Unlike reactors made from glass-lined metals or those made entirely from stainless steel or more exotic metals, such as Monel or tantalum, the transparency of glass reactors “lets users see what’s going on inside the vessel,” says Alan Kramme, vice-president of engineering for Ace Glass, Inc. (Booth 511; Vineland, N.J.). This is just one advantage they offer over traditional alternatives. The high degree of chemical inertness (some chemistries cannot tolerate even trace amounts of leachables that may be found in metal reactors), cost advantages, ease-of-cleaning and reusability provide additional benefits.
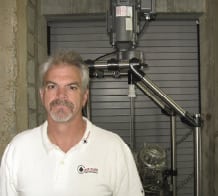
In his workshop, entitled “Optimizing Pilot Plant Reactors and Efficiencies” (to be presented Tuesday, November 17 at 10:00 a.m. in Theater B), Kramme will profile the advantages of glass reactor systems for applications ranging from small-volume, lab- and bench-scale operations (in the 100-mL range) to larger-scale ones (up to 100-L jacketed systems and 200-L unjacketed reactors).
Advanced glass reactor systems give users a lot of flexibility. They may be cylindrical or spherical, and have domed tops, flat heads and low profiles. “These customizable geometrical aspects that are important to help users demonstrate and verify the mixing dynamics and thermodynamic aspects of the bench-scale reactions while still meeting space and access limitations,” says Kramme.
Similarly, they may be equipped with different motors for stirring, pumps for automated dosing of reactants, and bottom control valves for dispensing, and allow for a range of accessories, such as baffles and spargers to be incorporated into the design. “Especially in bench-scale operations, users like reactors to be as universal as possible,” says Kramme.
“Many fear that glass reactors may be fragile but this is not the case,” he says. However, he notes that low-expansion borosilicate glass is very rugged and has good thermal shock resistance, and that vessels, mixers and motors are routinely mounted on stainless-steel support stands (with casters for mobility).
Glass reactors may also be jacketed or unjacketed. “Jacketed reactors for bench-scale and larger applications are growing in popularity because they provide the precise temperature control that many of today’s complex chemical selective reactions require,” says Kramme. And because the jackets themselves are also made from borosilicate glass (with heat transfer fluids pumped throughout the enclosed space) visual access is maintained.
Kramme will also discuss the software control and datalogging capabilities of today’s semi-automated, glass-reactor systems. These tools allow users to develop and capture reaction details, operating conditions, and information related to thermodynamics and kinetics in the form of reproducible recipes.
Recently, in some industries, the use of disposable plastic vessels for bench- and medium-scale applications has been on the rise. However, Kramme notes that the use of permanent, reusable glass reactors provides both environmental benefits (by reducing disposal requirements) and long-term, lifecycle-cost advantages (by eliminating replacement expenses).
Suzanne Shelley