Intermediate buik containers (IBCs) are commonly used to contain and transport flowable solid materials across many industry sectors. Provided here is an overview of the applications for which different types can be used, as well as their benefits
Intermediate bulk containers (IBCs) are extremely popular in industry because of their economics and convenience. They are used to safely contain and transport bulk quantities of liquids and flowable solids. The global IBC market is driven by the industrial, chemical, building and construction industries. In 2023, the food and beverage industry commanded the 5th largest share of the global IBC market [1].
This article is aimed at manufacturers, processors, shippers, warehouses and other industrial users of IBCs. The purpose is to provide an overview of the application and value of IBCs for industrial users. IBCs can be divided into two general categories: rigid (rIBCs) and flexible (fIBCs). See Tables 1 and 2 for a partial list of suppliers. Hybrid IBCs that are both flexible and rigid (collapsible) are not distinctly addressed in this paper. A set of definitions for terms used here can be found in the box below.
Rigid and flexible IBCs
Rigid IBCs (rIBCs) have a large portion of the overall IBC market, with a valuation of $9.0 billion in 2023 [2]. rIBCs are versatile, rugged containers that can be stacked, cleaned and reused. They are commonly made of plastic, metal, wood, corrugated cardboard or a combination of those materials. Units made of metal or plastic are intended to be reused and are designed for a useful life of up to 20 years [3]. According to Liquid-IBC Container and Rental Systems (liquid-ibc.com), stainless steel rIBCs are “by far the most popular” due to their United Nations (UN; New York, N.Y.; www.un.org) approval for use with hazardous goods. Some rIBCs are available with flexible plastic liners. Bag-in-box-style rIBCs protect the contents from contamination and maintain the container in a clean condition.
rIBCs include a top opening for filling and a side or bottom discharge port. Discharge ports are often equipped with a valve to retain the product. A few rIBC offerings include discharge valves with flow-modulating capability, but most are on/off valves. rIBCs for liquids are commonly cube-shaped and have a protective framework, or a cage, to maintain container integrity. Tapered outlets are observed on rIBCs used to carry powders. The vertical walls taper to promote discharge flow. Heating packages are available for some rIBCs carrying temperature-sensitive products. On the downside, rIBCs can be expensive, bulky and costly to ship empty.
Flexible IBCs (fIBCs; Figure 1) hold a significant portion of the overall IBC market. In 2023, the market size for fIBCs was valued at $7.6 billion [4]. fIBCs have many useful attributes, the first of which is price, followed by low mass and volume when folded for storage and shipping. fIBCs are normally made of polypropylene cloth and have a mass capacity of 1,000 kg. Liners may be added to to the fIBCs to make them hygienic, reduce maintenance requirements and improve cleaning costs [5]. Like other IBCs, reuse and recycling of fIBCs makes them more economical.
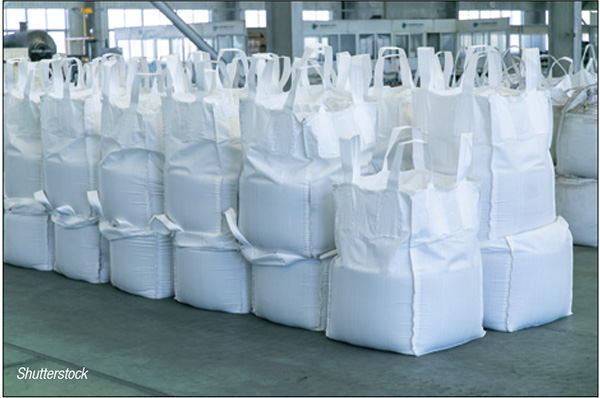
FIGURE 1. Flexible IBCs, like those shown here, have many attractive attributes when it comes to carrying solids, such as price and low mass and volume when empty
IBC configurations
According to Southern Packaging LP (Venus, Tex.; southernpackaginglp.com), there are five major configurations of fIBCs [6]:
U-panel. This type of fIBC is a three-piece bag with one “U”-shaped piece making up the bottom and two sides with two separate pieces making the other side panels. These are the most popular and maintain a square shape when filled.
Circular. This two-piece bag has one body tube and a base. The body tube is seamless. They are not truly circular and resemble a square bag when filled.
Four-panel. This a five-piece bag made of four side panels and a base. This configuration has more stitching than the first two, resulting in more opportunities for failure.
Baffled. This type refers to any of the previous three bags with baffles added. Baffles are fabric panels or strings sewn inside the corners of a bulk bag. Baffles improve stability, stackability, and capacity.
Single loop and double loop. Made of a single tubular body, the fabric is extended into lifting loops giving it greater strength and making it easier to lift.
