As regulatory activity surrounding per- and polyfluoroalkyl substances (PFAS) increases, there is a need to minimize the generation of fluorinated byproduct streams in the production of industrial processes. Some fluoropolymers — used extensively in industrial and consumer products, including pipes, valve components, distillation column internals, gaskets and seals, membranes and much more due to their unique properties compared to metals — have been conventionally manufactured via emulsion polymerization using fluorinated surfactants as a polymerization aid to encourage product homogeneity. Even processes utilizing non-fluorinated surfactants may result in the generation of fluorinated byproducts, and may not produce fluoropolymers with the same properties as those using conventional processing.
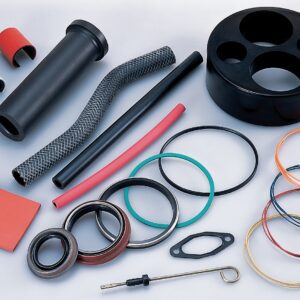
A large number of industrial products utilize fluorpolymers, and there is a need to develop moe environmentally-friendly production methods (Image source: AGC)
Now, a new manufacturing process developed by AGC Inc. (Tokyo) eliminates not only fluorinated surfactants, but any surfactant at all, from fluoropolymer production via emulsion polymerization.
“By using this technology, even without any surfactants, produced fluoropolymers demonstrate the same properties as those from conventional production processes, such as resistance to heat, cold and chemicals. Furthermore, the amount of individualized non-polymeric fluorinated byproducts contained in a product can be controlled to less than 25 parts per billion,” explains Jiro Nishino, general manager of the Performance Chemicals General division of AGC.
AGC is planning to start the commercial production of the technology by 2030 at the latest, and Mr. Nishino thinks that it would be possible to manufacture fluoropolymer products using the new method in the company’s existing facilities. “During development and commercialization, we are continuously taking into account feedback from customers. As part of our development process, we have also conducted sample testing with our customers,” says Mr. Nishino.
Fluoropolymers background
Fluoropolymers are primarily composed of carbon and fluorine in their chemical structure. Even minor variations in fluorination levels or the introduction of other elements can significantly impact their performance properties. These materials are categorized into two main types: perfluorinated and partially fluorinated. Partially fluorinated polymers contain hydrogen or other elements, whereas perfluorinated polymers, also known as fully fluorinated, are derivatives or copolymers of the tetrafluoroethylene (C2F4) monomer. Common commercial fluoropolymers include polytetrafluoroethylene (PTFE), perfluoroalkoxy polymer (PFA), fluorinated ethylene propylene (FEP), polyvinylidene fluoride (PVDF), ethylene tetrafluoroethylene (ETFE), and ethylene chlorotrifluoroethylene (ECTFE). There is much work underway to make the fluorpolymers supply chain more sustainable in the wake of PFAS regulations, including upcycling end-of-life and waste materials, and a wide range of PFAS water-treatment techniques, such as adsorbent materials; super-critical water; foam fractionation; induction heating; and electrochemical oxidation.