New pump technologies offer better containment and reliability to keep product flowing safely and efficiently
Because moving hazardous or high-value product through the process in a cost-effective manner is the name of the game in today’s chemical process industries (CPI), ensuring containment, reliability and efficiency is crucial when pumping materials in challenging chemical applications. To help processes run optimally, pump manufacturers aim to provide pumps that offer leak-free, reliable operation.
“Reliability is the number one thing processors are looking for,” says John Hall, strategic market manager with Viking Pump, Inc. (Cedar Falls, Iowa; www.vikingpump.com). “Unplanned shutdowns for pump maintenance are unacceptable, so we’re continually working to build greater reliability into our pumps, with higher strength or harder materials, longer-life bushings and bearings and better shaft sealing systems,” Hall says.
Ensuring containment
Because chemical and emissions containment are key to running a profitable operation and ensuring compliance with environmental and safety regulations, pump manufacturers strive to offer a variety of solutions that make pump leakage a non-issue.
“Shaft sealing is always an issue,” says Hall. “Simple sealing techniques like packing require some leakage. Mechanical seals prevent leakage, but may require external support systems that add complexity. Sealless magnetic drives prevent leakage and don’t need external support systems, but are expensive. So it comes down to what system best supports the processor’s needs in terms of emissions, their operations personnel and the liquids being handled.”
Because containment is not a one-size-fits-all issue, pump manufacturers continue to improve sealing and sealless technologies that address leakage. For example, Viking’s Universal Series of internal gear pumps, which are the company’s main chemical-pump product line, offer a variety of sealing options, including a double-O-ring seal, component seals, cartridge seals and sealless magnetic (mag) drives. The sealless mag-drive option eliminates the shaft seal to provide high levels of liquid and vapor containment, as all liquid and vapor are hermetically sealed in the pump. These pumps are designed especially for hazardous and difficult-to-seal liquids.
In addition, the company frequently develops special solutions for unique applications, and can then apply them to the broader chemical market, says Hall. “For instance, we developed a unique double-o-ring sealing system for pumping chocolate, and are now looking at chemical applications to eliminate leakage from pump packing glands.”
The sealing system features an O-Ring Seal Bushing with two sets of O-rings to seal food-grade grease (for handling chocolate) in the bushing area. This prevents migration of the pumped material along the shaft and keeps it in the pump. The bracket bushing is lubricated by clean grease for long life and requires no special clearances. O-ring seals are tolerant of abuse and require no periodic re-tensioning like packing does. They exhibit strong abrasion resistance and can handle most viscosities. And, unlike lip seals, which are designed for low pressures, O-rings can tolerate very high pressures.
Goulds Pumps (Seneca Falls, N.Y.; www.gouldspumps.com), too, is improving its seal technology to prevent leakage. “We found that 70% of pump downtime is tied to failure of the mechanical seal, which manifests itself as a leak, so we’ve had a significant focus on optimizing the seal chamber environment in the area where the mechanical seal sits,” says Stan Knecht, vice president and general manager of industrial products. One of the outcomes is the Taperbore Plus seal chamber, which addresses the most common reasons for seal failure — inadequate heat dissipation and poor lubrication. The Taperbore Plus technology allows the mechanical seal to run cooler with better face lubrication. It also keeps solids, air and vapors away from the seal faces, further extending seal life. It is an enlarged seal chamber, allowing increased radial clearance between the mechanical seal and the chamber, providing better liquid circulation and improving heat removal.
Sealless pumps are also being improved upon for better containment. “Since so many chemical-based raw materials and finished products, such as acids, caustics and solvents, can be dangerous to handle — or are produced in explosive atmospheres — it is imperative that pumps used in these processes are leak free and can offer full containment,” says Christophe Jovani, marketing communications manager with PSG, a Dover Company (Oakbrook Terrace, Ill.; www.psgdover.com). “The most effective way to achieve reliable product containment is through a sealless design. That’s why many of PSG’s product brands have developed sealless versions of their products, with safe and reliable use in demanding chemical processing applications the ultimate goal.”