Beyond the major configurations, bulk bags have a range of features available for specific products, applications and processes. One supplier (nationalbulkbag.com) claims to stock 75 types of fIBCs. Custom bulk bags are also available.
rIBCs are available in three main configurations, each with several optional features. The three main rIBC configurations are the following: cube, cuboid or cylinder; bag-in-box; and collapsible.
Most rIBCs have integrated pockets or openings for forklift tines, normally located near the base. Some rIBCs have lifting lugs. Almost all rIBCs are designed to be stackable.
IBC top openings
fIBCs have four main types of top openings that may be selected according to user needs. The four types are listed below:
Open. Open top openings are ideal for quick filling.
Tie down. A flap secures the contents. Flaps are favored for quick-filling applications.
Duffle. The sides of the bag extend up, resembling a duffel bag. Extended sides are gathered and tied to secure the load.
Spout. A cylindrical tube is sewn into the top of the bag and interfaces with filling equipment, providing a controlled filling method. The spout is a necked-down version of the duffle. A spout can be tied off or cinched to secure the load. The spout top is the most common opening on fIBCs.
rIBC top openings include manways, bungs, lids, vents and custom ports. Manways often include gaskets, screw, clamped or hinged lids. Custom options are available, such as the number of openings, diameter, fittings, threads, and location of accessories. Some lid configurations are designed to dock securely with other materials handling and processing equipment. Openings may include locking devices for security. Some rIBCs are equipped with grounding connections, pressure relief vents and atmospheric vents to meet safety and processing standards.
IBC bottom openings
Bottom opening options for fIBCs are more numerous than top openings. Several types are reported [7]:
Plain. In this case, no bag opening is included. Plain-bottom bags are cut open to discharge and are therefore single-use.
Spout. This is the most popular opening and consists of a tube sewn into the bottom panel. Tube dimensions vary, with 14 in. in diameter by 18 in. in length common.
Conical spout. Conical spouts are designed to alleviate the collection of materials in the bottom corners of the bag.
Duffle. The entire bottom of the bag opens for rapid discharge. Some duffle bottoms include a flap.
Diaper. A flap the size of the bottom of the bag is sewn onto one side of the bag and the other side is tied off (also known as a full drop).
Spout with flap. The spout (described previously) includes a flap to protect the bag’s contents.
rIBC bottom openings are similar to their top openings described above. Tapered sides, conical transfers and sloped bottoms may be added to help discharge contents.
fIBC lifting loops
Lifting loops are the “handles” located near the upper portion of a bulk bag. They are used to hoist the bag from above. The standard configuration is one loop attached to each of the bag’s top corners. Unique lifting loops and versions are available (elwayinc.com) in the following eight categories.
Standard. A single strap, forming a loop, with each free end attached to the same top corner of the bag, repeated at each corner.
Single stevedore strap. A single strap is threaded through the four lifting loops and the loose ends of the strap are connected.
Double stevedore straps. A strap is threaded through two adjacent lifting loops and the loose ends of the strap are connected. A second strap is similarly threaded through the remaining two lifting loops.
Ancillary loops. A loop is added around each of the four corner loops to extend them.
Hood lift. A panel is attached to opposite sides of the top of the bag, making a tunnel for lifting.
Side-seam loops. The standard loops are formed from four straps. Each strap starts and ends at a different bottom corner of the bag. The straps are fastened along the length (side seam) of the vertical corner of the bag.
Sleeve lift. Two loops of material are formed on opposite sides of the top perimeter of the bag. Each loop runs along the entire length of one side.
Cross-corner loops: In this case, four lifting loops are each attached to adjacent sides of the bag, near the same corner of the top perimeter of the bag. Loops are not attached to a side seam.
IBC handling
IBCs are made for handling with forklifts, pallet jacks, hoists and cranes (Table 3). A multi-purpose intake chute (Flexicon Corp., Bethlehem, Pa.; www.flexicon.com) allows operators to manually empty other containers into the same discharge chute used for IBCs and may include an optional dust collector. fIBC handling includes several specialty devices. A bag pre-inflator/de-aerator is available (Hapman N.A., Kalamazoo, Mich.; www.hapman.com) to remove folds and wrinkles in fIBCs before filling. Scale systems may be purchased for precision filling of fIBCs by weight. Custom breaker bars are available for lumpy powders. Breaker bars work in pairs to engage the fIBC from opposite sides and crush lumps in the gap between the bars. Flow-Flexer® bag activators (www.flexicon.com) raise and lower bottom edges of the fIBC to move materials toward the bag outlet spout. Pop-top™ bag stretching devices are designed to stretch the bag into a cone shape as the contents are discharging. A standalone bulk bag conditioner is available for resolving compaction issues separately from other handling steps. The Flo Series of fIBC unloaders (www.spiroflow.com) incorporates sloped hoppers with pulse vibration technology. Flexible Packaging Systems (www.fps.com) provides MAPGuard™ technology that is used to flush the air from the contents of an fIBC and replace it with a gas specified to preserve the contents. Vibrators and shakers are applied to rIBCs to encourage the flow of powders.
