Significant sustainability benefits can be gained through optimization in steam-cracking furnaces. The study detailed here shows the specific decarbonization strategies that can help improve energy efficiency and reduce emissions
The chemical process industries (CPI) rely heavily on steam cracking to produce essential olefins — especially ethylene, a key feedstock for polyethylene, polystyrene, polyethylene terephthalate and polyvinylchloride. Over the past decades, there has been significant growth in ethylene demand, with an anticipated increase of approximately 5.58% by 2030, and the associated global polyethylene market is expected to increase 9.6% by 2032 [1– 3]. Steam crackers are the main technology to produce ethylene from light gas or liquid hydrocarbon feedstocks in petrochemical plants (Figure 1). The process is severely endothermic, meaning that conventional steam cracking is the largest energy consumer, and thus also the largest emissions producer, among process units in the CPI, with more than 8% share of the total energy use in these sectors [4, 5]. The energy consumption of ethylene production varies from 15 to 27 GJ/kg of ethylene produced, depending on the feed used in this process [6, 7]. Since energy costs may constitute as much as 70% of the net product cost of an olefin plant, advancing energy efficiency is crucial to reduce energy costs [4].
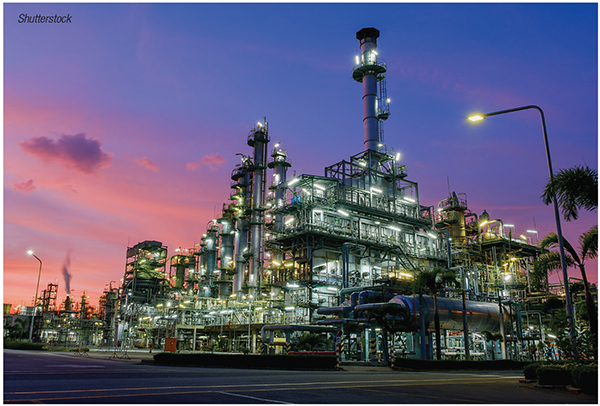
FIGURE 1. Steam crackers are nearly ubiquitous across the petroleum refining and petrochemicals sectors. They are also major consumers of energy and contributors to carbon emissions, so the optimization of steam crackers is often a central part of sitewide sustainability initiatives
Ethylene production stands among the top three CO2 emitters in the CPI, with studies indicating that worldwide CO2 emissions from steam crackers could increase by 33%, from 198.9 million metric tons per year (m.t./yr) to 264 million m.t./yr [8]. In conventional crackers, roughly 0.85 to 1.8 m.t. of CO2 is emitted per metric ton of produced ethylene, depending on the type of feedstock [9].
As a result, decarbonization and energy efficiency have become major concerns for olefin producers. While they are compelled to take measures to improve environmental sustainability, most refiners prefer to keep their existing steam cracker configuration and implement energy-optimization and carbon-reduction strategies without any significant changes to their hardware and infrastructure, rather than taking drastic measures to re-design their processes or equipment. Such decarbonization strategies include carbon capture, utilization and storage (CCUS), hydrogen fuel switching, renewable feedstock adoption, steam-cracker enhancement and process optimization.
Process simulation software is a powerful tool to facilitate precise modeling and optimization of complex processes. In this article, a process simulation software with an integrated steam-cracker-furnace model is used to investigate various decarbonization strategies aimed at improving furnace energy efficiency and reducing CO2 emissions, while providing a comprehensive overview of the decarbonization potential of steam-cracking furnaces.
Decarbonization strategies
There are various approaches for decarbonizing steam crackers — some of these approaches are aligned with net-zero emissions, while others are considered to be near-zero emissions. Several net-zero strategies are illustrated in Figure 2 and discussed further in Refs 8 and 10–12.