Specifically, all models of Almatec and Wilden air-operated double-diaphragm (AODD) pumps and Abaque peristaltic pumps, due to their traditional design and method of operation, are sealless. Blackmer offers the SMVP Series pumps, which feature a magnetic coupling. “The stainless-steel SMVP Series Sliding Vane Pumps feature a sealless magnetic coupling that enables them to meet the need for zero leakage when handling expensive, hazardous and hard-to-seal fluids,” says Jovani. “The pumps use standard samarium-cobalt magnets that prevent magnet degradation if adverse operating conditions are encountered. Also, their self-lubricating, carbon-graphite sleeve bearings ensure no metal-to-metal contact and allow for limited dry-run operation.”
And, building off its sealless diaphragm Hydra-Cell pump technology, Wanner Engineering, Inc. (Minneapolis, Minn.; www.hydra-cell.com) extended the product line to include the Hydra-Cell T100 Series high-pressure pumps (Figure 1). “The T100 Series triplex pumps are packing-free and designed to replace horizontal centrifugal pumps and packed plunger pumps in oil and gas applications,” says Donelle Capriotti, business development director, with Wanner Engineering. Featuring a sealless, multiple-diaphragm design, the pumps eliminate hazardous volatile organic compound (VOC) emissions along with cleanup and disposal costs of packed-pump leakage. The design also eliminates the need for external lubrication and maintenance, as well as plunger wear problems associated with packing. “These are the first triplex diaphragm pumps able to run at the flow and pressure rates normally handled by packed plunger pumps in the petrochemical, oil and gas industries,” says Capriotti. “They rely on hydraulically balanced diaphragms to handle high pressures and are great in these applications because they keep pumped fluids from leaking. This is important because these industries are fined for emissions and typically have to build expensive secondary containment areas around other pumps. These pumps don’t require that.”
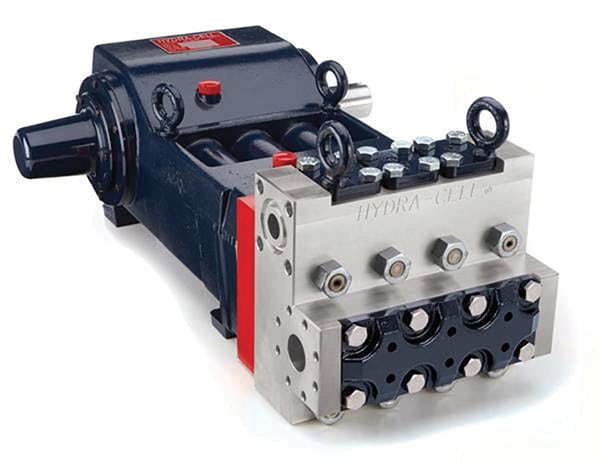
Figure 1. The Hydra-Cell T100 Series high-pressure triplex pumps are packing-free and designed to replace horizontal centrifugal pumps and packed plunger pumps in oil-and-gas applications
Wanner Engineering
Reducing cost of ownership
“Many productivity achievements are driven through the cost of total ownership, which can include improving efficiency of processes, but also reducing maintenance and operating costs, as well as increasing reliability of pumps,” says Goulds’ Knecht. For this purpose, Goulds developed PumpSmart technology, which provides advanced pump control protection and optimized logic designed to prevent failures, improve pump reliability and maximize the flow economy of process systems by using a standard variable-frequency drive (VFD) with pump-specific algorithms embedded directly into the drive. “The pump controlling software enables users to change the design of their operating systems, leveraging variable-speed technology, allowing them to reduce the lifecycle energy costs of their pumps by 30 to 40%, in many cases,” says Knecht.
Goulds I-Alert 2 equipment health monitor was also developed to help increase reliability and reduce total cost of ownership, he says. The health monitor combines Bluetooth and sensor technology to allow monitoring and diagnostics from a safe distance via a cell phone application (app). It provides continuous machine monitoring through early detection of failures, vibration, temperature and run-time monitoring, data logging with trend analysis, advanced vibration analysis tools and instant access to machine records. “This allows users to get quantitative data and analyze their pumps,” says Knecht.
PSG has been working to improve the design and operation of their pumps and related technologies in order to increase reliability and efficiency, says Jovani. One example is the recent development of Wilden’s Pro-Flo Shift air-distribution system (ADS). “A historic shortcoming in the operation of AODD pumps has been the loss of air, or energy, at the completion of the pump stroke,” he explains. “The Pro-Flo Shift features a unique air-control spool that eliminates this ‘over-pumping’ at the stroke’s completion, resulting in optimized air usage that can be as much as 60% less than competitive models.”
