Across several regions of the U.S., new lithium projects are emerging to build up a more localized supply chain
Despite growing demand in the U.S. for batteries in consumer electronics and electric vehicles (EV), the vast majority of lithium extraction and processing occurs overseas, with most extraction taking place in Australia (from spodumene ore) and South America (from brines), and nearly all processing and production activities occurring in China. Recent federal incentives have encouraged the development of a U.S. lithium supply chain, which has spurred a number of new projects and much research and development, all in the interest of promoting U.S. lithium resources and expanding domestic processing and recycling capacities.
Outlook and incentives
“Considering where we were four years ago in the U.S., I feel really optimistic about where we’ll be in two years. I am also optimistic that our percentage of global demand is going to increase, which to me is a key metric. We do have an excellent innovation landscape here, from national labs to private industry,” says Samm Gillard, co-founder and executive director of the Battery Advocacy for Technology Transformation (BATT) Coalition (www.battcoalition.org). BATT’s members include battery experts spanning the entire value chain, from materials extraction through component manufacturing and recycling, as well as advanced materials science, all of whom are interested in incentivizing the domestic production of lithium-ion battery (LIB) materials.
Despite a significant increase in announced lithium projects across the U.S., there are still challenges to overcome in order to move toward commercial-scale production, the most significant being the current low cost of lithium. “If lithium prices are where they are today, it’s going to be a challenge to scale up and to get capital in this climate, and also have viable businesses in the U.S. The big question on the processing side is who’s going to capitalize at the right time,” says Gillard. He further emphasizes that at this point in the economy, companies who can utilize their full capacity effectively will be at an advantage even over those with access to more sophisticated technology assets. “There are a lot of companies that are on the cusp of that. Hopefully the next round of capital from the Bipartisan Infrastructure Law will unlock some of that potential,” he adds.
These incentives, coupled with the energy transition encouraging companies to diversify, has led to energy majors like ExxonMobil and Equinor — both of whom have announced investment in lithium production at Arkansas’ Smackover formation — to join more traditional electronics conglomerates like Panasonic and Samsung as players in the U.S. battery supply chain. “It’s interesting to see these monoliths start to get into the lithium space because the economics are favorable. I think it’s a good thing to have companies involved who aren’t completely dependent on the dynamics of one particular market,” says Gillard.
Midstream refining capacity
Once lithium has been extracted, whether from brine, hard-rock mining or battery recycling, it must undergo a series of refinement steps to prepare it for battery processing. At this point in the lithium value chain, location is key. Currently, China significantly dominates the lithium refining market, but new electric-vehicle tax credits available under the U.S. Inflation Reduction Act provide benefits for a more domesticated supply chain.
Stardust Power Inc. (Oklahoma City, Okla.; www.stardust-power.com) has announced plans to construct a strategically located lithium refinery in Muskogee, Okla. (near Tulsa). “There’s a lot of lithium in the U.S. — potentially up to 14% of the global market — but very little battery-grade lithium produced domestically. A critical gap in the supply chain is midstream refining capacity,” explains Roshan Pujari, Founder and CEO Stardust Power.
The Stardust Power project is currently one of the largest lithium refineries in the U.S. under development, with a planned capacity of up to 50,000 metric tons year (m.t./yr), to be brought onstream as two 25,000-m.t./yr processing lines (Figure 1). This capacity, says Pujari, could account for up to 10% of future lithium-processing demand in the U.S.
