Greener chemistries and equipment advances provide more sustainable water-treatment options for chemical processors
Chemical processors face tough challenges when it comes to the water used in the facility — namely, water scarcity and ever-increasing regulatory requirements associated with discharging effluent. At the same time, there is a move toward sustainability and “greener” approaches to all aspects of chemical processing, including water treatment. As these two forces collide, there is a growing trend toward water reuse and more environmentally friendly approaches to water treatment, which has resulted in not only new technologies and greener chemistries, but also novel combinations of these technologies, allowing processors to reuse water and treat both recycled and discharged water in a way that is easier on the environment.
“Earth has naturally recycled water for millions of years; however, pressure from scarcity, increased demand and the rising cost of treated water have influenced industries to review their method of consumption of water and treatment methods,” says David Gilbert, director of engineering, with EMO3 (Quebec City, Canada; www.emo3.com). “In addition, pressure from federal and state regulators has motivated action to find enhanced methods that address effluent discharge water.”
He continues: “Some of the primary goals of water reuse are to limit the use of available groundwater and aquifer for industrial processes, to decrease discharges to sensitive water ecosystems and increase groundwater recharge. The greatest challenge facing chemical processors is the huge cost of off-site disposal. This burden can cost up to $6 per gallon, depending on the contaminant and local discharge regulations, and the costs are increasing due to more stringent regulations. Hence, the interest and increasing adoption of onsite treatment systems.”
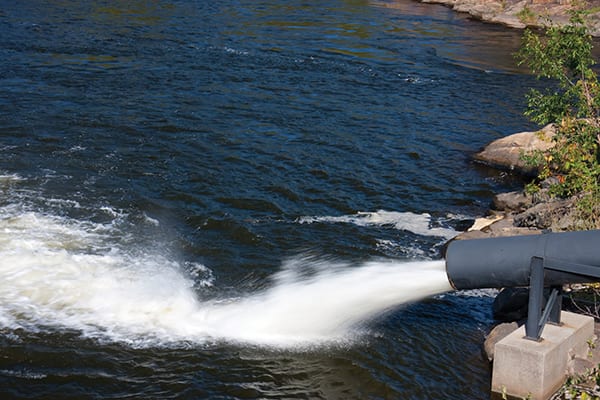
Figure 1. While water reuse is not a new practice, it is rapidly accelerating due to water scarcity issues, as well as the increasing costs of obtaining water for use in processes and treating water for discharge
Water reuse
While water reuse is not a new practice, it is rapidly accelerating due to water scarcity issues, as well as the increasing costs of obtaining water for use in processes and treating water for discharge (Figure1). In addition, many companies are self-imposing sustainability practices involving water, says Kevin Milici, vice president of marketing and technology, with U.S. Water (St. Michael, Minn.; www.uswaterservices.com). “As a result, they see water reuse as an opportunity to help curtail the consumption of fresh water in a significant way and it is driving the practice.”
Meeting the demands of minimal liquid discharge (MLD) and zero liquid discharge (ZLD) is another driving force behind reuse options. “Chemical and petrochemical facilities with large wastewater streams are increasingly looking to reduce or reuse liquid discharge. Though there has been significant progress, completely eliminating the gap between MLD and ZLD can be prohibitively expensive in terms of capital and operating costs,” says Alexander Lane, commercial director, DuPont Water Solutions EMEA (Luzern, Switzerland; www.dupontwatersolutions.com). “At a 95% water recovery rate, a MLD approach can be operated at a fraction of the cost compared to a 100% ZLD system. By using cost-effective membranes, chemical processors can reduce the volume of water that needs additional dewatering via expensive thermal ZLD methods.”
He continues: “Advancing a circular economy — in which raw materials are continually recycled and reused — is of increasing interest as brands seek to maximize the efficient use of water, close the resource loop and protect their license to operate. Sustainability is no longer a separate activity — it is inherent in the business plan.”
