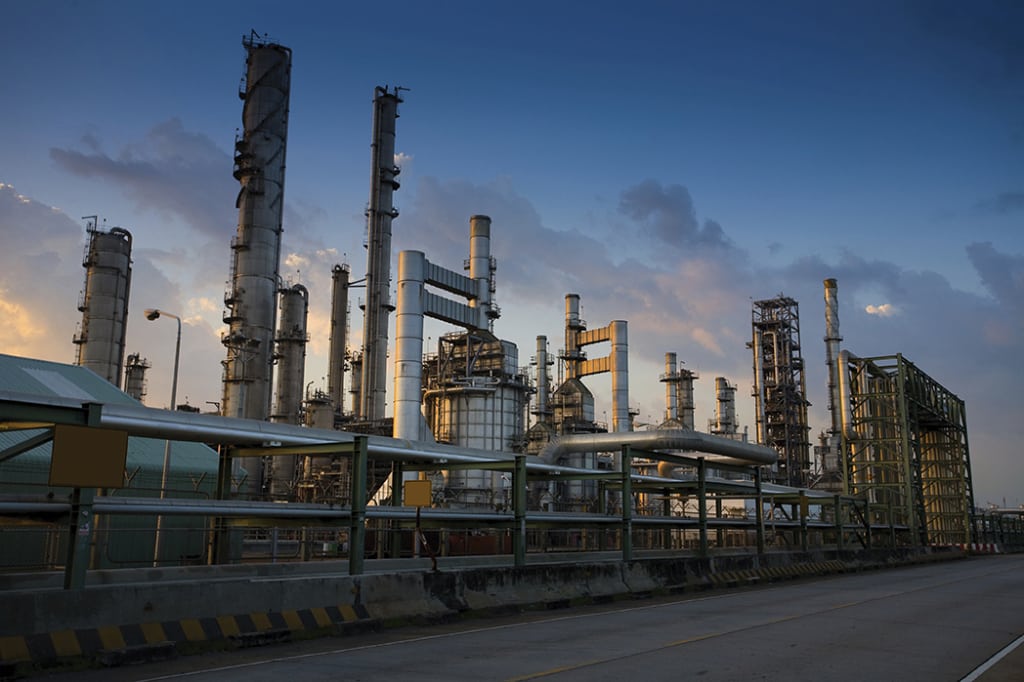
Figure 4. Piping design, supply, fabricate and erect process constitutes one of the most complex work processes the E&C contractor faces. The use of a consistent, sophisticated management protocol is essential for success
On a recent gas-plant project, the engineering team encountered some piping in a size range that was larger than normal. The team chose to modify the normal requisitioning protocol, using the mechanical team to requisition some piping components (a function that the piping team normally completed). In doing so, the mechanical team failed to follow the consistent component identification (ID) protocol used by the piping team — unaware that downstream protocols relied on upstream consistency. The components were purchased and shipped to the pipespool fabricator, but figuratively speaking, they were lost in the thousands of details that the materials-management system must track because they possessed a different component ID than the construction drawings.
This large-diameter piping required careful construction planning, utilizing limited cranage resources at the site. When the construction team began detailed planning two months ahead of erection, it came to light that several critical pipespools had not been fabricated, as the materials-management systems had been assigning a status of “short of materials” due to the inconsistency in component ID assignment. Upon closer examination, the misidentified items were physically located at the fabricator, and the pipespools released into fabrication. Unfortunately, these pipespools had a ten-week fabrication cycle and, due to challenges in the logistics at the site, an additional ten-week shipping cycle. The pipespools finally arrived, 12 weeks late, and the construction team was forced to reschedule significant erection work to accommodate modified crane usage.
Example 2. Major mechanical POs are poorly managed by procurement. At many facilities, the E&C contractors deliver major sub-processes where the suppliers are employed to deliver not just equipment, but also to design and guarantee many sub-systems. Examples include bulk- materials-handling facilities in smelters, conveyor systems on concentrators, and onsite manufacturing facilities, such as casthouses and anode rodding shops. These complex POs can entail tens of thousands of individual components and associated delivery lines or data records in the materials-management system — typically ranging into tens or even hundreds of millions of dollars. For such POs, procurement organizations tend to be the weak link. While design engineers and construction staff may be technically versed on the specific components of the PO, often the expediting staff is overwhelmed and fails to manage delivery information in the materials-management system to provide useful planning information. In the worst cases, shipment information is so poorly coordinated that site warehouse staff is unable to associate the physical shipment with the data in the materials-management system, and delays in the receiving process create delays for installation.
