Hydrogen (H2) is an important chemical feedstock, mainly applied in the manufacture of ammonia and methanol, and for hydroprocessing operations in petroleum refineries. Also, since H2 is an energy carrier, it has been considered for stationary power and transportation applications. Hydrogen production technologies are separated into three main categories: thermal, electrolytic and photolytic. In thermal processes, such as reforming and gasification, H2 is produced from biomass and fossil fuels, such as coal and natural gas. In electrolytic processes, H2 is obtained from water-splitting, using electricity that can be generated from a variety of sources, such as wind. In photolytic processes, light energy allows hydrogen production using novel photoelectrochemical and photobiological water-splitting processes. In the U.S., H2 is mostly produced from natural gas using the thermal steam methane reforming (SMR) process. Natural gas is an important feedstock for H2 production since it is widely available and presents a high hydrogen-to-carbon ratio, reducing the generation of carbon dioxide (CO2) byproduct.
The process
In the process described below and depicted in Figure 1, H2 is produced from natural gas using an SMR process. The process was compiled based on information available in the chemical literature.
Sulfur removal. Natural gas feedstock is purified by catalytic treatment with H2 for removal of sulfur impurities. In the hydrotreater, H2 reacts, over a catalyst, with sulfur compounds present in the feed stream to form hydrogen sulfide (H2S), which is then adsorbed in the desulfurizer. Steam reforming. Purified natural gas is mixed with high-temperature steam and reformed into CO and H2. The reforming reaction requires a large amount of heat and takes place in an externally fired tubular reactor filled with catalyst. Water-gas shift. CO and steam react in a catalytic water-gas shift reaction, forming additional H2 and CO2. Purification. CO2 and other impurities are removed from the H2 stream in a pressure-swing adsorption (PSA) system. The purge stream from the PSA system is recycled to the reformer, where it is burned with fuel to provide heat to the reaction. The H2product obtained has purities of 99.99 wt.%.
Economic evaluation
An economic evaluation of the process was conducted based on the following assumptions: A central facility with a nominal capacity of 450,000 ton/yr of H2 erected on the U.S. Gulf Coast Distribution costs and storage for feedstock and product were not considered The estimated total fixed investment for the construction of this plant is about $460 million.
Global perspective
There are three kinds of facilities for H2 production: central, semi-central and distributed facilities (Figure 2). They differ in their location and scale of production, characteristics that directly affect H2 cost, competitiveness and timeframe to market.
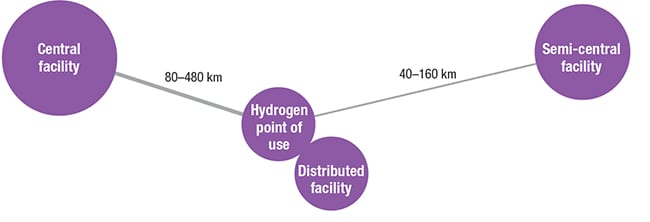
Figure 2. There are three types of hydrogen production facilities, and they differ in location and scale of production
Central facilities are located far from the H2 point of use and are able to produce large amounts of H2, benefiting from economies of scale. This type of facility requires high capital investment, as well as a distribution infrastructure able to cover large distances. Semi-central facilities present intermediate H2-production capacity. They present reduced distribution costs, since they are sited closer to H2 points of use. Distributed facilities are small facilities located close to or at the point of H2 use, reducing delivery costs. These facilities may present production capacities fitted to local demand. They require less investment than the other facilities, although unit production costs may be higher. n Edited by Scott Jenkins Editor’s Note: The content for this column is supplied by Intratec Solutions LLC (Houston; www.intratec.us) and edited by Chemical Engineering. The analyses and models presented are prepared on the basis of publicly available and non-confidential information. The content represents the opinions of Intratec only. More information about the methodology for preparing analysis can be found, along with terms of use, at www.intratec.us/che.