Milici says recycled water is not just used for irrigation or flushing toilets in the facility (although it does have application here), but also for tasks directly related to operation. “We are seeing trends towards replacing fresh water with recycled water in ancillary systems like emission control to scrub waste gases and in applications such as steam generation and cooling water,” he says.
Milici provides examples of how these applications might look in the facility. A plant may be using reverse osmosis (RO), a membrane-based technology, to produce high-purity water for the generation of steam (Figure 2). Raw water comes into the RO system, which produces clean process water. The reject, or brine, from that system would typically go to waste treatment. However, processors can now take that brine and, with adequate treatment chemistries, use it to become make-up or partial make-up water for applications such as cooling towers. “So now instead of using fresh water for the RO unit and the cooling tower, they are taking the waste stream from the RO unit and it becomes the primary source of, and replaces, fresh water for the cooling tower.”
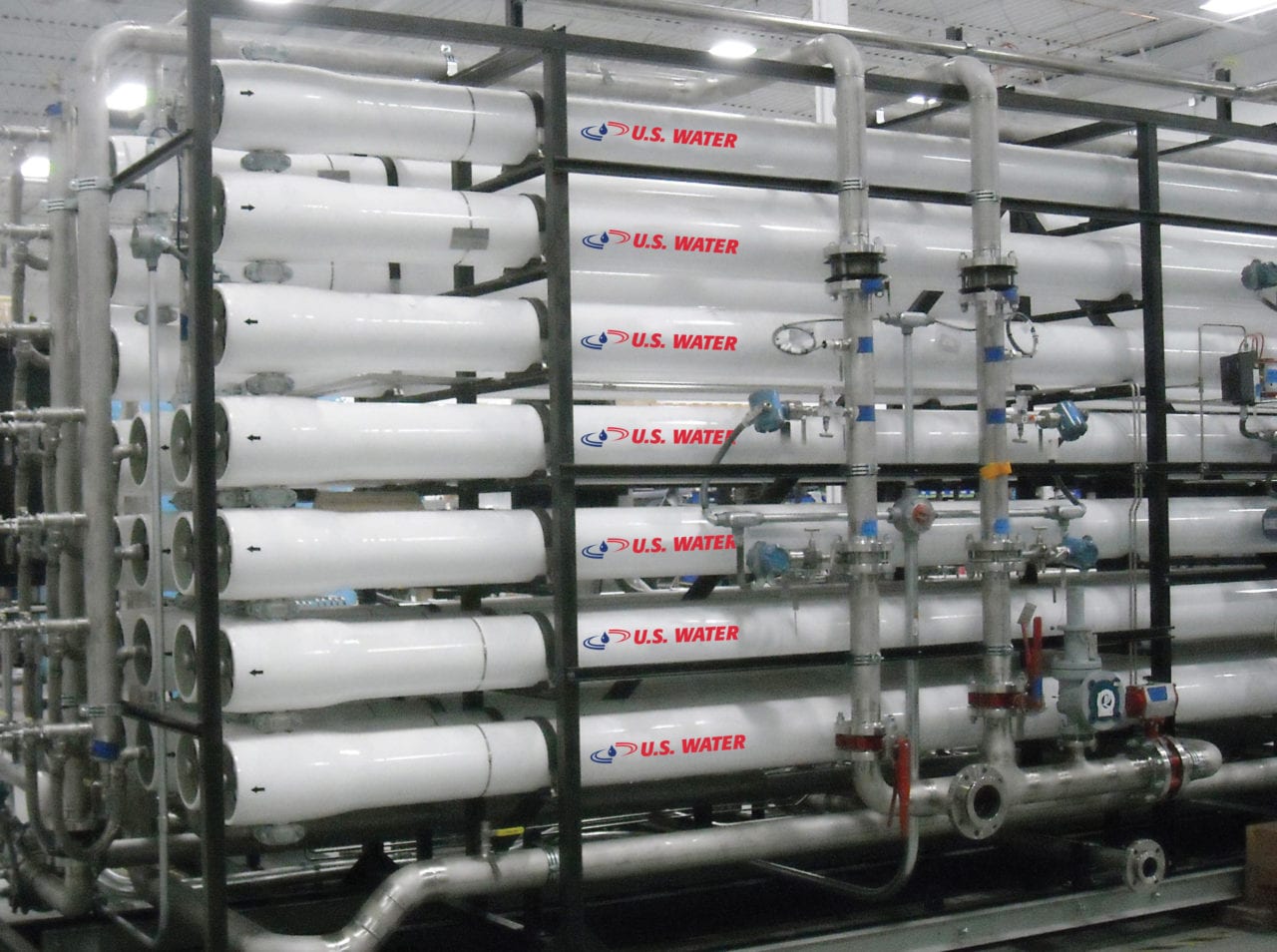
Figure 2. A plant may be using reverse osmosis (RO), a membrane-based technology as shown here, to produce high-purity water for the generation of steam
Another application might be cooling tower blowdown recovery. You may have a cooling system with make-up water coming into it and bleeding off a continuous stream of water under controlled conditions. Again, instead of taking effluent from the cooling system and sending it to waste treatment, it can be reused right on the spot. “Different forms of filtration and membrane-based technologies can treat the wastewater from the cooling tower and bring it to the front end to use as a source of make-up [water] in lieu of brand new, fresh water.”
