Advances in sliding-vane and internal-gear seal-less pump technologies can provide many benefits when compared to centrifugal pumps or more well-known positive-displacement pump options
Facilities in the chemical process industries (CPI) use a wide array of flowing substances that must be processed, stored and transferred during manufacturing activities. The technology tasked with facilitating this liquid movement is the industrial pump. As befits what has grown into a very large global industry, a number of competing technologies are constantly positioning themselves to grab the attention — and capital-investment dollars — of the world’s chemical processors.
The oldest of these battles divided the camps into those that favored centrifugal pump technology, which uses velocity, momentum and kinetic energy to transfer the liquid — but only if the pump is operating at or near its best efficiency point (BEP) — and those with an affinity for positive displacement (PD) pump technologies, which capture a fixed volume of liquid and transfer it “like clockwork.” These distinctions have led some to call centrifugal pumps “emotional,” since changes to their liquid and system environment directly influence their operational capabilities, while PD pumps are seen as more “stoic,” with the pump steadfastly achieving peak efficiency at all times, no matter the changes in operating environment.
In recent years, however, the discussion has begun to revolve around another design distinction: is the best pump — be it PD or centrifugal — for CPI applications sealed or seal-less? This article answers that question while illustrating that seal-less PD pump technologies, including sliding-vane and internal-gear pumps, can ultimately be the better choice for certain applications within the realm of the PD pump universe (Figure 1).
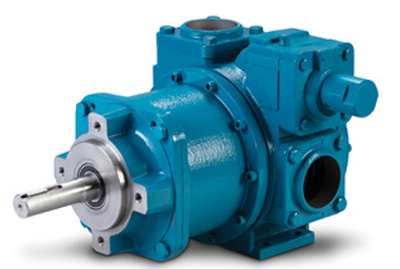
FIGURE 1. A sliding-vane pump is a type of sealless positive-displacement (PD) pump that can offer some operational benefits when compared to centrifugal pumps or more well-known PD pump options
Un-sealing the deal
The difference between sealed and seal-less pump technologies is very simple — sealed pumps use dynamic seals to keep the liquid contained, while seal-less pumps do not require dynamic seals to contain the liquid. Sealed pumps can accommodate a constant bleed of trace fluid across the seal faces (even in double seals), whereas seal-less pumps offer true leak-free operation. Although sealed pumps remain more common, seals are viewed as the weakest link in a pump’s operational chain, with some analyses of pumping operations indicating that upwards of 80% of all pump failures may originate at the seal. A quick tour through any CPI facility will support this hypothesis: look for wet baseplates and empty baseplates. Both indicate reduced uptime related to a failure in a sealing device.
Now, this doesn’t mean that all of these failures are solely the seal’s fault. In fact, there are many operational occurrences — including pulsation, vibration, shaft deflection, dry run, viscosity, temperature and pressure changes and liquid crystallization, to name just a few — that can cause the seal to leak or fail, either of which will put the pump out of service. Regardless, a compelling case is created for seal-less pumps, since using this pumping technology could theoretically significantly reduce seal-related downtime occurrences, ancillary costs for maintenance and repair and maintenance requirements — some of the major headaches that are inherent in operating a pump.
So, if we can agree that there are compelling reasons to consider incorporating seal-less pumps in a chemical-processing operation, the next question becomes, “Which type of seal-less pump?” Which brings the discussion back to the centrifugal or PD pump conundrum.
There has been recent growth in next-generation seal-less designs that feature a magnetic-drive (mag-drive) coupling that is used to transmit torque to the pump. In these configurations, a magnetic coupling connects the driving shaft to the driven shaft without use of a dynamic seal to keep the pumped liquids contained.
