There are a number of process technologies available to meet the strict standards for high-purity water in different industrial sectors
It is easy to think that the water coming out of our faucets can be used anywhere. Although potable water provided by a municipality is treated and held to specific safety and health standards, it often contains impurities that can have a significant impact on certain manufacturing processes and end products (Figure 1). This article reviews how water is purified for industrial use, why high-purity water is needed in different markets and how to maintain water quality over time.
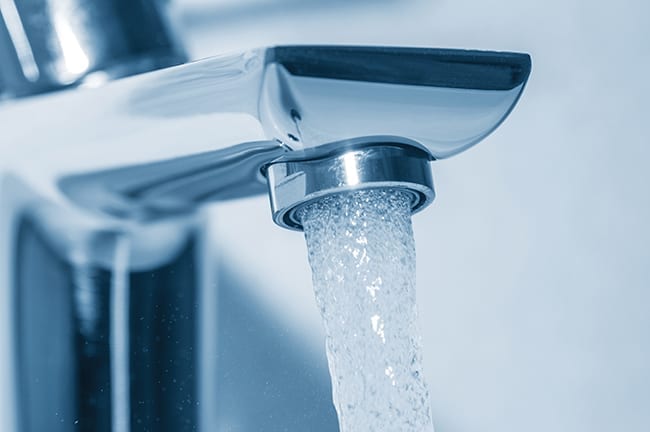
FIGURE 1. Many industrial processes demand water of higher purity than what is typically provided by municipalities, so additional treatment steps are often required
Purifying water for industrial use
There are a variety of systems and methods available to achieve differing degrees of water purification. Some methods are simple, such as media or carbon filtration, while other systems are far more complex, such as reverse osmosis and ultrafiltration. Typical components of a water purification system include the following:
- Activated carbon — Water is filtered through carbon to remove organic material and chlorine
- Particle filtration — Water is filtered through a physical barrier, removing fine particles and microorganisms
- Reverse osmosis (RO) — Water is forced through a semi-permeable membrane in the opposite direction of the natural flow with enough force to exceed the osmotic pressure, rejecting dissolved solids
- Ion exchange (IX) — Resins remove ionic impurities from water and are regenerated through a reversible chemical process
- Electrodeionization (EDI) — Combines ion exchange and ion-selective membranes with direct current to remove ionic impurities without the need for acids and caustic chemicals
- Ultraviolet (UV) light — Organic carbon reduction, bacteria, viruses and protozoa are exposed to UV light, damaging their DNA and rendering them inactive
- Ultrafiltration (UF) — Membrane filters remove extremely small particles, bacteria and pathogens
Different industries have specific regulations to follow in order to ensure ultrapure water meets their needs. Because each application is unique, a water purification system may include a single technology, or a combination of multiple technologies to achieve optimal results.
Pharmaceuticals and personal care
In the pharmaceutical and personal care markets, high-purity water regulations are defined by the United States Pharmacopeia (USP; Rockville, Md.; www.usp.org) and equivalent organizations in other parts of the world. The USP provides minimum standards around ionic and organic chemical purity and microbial contamination to protect the health and safety of consumers using the products (Figure 2).