In addition to the straight-up benefits of water reuse, this type of circular economy, according to Lane, considers “fit-for-purpose” water quality requirements versus strictly environmental discharge requirements. “The ‘fit-for-purpose’ water requirements are often more relaxed, meaning that water can be treated to the level needed for the intended purpose. For example, the concentrated reject stream from RO wastewater reuse systems can be a reliable water source for industrial plants and requires a varied level of treatment compared to water being reused for drinking. Additionally, when recycling and recovering pure water for circular water management, the trace contaminants in the water can be elevated, making them easier to capture and remove.”
Fortunately, Lane says, product and technology innovation has improved many of the factors that go into water treatment, such as cost, energy, chemical use and maintenance. “Traditional processes like RO, ion exchange and filtration are gaining traction as more cost effective, sustainable methods for companies to improve their water footprint — enabling recovery of up to 95% of liquid discharges.”
Improved technologies
Often, traditionally applied wastewater recovery methods are not equipped to handle the challenges presented when water contaminants, including suspended solids, hardness, dissolved organics and high-salt levels are concentrated to extreme levels, but advances in proven technologies such as RO, ultrafiltration, nanofiltration and ion exchange used in a way that is tailored to each unique wastewater treatment challenge are making it possible.
For example, existing technologies such as RO, ultrafiltration, nanofiltration and ion exchange, are now being used in new ways for MLD, says Lane. “DuPont Water Solutions’ Filmtec Fortilife RO Elements [Figure 3] help reduce costly concentrate waste, lower operating expenses and enable customers to move toward MLD,” he says.