IBC liners
Liners are flexible bags that fit between the product and the interior surface of an IBC. They help to protect the product from contamination by air, moisture, residues, odor, electrostatic buildup and the IBC itself. Liners may also provide a barrier to sunlight and pests. There are many types of liners, including form-fit, gusseted, lay-flat, round-bottom, anti-static, perforated, vented, heat-sealed and barrier (palmetto-industries.com). Disposable liners facilitate the recycling of IBCs, while some liners are designed for multiple uses. Bag inflation is necessary before filling fIBCs [5].
Automation
IBCs fit well into automation schemes. They are designed to be managed, handled and transported by a range of standard and customized machinery. Incorporating IBCs into processes can result in widespread gains, including production costs and efficiency, improved quality, better customer satisfaction, reduced errors and higher levels of safety. Standard machinery used to automate the handling of IBCs includes forklifts, conveyors, pallet wrappers, elevators, loading and discharge stations, and scanning and tracking equipment. Dematic (Atlanta, Ga.; www.dematic.com) provides an example of customized automation of IBC handling. Dematic manufactures autonomous mobile robots (AMRs) to move pallets between functional areas. AMRs are flexible alternatives to manually operated forklifts and pallet jacks for transport distances greater than 31 m (100 ft), and pallet throughput under 400 per hour.
Filling and discharging
Filling and discharging IBCs are probably the two most important processes encountered in industry. While not trivial, filling operations are less complex than emptying and do not tend to be a process constraint. Filling is often regulated by weight or volume. During filling, air in the IBC is displaced by the product, and escapes through a vent, migrates to upstream equipment, or leaks out of the system. Holbrow [5] claimed that filling IBCs is the most hazardous operation due to material dispersion and acquired electrical charge. Electricity is generated by friction between moving particles of product and between moving particles of product and the IBC surfaces. The result, known as “triboelectrification,” is an electric charge transfer between two objects.
If a powder is charged as it enters a non-conductive IBC, the charge will accumulate due to the insulating properties of the walls. Discharges of electricity may ignite dust, gases or powders (Figure 2). Four main types of electrical discharge may occur during the filling and discharge operations of IBCs. They are called spark, brush, propagating brush and cone.
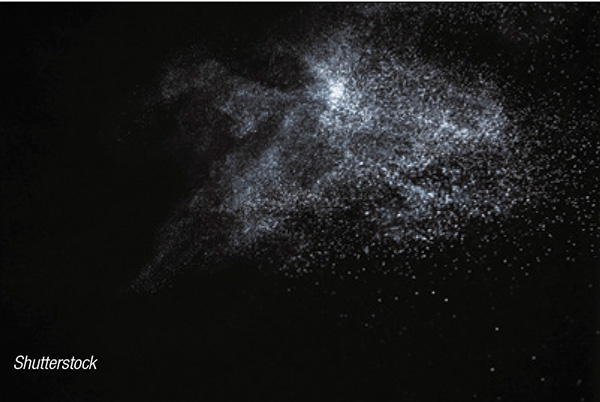
FIGURE 2. Friction between moving particles of products and between moving product and IBC surfaces can ignite dust, or gases
Sparks may occur from an isolated, conductive product or the IBC, with the associated energy depending on capacitance and voltage. Brush discharges occur from insulating bulk product and from IBCs made of insulating material. The energy required for a brush discharge is less than 4 mJ. Propagating brush discharges require several joules of energy and emanate from IBCs made of insulating material with high dielectric strength. Cone discharges occur from coarse, insulating, bulk product, and require less than 10 mJ of energy, depending on the surface area of the product and particle size [5].
The emptying process for IBCs has captured the attention of industry and some academics. Emptying can be a pinch point in operations, defining production throughput. The emptying process can also impact product quality and increase hazards. Uniform discharge is critical for powders. A mass-flow pattern is desired, where the material evenly discharges without preferential flow. Unfortunately, flow patterns from IBC discharge frequently fall into the category of core, or funnel, flow. Core flow occurs when a narrow flow channel opens from the outlet of the IBC to the top surface of the material. This flow pattern induces the separation of fine particles, which tend to discharge first [8].