Example 3. Structural steel fabrication sub-processes are not timely managed. Almost all CPI facilities involve structural steel (SS). The process to design, supply, fabricate and erect SS is another complex materials-management undertaking, but not nearly as complicated as that required for piping. The process for steel is generally organized so that the fabricator handles most of the supply process, and often executes detailing. Project scope can range from 5,000 to 50,000 tons or more.
On a project involving a PO with a scope of 10,000 tons of SS, the E&C engineering organization designed the structure using 3-D modeling software and delivered that model to an SS fabricator for detailing and delivery. Detailing entailed approximately 50,000 individual piecemarks (individual pieces of fabricated steel).
The structure was broken into about 50 sub-structures, or areas, within the model. For each area, the E&C engineering organization transmitted individual area models. Execution involved fabricator-detailed design and submittal to the E&C engineering organization, review and approval by the E&C engineering organization, release into fabrication by the fabricator, and subsequent delivery of the individual piecemarks to the jobsite. Each of these 50 area scopes involved approximately 1,000 piecemarks, and within the process was a data-delivery sub-process integrated into the materials-management system.
This data-delivery process captured 25 or more individual piecemark attributes (including component ID, description, weight, length, cost code and more) that the E&C contractor used to validate design, manage the steel, pay the fabricator, manage erection of the steel and so on. All POs involve some degree of supplier submittals, depending on the subject matter. SS-fabrication POs with detailing typically involve an extensive submittal process, with each piecemark drawing requiring review. E&C contractors typically use a review process that allows some fabrication to proceed, subject to conditions, with one common mode being released subject to incorporation of minor comments.
Meanwhile, the area data-delivery process required a submittal unto itself, with the E&C engineering organization feeding the materials-management system with these data. Both the E&C engineering organization and the fabricator were slow to finalize these area data submittals — so slow, in fact, that steel was being fabricated and shipped to the jobsite before the data were fed into the materials-management system. The net result was that many shipments of steel could not be “received” in the material-management system upon arrival at site, and this significantly impacted both warehouse operations and construction operations. The situation reached a level where an SS installation contractor filed a claim for delay, while tons of steel needed for erection sat in the laydown area, with the E&C contractor unable to “issue” the steel to the contractor, due to data-related issues.
Opportunities for improvement
Now let’s review each of these three specific opportunities to see a proactive materials-management organization can add value.
Opportunity 1. Material-management review of POs, material requisitions (MRs), and extra-charge approval requests (ECARS). In the example noted above, project management failed to comprehend the value that a cross-functional materials-management team could offer, and did not fully support the materials-management team — often siding with an engineering organization that portrayed the materials-management team as making recommendations that offered little apparent value. For the piping process, issues arise almost daily that can lead to a serious unintended consequence, such as the delays described in this example. A competent materials-management team —one that has the attributes described above, the support of project management, and the work process knowledge and vision to see downstream issues — can help to avoid many of these problems. One way to integrate this knowledge is to require the materials manager to review and sign off an all MRs, POs, or ECARs. Adding such a requirement can help to reduce many of the issues mentioned above.
Opportunity 2. Provide materials-management assistance to the procurement organization.As noted in this example, procurement — generally the expediting organization — is the weak link in the chain for these complex POs. Expeditors do not generally possess the technical knowledge needed to understand how many of the components of these large POs will ship, or the significance of separate shipments of individual components. Also, expeditors are generally unaware of how the jobsite intends to manage materials — for instance, will each shipment be direct-issued to construction on receipt, will all items be received into the materials-management system and stored and issued to the construction department as needed and requested by the construction department and so on. Many E&C contractors fail to recognize the inefficiencies in their construction and warehouse operations. Such inefficiencies result from poor delivery information (incurring unnecessary costs in additional jobsite warehouse operations), and poor use of construction craft (due to less-than-optimal planning).