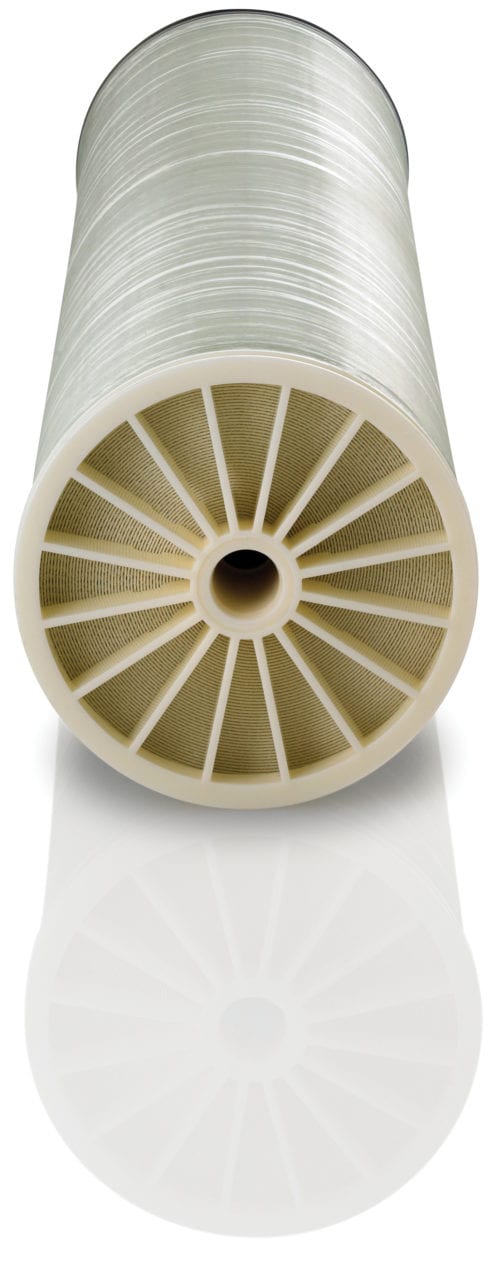
Figure 3. Filmtec Fortilife RO elements are designed to tackle bio-fouling, organic fouling and scaling and can recover water from brine with salt levels ranging from 0 to 80,000 mg/L
The company’s Amberlite IRC83 Weak Acid Cation resin can be used in combination with RO to help facilitate higher productivity and lower operational costs. Additionally, DuPont’s Tequatic Plus F-75 filters can be used as an alternative to bag filters. “We’ve seen the volume of recycled produced water reach levels close to 100% while reducing operating costs by about 60%,” says Lane.
Another area of interest is in the use of ozone treatments, says EMO3’s Gilbert. “Ozone technology is a mature one, but there has been an increasing interest in it following the detection of pharmaceutically active and endocrine-disrupting compounds (EDCs) in reclaimed water,” he says. “As a sustainable technology, O3 is produced onsite using compressed air or O2. O3 has the secondary benefits of not releasing toxic disinfection byproducts in the discharge.”
Advances in electronic technology have recently permitted modular, higher frequency/higher voltage O3 cells with a smaller footprint and lower cost to address a multitude of sustainable water oxidation/disinfection needs. “Our latest O3 technology platform, Taurus [Figure 4], is a modular, ruggedized unit for highly efficient O3 treatment processes. Every unit provides a constant concentration of 50 g/h of O3,” he says.
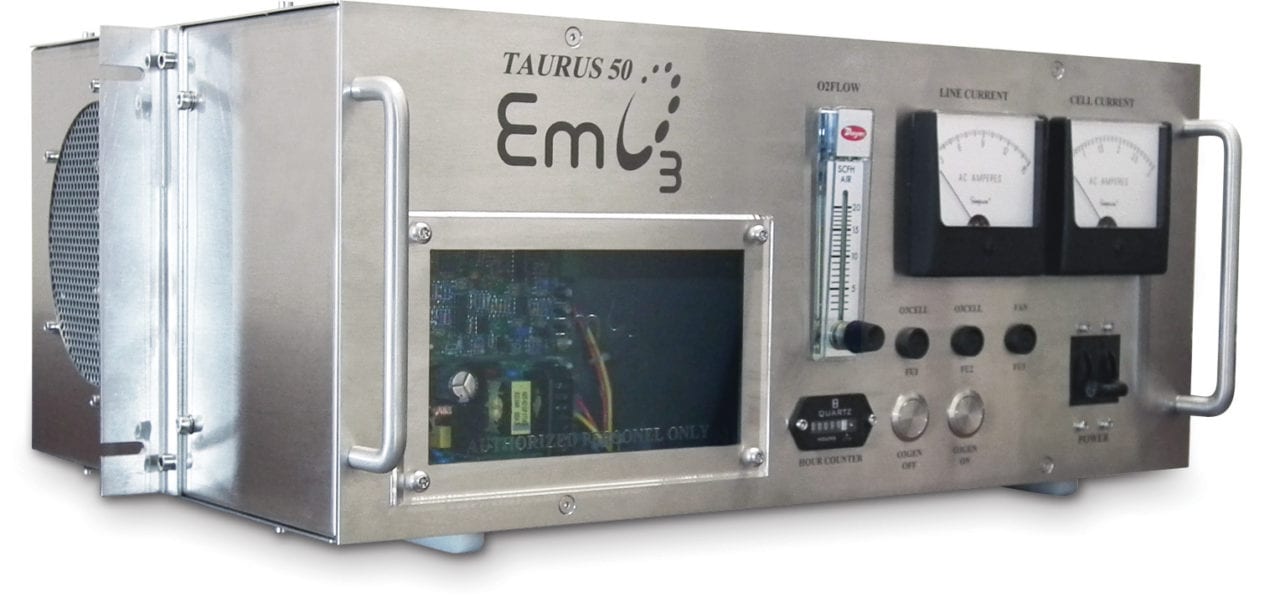
Figure 4. Taurus is a modular, ruggedized unit for highly efficient ozone treatment processes
For applications that require removal of dissolved salts, a tunable water-deionization technology, known as capacitive deionization, or Cap DI, is making waves. “We’re finding that it is favorable to use electrostatic attraction to remove dissolved salts from water,” says L. Bryan Brister, CEO of Voltea (Farmers Brand, Texas; www.voltea.com). “The reason is that once salt dissolves into water, it dissolves into a molecule that carries a positive charge and, separately, a molecule that carries a negative charge, so the idea with electrification is very simple. Using direct current you can have a positively charged electrode surface and opposite that, a negatively charged electrode surface through which the water flows freely and the natural phenomenon of oppositely charged species attracting each other creates a scenario where positively charged salt is attracted to the negatively charged electrode and the negative salt is attracted to the positively charge electrode.