Megarry and others [9] observed that core flow was common for IBCs used in multiple manufacturing steps. They also noted that the hopper angle and discharge area had a limited impact on the flow rate of fine materials from an rIBC. Accelerated particle movement, due to steeper hopper angles, was offset by vertical air movement. For a wider orifice, the pressure gradient increased, limiting flow. Based on video analysis, Megarry concluded that regardless of flow mode, an airburst was necessary for powder flow to initiate in unvented rIBCs. An airburst in an unvented rIBC was defined as a turbulent air channel opened in the material from bottom to top. The air burst through the powder bed to the headspace was required for the material to flow, similar to the case of emptying water from a bottle.
Megarry also identified a linear correlation between rIBC discharge rate and flow through an orifice. A similar correlation was also observed by Wickstrom and others [10]. They discovered that a simple model that relied on particle size and diameter of the discharge opening predicted IBC discharge rate. They also observed that powder flow is often accompanied by separation.
Equipment for aiding discharge. Matcon cone valve technology (West Evesham, U.K.; www.matconibc.com), used in rIBCs carrying powders, is designed to prevent core flow and bridging. The cone valve consists of an inverted cone sealed to the outlet of an IBC. The cone breaks the seal and rises into the powder material to open an annular flow path for the powder to discharge. Powder flow can be induced by lowering, raising, and vibrating the cone valve during discharge [8]. Matcon also supplies cone valves that can be mounted in silos, bins, and hoppers.
fIBCs have unique properties that can facilitate unloading. In automated systems, some unloaders include massaging arms, vibrating plates, and other devices that operate on the outside surface of the fIBC to encourage flow. Operators may manually massage or strike fIBCs to start and maintain flow.
A containment transfer system (CTS) enables the transfer of powders to or from an IBC while maintaining the containment of the material from the outside environment. Iris and pinch valves are part of a CTS for fIBCs. The discharge spout of the bag is pulled through the iris or pinch valve. The valves are closed to restrain material flow. The iris and pinch valves may be opened gradually to control flow. Pinch valves may be successfully closed when material remains in the spout. Rotary airlock feeders and discharge units are used to meter materials into and out of IBCs. Explosion-proof rotary airlocks also control dust and isolate the IBC in case of an explosion.
Powder consolidation, or compaction, in IBCs plays a key role in flow properties [9]. Origins of consolidation cited in Ref. 11 included dipole interactions (van der Waals forces), electrostatic interactions, capillarity, sintering and recrystallization. Powders are likely to be cohesive when the described forces are of the same order or greater than the weight of the powder. Cohesion also depends on the size of the particles. Smaller particles are more cohesive, and cohesion increases with compaction. For most materials, aging, humidity, and vibration may also increase compaction.
IBCs may be vacuum unloaded. A hose is inserted into the product through the top opening of the IBC and the vacuum removes the material. An antistatic or grounded conductive hose is often specified for safety [5].
For bag-in-box rIBCs carrying liquids, equipment is available to help promote product flow and emptying of the bag. A ratcheting device rolls the bag on a bar as it empties, simultaneously squeezing out contents. An automated tamping device to uniformly force the contents out of the bag is also available. rIBCs may be discharged using a dumper mechanism that retains the IBC while tilting and optionally lifting. Flowability of many liquids improve when heated. Silicone heating mats and jacketed walls are common solutions. Permanent heating pads and jacketed walls are available as an option for some IBCs, as well as removable heating pads and heated enclosures.
Powder additives for discarge. Additives are used to improve the flowability of powders and liquids for filling and discharging operations. Additives are normally combined with the material at its origin. Industry terms for flow additives include anti-caking agent, glidant, lubricant, flow aid and flow promoter. Flow additives can be an advantage to the consumer when a bulk material is the final product. Flow aids are subject to limits like cost, regulatory restrictions, product compatibility, and effectiveness. Some flow additives may have additional benefits such as a flavor carrier, colorant, scent carrier, tablet disintegrant, or structural reinforcement [12].
Mixing
rIBCs are convenient mixing vessels. Mixing occurs by rotating the rIBC. Since the rIBC remains closed during mixing, the contents are not exposed or transferred to other equipment and the environment. Assuming no leaks, the mixer does not need to be cleaned between batches. An rIBC should be about two-thirds full to achieve the best mixing results [8]. After mixing, an rIBC may be connected to a filling machine or batch tank for transfer, avoiding the potential of degradation due to transfer from a separate mixer.
Dust and dust explosions
Dust control is an important aspect of safety and hygiene when using IBCs. Dust may be classified as particles smaller than 0.5 mm in diameter. Most solid materials are flammable, and when formed into a dust cloud (with air), may explode. A guiding principle to preventing dust explosions is to avoid dust. Unfortunately, dust is present in most materials. During conveying, fines can accumulate in the headspace of the receiving container. Dust control is accomplished in IBCs and associated equipment by containment and extraction. Containment is a strategy to keep dust in a defined space. An enclosure, like the Containment Transfer System (CTS) described above, creates a space where dust is permitted. Extraction of dust is accomplished by removing dust from a volume or surface. Dust is removed by air entrainment, then separated from the air in a downstream step.
