Turndown and rangeability have a big impact on the flexibility and efficiency of chemical process operations
During the design of a chemical process plant, the main focus is on which process units or unit operations must be integrated to convert the feed streams into product stream(s). Design engineers work to achieve this goal; however, in terms of making sure the plant operates smoothly, which is equally important for operation engineers and operators, there are less well-know parameters facing the design engineers.
There are five primary process parameters in each plant — flow, (liquid) level, pressure, temperature, and composition. Composition can be considered a collective term that reflects all parameters (chemical and physical), and provides an indicator of the quality of the stream. Composition can be used to describe the moisture of a gas stream or the octane number of a gasoline stream, or even the electric conductivity of a water stream.
During operation, equipment process parameters generally deviate from the design values (normal level) over time. Five levels can be defined for each process parameter: normal level, high level, high-high level, low level and low-low level. In essence, the operational parameters of a plant relate to the behavior of the plant between the low level and high level of each parameter of the individual equipment components, individual units or the entire plant. In most cases, the operability of a plant can be defined using at least three key parameters: flexibility in operation, resistance against surge (or upset) and the speed of recovery from upset.
Maintaining operating flexibility
Flexibility of operation in this context means the ability of a plant to operate reliably across a wide range of flowrates without sacrificing the overall quantity or quality of product(s).
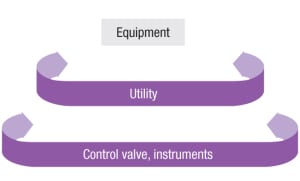
Figure 1. Different elements of a plant need different levels of operating flexibility. Since the utility network provides support duty to the equipment, it needs a higher turndown ratio. Control valves and other instruments have a duty to take care of equipment across a wider operating range; thus they require an even higher rangeability
From a process standpoint, a chemical process plant is a combination of equipment, utility networks and control systems. To design a plant with sufficient flexibility, each of these three elements needs to allow flexibility. Generally speaking, the control system (including control valves and sensors) and utility network should offer the largest amount of operating flexibility, while the equipment itself could offer the lowest amount of flexibility (Figure 1). This requirement for larger flexibility for control items and utility network considerations is important because of the supporting role of the utility system and the controlling role played by instruments in a plant.
Two important concepts are used to quantify flexibility: turndown (TD) ratio and rangeability. These are discussed below, and illustrated in Figure 2.
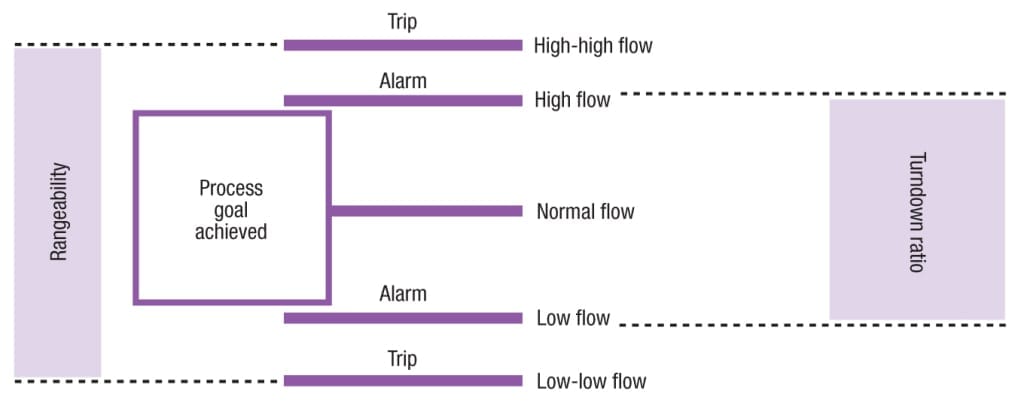
Figure 2. Process plants typically define different threshold values for flowrate levels, and set appropriate alarms and trips when the threshold values of this important parameter are reached. The concept of turndown ratio and rangeability are shown, in relation to these key threshold flowrate values
Turndown ratio
The flexibility of equipment or a plant can be defined using the TD ratio. The most common definition for TD ratio is “ratio of the normal maximum parameter (numerator) to the normal minimum parameter (denominator).” However, the meaning of “normal maximum parameter” and “normal minimum parameter” is not always clear and the interpretation may vary in different companies and plants (This is discussed below).