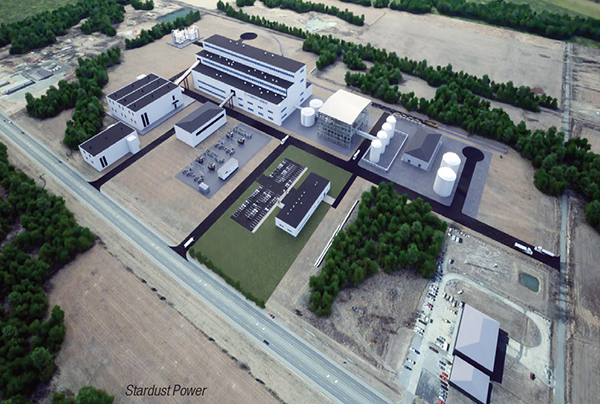
FIGURE 1. A rendering of Stardust Power’s planned lithium-refining facility shows the scale of the site, which could significantly increase U.S. domestic capacity for lithium processing
He likens Stardust Power’s approach to the lithium market to the oil-and-gas industry where there are producers and refiners in a “hub-and-spoke” model, without necessarily requiring vertical integration across a single organization or site. “The innovative approach that we take is optimizing the large central refinery for multiple sources of lithium, so we can aggregate supply and quickly scale manufacturing of battery-grade lithium. That way, we’re not dependent on a single asset,” he adds. Another benefit of the U.S. market being primarily in the brine space, is the flexibility that direct lithium extraction (DLE) processes afford in the upstream removal of impurities. “The advantage of DLE using brine is that if there is an impurity that our central refinery cannot accommodate, that can be removed upstream in the DLE process,” notes Pujari.
“Being located centrally in the U.S., our shovel-ready site is already connected to major highway, railway and the largest inland waterway system in the U.S. and takes advantage of low-cost renewable power in the form of solar and wind power. We’re designing fully electric processing trains to limit air emissions, and we’re using zero-liquid-discharge technology, so there’s no water pollution. In fact, our byproduct is largely salt,” says Pujari.
Stardust Power currently has exclusive options to acquire interests in several lithium-brine projects in the U.S., including Jackpot Lake in Nevada and Pilot Valley in Utah. The company recently awarded a contract to engineering firm Primero USA (www.primero.com.au/northamerica/) to complete a front-end loaded level-3 engineering design and cost study for the facility, after which detailed engineering and procurement will take place.
DLE will be dominant
As the lithium supply chain in the U.S. evolves, it is clear that DLE technologies are a key element in making the most of the available lithium, much of which is incorporated into brine, rather than hard rock.
“Unequivocally, DLE is the way of the future for brines in the U.S. Evaporation ponds have really low recovery rates, and it takes a long time for lithium to go through the process. And in many places, they simply aren’t viable without the right amount of sun or with too much precipitation,” says Teague Egan, CEO of Energy Exploration Technologies Inc. (EnergyX; Austin, Tex.; www.energyx.com). Taking climate and terrain into account is important as new projects emerge across the U.S. A major area of activity is in the Smackover formation in Arkansas, and neighboring areas of Louisiana and eastern Texas, where the land is much hillier and more forested than the desert regions in South America where brine-evaporation ponds are more common. “This region has some of the best discovered lithium deposits in the U.S. EnergyX’s view is that the Smackover shows the highest probability of success and has the most favorable brine characteristics in the country,” adds Egan.
With the variation in brine makeup across regions, there are many factors to consider in determining a brine’s promise for lithium extraction, such as lithium concentration, impurity profile, temperature and whether processing the brine requires freshwater or other chemical inputs. “Our first goal in designing DLE technology was that we wanted to design a platform that could essentially treat any brine in the world. Our second goal was to develop an end-to-end system, like a petroleum refinery. There’s not just one technology in an oil refinery, everything goes through several separation and purification steps to get to usable products. And the same is true of lithium — going from a brine to battery-grade lithium product isn’t just one technology. That’s why we’ve pursued a holistic view that incorporates several technology pillars to complete the process,” says Egan. For more on EnergyX’s DLE technology, read “Lithium Extraction: Prime Time for Brine,” Chem. Eng., June 2023, pp. 13–16.
EnergyX recently announced a major lithium project in the Smackover area, Project Lonestar Lithium, which has an anticipated initial processing capacity of 5,000 tons/yr, scaling up to 25,000 tons/yr in a subsequent phase. Kiewit Corp. (Omaha, Neb.; www.kiewit.com) is conducting front-end engineering plans for the project currently.