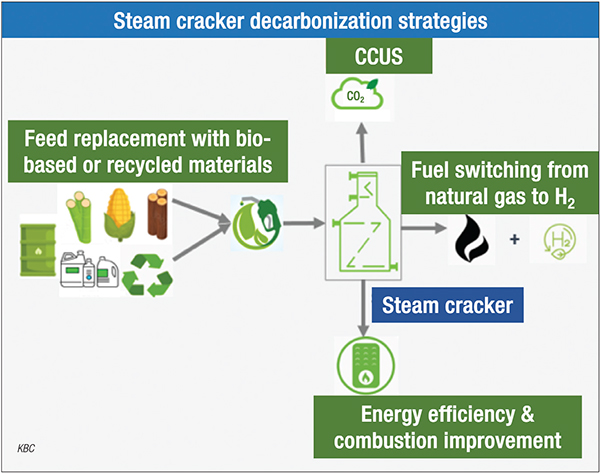
FIGURE 2. Several decarbonization strategies related to steam crackers have been identified as promising paths toward net-zero emissions
Bio-based and recycled plastic waste feedstock. Transitioning toward decarbonization necessitates a fundamental re-evaluation of feedstock. Adopting a circular economy approach, energy consumption and carbon footprint reduction are achieved by substituting conventional fossil fuels with bio-based alternatives, and waste plastics from depolymerization or pyrolysis processes. This approach not only mitigates emissions, but also reduces reliance on finite fossil resources, thereby laying the groundwork for a more sustainable lifecycle [12– 15].
Thermal efficiency. Remarkable evolution in the energy efficiency of steam-cracker furnaces can be obtained by improving two furnace sections — the firebox and the combustion section. Reduction of energy consumption in the firebox can be achieved by improving firebox radiation efficiency, such as by increasing emissivity, changing coil type and configuration and optimizing the process conditions to increase ethylene yield, including the steam-to-hydrocarbon ratio and coil outlet pressure (COP).
Coil configuration refers to how the heat-exchange coils in the radiation section are arranged within the furnace to facilitate efficient heat transfer. Applying specific coil or tube types, such as ribbed tubes and finned tubes, especially mixing-element radiant tubes (MERT), can improve heat transfer by either increasing the heat-transfer area (cross-sectional area) or heat-transfer coefficient directly. These tube types help increase heat flux through the axial profile and increase run length [16, 17].
Pre-combustion strategies. To reduce the emissions associated with energy-intensive combustion processes, innovative technologies to optimize combustion and fuel switching (changing the ratio of methane to hydrogen) can be investigated, which consequently also will reduce energy consumption. Pre-combustion strategies enhance combustion efficiency by optimizing fuel composition before entering the combustion burner to achieve better fuel and air mixing. This approach aims to maximize combustion efficiency while minimizing emissions from incomplete combustion, improving fuel utilization and consequently, increasing overall furnace efficiency.
Incorporating hydrogen into the fuel mix can lead to efficient combustion, and consequently reduces the carbon footprint, since hydrogen has a high energy content and burns with minimal emission. The hydrogen required for hydrocarbon fuel switching can be obtained through various methods, including water electrolysis, as well as steam methane reforming (SMR) or auto-thermal reforming (ATR) followed by CCUS (“blue” hydrogen). Additionally, hydrogen can be produced by the gasification of fossil- or bio-based fuels into synthesis gas (syngas; a mixture of CO and hydrogen), with subsequent conversion of syngas to hydrogen and CO2 through the water-gas shift (WGS) reaction. Another source of hydrogen is from the recycled hydrogen-rich byproducts of the olefin plant itself.
Water electrolysis uses electricity to split water molecules into hydrogen and oxygen, while SMR produces hydrogen from natural gas with carbon capture or electrified SMR with no emission. All methods offer opportunities to incorporate clean hydrogen into the furnace operation. These upgrades not only lower energy consumption but also set new benchmarks for decreasing emissions [12– 15].
Oxy-fuel combustion is an innovative approach that uses pure oxygen instead of regular air for combustion. This approach eliminates nitrogen from the combustion process. Oxygen is separated from the air separation unit (ASU). The oxygen is mixed with recycled fluegas to lower the flame temperature. The fluegas is a mixture of steam and concentrated CO2, where the steam is easily separated through condensation and the remainder is pure CO2. Additionally, oxy-fuel combustion reduces the volume of fluegas that may require carbon capture [12– 15].
Post-combustion strategies. Improving combustion processes and employing advanced emission-control technologies assist in emissions reduction, but further emission reduction and elimination may be needed to meet certain regulations.