For an individual equipment component, or multi-component equipment systems, low-flow or low-capacity operation happens frequently over the lifetime of a plant. The reduced-capacity operation may be intentional or accidental.
For instance, reduced-capacity operation could be planned for the purpose of off-loading the equipment for inspection, testing, monitoring, or even to support the shutdown of downstream equipment. But it may also occur accidentally due to, for example, a drop in feed flowrate.
But process plant operators like to know by how much the flowrate of the equipment (and in the larger sense, the entire plant capacity) can be decreased without compromising the process goal or generating off-specification product. Thus, TD ratio can be defined as the ratio of high flow to normal flow, as shown in Equation 1.
Q High = the flowrate of the system at high level
Q Low = the flowrate at low level
The numerical value of the TD ratio is typically reported as a ratio, such as 2:1.
It is important to note that the denominator term is flowrate in low level, and not low-low level. This is important as it is the differentiator between the concept of TD ratio and rangeability, which is discussed later. Generally, flowrate in low level (as shown in Figure 2) is considered to be the minimum level of flow at which the process goals can still be reached.
However, there is another interpretation of TD ratio that is often used by operations staff. During operation, people expect the TD ratio to answer the question in this scenario: “My plant is running normally and all parameters are normal. However, occasionally, because of different reasons (including shortage of feed, reduced plant or unit capacity), the flowrate falls. What is the minimum value I can withstand without compromising the quality of the product?”
They basically interpret the TD ratio so that the numerator is the “normal level parameter” (and not the “high level parameter”). However, the difference in the interpretation does not generate a big difference in numerical value of TD ratio, as the normal and high level of parameters are often not very far from each other. Due to this potential confusion, the TD ratio should be considered an approximate parameter and not a precise number. In general, the academic definition of TD ratio generally uses a high-to-low values set up, while in the field, operators often define TD ratio using normal-to-low values.
The TD ratio can be defined for parameters other than flowrate, but it generally refers to flowrate. One reason for this is because flowrate can be the most important parameter of a plant, helping to define the economy of the system. The other reason is because the flowrate might be influenced by constraints outside of the plant (for instance, a lack of stored feed), which the control system cannot necessarily adjust (thus making a reduction in flowrate unavoidable).
While the TD ratio is not always a requested parameter, and is often not mentioned in project documents for design purposes, operators are usually looking for a TD ratio of least 2:1 for a plant. The required TD ratio could be as high as 3:1 or 4:1 for a plant.
Equipment flexibility
The TD ratio can also be determined for a given piece of equipment, using other values that are stated for the component. For example, even when a TD ratio is not explicitly stated for a centrifugal pump, when the pump is said to have a capacity of 100 m 3/h and a minimum flow of 30 m 3/h, this means that the centrifugal pump has a TD ratio of 3:1.
The TD ratio of a reciprocating pump could theoretically be defined as infinite because it can work over a very wide range of flows. However, in practice, such a pump cannot handle any flowrate that fails to fill the cylinder of the pump in one stroke. Partial filling of the cylinder may cause some damage to mechanical components of the pump over the long term. Thus the minimum required flow is a function of cylinder volume and stroke speed of a specific pump.
The TD ratio for pipelines presents a more complicated situation. With piping systems, there are several different ways to define the minimum flow. For instance, it could be defined as the minimum flow that does not fall into the laminar flow regime. Or, it could be considered as the minimum flow that keeps a check valve open (if a check valve is used).
For liquid flows in pipes, the minimum flow is more commonly interpreted as the minimum flow that makes the pipe full, or the sealing flowrate (that is, no partial flow), or a flow threshold below which the fluid will freeze in an outdoor pipe. If the flow bears suspended solids, the minimum flowrate could be defined as that at which sedimentation of suspended solids may occur.