“We’re very confident in our DLE technology, so much so that we’ve taken the step to start acquiring resources so that we can vertically integrate that technology into our own projects, as opposed to just licensing it to existing lithium producers,” says Egan.
Large-scale demonstration
In September, SLB (Houston; www.slb.com) announced a breakthrough in its first sustainable lithium-production project, located in Clayton Valley, Nev. At the site, a 100-gal/min demonstration plant integrates lithium extraction from brine with impurity treatment and concentration technologies to yield high-purity lithium carbonate or hydroxide. “We definitely understand that if we want to meet lithium demand, we can’t just rely on the current reserves that in a few hard rock mines in Australia and brine that’s coming mainly from Chile and Argentina. So the questions are how can we open up these reserves that have lower concentration, and how can we deal with impurities? This is why DLE technologies keeps popping up, since they are able to handle different kinds of brines. DLE, however, is just the engine, you still need to consider pre-treatment and post-processing requirements,” says Nicholas Lugansky, head of mining at SLB.
This is why, in the development of its lithium-production technology, SLB wanted to investigate the entire chain from well to product, bringing in its expertise in subsurface reserve modeling with the development of DLE and other process technologies. “We set out to create an entire flowsheet, starting with the engineering work on how to handle the brine when it comes out of the ground and how to pre-treat it so it can go into the DLE system. We then deploy secondary impurity removal to treat any residual impurities before concentrating the lithium chloride so it can either be shipped as an intermediary or converted into lithium carbonate or hydroxide,” explains Lugansky.
The significance of the Clayton Valley site is not only its size — which Lugansky believes is the largest end-to-end lithium-processing demonstration unit currently in operation — but also its focus on sustainable resource utilization. The site was designed to not require any external water source besides the brine, and also to minimize the consumption of reagents and other chemicals, using them for pH adjustment and nothing else. “Taking balance of plant into consideration, we wanted to make sure to address the water question. If you look at where the lithium resources are today, most are in very arid environments, such as Nevada, Utah and California, or desert environments of Chile and Argentina,” says Lugansky.
SLB says that its holistic lithium-production technology is 500 times faster than conventional evaporation methods while producing a verified recovery rate of 96% lithium from brine. SLB is currently developing front-end engineering for the entire process flow at the commercial scale, designing for customer parameters so that the units can be fabricated and delivered to customer sites. Lugansky emphasizes that the systems are designed to be modular, standardized and easily replicable for rapid installation at customer sites. “Customers are currently testing our systems at their sites. We hope to announce the first commercial deployment in the next year or so,” he notes.
Battery recycling
To augment the demand for “virgin” lithium and other battery metals, and to help make the battery supply chain more circular, new recycling capacity is coming onstream and novel technologies are emerging. In April, Green Li-Ion Ltd. (Singapore; www.greenli-ion.com) opened its first site, a commercial-scale lithium-ion battery recycling plant in Atoka, Oklahoma (Figure 2). The plant is currently designed to process around 700 tons of black mass, equating to a processing capacity of about 2 ton/d, and scaleup plans are already in process. “What we’re looking to do in 2025 is support the growing battery materials industry in North America by producing high performance green battery material at scale,” says Lucas Marks, vice president of Business Development — North America at Green Li-Ion.