After minimizing emissions through the optimization of the steam-cracking process and combustion, the next step involves removing any remaining CO2 emissions from the exhaust fluegas. The objective is to capture and remove fluegas emissions to mitigate environmental impact, which is called post-combustion capture. As part of post-combustion capture, heat recovery from furnace fluegas can be utilized to preheat combustion air, thereby improving energy efficiency and reducing CO2 emissions. In the case of conventional steam crackers, post-combustion technologies can be implemented independently without the need for pre-combustion processes or optimization of the furnace and combustion section [12– 15].
In post-combustion processes, CO2 is separated and captured from conventional fluegas using various methods, including cryogenic distillation, membranes and physical and chemical absorption, with the latter being the most widely used. The adsorption efficiency varies from 80 to 95%, with the regenerator energy costs ranging from 3 to 5 GJ/m.t. CO2 [12].
For most conventional plants, decarbonizing steam crackers by post-combustion technologies would be a feasible solution because few changes are needed for the current plant if the required energy for regenerator and compressor is available. For these units, the energy source could be low-pressure steam from the steam system or from process electrification [8].
The captured and compressed liquified CO2 can be sent to storage or to a utilization process. At this point, CO2 can be converted into methanol through hydrogenation, followed by methanol-to-olefin conversion. Conversely, CO2 can be converted into ethanol and then into “green” ethylene and polyethylene. Additionally, CO2 can be fed to dehydrogenation and methanation processes to obtain methane. Another potential CO2 utilization method could be the production of sustainable aviation fuel (SAF) through the Fischer-Tropsch process [15].
Simulation and optimization
Process simulation software provides a versatile and accurate platform for techno-economic assessment of decarbonization strategies. Process simulation software can be used to perform unit monitoring, optimize processes and create a digital twin of the steam cracker. This approach enables engineers and technologists to study the effects of many factors, such as hydrocarbon feed, steam properties, coking inhibitors, fuel flowrates, operating conditions, coil configuration and type, coil metallurgy, wall coatings and emissivity, on energy efficiency and overall performance. Consequently, strategies for reducing coke and carbon emissions can be studied to make informed decisions before implementing changes in the plant.
For the study in this article, a process simulation software including an integrated steam-cracker-furnace model was applied to examine various decarbonization strategies and evaluate energy efficiency and CO2 capture from fluegas.
The model contains numerous parameters, including feedstock composition, operating conditions, equipment configuration and heat-transfer mechanisms. By simulating the real-world furnace behavior and characteristics, the software provides a virtual environment to experiment with different scenarios for decarbonization.
The study explored the impact of various parameters on the performance of the cracker, focusing on energy efficiency and emissions intensity. The primary objective was to minimize emissions and associated costs, while maximizing energy efficiency, product yields and resulting profit. The profit is determined by the difference between revenue and costs, where revenue is derived from products sales and costs encompass expenses such as feedstock and utilities. By optimizing these parameters, this investigation provides the means to select the most effective decarbonization strategies.
Results and discussion
Process simulator software was used to investigate and analyze the effect of different scenarios related to the energy efficiency and CO2-emissions reduction of the steam cracker, as follows:
(A) Altering the hydrocarbon feed ratio (S/C)
(B) Altering the coil outlet temperature (COT)
(C) Adjusting excess air
(D) Adjusting fuel composition (fuel switching)
(E) Multi-objective optimization
This study examined these scenarios because they require relatively minor physical modifications and can be readily implemented into existing plants. To perform this analysis, several key performance indictors (KPIs) were considered, whose definitions are provided in Table 1. In Table 1, the margin is defined as: margin = revenue – cost, where revenue is related to product yield and price, and product yield is a function of S/C and COT.
Cost is calculated as cost = feed cost + energy cost + emissions cost, where energy cost is a function of energy type, rate and price, and emissions cost is a function of emissions rate and emissions cost index.
For the study’s base case and (A)–(E) scenarios, two types of margin calculation are considered: one incorporating a carbon tax (CT) index of $0.05/kgC2, C3 and the other considering CCUS cost ranging from $15–25/m.t. CO2.