Also helping to increase reliability of pumps is selection of the proper material, says John Dean, U.S. Business field manager, chemical, pulp & paper with Netzsch (Exton, Pa.; www.netzsch.com/us). “Because the chemical industry has many demanding applications that involve the pumping of corrosive chemicals, one of the biggest challenges in selecting the right pump is determining what the best material of construction is for the pump,” he says. “Depending on how aggressive and corrosive the chemical is, the pumps may need to be supplied with anything ranging from 316SS, Duplex SS, Hastelloy, titanium or other metals and Buna, Viton, Teflon or other elastomers. For abrasive slurries and products, it is also important to size the pump and select the right materials for abrasion resistance” (Figure 2).
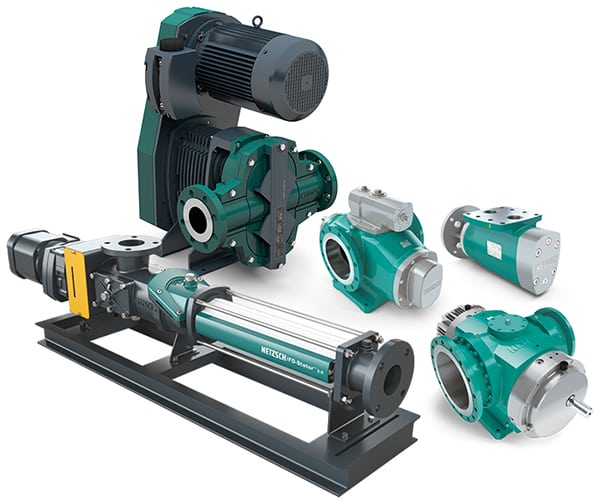
Figure 2. Netzsch offers pumps in a wide range of materials to meet some of the most demanding chemical applications. For abrasive slurries, the company can also supply the wear components of the pumps with coatings, such as tungsten carbide coating, to increase the life of the pump
Netzsch
Challenging applications
In addition to the need for containing leaks and increasing reliability, the CPI are also fraught with difficult applications that require pumps designed to handle the challenges.
One such example is GEA Group AG’s (Düsseldorf, Germany; www.gea.com) Hilge Novalobe rotary lobe pump. It was designed specifically for viscous media and for applications where gentle pumping or dosing is required. “The pumps are used mostly for highly viscous media, but, because they can operate at very slow rotations and speeds, they have very low shear, so they are also used for media that is not that viscous, but is sensitive to shear forces,” says Ulla Fraemke, product manager with GEA.
The company has recently expanded the Novalobe line to include larger pumps. “We realized we needed to have a larger pump to accommodate the larger equipment used in processes, as well as to provide the ability to operate it even more slowly to pump more sensitive products,” she explains. The Hilge Novalobe 60 (Figure 3) was designed for pumping and dosing highly viscous media, that may also contain large particles. The chamber volume was nearly doubled to 2.1 L per revolution and can pump particles measuring up to 41 mm. The new Novalobe can pump larger quantities at low speeds while ensuring that emulsions and sensitive materials do not separate while pumping.
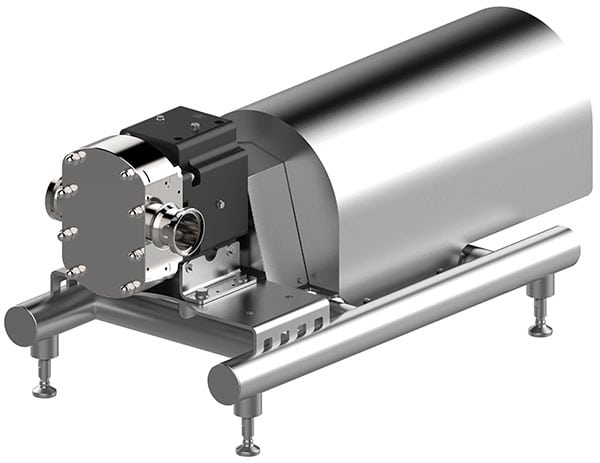
Figure 3. The Hilge Novalobe 60 was designed for pumping and dosing highly viscous media, also with large particles. The new Novalobe can pump larger quantities at low speeds while ensuring that emulsions and sensitive materials do not separate during pumping
GEA
A year of successfully field-testing the Novalobe 60 in a sugar factory confirmed its strengths in daily operation. Fraemke says production managers at the factory found it easy to operate the pump, and that wearing parts could be replaced without any retrofitting. The internal mechanical seals can be replaced from the front without removing the pump and the seals are lubricated and cooled optimally, extending the product lifetime.
