LED lighting can provide a safer alternative to conventional high-pressure sodium, and fluorescent lighting fixtures in industrial settings
In many chemical facilities, lighting is a necessary but challenging feat. Adequate illumination is, of course, essential to operations and worker safety, but maintaining safe and effective light levels is a never-ending chore. In fact, lighting is often taken for granted, a facet of facility operation that’s rarely given much attention, until it doesn’t work.
But lighting is actually a critical component of overall plant safety (Figure 1), and inadequate lighting can have a major impact on workers’ ability to do their jobs carefully and reduce the risk of injuries. According to U.S. labor safety statistics, poor lighting is the leading cause of slip, trip and fall accidents and incidents caused by contact with objects and equipment—the most common incidents after transportation accidents. With some 2.8 million workplace injuries [1] and nearly 5,200 on-the-job fatalities [2] in 2017 alone, improving facility safety should be a top priority for every company.
The problem is that most facilities rely on antiquated, outdated lighting, such as high-pressure sodium (HPS) and fluorescents. These sources are not only extremely inefficient, but they also perpetuate a host of safety concerns.
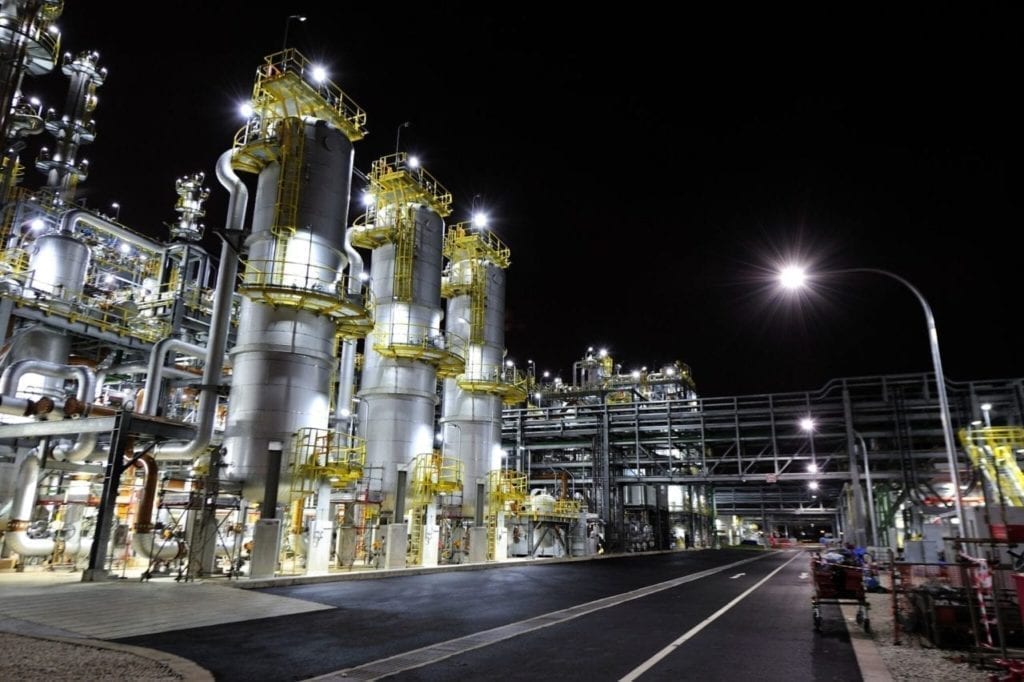
Figure 1. Lighting is a critical component for plant safety
The risks of poor lighting
Old lighting fixtures require frequent maintenance. HPS bulbs and delicate fluorescent tubes simply aren’t durable enough to withstand the harsh environment of a chemical facility. Not only are they prone to failure due to vibration and exposure to caustic materials, they also break easily. Because they contain hazardous materials — HPS bulbs contain mercury — broken bulbs expose workers in the vicinity to mercury. Over time, this chronic exposure can cause serious, permanent health issues.
Broken bulbs aside, simply changing bulbs is a dangerous job, often requiring the use of ladders or manlifts to access fixtures over top production equipment. This can put workers at risk of falling from dangerous heights or being struck by dropped tools or debris. And, because fixtures can be hard to access, many burned out lamps go unchanged until a site-wide maintenance shutdown. This results in poor visibility that only gets worse over time.
HPS fixtures are also notorious for poor color rendering, creating a dark, orange-ish glow that makes it extremely difficult to distinguish colors. This can be dangerous for workers when it comes to interpreting warning signs and placards that rely on color coding to communicate hazards. It can also be dangerous for electricians, for example, who must identify wiring schematics based on the colored coating — accidentally cutting the blue wire instead of the red because they’re indistinguishable can result in a dangerous incident.
Uneven light distribution can cause harsh shadows and dark areas that make it difficult for workers to see obstacles clearly or to detect peripheral movement. This lack of visibility often requires workers to use flashlights, giving up the use of one hand, or other auxiliary lighting, which creates additional trip hazards from extension cords and light stands.