Scenarios (A) and (B). In Table 2, the results from the base case simulation are compared with the process variations resulting from scenarios (A) and (B). The implementation of the carbon capture technology for this cracker scenario results in 85% reduction in emissions as a result of carbon-capture efficiency, coupled with a 2.8% improvement in margin attributed to the lower cost of carbon capture in comparison to expenses associated with carbon emission taxes.
The second and third column present the effect of altering the hydrocarbon feed ratio and coil outlet temperature, respectively, on the furnace performance. The findings demonstrate that augmenting the S/C ratio from 0.3 to 0.5 wt./wt. results in a 7.8% rise in energy consumption, along with an approximately 5.8% increase in energy intensity (GJ/m.t.C2, C3), a 7.2% elevation in carbon emissions and a 9.5% uptick in carbon intensity (CO2kg/kgC2, C3). Raising the COT from 825 to 855°C results in an 6.9% increase in fuel consumption and a 1.2% rise in CO2 emissions. Nevertheless, the energy intensity and emissions intensity remain nearly constant, as the 10% enhancement in ethylene yield compensates for the increase in energy consumption and emissions.
Scenario (C). In Table 3, the first column corresponds to the base-case simulation results, while the second and third columns denote the impact of adjusting excess air (C) and fuelgas composition (D), respectively, on the furnace performance.
Excess air plays a pivotal role in fuelgas combustion within the burner, which is controlled by the CO composition at the bridgewall or fluegas exhaust. The presence of CO in fluegas indicates poor combustion and fuel loss, necessitating targeted emissions control and prevention, due to health and safety hazards and environmental impacts. Elevating excess air from 5 to 15 wt. % for achieving complete combustion leads to an 8.5% increase in fuel gas consumption. This elevation results in a 1.98% increase in energy intensity and an 8.1 % increase in carbon intensity.
Excess air beyond the necessary quantity for complete combustion needs to be regulated, as an increase in excess air raises both energy intensity and carbon intensity, thereby lowering furnace thermal efficiency. Therefore, an optimal amount of excess air of around 5 to 10% is recommended.
The required heat source for thermal cracking reaction is radiation, which is provided through combustion of hydrocarbon fuelgas, mainly methane, in the burner. Hydrogen integration involves substituting hydrogen for a portion of the hydrocarbon fuel, reducing or eliminating CO2 emissions. Furthermore, due to the heating value of hydrogen, increasing hydrogen percentage of fuel reduces fuel consumption, which improves energy efficiency. In cases where blue hydrogen is employed, pre-combustion technology is utilized. This involves the production of hydrogen through either autothermal reforming or steam reforming, accompanied by a carbon capture unit to mitigate emissions. Conversely, when green hydrogen is utilized, hydrogen is produced from electrified reformer furnaces or electrolyzers.
Scenario (D). Table 3 also illustrates the impact of hydrogen fuel switching within two scenarios, where the hydrogen content of fuel is increased beyond the base case (where H2 = 10 wt. %). In the first scenario, CH4/H2 = 1.5 and H2 is increased to 40 wt. %, and in the second scenario, CH4/H2 = 0.66 and H2 is increased to 60 wt. %. In these scenarios, there is a significant reduction in both CO2 emissions and carbon intensity (about 70%), accompanied by a decrease in both energy consumption and energy intensity by approximately 1%.
The economic and environmental feasibility of utilizing hydrogen as a fuel for carbon reduction hinges on several factors, such as carbon tax considerations and the prices of hydrogen and for CCUS. Two cases are studied: one with carbon tax included and the other with CCUS.
The comparison margin of both cases with the base case are presented in Table 3. In the first case, where a carbon tax index of 0.05 $/kgC2, C3 and a hydrogen price of $2/kgH2 were considered, decreasing the CH4/H2 ratio leads to a marginal loss of about 5.4%. In the second case, considering CCUS cost of 15–25/m.t. CO2 and a hydrogen price of $2/kgH2, changing the CH4/H2 ratio reduces the margin by 4.6%.
The results of the various investigated scenarios in this study show that hydrogen integration with combustion fuel has the highest impact on emission and energy intensity reduction. However, components like carbon tax index, CCUS cost and the price of hydrogen determine if this method is economically viable and sustainable.