Meanwhile, Sundyne (Arvada, Colo.; www.sundyne.com) also has developed pumps for challenging applications in the CPI. Its Ansimag sealless magnetic drive pumps (Figure 4) are finding use in the difficult production of chlor-alkali products, says Colin Guppy, chemical and industrial business unit leader. Because pumps are needed at each stage of the chlor-alkali manufacturing process to introduce catalysts and to move hazardous chemicals onto the next stage, plastic-lined pumps used for this application must eliminate emissions and leakage for worker safety and environmental protection. For this reason, sealless pumps are the preferred choice in these applications. The Ansimag pumps have no seals to replace, which means there are no leaks and no emissions. The pumps are also designed to streamline maintenance requirements and increase plant uptime. Ansimag pumps provide replacement options for aging ASME/ANSI B73.3 and ISO 2858 sized pumps, because the line covers a range of sizes and standard external dimensions to facilitate sealless or sealed pump replacement without changing piping or baseplates.
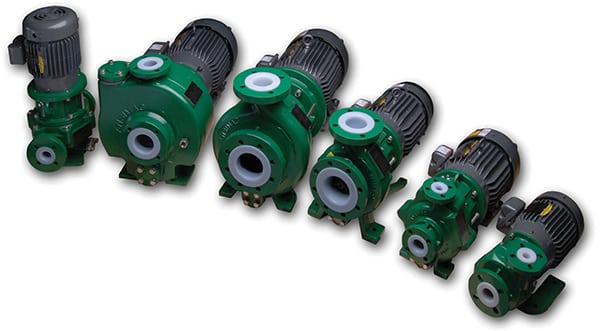
Figure 4. Ansimag pumps have no seals to replace, which means there are no leaks and no emissions. The pumps are also designed to streamline maintenance requirements and increase plant uptime
Sundyne
And, for applications where there are variations in the materials being pumped, Goulds’ ITT Bornemann recently released the SLW pump (Figure 5). Using a magnetic coupling, the SLW is a hermetically sealed, twin-screw pump used in the chemical and petrochemical sectors because it is environmentally friendly. The sealed chamber means critical media with harmful substances are confined to the pump and not released into the environment. The twin-screw technology allows high viscosity fluids and fluids with variations to be more ideally pumped due to the positive displacement technology (versus centrifugal), says Knecht.
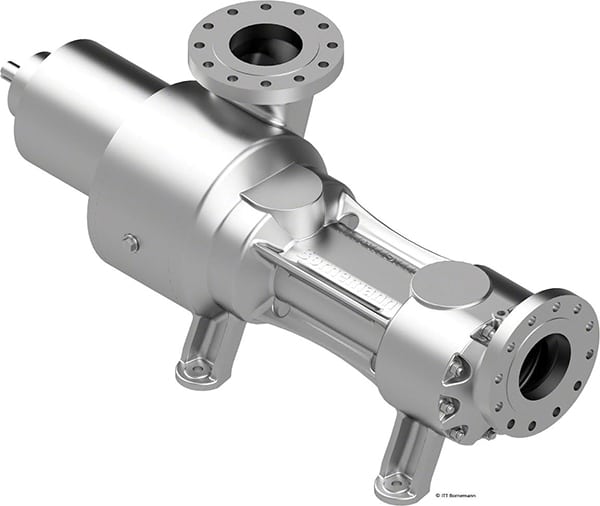
Figure 5. Using a magnetic coupling, the SLW is a hermetically sealed, twin-screw pump used in the chemical and petrochemical sectors because it is environmentally friendly
ITT Bornemann
A recent addition to Viking’s Universal Seal range — a widely used positive displacement internal gear pump — features a modified ribbed/stepped idler gear design (Figure 6). This pump has been specifically developed for sugar processing, but is finding use in applications where there are crystals in the pumped fluid. Removing 0.9 mm of material from 80% of the flank of each idler gear tooth on both sides results in reduced gear-to-gear contact that could damage tiny sugar crystals or other solids in the pumped fluid. “The special modification prevents crushing of growing sugar crystals in sugar mills and is finding chemical applications in preventing damage to microencapsulated products in herbicides and phase-change materials in polyurethanes,” says Hall. n