Admittedly, mag-drive seal-less pumps typically have a higher purchase price than basic sealed pumps, but as the seals and accompanying seal-support systems get more complicated (and remain more prone to failure), they get more expensive. For example, a triple-lip seal can cost $3,000, and if you’re repairing or replacing it every 12 to 18 months, that cost will add up, along with the added expense of any maintenance or repair calls. Or, for double mechanical seals that require seal-support systems, the seal-support system adds $4,000 to $8,000 itself in purchase cost, plus associated costs for monitoring equipment.
Financial considerations aside, mag-drive seal-less PD pumps outperform their seal-less centrifugal cousins by offering new functionality that is not possible with centrifugal pumps. First, seal-less PD pumps are self-priming and have good suction-lift capabilities, while mag-drive centrifugal pumps, just like sealed centrifugal pumps, rely on an integral reservoir that must be pre-filled before it is turned on. This means that they technically are not self-priming pumps, but pre-primed pumps. Second, seal-less PD pumps allow for bi-directional operation. Simply rotate the pump forward or backwards to achieve line stripping in either direction, saving on fluid waste and improved safety in your facility. Third, seal-less PD pumps are not sensitive to changes in operating environment (liquid or system conditions), unlike centrifugal pumps, which must be tuned to a single BEP or they will react negatively to changes in their environment. Finally, seal-less PD pumps can run dry for extended periods, process suspended solids, and accommodate systems with zero net positive suction head available (NPSHa), whereas centrifugal pumps struggle in each of these areas.
Assessing the PD options
With seal-less centrifugal pumps removed from the equation, it’s time to fully consider the seal-less PD options. The most popular in chemical-processing applications have proven to be air-operated double-diaphragm (AODD) and peristaltic (hose) pumps. The standout feature of both of these technologies is their ability to pull a perfect vacuum, which thereby enables them to self-prime and achieve good suction lift.
Specifically, AODD pumps are a first-choice seal-less technology for utilitarian pumping applications for a number of reasons: they are inexpensive, very flexible and easy to operate (all you need is an air hose and suction pipe). There are also some shortcomings: their flow and pressure capacities are narrower than some other PD pump technologies; they create pulsation in the liquid path; and because air is expensive, they can be costly to operate, especially when used in continuous-duty applications.
Peristaltic pumps are suitable for handling thick slurries and liquids with large solids. They deliver flowrate consistency despite changes in pressure, but their flowrate range is limited, and pulsating flow can occur, which will make it difficult to dial in a specific flowrate. From a footprint standpoint, peristaltic pumps are larger than many other technologies, which means they require more operating space. Also, when or if the pump’s hoses fail, a catastrophic leak can occur, and hose degradation during operation can compromise the integrity of more sensitive liquids.
On the other hand, two of the lesser-known seal-less PD pump technologies that feature a mag-drive design are sliding-vane and internal-gear pumps. The basic advantages of these mag-drive pumps are that they are electrically driven, so there is no need for compressed air; they have a wide and consistent flowrate range; they create no pulsation in the liquid; they operate well at higher temperatures; they are immune to changes in liquid viscosity or pressure; and they are truly self-priming, meaning they can prime while being fully dry, right out of the box. The following sections take a closer look at the specific advantages of these technologies.
Sliding-vane pumps
Sliding-vane technology (Figure 2) self-compensates for wear, sustaining new performance throughout the pump’s operational life. Vane pumps uniquely allow a wide viscosity and pressure range, and are well suited for challenging applications, such as those with suspended solids, varying system pressure, zero NPSHa, liquid-vapor mix and regular dry-run operation.
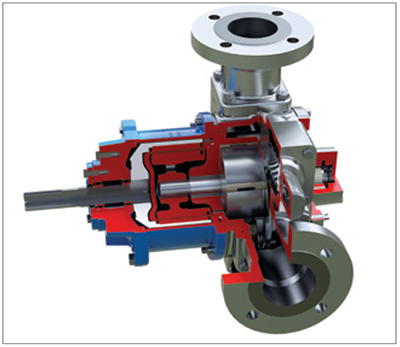
FIGURE 2. Sliding-vane pump technologies are designed to handle a wide range of fluid viscosities and pressures, including media with suspended solids
Reliability. Mag-drive sliding vane technology allows for extended and expected dry-run; high suspended-solids levels (up to 20% in some cases); zero-NPSH-required performance that is ideal for challenging pump inlet conditions, including with liquids featuring up to 20% vapor or air content; and provides uptime without the use of current-monitoring systems.