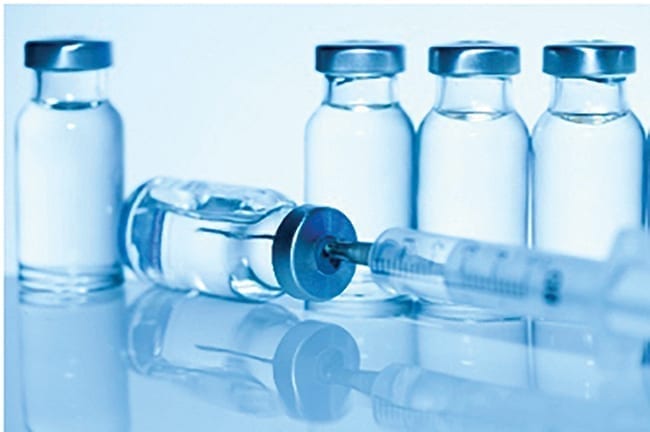
FIGURE 2. The production of pharmaceutical and personal-care products requires water that meets specific guidelines set forth by the Unites States Pharmacopeia (USP) organization
There are two grades of water quality that manufacturers of pharmaceutical and personal-care products may need: USP Purified Water or USP Water-for-Injection (WFI). Both grades have specific minimum levels for certain parameters. These include total organic carbon (TOC) content, as well as the amount of bacteria and endotoxins for WFI. Another important parameter is conductivity, which provides an indication of inorganic materials present in water, and is usually expressed in units of microSiemens (µS) per centimeter. The primary difference between the two grades is the more rigorous set of standards for microbial control required for WFI, as shown in Table 1, and the incoming water quality, for which USP Purified Water is based off of requirements set forth by the U.S. Environmental Protection Agency (EPA; Washington, D.C.; www.epa.gov) and the World Health Organization (WHO; Geneva, Switzerland; www.who.int).
A variety of water-treatment technologies are utilized to achieve these quality standards and typically include a combination of softeners, carbon filtration, UV light, particle filtration, reverse osmosis, ion exchange, electrodeionization and final filtration. In addition, the water treatment system should be regularly sanitized to prevent the growth of bacteria by using chemical, heat or ozone technology.
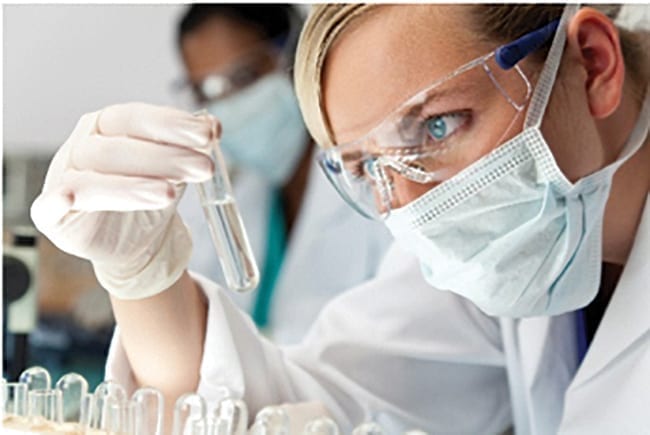
FIGURE 3. Water used in healthcare applications, such as laboratory testing and device processing, must meet stringent purity requirements
Medical industry
The healthcare market has very specific high-purity water-quality needs tied to various applications within hospitals, clinical-care facilities and medical research institutions (Figure 3). International and national standards authorities have established water-quality guidelines to ensure the highest-quality care can be provided to patients. High-purity water is critical as a feedwater source to equipment in four key application areas, described in the following sections.
Clinical chemistry and pathology. Reagent-grade water is necessary for laboratory testing and analysis. Poor water quality can affect the efficacy and accuracy of tests, operation of equipment and overall efficiency of the process.
Medical device reprocessing. High-purity feedwater is used for washers, disinfectors and steam sterilizers to clean and sterilize surgical instruments and medical devices. Water quality guidance is provided by the specifications of the Association for the Advancement of Medical Instrumentation (AAMI; www.aami.org) TIR34, “Water for the reprocessing of medical devices” to ensure that medical devices are properly disinfected and safe for patient use. Poor water quality can lead to instrument damage, reduced cleaning efficiency and more.
Dialysis. High-purity water is used as feedwater to dialysis machines and for dialyzer reprocessing and reuse. The incorrect water quality could have an adverse effect on the patient’s health and the quality of treatment.
Research laboratories. Several standards and guidelines are followed, such as those set forth by the Clinical and Laboratory Standards Institute (CLSI), ASTM International and the International Organization for Standardization (ISO). Water is one of the major components in many research applications and it is important to have the correct level of purity for consistent and accurate results.