This represents a major opportunity for a knowledgeable materials-management team to work with the expediting team, coordinate with the jobsite, organize the shipments, and manage data in the materials-management system, to leverage information that will both facilitate construction planning and optimize warehouse operations.
This represents a major opportunity for the materials-management team to bridge the gap. With some technical knowledge of the subject matter, interaction with both engineering and construction personnel, and close contact with the warehouse operations, a materials-management team can and should involve itself early with the expediting effort to facilitate planning of shipments and development of data in the materials-management system. This will support overall improvements in construction planning and optimization of warehouse operations.
Opportunity 3. Minor intervention in the SS process.In this example, the submittal process, which fed the materials-management system and was pivotal to efficient jobsite operations, took a back seat to shipment from the fabricator. Here, the procurement organization was optimizing the important milestone of shipping the steel from the fabricator, but failed to comprehend the impact of missing data in the materials-management system — to the extent that it significantly and detrimentally impacted jobsite operations. The materials-management team recommended a simple solution — the release of steel from the fabricator for shipment should require verification by the E&C supplier quality team at the fabricator, and that all steel data related to a given shipment be captured in the materials-management system. Failure to do so caused trucks to back up at the fabricator’s facility, underscoring the importance of timely execution of the submittal process, which the fabricator corrected almost overnight. The net result of making this procedural change was that subsequent steel deliveries were all entered into the materials-management system at the jobsite at the time of delivery, making the steel issuable to the installation contractor almost upon receipt.
Closing thoughts
Each of the three examples discussed here represents different types of materials-related issues that can occur on a project. In Example 1, we saw the impact of a minor protocol variation that resulted in significant disruption to construction planning, emphasizing the need for both vigilant materials-management review of all process modifications, and the need for the materials-management team to be integrated into the review and approval processes to facilitate identification of detrimental variations that can easily slip under the radar.
Example 2 underscores the value that a knowledgeable, cross-functional materials-management team can offer to individual transactional disciplines, especially when it comes to working with upstream disciplines to streamline and optimize downstream work process such as warehouse and construction planning.
Example 3 emphasizes the need for the materials-management team to actively monitor execution of all materials-related processes, because over the lengthy course of any capital-intensive project, even a well-coordinated process will likely deviate at some point. Active monitoring by the materials-management team will help to identify these deviations early, and mitigate negative downstream impact.
Addressing work-process evolution, E&C contractors that structure their materials-management organizations according to the following objectives will be able to meet evolving market conditions:
- Maintain cradle-to-grave oversight throughout project duration
- Develop skillsets that are knowledgeable in all enterprise and supplier materials-related work processes
- Address all materials-related work processes cross-functionally
- Remain knowledgeable in enterprise, partner and supplier automation tools
- Be assertively proactive and non-transactional in execution
- Maintain close alliance with, and support by, project management n
Edited by Suzanne Shelley
References
1. Global Procurement and Materials Management, Construction Industry Institute, Research Summary 257-1, December 2010.
2. Global Procurement and Materials Management – An eGuide to Effective Project Execution, Construction Industry Institute, Implementation Resource 257-2, 2011.
3. Global Procurement and Materials Management – Materials Management Planning Guide, Construction Industry Institute, Implementation Resource 257-3, November 2010.
4. Caldas, Carlos H., Menches, Cindy L., Navarro, Laure, Vargas, Daniel M., Reyes, Pedro, An Analysis of Global Procurement and Materials Management Practices in the Construction Industry, Construction Industry Institute, Research Report 257-11, December 2010.
Author
Stephen Wyss is a materials manager with Bechtel Corp. (3000 Post Oak Blvd, Houston, TX 77056-6503; Phone: 713-235-2000; Email: [email protected]). He has more than 40 years of experience working with EPC contractors, including tenures at Black & Veatch Pritchard, CF Braun, and Intergraph. His current duties entail coordinating materials-related aspects of engineering, procurement, suppliers and construction, for bulk materials related to piping, electrical, and structural activities, for large process plant projects. His project experience has generally been in emerging economies with logistical challenges,including the Middle East, India, Africa and South America. A registered mechanical engineer in Texas and California, he holds a J.D. degree in law from Loyola Law School (Los Angeles) and an A.B. degree in architecture from the University of California at Berkeley.