Table 1 provides examples of typical values and rules of thumb regarding the TD ratio for various types of process equipment. Note that in Table 1, the TD ratio of storage containers is relatively large. This high TD helps to explain why large containers are used for surge dampening as part of a typical plant-wide control system.
In some cases deciding on a required TD ratio needs good judgment. One example is chemical-injection packages. The TD ratio is important for chemical-injection packages to protect against chemical overdosing or underdosing.
Chemical-injection packages typically provide a TD ratio of about 100:1 or lower. In some cases, 10:1 can be provided by stroke adjustment, and another 10:1 through the use of a variable frequency drive (VFD) to control the motor. But the question that arises is why such a large TD ratio is necessary if the host flow experiences, for example, only a 2:1 TD ratio. This high TD ratio is generally desired because of uncertainty in the required chemical dosage and the variety of available chemicals. The required dosage of a chemical depends on the type of chemical and the host stream properties.
Thus, during the design phase of a project, the designer doesn’t exactly know what the optimum dosage would be, even though a chemical provider recommends a specific dosage. Often, he or she prefers to conservatively have a chemical-injection system with a high TD ratio.
There is generally less uncertainty when using chemicals of known composition, rather than proprietary mixtures. If the dosage is fairly firm and the chemical used is a non-proprietary type, the TD ratio could be decreased, to reduce the overall cost of the chemical-injection system.
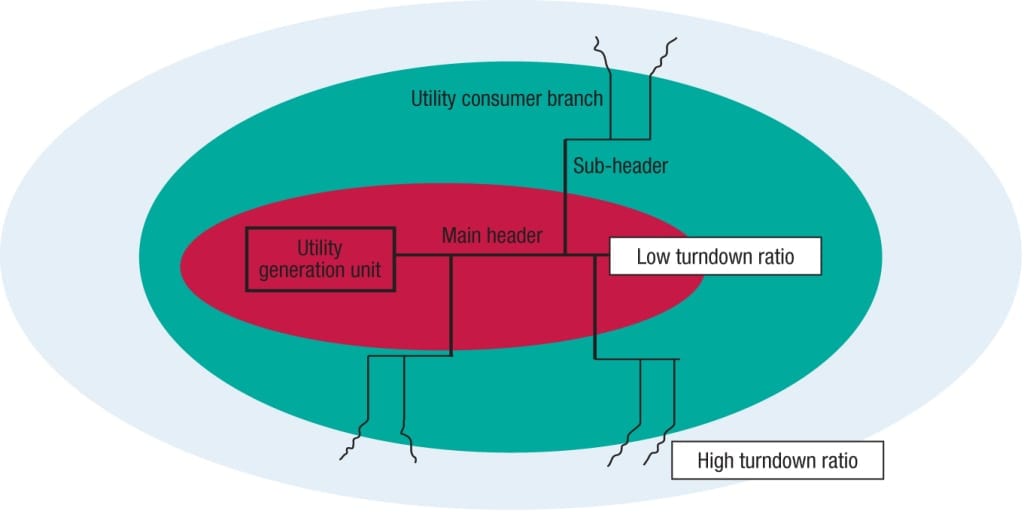
Figure 3. Shown here is a map of turndown ratio for a typical utility network.The pipes closer to the utility generation system (main header) need less turndown ratio compared to sub-headers and branches
Utility network flexibility
The flexibility of a utility network is also defined by the TD ratio. As mentioned above, when a plant requires a TD ratio of, say, 2:1, the TD ratio of the utility network should be higher.
To accommodate a larger TD ratio, the utility network generally requires containers to absorb fluctuations that may be caused by utility usage changes in process areas. Table 2 provides additional details to support this concept.
Different segments of a utility network experience different levels of turndown, and consequently each segment may need a different TD ratio. For instance, as shown in Figure 3, the main header could need the minimum TD ratio, while sub-headers may need a higher TD ratio.
The good news is that achieving a high TD ratio for the utility network and related instruments is not difficult. The overall utility network is mainly a series of pipe circuits that inherently show a large TD ratio. If instruments are included in the utility network, this poses no problem.Many instruments (including control valves and sensors) have an intrinsically large TD ratio — generally greater than 20:1.