The speed of a dust explosion increases with a decrease in particle size and typically takes a few hundred milliseconds [13]. Flammable concentrations of dust may appear occasionally in a process. Examples include fines from the bottom of a bin fed into a silo, dust sticking to a vessel released by a disturbance and a collapsing bridge that creates unusual flow conditions.
Dust explosions require five elements: fuel, oxidant, mixing of the fuel and oxidant, confinement and ignition source. If the explosion is not confined, it will result in a flash fire [13]. The first four elements normally occur in dust-handling equipment and infrequently in other spaces, such as silos, receiving vessels, sifters and mills. The most common ignition sources are fire, welding and cutting, electrical equipment, mechanical sparks, static electricity, hot surfaces and self-heating materials. A secondary dust explosion occurs when dust is raised to a cloud by a primary explosion and is subsequently ignited. The secondary explosion is often more devastating than the first and can be responsible for the collapse of an entire building. The quantity of dust required for a secondary explosion is relatively small [13].
Two options are available to control dust explosions. The first is to remove the oxidant by replacing air with an inert gas. The second is to remove ignition sources. Protection from explosions is accomplished through containment, venting, and suppression. In every case, the propagation of an explosion must be prevented. Explosion vents for enclosed spaces are incorporated to displace the explosion to another area (frequently outdoors). A huge flame jet or fireball is created outside the vent during an explosion. The size of the fireball is often underestimated. Explosion vent openings of sufficient size are critical.
Explosion suppression is used to prevent the propagation of an explosion from one vessel to connected vessels. Pressure piling and flame acceleration are important effects. The pressure in the secondary vessel could be 10 times higher than the first. Turbulence in the second vessel is also much higher, contributing to a more explosive environment [13].
Process developers control explosion propagation by disconnecting vessels. When disconnection is not possible, explosion-proof rotary valves should be used to connect vessels where propagation may occur. The rotary valves should be configured to automatically stop during an explosion. Other options include using a diversion valve to direct an explosion to a vent, and advanced inerting barriers.
Static hazards with IBCs
The electrostatic properties of IBCs are important for safe usage. Normally, the charge density of a liquid is much lower than a powder, making powders the main safety concern. Safety requires conductive containers or dissipative grounding. Many IBCs are made of non-conductive materials which necessitate safety measures. For conductive and dissipative containers, a ground will drain off charges.
Pekkala and others [14] studied electrostatic discharges from IBCs. Peak current was higher and duration was longer for discharges from surfaces with negative polarity. They found this result agreed with observations reported in the literature. In cases reported, a threshold surface potential was required before an electrostatic discharge would occur.
fIBC bags come in four main types with regard to electrostatic protection [7].
Type A. No electrostatic protection
Type B. Made of materials that have a low breakdown voltage (less than 4 kV) to prevent the occurrence of brush electrostatic discharges
Type C. Electrically conductive (resistance less than 108 Ohm) or can be grounded
Type D. Anti-static bags made of protective fabrics that do not need to be grounded (fabric dissipates electrostatic charges via corona and enhanced surface conductivity)
Investigations have shown that reliably grounded, Type C fIBCs are the top choice for safe handling in environments with explosion hazards. Type D fIBCs do not generally remove enough charge, by corona discharge, to avoid spark discharges [15]. Generally, higher charges are generated when filling an IBC compared to emptying. This is especially applicable for fIBCs [16].
Britton [17] reported on static hazards associated with fIBCs used for powder handling, and drew the following conclusions:
fIBC design considerations.
- Grounding system failures lead to sparks in the spout region. Failures were attributed to manufacturing defects (of the bulk bag), and improper grounding.
- Fully conductive fIBCs were preferred over antistatic types since discontinuities in the internal grounding were not an issue.
- Smaller fIBCs (300 to 500 kg) were judged to be safer than larger capacity bags. Larger sizes increase the possibility of bulking brush discharges during filling, and greater capacity may increase problems with dust clouds, air entrainment and explosions.
- fIBCs are known to entrain air when unloading powders. In flammable atmospheres, an intermediate hopper and a rotary feed valve should be implemented.
Operator grounding.
- Ungrounded operators working around 100% plastic fIBCs are in danger of receiving an inductive charge from the bag. This charge can create an ignition risk by sparks from the operator to the ground (note that 100% plastic fIBCs are not allowed in flammable gas environments).
