The chemical process industries (CPI) are exploring and investing in multiple technologies and operational improvements, striving to create smarter plants and more efficient processes so they can continuously improve productivity, sustainability and safety in their operations.
These factors are pushing manufacturers in every industry segment to “do more with less.” While different industry segments face specific challenges, doing more with less means finding better ways to increase productivity and differentiate chemical production processes using technology to identify which processes to invest in that have a greater value and return on investment (ROI).
Along with these investments, chemical companies work to improve sustainability, advance decarbonization and limit or reduce the use of natural resources. They recognize the need to have better insight into where waste is occurring in the production process and the best technologies that can be applied to drive this waste out of their systems, or, if possible, reuse waste as a source of selected components.
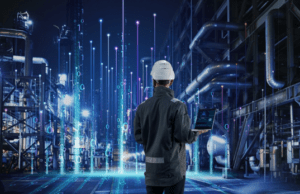
FIGURE 1. A comprehensive approach to digital transformation in chemical manufacturing allows companies to utilize technology and expertise better than ever before. (image courtesy of Emerson)
CPI companies that want to stay competitive and grow their businesses are using digital transformation to drive process optimization across their operations (Figure 1). They are expanding the use of smart sensors, measurement devices and automated valve systems (Figure 2) for greater efficiency and more process data. They are using control systems with built-in redundancy and support for major communications protocols, as well as open, scalable and modular software for both pilot applications and industrial plants.
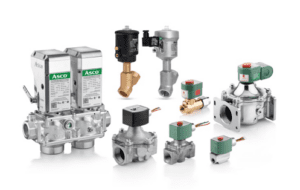
FIGURE 2. Chemical companies starting their digital transformation journeys can begin with valves, sensors and actuators on the plant floor
Additionally, CPI companies are making major investments in advanced edge computing and cloud-based analytical technologies to gain the kind of real-time visibility into their processes that supports efforts to boost productivity and sustainability at the same time.
Starting with pilot projects to drive transformation
Taking a digital transformation approach that starts with a specific challenge or issue allows companies to better exploit technology and expertise and begin to implement a scalable technology strategy.
Many companies are at different stages of their digital transformation journeys. Smart technologies enable the industry’s workforce to see real-time data, make decisions based on it and act based on those informed decisions, taking the best steps to meet and exceed their productivity and sustainability targets.
This includes improving overall equipment effectiveness (OEE) through access to new and trapped data from across production platforms. It is these data that can increase energy efficiency, reduce waste and support expanded use of recycled materials, such as reusing polymers to obtain base monomers in a circular way.
Chemical manufacturers can successfully use digital transformation through staged development of these systems using small production plants — laboratory, pilot or semi-industrial scale — depending on the size. This lets them capture critical data and rapidly analyze it to see if the targeted improvements in energy efficiency or waste reduction are achievable.
Fast, real-time data capture and analysis at this scale can utilize the latest edge computing technology and edge controller platforms. These tools are easy to implement and create an integrated and smart automation solution. Edge devices are typically available with built-in cybersecurity features and are engineered to aggregate process data streams and push that data to software that contextualizes and presents it on a dashboard.
Edge controllers also bring significant computational power extremely close to the process they are controlling. In addition, many are designed to operate in areas where they are exposed to extreme temperature or environmental conditions.
The control functions that edge controllers provide are critical. They can perform thermodynamic calculations according to specific technical standards right at the plant or even above the process unit they are controlling. This makes it possible to avoid any delay in the calculation of key performance indicators (KPIs). It also reduces the demand for data transmission bandwidth that needs to be delivered to central control units locally or communicated to plant operators and managers remotely.
In addition, edge controllers (Figure 3) can support process-simulation algorithms and machine-learning routines to provide immediate process insights directly at plant level. These and other technical capabilities demonstrate the value of investing in digital transformation in chemical processing applications.
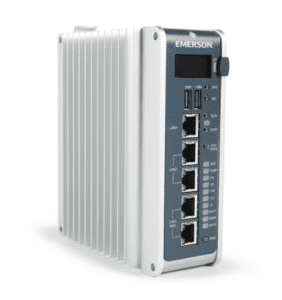
FIGURE 3. Edge solutions can generate, distribute and show significant results rapidly, especially on projects with tight timeframes
Edge solutions like these can generate, distribute and show significant results rapidly, especially on projects with tight timeframes. For example, an ammonia production facility used state-of-the-art automation and controls to successfully conduct and complete a tight, 60-day production test and acceptance requirement. If the test had to be stopped and restarted, heavy additional costs would have been incurred and negatively affected the plant’s financial performance.