Instrument rangeability
Instruments typically need to operate over a wider range of process conditions than other equipment or utilities. This is because their duty is not limited to normal operation, or a band defined by low and high values. Rather, they have to be operational across the entire, wider band from low-low to high-high threshold values. Therefore, rangeability, R, can be defined as:
Where:
Q High-high = the flowrate of the instrument or control valve at the high-high level threshold value
Q Low-low = the flowrate at the low-low level threshold value
For control valves, the formula is a bit different because a control valve is a device that passes flow and also drops the pressure of the flow. Thus, the rangeability cannot be defined only as a function of flowrate — pressure drop also needs to be incorporated. The rangeability of control valves is a function of the control-valve flow coefficient ( C v).
Rangeability can also be defined for other parameters, such as temperature, but generally defining rangeability with regard to flowrate is the most important parameter. Table 3 shows some typical rangeability values for commonly used instruments.
It should be stressed that TD ratio and rangeability are two separate parameters, for two separate systems. They cannot be used interchangeably and attempts to relate or convert them to each other do not have much meaning.
Providing required flexibility
There are three main ways that one can provide a specific TD ratio for process equipment, and each is discussed below:
- Using equipment with an inherently high TD ratio
- Replacing equipment with multiple similar, smaller-capacity equipment in a parallel arrangement
- Providing a recirculation route
Using equipment with an inherently higher TD ratio. Some process elements have an inherently higher TD ratio. Two of them, tanks and pipes, were mentioned above.
It is not always easy to recognize if a piece of equipment has an inherently high or low TD ratio. However, the following rules of thumb can be used as guidelines:
- Smaller-volume equipment tends to have a smaller TD ratio than larger-volume equipment
- Equipment with internal baffles tends to have a lower TD ratio (a good example is some gravity separators, such as baffled skim tanks)
- Equipment in gas service may show a higher TD ratio than equipment used in liquid service
- Equipment with an internal weir (especially fixed ones) may have a very low TD ratio
- Equipment that uses some properties of the inlet stream for their functioning, may have a lower TD ratio. For example, in cyclones or hydrocyclones, the energy of the inlet stream (“energy” as a property of the inlet stream) is used to generate centrifugal force, so any reduced flow will reduce the centrifugal force, which may reduce the effectiveness of the system
- Equipment containing loose, porous media may show a lower TD ratio in liquid service, and the TD ratio may be lower when the porous media is comprised of larger solid particle sizes. Examples include sand filtration systems, catalyst contactors and related systems
- Despite a common misconception, perforated-pipe flow distributors do not necessarily have limited TD ratios [ 3 ]
As noted, the utility network should have a relatively large TD ratio. Fortunately, utility networks consist mainly of pipes in different sizes, which have inherently large TD ratios. If control valves are needed on the network, their lower TD ratios may generate bottlenecks. In such situations, it may be necessary to install parallel control valves with split control, because of the required large TD ratio.
Using parallel equipment.Instead of using a component with a capacity of 100 m 3/h, this technique is essential to use an arrangement that employs two parallel components, each with the capacity of 50 m 3/h. By doing so, a TD ratio of at least 2:1 can often be provided. It should be noted that the equipment by itself may have some inherent TD-ratio capability, which may have to be added to the provided 2:1 TD ratio.
For example, instead of using one shell-and-tube heat exchanger with the capacity of 100 m 3/h, three heat exchangers — each with the capacity of 33 m 3/h —can be used to achieve a TD ratio of at least 3:1. The TD ratio may actually be higher because each shell-and-tube heat exchanger has an inherent TD ratio too, even though it is very small. This technique has additional benefits. The parallel arrangement provides higher availability for the system, because the failure of two or three parallel equipment components is less likely than the potential for failure when the system relies on a single equipment component.
Using two control valves in parallel in a single control loop (through a “split range” control) is also another example of this technique in the area of instrumentation.
However, there are some disadvantages associated with this technique. In particular, capital cost and operating cost considerations may rule against it.