Functionality. The mag-drive sliding vane technology can achieve suction lift of more than 25 ft (7.6 m) without the need to pre-prime the system; provides bi-directional flow; and can line strip to reduce product waste during or after production runs.
Flexibility. The mag-drive sliding-vane technology provides a wide operating range that is immune to changing fluid and system conditions. Furthermore, a wide flow and pressure range is achievable, potentially over a smaller equipment model range, optimizing asset flexibility.
Internal-gear pumps
Today’s advanced magnetically coupled internal-gear pumps (Figure 3) have a simple design that features only seven main components. The heart of the design is a bearing-to-bearing support system that eliminates leaks. The pump’s short spindle also overcomes the challenges that are inherent in pump technologies with longer spindles, namely the impact of overhung loads that can lead to premature wear and failure. Also, unlike centrifugal pumps that rely on cantilevered bearings, internal gear pumps have a symmetrical shaft support, which eliminates shaft deflection during operation, resulting in less maintenance and downtime.
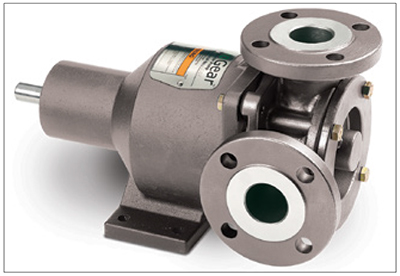
FIGURE 3. Magnetically driven internal-gear pumps have a simple design with fewer components than other pump types, resulting in streamlined maintenance and reduced downtime
Another standout feature of some magnetically coupled gear pumps is a single-liquid-chamber design that improves liquid circulation through the coupling area. This results in longer magnet life, lower operating temperatures and more efficient cleaning and flushing processes. By comparison, some gear-pump designs feature a long, tortuous flow path, which can raise the temperature of the liquid as it is being transferred to levels that can compromise magnet life.
So, now the decision involves a choice between PD seal-less mag-drive sliding vane and seal-less mag-drive internal gear pumps. Table 1 provides some representative operating information to compare sliding-vane and internal-gear technologies, which operators can use to select the best option for their specific applications.
Recent advancements in seal-less sliding vane and internal gear pump technology provide new functionality, reliability and flexibility for CPI facilities. These pump designs are leak-free and help eliminate pervasive pain points of legacy technologies that have been used in CPI applications. Now, chemical processors can leverage new options that combine leak-free, seal-less performance with the inherent operational advantages that positive-displacement sliding and gear pumps possess. ■
Author
Geoff VanLeeuwen is the director of products and applications for Blackmer and PSG (1809 Century Avenue SW, Grand Rapids, MI 49503; Phone: 1 (616) 241-1611; Email: [email protected]; Website: www.blackmer.com). He has worked at Blackmer since 2014 and held previous roles at Sargent & Lundy and Innotec. VanLeeuwen is a Licensed Professional Engineer in Illinois and Michigan. He holds a B.S. in mechanical engineering from Calvin University and an M.S. in energy engineering from the University of Illinois Chicago, along with an M.B.A. from Grand Valley State University.
Michael Coburn is the product manager for EnviroGear and PSG, (1815 S. Meyers Road, Oakbrook Terrace, IL 60181; Email: [email protected]; Phone: 1-909-422-1731; Website: www. psgdover.com/envirogear). Coburn has worked at PSG for five years, and has over 15 years of experience in engineering. He holds B.S. and M.S. degrees in mechanical engineering.