The plant implemented a digital transformation approach using predictive maintenance software and a specially developed sensor and alarming suite. It gives operating personnel real-time alerts if key instruments, control valves or rotating equipment begin to show signs of degradation so corrective action could be taken.
The investment paid off. Not only did the plant successfully complete acceptance testing, but the fast startup also produced several million dollars in extra revenue due to increased uptime.
Using a pilot test to full deployment approach drives digital transformation in two critical ways. On the one hand, it allows management to quickly demonstrate the profitability of new technologies, processes and products. Equally important, pilot-plant implementation with internal company resources creates a cadre of plant-operating associates and process managers with hands-on experience with this technology.
When systems and platforms are leveraged across multiple plants and operations, these experienced personnel can help facilitate the scaling-up with colleagues and become advocates and drivers for further digital transformation.
Scaling automation to maximize value
Fully scaling digital transformation technology across the entire enterprise is the ultimate goal, merging the digital machine with the smart factory and then expanding the impact of those enhancements across the entire operation. Chemical companies can apply this approach to a single machine, a line, a plant or an entire enterprise to provide real-time visibility and control to optimize results. Organizations that already have large, distributed control systems in place can benefit from this approach, as it perfectly integrates and adds value to existing control units, exchanging data via standard industrial protocols.
Leading automation technology suppliers have broad technology portfolios engineered and integrated to advance chemical manufacturing transformation. These include smart sensors, valve controls and software to collect data across the plant floor. These devices are connected by high-speed, feature-rich edge controllers to efficiently move the data and analytics software to translate it into actionable insights.
Whatever stage chemical companies are at in the digital transformation process, it is important that any new investment increases performance and sustainability. Collection of data from sensors, data storage, data processing and management in real time are essential starting points. Chemical manufacturers that work with automation technology suppliers with digital transformation expertise are at an advantage. With expert guidance, they can upgrade their systems in ways that result in the outcomes that matter most.
The digitalization of sensors, the scalability of controllers, the openness and power of visualization software, the KPI generation and processing — all are key attributes to consider, then match with specific performance, productivity or sustainability challenges that must be solved.
Advance sustainability through smarter automation
Automation technology is clearly key to transforming efforts by CPI companies to improve sustainability and combat climate change. From the factory floor up through the cloud, digital transformation can impact sustainability efforts by reducing the causes of unexpected shutdowns.
Real-time monitoring and clear performance indicators improve process optimization and refining thresholds. Ultimately, these data can be used to conduct root-cause analyses based on alarm chains.
Precise, real-time visibility into chemical production processes can advance decarbonization efforts, reducing energy peaks generated by sliding and malfunctions. In addition, real-time data and well-designed dashboards can help improve operator and plant safety, thanks to greater visibility into the processes and stoppage causes.
Pilot-plant testing of digital sensor, smart valve and edge controller technologies should include waste reduction, energy efficiency and other sustainability goals as part of the overall development program. If the digital technology’s process improvement and sustainability benefits are proven at a pilot-plant level, it should be possible and less risky to use the same sensors, control valve, edge computing and analytics for rapid and immediate scale-up into production plants, leveraging existing internal resources.
A holistic approach to transformation
The CPI have long embraced — and even developed — safety, sensor and automation technologies to keep its processes operating with peak throughput and efficiency. But innovation and process improvement never stop.
The latest generation of digital automation technologies offer the potential to drive new levels of productivity, increased operator safety and waste reduction. Taking a comprehensive approach to digital transformation weaves smart technology throughout every part of chemical manufacturing machines, production lines and entire plants, with the ability to demonstrate quick return on investment at small scale and scaling up by using the same set of hardware and software.
Investing in data-driven systems will generate new levels of visibility into process performance with actionable data. Connecting production lines, plants and entire global enterprises gives chemical companies new tools to rapidly assess an investment’s profitability and value. That’s the goal of transformation: to make better, more fully informed decisions about new investments and process changes, help reach sustainability objects and drive long-term competitive advantage. ♦
Edited by Mary Page Bailey
Author
Martino Caranti is a chemical engineer who has managed R&D teams in companies of the chemical and biotech sectors. Currently he is Italy & Israel leader, Controls & Software, for Emerson Discrete Automation. Caranti has held various roles, including proposal manager and commercial director at packaging and converting machine manufacturing companies in Bologna, Italy. His experience includes serving as head of strategy for the advanced packaging sector, marketing manager of the EMEA Region and sales manager for Italy, Israel and Eastern Europe in multinational companies. He holds a European patent (EP0957150) and is an author of several books and over 200 publications, focusing his expertise on technology, automation and digital transformation, communication and team management.