High-shear, high-speed mixing equipment supplies the mechanical energy necessary to reduce the size of solid particles and liquid droplets in emulsions and dispersions. Emulsions are mixtures of two normally immiscible liquids in which tiny particles of one liquid are suspended in another. Dispersions refer to solid particles distributed uniformly throughout a continuous medium. High-shear mixing processes are common across the chemical process industries (CPI), including in foods, cosmetics, pharmaceuticals, greases and lubricants, specialty chemicals, paints, inks and others. This one-page reference provides information on high-shear mixing operations and equipment.
Rotor-stator mixers
Rotor-stator mixers are standard workhorses used throughout the CPI for preparing fine dispersions and emulsions. The traditional design features a four-blade rotor running at tip speeds in the range of 3,000–4,000 ft/min within a close-tolerance fixed stator. The mixer creates mechanical and hydraulic shear by continuously drawing product components into the rotor and expelling them radially through the openings in the stator. Rotor-stator mixing devices are offered in both batch and inline configurations. Multi-stage designs are also available. These typically consist of 2–4 rows of teeth, and run at the same maximum tip speeds as their single-stage counterparts.
Particle size profile
Any high-shear, high-speed mixing operation — whether the process goal is powder dispersion, deagglomeration or emulsification — generates a Gaussian distribution of particle size. The objective is usually to produce the narrowest distribution possible with equipment that meets both process and business needs. In some applications, quality control is generally concerned with average particle size, while others follow strict standards pertaining to the largest diameter particles permitted in a suspension. Particle size profile is just one of many indicators of a good product. Depending on the end use, other properties like conductivity, stability, viscosity, color, gloss and so on, whether directly or indirectly related to particle size, are also considered during equipment testing and selection.
Particle size equilibrium
The majority of particle or droplet size reduction occurs within the first few passes through an inline mixer, or the first few tank turnovers in a batch mixer. This phenomenon is true for almost any dispersion or emulsion. Past this stage of sharp decrease in particle size, the distribution hovers at an equilibrium (see Figure 1). Additional processing will gradually narrow the distribution curve, but extending the process for this purpose alone is almost always unprofitable. If the equilibrium particle or droplet size achieved in a single-stage or multi-stage rotor-stator is larger than desired, manufacturers are often forced to use more expensive, higher-energy devices, such as high-pressure homogenizers and colloid mills.
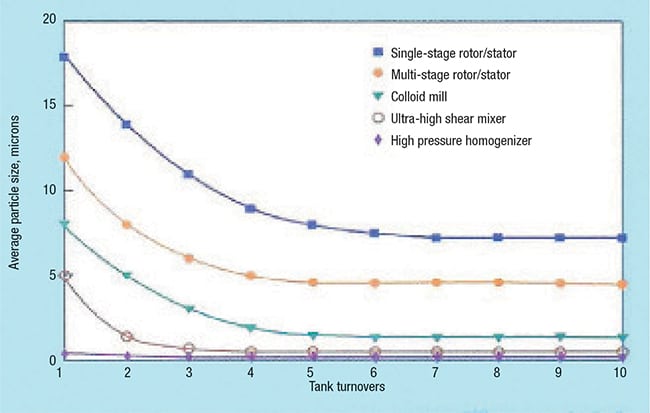
Figure 1. Various technologies can achieve different particle sizes (particle fineness) in emulsions
In a high-pressure homogenizer, the fluid is subjected to very high shear stress as it is forced through a specially designed homogenization nozzle at pressures of 150–200 MPa. However, high-pressure homogenizers, colloid mills (which also work on a rotor-stator principle) and similar equipment are commonly associated with several drawbacks, including higher capital cost and lower throughput than mixing technologies, along with frequent clogging, labor-intensive cleaning and high maintenance requirements.
Ultra-high shear
Among the recent developments in mixing are more cost-effective rotor-stator designs capable of delivering intense mixing along with rugged efficiency. Ultra-high-shear mixers offer the ability produce dispersions and emulsions superior to those made in multi-stage rotor-stators and colloid mills. In certain applications, these can replace high-pressure homogenizers, delivering comparable size reduction at significantly higher throughputs.
Ultra-high-shear mixers do not eliminate the premixing process — the feed must be a dispersion or emulsion in liquid form. Simple to operate, much like a regular inline rotor-stator mixer, these behave like a centrifugal pumping device. Materials are fed by gravity or pumped to the mixer. With the assistance of an auxiliary pump, ultra-high-shear mixers can process non-flowing, viscous materials like gels, pastes and creams.
Editor’s note: Material in this month’s column was contributed by Christine Banaszek, Charles Ross & Son Co. (Hauppauge, N.Y.; www.mixers.com).