That same dingy atmosphere can even impact workers’ mood and energy levels, causing them to feel drowsy, complacent and fatigued. This is especially concerning for second- and third-shift employees who are working against their natural circadian rhythms and may already be struggling with inadequate rest.
In the event of a power outage, both HPS and fluorescent fixtures can take up to 20 minutes to restrike and come up to full output. During that time, emergency lighting is typically inadequate for production to take place, forcing workers to stop what they’re doing and wait. In those first few dark moments, tripping hazards are a major concern.
Finally, extreme temperatures are not friendly to HPS or fluorescent fixtures. The excessive heat output of HPS bulbs makes them unsuitable for use in volatile or high-heat environments that call for T5-rated fixtures. Using HPS in this situation risks explosion of the fixture, creating an ignition hazard, as well as potential mercury exposure and broken glass.
Neither HPS nor fluorescents perform well in cold temperatures, which extends the restrike period and can cause condensation and ice to build up, which could fall and strike an employee or damage equipment.
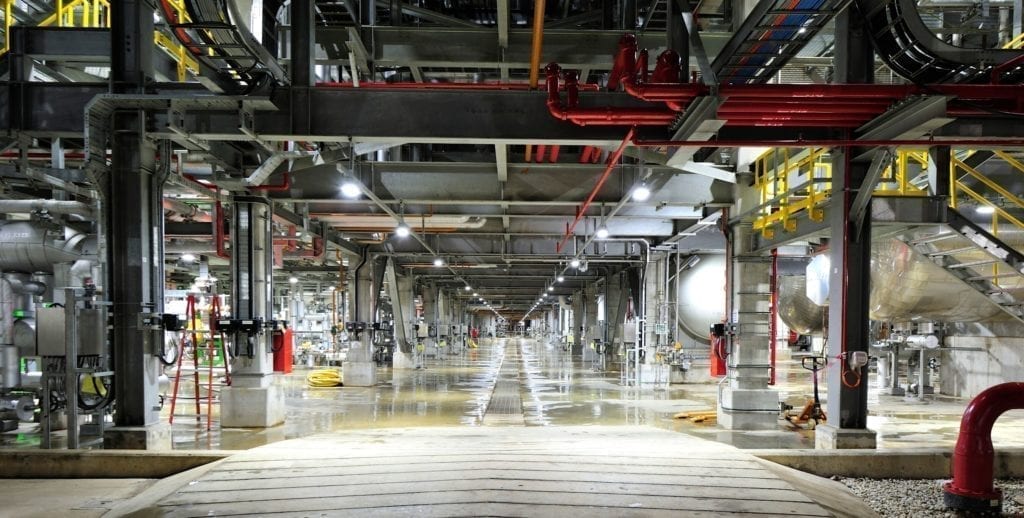
Figure 2. LED technology offers a range of Class I and Class II hazardous location certified options
LEDs provide a safer alternative
Upgrading antiquated lighting to more modern, efficient and safer technology is one of the simplest and most effective ways to improve chemical facility safety. Industrial light-emitting diode (LED) technology is well-suited for the chemical industry with a wide range of Class I & Class II hazardous location certified options available for maximum safety and environmental tolerance.
With higher efficiency, LED fixtures also outperform conventional fixtures when it comes to providing a safer, better illuminated work environment. LED lighting is much more durable and lasts far longer than HPS and fluorescents, virtually eliminating the need for lighting maintenance. This greatly reduces the risks workers face when performing lighting maintenance, including falls or electrocution. And, because LEDs contain no hazardous materials, there is no risk of exposure to toxic chemicals in the event of a fixture break.
LEDs also provide the light color to ensure visual acuity and color perception. With a color rendering index that mimics near daylight, this eliminates color ambiguity and enables workers to easily distinguish colors on safety placards, wiring and labels. Plus, the brighter light eliminates the need for flashlights and other extra lighting, freeing up workers to use both hands and keep tripping hazards out of the way.
In fact, a Centers for Disease Control and Prevention (CDC; www.cdc.gov) study found that LED lighting improves workers’ ability to detect trip hazards by 23.7%, and workers in a CDC/NIOSH (National Institute for Occupational Safety and Health) study were able to detect trip hazards 94% faster and peripheral motion 79% faster under LED lights compared to conventional fixtures. In a chemical facility, faster detection can mean fewer accidents.
That same crisp, near-daylight light has also shown to improve alertness and reduce fatigue in workers by a factor of five, suppressing melatonin levels and helping workers to be more engaged, aware of their surroundings and faster to react.
Because LED fixtures are much more tolerant of heat and harsh environments, they pose little risk of explosion, and LEDs actually perform better in cold temperatures over moderate temperatures.
Edited by Dorothy Lozowski
References
Author
Luis Ramirez is the chief operations officer at Dialight (1501 Route 34 South
Farmingdale, NJ 07727; Web: www.dialight.com) and is responsible for global operations, including: direct and contract manufacturing; supply chain, planning and logistics; quality, warranty and technical services; and sustainability initiatives.