He continues: “Over the last few years, Cap DI has become more practically possible. The reason is that while the material science that allows it to work had been very expensive, it has recently gotten to the point where the components are reliable, robust and inexpensive enough to make sense in the real world.”
While Cap DI has many applications, in industry it is often used in wastewater reuse applications where it is installed after membrane bioreactor (MBR) and sequencing batch reactor (SBR) systems to enable customers to re-use the effluent for a variety of applications, such as cooling towers, boiler feed and irrigation. For these applications, Cap DI recovers up to 95% of the effluent with minimal chemical and power usage.
In cooling-tower applications, the water contains natural salts, such as calcium, bicarbonate, chloride and sulfate. The salts do not evaporate, so they build up over time, causing corrosion and scaling. To prevent this, chemicals are the traditional solution. However, CapDI can be used to treat the water before it enters the cooling tower, reducing salts from the incoming water stream by 80%. The cooling tower does not need to be adapted since CapDI is placed before it, treating only the incoming water, therefore the composition of the recirculating water remains unchanged. This increases the cycles of concentration significantly, resulting in lower overall water consumption and wastewater production.
Greener chemistries
“Industry is trying to be more efficient and prudent in the use of chemistries in water treatment and, as result, they are selecting chemistries that meet environmental requirements and that means moving in a greener direction over time,” says U.S. Water’s Milici.
One such product comes from Bionetix International (Quebec, Canada; www.bionetix-international.com), which offers natural wastewater solutions in the form of specially targeted microorganisms and nutrients that degrade waste with greater efficiency. Bionetix offers products that target waste compounds such as grease, starch, petroleum hydrocarbons, cellulose, manure and ammonia (Figure 5). While these are often used at the wastewater-treatment facility, they can be used by chemical processors and other industries, as well.