- Operators should be grounded in flammable environments regardless of fIBC use.
Vacuuming. Conductive vacuum hoses should be used to empty and clean fIBCs.
Powders in flammable gas.
- A flammable atmosphere must be controlled.
- Conductive, grounded fIBCs could be used to mitigate hazards.
- Antistatic fIBCs with isolated threads may be safer.
- Conductive polypropylene threads improve the reliability of antistatic fIBCs based on thread breakage.
Powders in air.
- Due to grounding errors, 100% plastic fIBCs are preferred.
- Filling and emptying large fIBCs with sensitive powders could be performed with inert gas.
- Lower capacity fIBCs may still be hazardous due to propagating brushes and sparks. Brushes may be avoided with fabrics having a 4 kV maximum breakdown voltage at the wall. Grounding the bag and maintaining dry conditions will eliminate sparks.
Non-flammable powders.
- These are normally handled in 100% plastic fIBCs.
- In a flammable atmosphere, a static hazard is possible.
- In coarse granule and pellet transfers in air, a shock from personnel through the sides of a 100% plastic fIBC is possible.
Product quality. Static discharge can create pinholes in a liner. Pinholes may be present in used and recycled bags with liners, and could negatively impact product quality, especially related to moisture content.
Safety
IBCs are often used to minimize operator exposure to substances, especially in the pharmaceutical industry. In this case, the containment of dust is essential throughout operations and storage. Flammable powders may be stored in IBCs, which are regarded as “weak” containers that are likely to rupture in the event of an explosion. When explosion venting is used, it is preferred to install the vent in ducting upstream of the IBC and away from personnel. An IBC explosion could result in damaging fires, destruction of property, and injury of personnel [5].
Explosion suppression
Explosion suppression systems are said to be the most universal method of protecting assets and personnel from the effects of an explosion. An explosion suppression system consists of a detector, control unit and suppressor. When ignition occurs, the explosion is detected by pressure sensors. On detection of the pressure surge, the control unit activates the suppressor. The suppressor discharges material to extinguish the explosion before it expands.
Explosion isolation is needed to prevent an explosion from moving from one space to another. Isolation reduces the damage and simplifies the measures required. As an explosion moves from vessel to connected vessel, the pressure increases, along with turbulence and gas flow. A process that includes IBCs can be designed for isolation by avoiding the connection of vessels. Other isolation options include rotary valves, vents, and inerting.
Inerting refers to the process of introducing inert gases (for example, nitrogen or carbon dioxide) to the atmosphere inside an IBC and associated equipment, connecting pipes and valves. The inert gas displaces the air (including oxygen) that occupies the space, preventing explosions. Inerting is also a common quality control procedure employed to reduce oxidation of the product. Inerting and grounding are often applied together. When inerting is practiced for safety, oxygen monitoring with automated shutdown and other safety measures are required to prevent explosions and maintain safety.
National Fire Protection Association (NFPA; Quincy, Mass.; www.nfpa.org) code 30 permits only listed and labeled IBCs for storage and handling of flammable liquids with a flashpoint of 38ºC (100ºF), or greater, in an industrial building. The code is enforced in most states. Transportation regulations do not require IBCs to meet NFPA code 30. Consequently, hazards created by storing unlabeled and unlisted IBCs may be significant [18].
Humidity and condensation
For certain products and environments, condensation may occur inside IBCs, causing loss of quality and contamination. Moisture migrating from a product may condense on the inner surface of the IBC. Another example may occur when IBCs are moved from ambient to refrigerated storage. Condensation may form due to warm, humid air inside an IBC contacting the cooler, inner surface of the IBC and the product layer contacting the walls of the IBC. Butts and Lamb [19] examined temperature and humidity conditions in stacked fIBCs of shelled peanuts. They found that exchanging the air in IBCs as quickly as possible after placing the filled containers into cold storage would prevent damage due to condensation and associated mold growth. Exchanging air in IBCs is difficult considering logistics, equipment, and space available.
Other studies reported by Butts and Lamb examined fIBCs with different breathability characteristics of the top and side panels to prevent condensation. Incorporation of fabric that far exceeded breathability specifications for a typical fIBC did not have a clear benefit. The risk of mold growth for peanuts was greater during the summer months when peanuts were shelled during hot weather and placed directly into cold storage.
Damage and spills
Guerin [20] investigated spills of lubricants from IBCs. He recommended checking for IBC damage in the chain of custody. Most damage he recorded occurred at the lower portion or underside base of the IBC. Guerin noted that many IBCs had little protection from contact or puncturing by forklift tines. In addition, very few IBCs had features to capture spilled contents. Guerin recommended that a spotter be used when handling IBCs to reduce the risk of spilling.