Providing recirculation pipe. Implementing a recirculation pipe from the equipment outlet to its inlet is a widely used method to increase the TD ratio of the system. In many cases, a pump and definitely a control system, are needed to implement this technique. As long as you can afford an extra pump and control system on the recirculation pipe, this technique can be used. The recirculation pipe needs a control system, otherwise all flow goes through the recirculation pipe back to the inlet of the unit of interest (Figure 4).
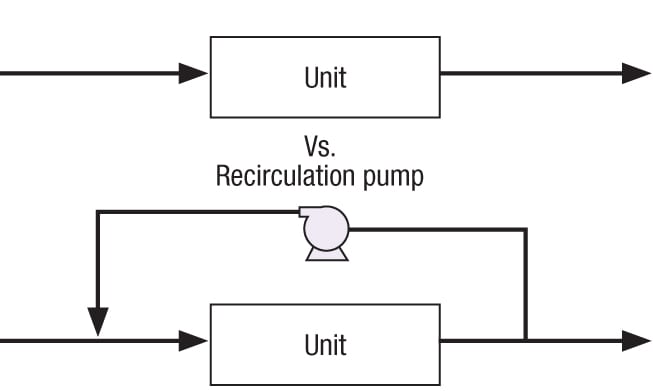
Figure 4. By providing a recirculation pipe, the turndown ratio of a piece of equipment can be increased. If the fluid pressure is not enough, a pump (or compressor) may be needed, and a control system is definitely needed
One example of this technique is using a minimum-flow line for a centrifugal pump. A centrifugal pump with a capacity of 100 m 3/h and a minimum-flow line of 30 m 3/h (thus, with a TD ratio of 1:3) can be equipped with a minimum-flow line with an appropriate control system to increase its TD ratio. If the minimum-flow line and the control system are designed to handle a maximum flowrate of 30 m 3/h, it means the TD ratio of the pump can theoretically be increased to infinite, by zeroing the minimum flow.
Another example is a vertical falling-film evaporator. This type of evaporator has a vertical tube bundle that is similar to the ones found in a shell-and-tube heat exchanger. The tube-side flow is two-phase flow. The liquid flows down by gravity, and the vapor (of the same liquid) is pushed down by liquid drag. The flow inside the tubes is an “annular regime,” meaning the liquid covers the internal perimeter of tubes and the vapor is in the center of the tubes.
In the case of low flow, there is a chance of “dry patches” forming on the tube’s internal surface. Because of this, vertical, falling-film evaporators are typically equipped with recirculation pipes to provide a minimum practical TD ratio (Figure 5).
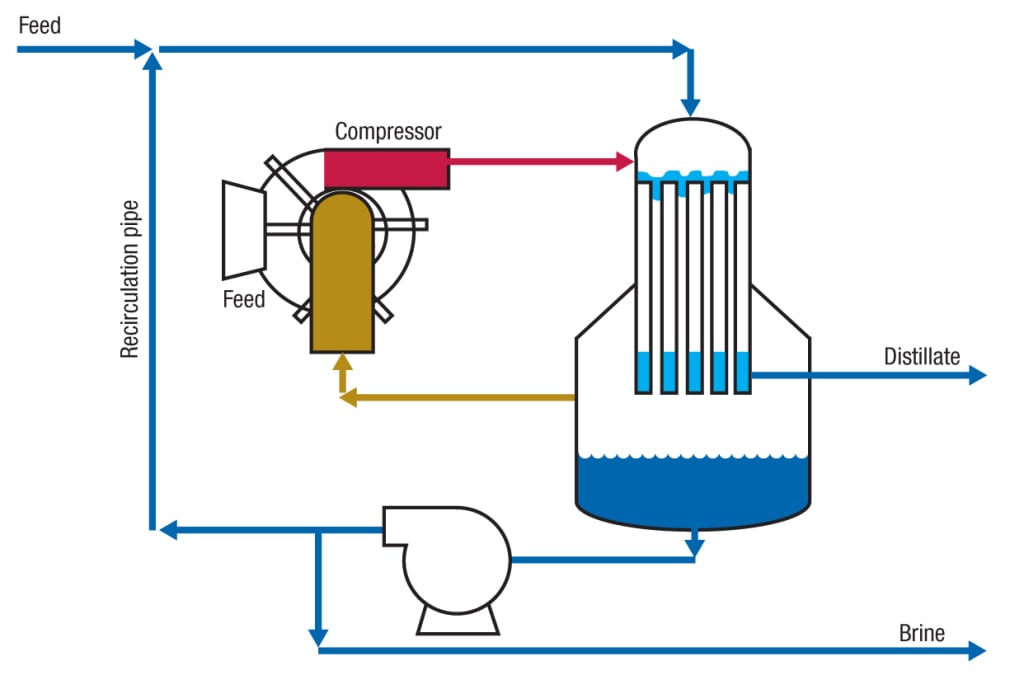
Figure 5. Shown here is a system for brine recirculation in a vertical falling-film evaporator. The brine-recirculation line in the vaporizer plays an important control role. Without the recirculation line, the
vaporizer has a very narrow turndown ratio, which is not generally acceptable for optimal operation
However, this method cannot be applied for all equipment. For example it is not a good technique to increase the TD ratio of a furnace or fired heater, because recirculation of fluid around a furnace may increase the furnace coil temperature and cause burning out if the firing system doesn’t have sufficient TD ratio. Table 4 provides some rules of thumb to gauge the flexibiliy of different elements of a process plant.
Resistance against surge
While TD ratio refers to the static behavior of a plant, there are two additional parameters (resistance against surge, and speed of recovery from upset) that refer to its dynamic behavior. However, there is less emphasis on dynamic theories, and only practical aspects of dynamic behavior.