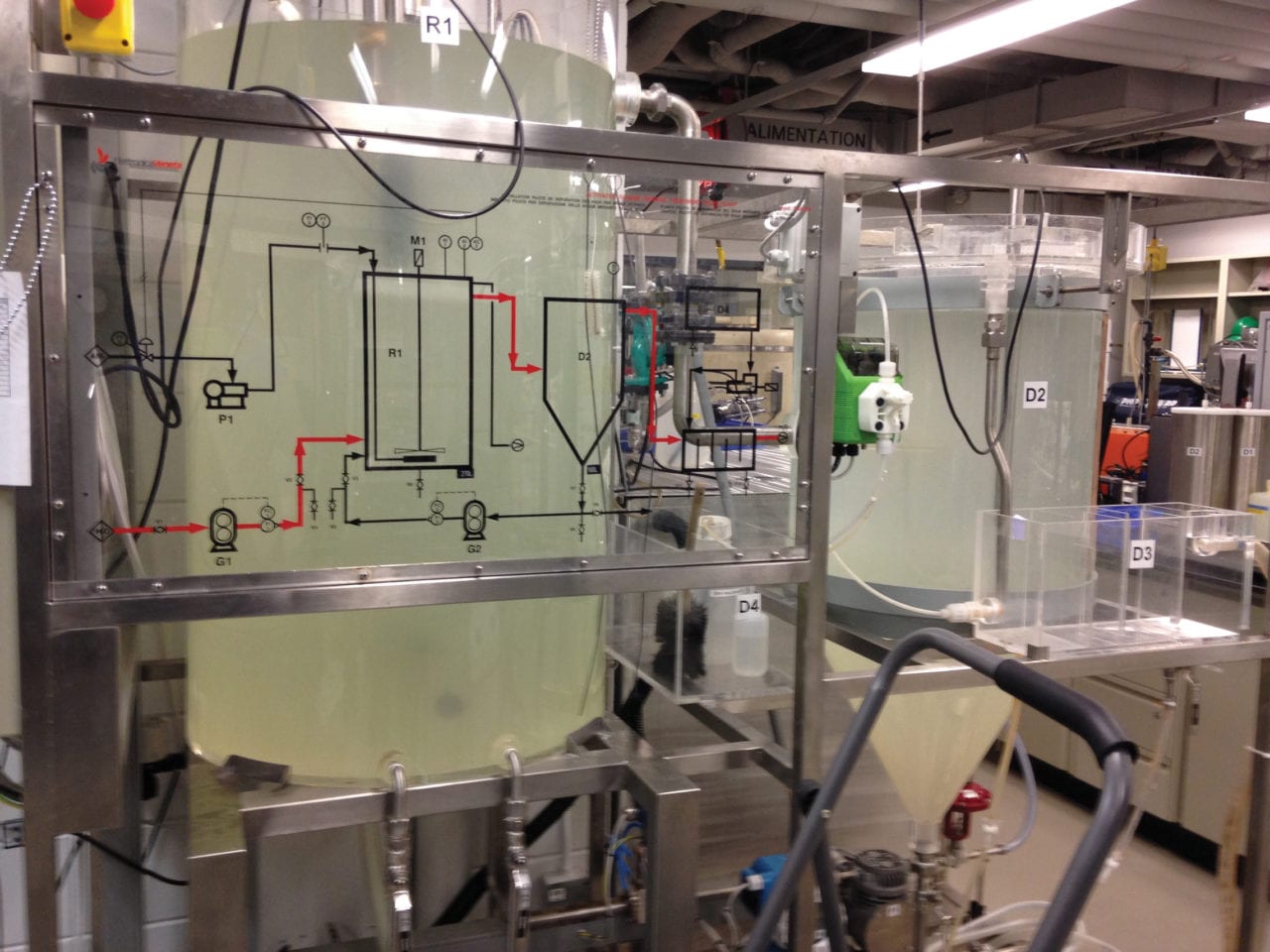
Figure 5. Bionetix natural wastewater solutions are specially targeted microorganisms and nutrients that degrade waste compounds such as grease, starch, petroleum hydrocarbons, cellulose, manure and ammonia
According to Julie Holmquist, marketing content writer for Cortec Corp. (St. Paul, Minn.; www.corteccvi.com), the parent company of Bionetix, “A lot of wastewater treatment plants have limits on the level of BODs and CODs [biochemical oxygen demand and chemical oxygen demand] they will allow a chemical plant to release with their waste. If the facility has a BOD or COD measurement that is above this level, they can face fines due to the extra load of contaminants. But, if the chemical processor applies our products to their wastewater, they can cut down on the BOD and COD levels before they release them to the wastewater facility.”