The Flexible Intermediate Bulk Container Association (FIBCA; St. Paul, Minn.; www.fibca.com) published a list of safe handling guidelines for fIBCs. Its list includes six general guidelines that are summarized below and detailed further in Ref. 21. The list would apply equally to most IBCs:
1. Consult with the source to select the right fIBC for the application.
2. Check approval of the fIBC for the product, environment and processes
3.Check for product compatibility with the fIBC materials and components
4. Ensure that each fIBC is free from damage that could compromise strength
5. Follow the manufacturer’s recommendations and information printed on the fIBC label.
6. Comply with regulatory and safety requirements.
Traceability
Location, tracking, ownership, history of use and repairs of IBCs may be tracked using asset tags, including serial numbers, barcodes and radio-frequency identification (RFID). Barcodes and RFIDs are scanned, and the location of the IBC is automatically updated in a centralized asset management system. The asset management system gives the user instant access to the number of IBCs in the facility, their location, contents and other logged data. This information can be relied upon for regulatory compliance, safety programs, quality schemes, proof of delivery, logistics, and improved maintenance.
Reuse or recycling
Most IBCs are designed for reuse or recycling (Figure 3). They can have a lifespan of many years, depending on the container design and contents carried. Reuse of IBCs translates to reduced waste of materials, labor, and other manufacturing resources. The cost of IBC reuse may include cleaning, shipping, inspection and repair. Cleaning and reuse of IBCs can lead to more sustainable processes.
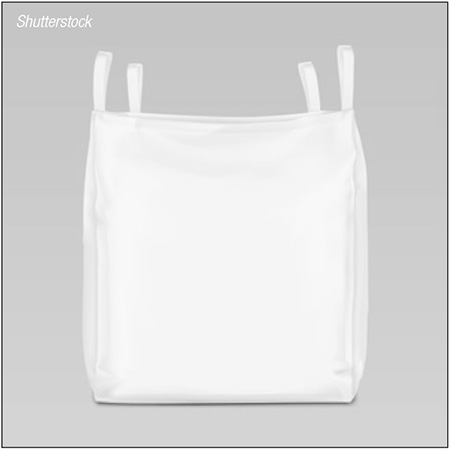
FIGURE 3. Most IBCs are designed for reuse and recycling, and their lifespan can be several years, depending on use
Biganzoli and others [22] conducted a study aimed at assessing the environmental impact of the lifecycle of IBCs (via lifecyle assessment methodology). IBCs were washed between uses with hot water and chemicals. Wastewater generated was treated on-site in a typical biological sewage treatment plant. On average, 25% of the IBCs could not be washed clean and were sent to incineration for destruction. Steel and plastic containers were sent to recyclers. Results showed that the impact of reconditioning was modest compared to producing new IBCs. Reconditioning and reuse are preferred to single-use, and benefits increase with the number of reuse cycles.
The cleaning and sanitizing of rIBCs is a standard application for automated clean-in-place (CIP) systems. Automated washers that clean the inside and outside of rIBCs are available from several manufacturers. A single operator can manage a semi-automated CIP system with high capacity. Disposable IBC liners can also be discarded and replaced. Some fIBCs (without liners) are claimed to be cleanable, but measures are required to remove residues trapped in wrinkles and within the fabric.
Testing requirements
Owner or lessees of an rIBC used for transporting hazardous materials must keep records of periodic integrity tests, per 49 CFR 180.352 (f). Integrity tests include the following:
• Internal pressure test (2.9 psig), every 30 months
• External visual inspections (every 30 months)
• Internal inspections (every 60 months)
Repairs must conform to the rIBC’s original design and test requirements. Inner bodies of plastic or composite rIBCs may not be repaired.
Edited by Scott Jenkins
References
1. Fortune Business Insights, IBC Market Size, Share and Industry Analysis, Fortune Business insights report, updated February 2025, (https://www.fortunebusinessinsights.com/intermediate-bulk-container-market-109253)
2. Towards Packaging, Rigid Bulk Packaging Market Size, Consumer Insights and Growth Strategies, Towards Packaging report, January 2025, www.towardspackaging.com/insights/rigid-bulk-packaging-market-sizing
3. Raymus, G. J., Handling of Bulk Solids and Packaging of Solids and Liquids, Section 21 In Perry’s Chemical Engineer’s Handbook, edited by R. Perry, D. Green, and J. Maloney, 1–78. McGraw-Hill Companies, Inc., 1997.
4. Toward Packing, Flexible IBC Market Size, Competitive Landscape and Future Outlook, Towards Packaging report, (www.towardspackaging.com/insights/fibc-market-sizing)
5. Holbrow, P., Explosion Hazards and Protection in the Use of Intermediate Bulk Containers, IChemE Symposium Series, no. 150, 2004.