A process upset could result from a surge. Surge can arbitrarily be defined as the deviation of a parameter (such as flowrate) beyond its normal level. The final value of the parameter may or may not be in a band between high level and low level and the change often occurs quickly. When a parameter moves quickly, an upset could happen. The surge/upset could be defined for each parameter including flowrate, temperature, pressure and even composition. A surge in the composition is often called a slug. Level surge is generally a consequence of other surges and it can be dampened in surge-equalization tanks or drums.
Surge can also be defined by its shape (in a diagram of parameter change versus time), and by its magnitude. The magnitude of surge can be stated as a relative number or an absolute number. For example, a flow surge of 2% per minute is a relative number and means if a surge occurs in every minute, the flowrate is increased or decreased by 2%. In another example, a system can be said to be resistant to temperature surge (thus no upset conditions will be generated) as long as any potential surge remains less than 2°C per minute (an absolute value).
A 2%-per-minute surge means that the flowrate could start at 100 m 3/h and then increase to 102 m 3/h, then to 104 m 3/h and so on. Or the surge may start at 100 m 3/h and then decrease to 98 m 3/h, then 96 m 3/h and so on.
Some systems show different behavior against surge, when it is a positive surge (an increase in the parameter value), or a negative surge (a decrease in the parameter value). Therefore, it is good idea to clarify it. For example, an API separator could be more resistant to the impact of decreasing inlet stream compared to the impact of increasing the inlet stream.
The first line of defense against a surge is provided by the control system or control valves. However, control valves alone cannot totally eliminate a surge, but will only stop a surge from impacting a downstream system. Ultimately, the surge needs to be handled, but by other methods.
There are basically two surge-management methods that can be implemented for each piece of equipment or group of equipment in a plant:
- Boxing-in a surge in a specific equipment component or series of equipmen
- Transferring the surge to an external or auxiliary system
Understanding the applicability of each of these techniques requires some knowledge about the inherent dynamic characteristics of the systems from a process control viewpoint. The three dynamic features of each equipment or unit are resistance, capacitance and inertia (dead time) [ 4 ]. A brief qualitative explanation of these three features is presented next.
If a system is more dominantly a “resistance” type, this system will be able to prevent the surge from transferring to downstream equipment. A piece of pipe is one example of a resistance-type element. A pipe could inherently stop the surge if it is narrow enough. However, because a pipe’s main function is to transfer fluid, the designer generally sizes the pipe based on its duty (transferring fluid) and then, if needed, a control valve is placed on the pipe to stop a potential surge.