While using natural mechanisms for wastewater treatment is not uncommon, the microorganisms in Bionetix “have a certain appetite for different types of contaminants and are better at creating a certain type of enzyme,” she says. “For example, if there’s a starch factory, they would be creating a waste stream with extra starch in it, so the targeted organisms used in that application would produce the type of enzyme that breaks down starch. Bionetix takes microorganisms that are very good at degrading a certain type of contaminant and they target those based on what kind of waste the facility is producing.”
One of the common regulatory issues from a discharge point of view is the use of phosphates in water-treatment applications, such as cooling towers. “Phosphates have been used for control of corrosion or formation of mineral scales and deposits in heat-transfer surfaces. But the problem with phosphates is that they eventually end up in a receiving body of water and those contaminants create problems in the environment,” says U.S. Water’s Milici. “So there has been a development of technologies that provide the same degree of corrosion protection as traditional phosphates but without the use of phosphates in the formulation. These ‘Non-P’ cooling-water treatments represent a very serious and significant advance in technology on the chemistry side of water treatment.”
Peter Macios, executive product manager with SUEZ Water Technologies & Solutions (Trevose, Pa.; www.suezwatertechnologies.com) agrees: “Users of these chemistries are moving toward greener products that provide more of a filming protection around their assets and provide better protection without creating a foulant,” he says. “Our latest offering is a program called E.C.O. Film, or Engineered Carboxylate Oxide, which is a technology that is designed to provide complete scale and corrosion protection in open cooling-water systems without the use any phosphorus or EPA [U.S. Environmental Protection Agency] priority pollutant materials. Our technology allows customers to go phosphorus-free and get the same performance and same corrosion protection at essentially the same cost to treat.”
Combined approach
Often, chemistries such as E.C.O. Film fit into a combined approach to water treatment. “If we think about a petrochemical plant, we are looking at how we allow them to use alternate water sources and typically the first stages of that is an equipment offering like membrane or ultrafiltration technology,” he says. “And, if there’s still contamination in that water, how do we use that water in the cooling water system without fouling? That’s where greener chemistries and new filming technologies come into play,” (Figure 6).
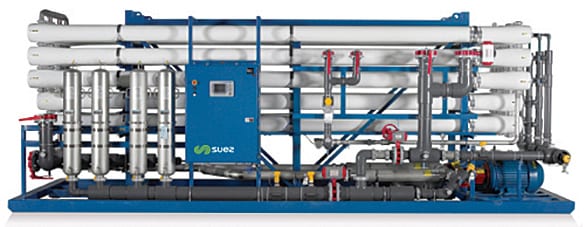
Figure 6. PRO Series Reverse Osmosis systems are well suited for a variety of applications and may be part of a treatment program that also includes greener chemistries
Milici from U.S. Water agrees: “Water treatment today is trending toward looking at each situation and providing a combination of chemistry, engineering, equipment and services that result in the optimal, best solution for a given application, and the solution is usually unique from plant to plant.”
He continues: “What’s really evolving, more than just the equipment or just the chemistry, is the combination of those technologies and how the different components are put together to solve particular problems with the smallest footprint and lowest capital costs possible.”