Scenario (E). In the final study, outlined in Table 4, a combination of investigated scenarios is examined (E). In this scenario, a multi-objective optimization scheme is employed by defining object functions aimed at maximizing margin and reducing energy consumption and emissions. The defined objective functions prioritize maximizing yield while minimizing emissions rates and energy consumption by adjusting independent variables (such as S/C, COT, excess air and CH4/H2 ratio). The optimal operating conditions derived from this analysis are as follows: S/C= 0.33 wt./wt., COT = 844°C, excess air = 7%, hydrogen-rich fuel composition of CH4/H2 = 1.5 wt./wt. Table 4 presents the KPIs under these optimum conditions for steam cracker decarbonization. Notably, this approach results in an energy saving of about 4.6% and emission reduction by 44%, while achieving a marginal gain of about 3.7%. The subtle increase in margin is attributed to reductions in energy cost via reduced fuel consumption, decreased cost associated with carbon capturing due to CO2 emission reduction and improvements in ethylene yield and radiation efficiency.
The integration of a gas turbine (GT) with a steam cracker is another applied method to realize energy savings in olefin plants. This technology facilitates energy savings through the dual mechanisms of electricity generation and reduction of energy consumption in the convection section of the furnace. The improved energy efficiency attained via GT implementation is realized by utilizing the hot fluegas generated in the GT to provide oxygen-rich, preheated air. This air is then mixed with fresh air, serving as combustion air for the burner heater. This process leads to significant energy savings by effectively reducing energy intensity [19].
GT implementation may not be feasible for every existing steam cracker due to certain limitations. Specifically, the increased rate of hot fluegas necessitates a larger convection section, which may not be feasible for all facilities. However, this technology can still be applied to current steam crackers by selecting the appropriate integration concept. It is important to note that integrating a GT may also require a larger convection section for the steam-generation bank.
Conventional GT-equipped furnaces do not inherently contribute to emissions reduction due to the utilization of hydrocarbon fuelgas for GT combustion. To fully leverage the energy-efficiency benefits of GT technology while addressing emissions concerns, the same strategy as for emissions reduction in radiation-box combustion is proposed. This approach involves integrating hydrogen into both GT fuel and burner fuel, alongside the option carbon capture for the emitted CO2.
Beyond the scope of this study
Note that this study does not consider all possible variations that can impact process carbon intensity and energy efficiency. Some of the considerations that were outside the scope of this study are discussed below.
Emissivity. Emissivity analysis on emissions reduction is excluded from this study, since increasing emissivity requires changing the refractory coating, and this study only investigated methodologies that require minimal changes to the existing plant. However, it has been reported that using a high-emissivity coating for the refractory wall improves radiation heat transfer and consequently increases the furnace’s thermal efficiency by 1.9% and decreases CO2 emission by 4% while reducing emissions [19, 20].
Unconventional feedstocks. Applying CCUS, CO2 emissions emitted from the steam cracker are captured and converted into valuable products. Captured CO2 can be used as a feedstock for rWGS and Fischer Tropsch, methanol-to-olefin conversions and methanation. These technologies transform CO 2 emissions into synthetic feed for refinery and petrochemical operations while reducing greenhouse gas emissions. Further studies will analyze the lifecycle of decarbonization using unconventional feedstocks with bio-feed and plastic recycling and CCUS.
Final thoughts
A combination of factors must be considered when determining the most efficient and economically feasible methods for decarbonizing steam crackers. These factors include technological innovation, technical feasibility, economic viability, scalability and environmental impacts.
Economic feasibility is crucial for the successful adoption of decarbonization strategies. The cost of carbon capture and utilization processes and the cost of hydrogen for fuel switching must be competitive with conventional methods. Investments in research and development are also crucial to drive down costs and improve the economic viability of these approaches. Depending on the target of the olefin plant, increasing olefin yield, severity and, consequently, margin or emissions and energy reduction, different strategies could be taken. In addition, considering carbon taxes or carbon capture cost can further influence the margin.