6. Southern Packaging LP, Understanding FIBC Types, blog post, July 10, 2023, www.southernpackaginglp.com.
7. Palmetto Industries, Types of FIBC bags, Resources Section, www.palmetto-industries.com
8. Cooper, P. Practical Solutions to Critical Solids Handling Problems. In Special Publications, edited by W. Hoyle, 29–41. Cambridge: Royal Society of Chemistry, 2007.
9. Megarry, Andrew, Håkan Wikström, Frida Bilén, Johan Remmelgas, Alexander Liljeblad, and Pirjo Tajarobi. Bench to Batch: Linking Pharmaceutical Powder Flow Characterisation, Intermediate Bulk Container Discharge and Video Observations. International Journal of Pharmaceutics 635, March 2023.
10. Wikström, Håkan, Johan Remmelgas, Sara Solin, Mariagrazia Marucci, Niklas Sandler, Catherine Boissier, and Pirjo Tajarobi. Powder Flow from an Intermediate Bulk Container – Discharge Predictions and Experimental Evaluation. International Journal of Pharmaceutics 597, March 2021.
11. Ryck, A. De. Experimental Observations of Powder Consolidation. In Special Publications, edited by W. Hoyle, pp. 112–19. Cambridge: Royal Society of Chemistry, 2007.
12. Harnby, N., Flow Aid Technology, In Special Publications, edited by W. Hoyle, pp. 82–92. Cambridge: Royal Society of Chemistry, 2007.
13. Zeeuwen, P., Explosion Hazards in Powder Handling and Processing: The Changes Ahead. In Special Publications, edited by W. Hoyle, 11–28. Cambridge: Royal Society of Chemistry, 2007.
14. Pekkala, P., Paasi, J., Hearn, G. and Smallwood, J., Characteristics of Electrostatic Discharges from Intermediate Bulk Container Materials. Journal of Electrostatics 63, no. 6–10, June 2005, pp. 489–494.
15. Luttgens, G. and Luttgens, S., Preventing Electrostatic Hazards of Flexible Intermediate Bulk Containers. In Conference Record of the 2000 IEEE Industry Applications Conference. 35th IAS Annual Meeting and World Conference on Industrial Applications of Electrical Energy, 1:666–69. Rome, Italy: IEEE, 2000.
16. Lüttgens, G., Jordan, E. and Lüttgens, S., IBC (Intermediate Bulk Container): A Safety Risk in Industry?, Journal of Electrostatics 63, no. 6–10, June 2005, pp. 517–522.
17. Britton, L.G., Static Hazards Using Flexible Intermediate Bulk Containers for Powder Handling. Process Safety Progress 12, no. 4, October 1993, 240–250.
18. National Fire Protection Association (NFPA). Intermediate Bulk Containers (IBCs) General Fact Sheet. Available at: www.nfpa.org/downloadable-resources/fact-sheets/intermediate-bulk-containers-ibcs-fact-sheet, 2014.
19. Butts, C.L. and Lamb, M.C., Temperature/Humidity Conditions in Stacked Flexible Intermediate Bulk Containers for Shelled Peanuts. In 2014 ASABE Annual International Meeting, pp. 1–11. American Society of Agricultural and Biological Engineers, 2014.
20. Guerin, T.F., An Investigation Into the Root Cause of a Spill From Procuring and Handling of Lubricants in Intermediate Bulk Containers. Environmental Quality Management, 24, no. 4, June 2015, pp. 23–50.
21. FIBCA, FIBC Safe Handling Guidelines, V 2.0., 2017. Available at: https://fibca.com/wp-content/uploads/2017/09/FIBC_Handling_Guidelines_PrintVer.pdf.
22. Biganzoli, L., Rigamonti, L. and Grosso, M. Intermediate Bulk Containers Re-Use in the Circular Economy: An LCA Evaluation, Procedia CIRP, 69, 2018, pp. 827–832.
Author
Tim Bowser is a registered, professional engineer with over forty years of experience in food processing. He is a professor of food process engineering at Oklahoma State University (Stillwater, OK 74075; Phone: 405-744-6688; Emaill: [email protected]). His responsibilities include technical assistance to entrepreneurs and food processors, as well as research and development of food processing equipment and techniques, and establishing outreach programs in food engineering. His industrial experience includes positions at the Gerber Products Company and Lockwood Greene Engineers (consulting), and co-owner of PetMech, LLC (pet food/product development and testing). He holds a Ph.D. in Agricultural Engineering from the University of Tennessee and M.S. and B.S. degrees in Agricultural Engineering from Penn State. He is a licensed professional engineer in Oklahoma and Texas.