The capability of a system to dampen the surge depends on the “capacitance characteristics” of the system. The higher the capacitance characteristic, the more it is able to dampen a surge.
Here, a capacitance-type element refers to whatever element that can be used to temporarily store excess mass (such as liquid volume or gas pressure) or energy (such as thermal or chemical energy).
For instance, large-volume equipment generally have a higher capacitance feature. Implementing a surge tank, equalization tank, surge drum (or even pond) is one means of providing a system with sufficient capacity to dampen the surge.
Another example of using a high-capacitance system is when transferring a surge to heat-exchange media. Utility heat exchangers use streams such as cooling water, steam, and other media, to transfer the heat to or from process streams. These utility streams are also able to absorb a temperature surge in the system. The capacitance feature of a utility network can be provided in part by pipes in the network (the pipes function mainly as resistance elements but they have some capacitance too), and also their surge tank, as discussed above.
A system is called robust against upset when it can tolerate a large surge (as defined for each process parameter) and no upset occurs, thereby allowing the process to proceed smoothly.
If an upset cannot be tolerated, one solution is to implement a rate-of-change control loop in the system. The following llist provides some general rules of thumb on the capability of a system to handle surges:
- Generally speaking, equipment with larger volume and fewer internals is better able to dampen upsets.
- Containers with plug-flow regime are more susceptible to upset from surge compared to mixed-flow-regime containers.
- The equipment that exerts centrifugal effect on the process fluid is more sensitive toward the upset (Examples include centrifuges and centrifugal pumps).
- Containers that hold loose media are less robust against upsets.
- Non-flooded containers can handle and dampen a surge better than flooded containers.
Speed of recovery from upset
The speed of recovery from an upset situation primarily depends on the dynamic characteristics of the system, and more specifically, the “process dead time” and “process time constant” of a system. The dead time is a result of inertia characteristics of the system, while the process time constant is a function of capacitance and resistance features of the system. A larger dead time or time constant means the system requires a longer time to recover from an upset.
However, in addition to this inherent characteristic of a system, other features can also impact (and decrease) the speed of recovery from an upset. Sometimes these features (rather than the dynamic behavior of the system) govern the behavior of the system. For example, a hot lime softener within a water-treatment system has an established sludge blanket. It takes time to “heal” a broken sludge blanket if an upset creates “breaks” in it.
Another example is “vessel- media” systems. These are systems that are used in operations such as ion exchangers, loose-media filtration systems, packing-type absorption towers, catalyst beds and so on. A big surge in flow may displace the media in a way that leads to flow channeling. Putting the displaced media back into a homogenous form takes time.
Similarly, a surge to a biological system will generally require a long recovery system, because a surge in temperature or slug of a toxic chemical may kill a large portion of the biomaterial growing there. n
Edited by Suzanne Shelley
References
1. Mullinger, P., and Jenkins, B., “Industrial and Process Furnaces,” 1st Ed., Amsterdam: Butterworth-Heinemann, 2008, p. 171.
2. Upp, E., and LaNasa, P., Fluid flow measurement,” 2nd Ed., Gulf Professional Publishing, Boston, 2002, pp. 157–158.
3. Perry, R., Green, D. and Maloney, J., “Perry’s Chemical Engineers’ Handbook,” 7th Ed., McGraw-Hill, New York, 1997, pp. 6–32.
4. Liptak, B., “Instrument Engineers Handbook — Vol 2. Process Measurements and Analysis,” 4th Ed., CRC Press, Boca Raton, 2003. Chapter 2.
Author
Mohammad Toghraei, is an instructor and consultant with Engrowth Training (Email: [email protected]; Phone: 403-808-8264; Website: engedu.ca), based in Calgary, Alberta, Canada. He has more than 20 years of experience in the chemical process industries. Toghraei has published articles on different aspects of chemical process operations. His main expertise is in the treatment of produced water and wastewater from petroleum industries. He holds a B.S.Ch.E. in from Isfahan University of Technology (Iran), and an M.Sc. in environmental engineering from Tehran University (Iran). He is a professional engineer (PEng) in the province of Alberta, Canada.