The study outlined here shows that hydrogen integration (partial or complete) is the most efficient way to decarbonize steam crackers, while resulting in energy savings by lowering fuel consumption rate. However, switching to a rich hydrogen feedstock may require a revamp of the unit due to operational and design constraints that must be addressed. In the next few years, by lowering the cost of blue or green hydrogen, fuel switching to hydrogen will become even more economical. ■ Edited by Mary Page Bailey
References
1. Precedence Research, Ethylene Market Size To Rise $287 Billion By 2030, September 2024.
2. Precedence Research, Polyolefin Market Size, Share, and Trends 2024 to 2034, September 2024.
3. Davarnejad, R., “Alkenes — Recent Advances, New Perspectives and Applications,” IntechOpen, London, November 2021.
4. Ren, T., Patel, M. and Blok, K., Olefins from conventional and heavy feedstocks: Energy use in steam cracking and alternative processes, Energy, Vol. 31, Issue 4, March 2006, pp. 425–451.
5. Ren, T., Patel, M. and Blok, K., Steam cracking and methane to olefins: Energy use, CO2 emissions and production costs, Energy, Vol. 33, Issue 5, May 2008, pp. 817–833.
6. Amghizar, I., Vandewalle, L., Van Geem, K. and Marin, G., New Trends in Olefin Production, Engineering, Vol. 3, Issue 2, April 2017, pp. 171–178.
7. Zimmermann, H., Walzl, R., “Ullmann’s Encyclopedia of Industrial Chemistry,” Wiley-VCH Verlag GmbH & Co. KGaA, Weinheim, Germany, 2009, pp. 465–520.
8. Middleton, J., Decarbonization of steam crackers, Decarbonization Technology, November 2021.
9. Chuapet, W., Limphitakphong, N., Tantisattayakul, T., others, A Study of Energy Intensity and Carbon Intensity from Olefin Plants in Thailand, The 3rd International Conference on Industrial Engineering and Applications, August 2016.
10. International Energy Agency (IEA), Achieving Net Zero Heavy Industry Sectors in G7 Members, May 2022.
11. International Energy Agency (IEA), Chemical and Petrochemical Sector: Potential of best-practice technology and other measures for improving energy efficiency, September 2009.
12. Lehle, T., CO2 Reduction Measures in Steam Cracker Plants, Chalmers University of Technology Dept. of Space, Earth and Environment, Gothenburg, Sweden, June 2022.
13. Guillaume, J., Overview of CO2 Capture Methods in the Petrochemical and Refining Industry, TIEEP Energy Forum, Houston, September 2022.
14. Mynki, O., Brown, D., Amghizar, I. and others, Reducing CO2 emissions of existing ethylene plants: Evaluation of different revamp strategies to reduce global CO2 emission by 100 million tonnes, Journal of Cleaner Production, Vol. 362, August 2022.
15. Young, B., Hawkins, T., Chiquelin, C. and others, Environmental lifecycle assessment of olefins and by-product hydrogen from steam cracking of natural gas liquids, naphtha, and gas oil, Journal of Cleaner Production, Vol. 359, July 2022.
16. Djokic, M., Van Geem K., Jeynderickx, G. and others, IMPROOF: Integrated model guided process optimization of steam cracking furnaces, Universiteit Gent Faculty of Engineering and Architecture, April 2017; www.improof.cerfacs.fr.
17. Jackson, S., The History of Ethylene Furnace Profiled Tube, published on LinkedIn, November 2021.
18. Moosavi, S. and Tahery, R., Integrating Gas Turbines with Cracking Heaters in Ethylene Plants, International Journal of Engineering Research & Technology, Vol. 3, Issue 6, June 2014.
19. Van Goethem, M., Barendregt, S., Grievink, J. and others, A kinetic modelling study of ethane cracking for optimal ethylene yield, Chemical Engineering Research and Design, Vol. 91, Issue 6, June 2013, pp. 309–318.
20. Vangaever, S., Van Thielen, J., Hood, J. and others, The Effect of Refractory Wall Emissivity on the Energy Efficiency of a Gas-Fired Steam Cracking Pilot Unit, Materials, Vol. 14, Issue 4, February 2021.
Author
Ghoncheh Rasouli is a product manager and R&D engineer focused on process simulation and modeling software at KBC Global (Email: [email protected]). She is an expert in industrial polymer process simulation with a focus on decarbonization and the circular economy. She holds a Ph.D. in chemical engineering from McGill University, with special focus on computational modeling of polymer-phase separation kinetics.