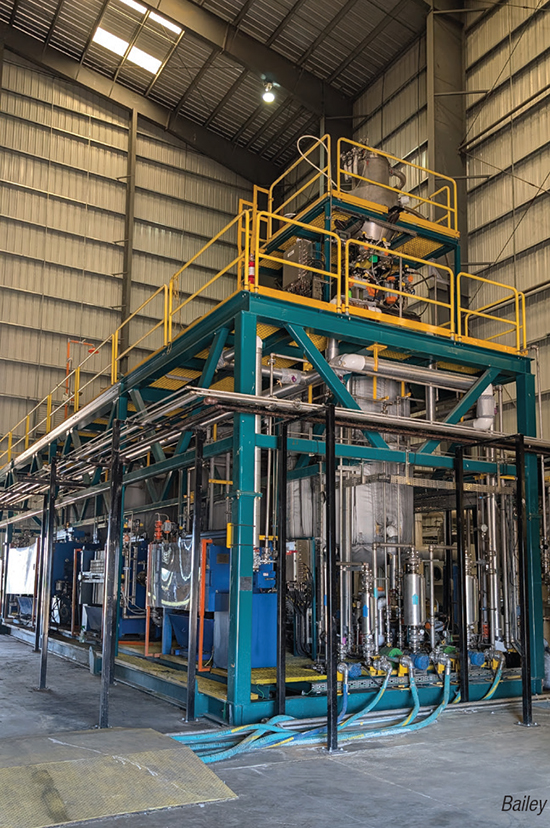
FIGURE 2. Green Li-ion’s plant in Oklahoma started up this year, and plans are in place to quadruple production capacity in the coming years
Green Li-ion’s Hydro-Rejuvenation TM recycling process is designed for modularity, meaning that battery companies can either provide their own materials to be processed at the site, or manufacturers can license the technology to be installed on their own premises for onsite processing of spent battery materials. The process includes a proprietary reactor design where precursor cathode-active material (pCAM) and mixed hydroxide precipitate (MHP) are produced along with lithium carbonate and graphite, eliminating two metal-refining steps from typical hydrometallurgical recycling processes. The plant includes an onsite quality-control laboratory to test customer materials and also ensure that its produced materials are “drop-in ready” for manufacturing new batteries. The plant is designed to minimize waste and effluent streams, and the only byproducts are solid sodium sulfate and water, which are reusable and saleable product streams. “We’ve worked with third parties to show that our sustainability numbers are not only a bit better than using virgin materials for pCAM, but also when compared to other hydrometallurgical recycling processes,” says Marks.
The company is taking advantage of its strategic location in the central U.S., working with domestic suppliers for spent battery materials to help move the supply chain away from a dependence solely on virgin materials and build the infrastructure required to make batteries more circular. “We’re moving in that direction. There are companies who are involved in picking up used batteries to help establish the supply chain. There are quite a few players that are doing upstream black mass production, but to keep and use these critical battery materials in the U.S., we must refine and produce cathode and anode precursors locally, and that’s where we come in,” adds Marks.
Kevin Hobbie, Global operations manager at Green Li-ion emphasizes the significance of the plant’s location within the lithium supply chain: “Oklahoma is uniquely positioned for this. The state has black-mass producers and a company that’s converting MHP back to sulfates, as well as the Stardust lithium-production facility that’s going to be built about 30 minutes north of our site. And of course, there is the Panasonic battery gigafactory being built in Kansas.”
Battery-recycling firm Blue Whale Materials LLC (Washington, D.C.; www.bluewhalematerials.com) is also constructing a processing facility for spent lithium-ion batteries in Oklahoma. The site will be the first-ever to employ Blue Whale Materials’ proprietary technology to process end-of-life batteries (with a range of battery chemistries) and production scrap into a “highly concentrated dry product containing cobalt, nickel and lithium as well as copper and aluminum products.” Startup is slated for late 2024.
Last year, American Battery Technology Company (ABTC; Reno, Nev.; www.americanbatterytechnology.com) began operation of a first-of-its-kind, commercial-scale Li-ion battery recycling facility located in the Tahoe-Reno Industrial Center (TRIC) in McCarran, Nev. This commercial facility has the capacity to process over 20,000 m.t. of battery feedstock materials per year when fully ramped, and this first phase of operations will process these battery feedstock materials into recycled products including copper, aluminum, steel, a lithium intermediate and a black mass intermediate material. In July, the company announced that it entered into a milestone purchase agreement with a domestic customer related to recycled black-mass material from its site.
One of the greatest uncertainties in the supply chain will be the handling of end-of-life battery materials and whether a streamlined infrastructure can be established to maximize the recovery of lithium and other critical materials from spent batteries. “We don’t know how much of a challenge this is ultimately going to be yet, because we don’t have good data, but there are a couple of things that give me hope,” says BATT’s Gillard. “The automotive manufacturers don’t want their batteries to end up at disparate dismantling facilities, so they have a need to close that supply-chain loop for themselves, because there will be a need for that material. They also are offering more modular battery designs that are much easier to take apart, both for repair and recycling. I think it’s hard to know exactly what’s going to happen with the recycling aspect because there are a few more variables,” he notes.
Microwave-based recycling.While the majority of battery-recycling processes are based on hydrometallurgical principles, researchers at Rice University (Houston; www.rice.edu) have developed a new methodology for battery recycling that reportedly provides ultrafast lithium recovery with high selectivity using a combination of microwave reactor technology and an environmentally benign deep-eutectic solvent (DES). “In battery recycling, sometimes less than 5% of lithium is recovered. This is because lithium is usually precipitated last after all other metals, and hence, the solution gradually becomes contaminated, with lithium loss in each step. It was important to devise a process that can quickly and selectively leach lithium,” explains Rice postdoctoral fellow Sohini Bhattacharyya. The Rice team has demonstrated, at the laboratory scale, the leaching of a 50% lithium stream in just 30 s. “Just as a microwave heats food much faster than a stovetop, the microwave used here accelerates the leaching process, making this process more commercially viable than other DES-based battery-recycling processes,” adds Bhattacharyya.
Since the process follows the same types of procedures (heating, leaching and so on) as typical hydrometallurgical recycling processes, the industrial-grade microwave reactor could easily be inserted into an existing hydrometallurgical recycling setup to help improve lithium recovery.
The DES composition used in this work, a mixture of ethylene glycol (EG) and choline chloride (ChCl), was carefully studied to optimize lithium selectivity. The team’s previous work showed that the leaching of transition metals, such as cobalt and nickel, require the involvement of both EG and ChCl, while lithium can be leached with only ChCl (Figure 3). Taking advantage of ChCl’s beneficial microwave-absorbance properties, and EG’s poor microwave absorbance, only the ChCl is activated in the microwave reactor, rapidly recovering only lithium in this part of the recycling process, and inhibiting the co-leaching of cobalt and nickel. “This demonstrated that tuning DES composition can be instrumental in achieving selectivity towards specific metals in certain conditions,” emphasizes Rice doctoral alumna Salma Alhashim.
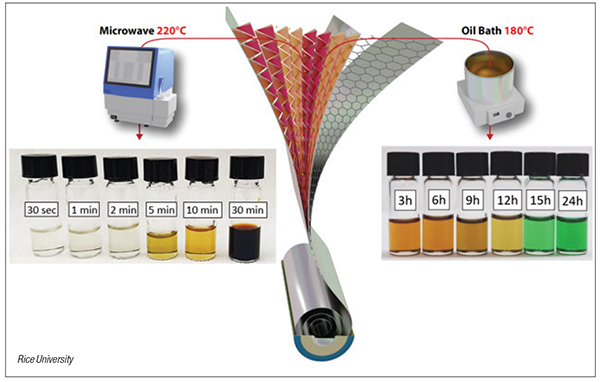
FIGURE 3. Leachate solutions after microwave leaching show yellow or brown shades due to the selective leaching of lithium. The same reaction done in an oil bath yields green colored solutions, since more cobalt and nickel have leached out
Finding new pathways for battery recycling will be increasingly important as the U.S. continues to cultivate its own reserves of critical metals. “These materials are, in fact, available in spent lithium-ion batteries, which often end up in landfills. If instead, they are collected and recycled properly, the U.S. can have a more uninterrupted supply of these minerals,” says Pulickel Ajayan, the senior researcher on the study and Rice department chair of materials science and nanoengineering. ■
Mary Page Bailey