A variety of treatment technologies are applicable for healthcare and research applications, including softening, carbon pre-treatment, reverse osmosis, deionization, UV and ultrafiltration. It is vital that water quality is consistently monitored to ensure that standards are met and to prevent any risks to research, testing or equipment that could impact patient care.
Microelectronics
High-purity water is used in a variety of applications for microelectronics, from circuits and microchips (Figure 4) to light-emitting diodes (LEDs), photovoltaic (PV) cells for solar panels, silicon wafers and semiconductors. Manufacturing semiconductors is a very complex process involving a myriad of chemicals and specialty gases. In simplistic terms, silicon wafers undergo multiple steps to build the transistors and circuit paths on the wafers. Each step requires high-purity chemicals and gases to create the layers and ultrapure water to rinse. Water-quality standards in these processes typically follow ASTM E-1.1, E-1.2 and SEMI C63 specification requirements with an emphasis on TOC, silica, metals (including boron) and particulate matter. The ultrapure water (UPW) system is usually made up of three major subsystems to achieve the required water quality: makeup, primary and polish. A typical UPW setup is shown in Figure 5.
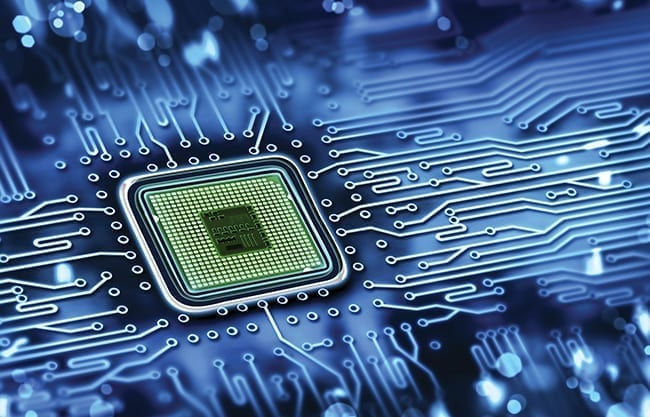
FIGURE 4. For the manufacture of semiconductors, impurities are closely monitored, with emphasis on total organic carbon (TOC), silica, metals and other particles
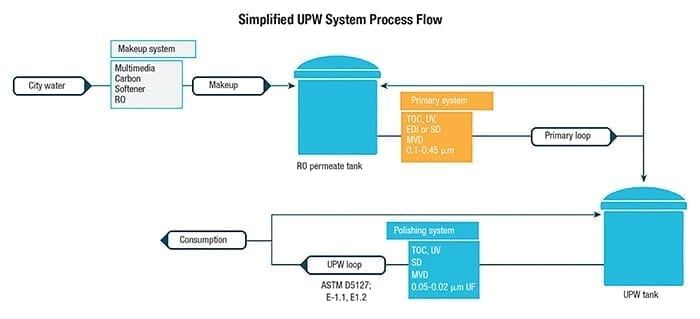
FIGURE 5. A typical ultrapure water (UPW) system will usually include three treatment units: makeup, primary and polishing
Makeup. The makeup system provides pretreatment, which is designed to remove the majority of contaminants from a municipal water supply. Here, greater than 99% removal of anions, metals, silica, TOC and particles is achieved using unit operations of media filtration, carbon filter or chemical feed, advanced oxidation processes (AOP), water softening and reverse osmosis (single or double pass). This equipment typically operates in an on/off fashion, as it fills a storage tank based on the facilities’ water consumption.
Primary. The primary subsystem focuses on the removal of trace amounts of contaminants to lessen the load on the polishing system. TOC-destruct UV, service demineralization (SD), membrane vacuum degasification (MVD), EDI or ion exchange and sub-micron cartridge filters (CF) are typical unit operations. This system is designed to run continuously in recirculation and feed the polish loop based on consumption of water in the facility.
Polish. The final part of the treatment system focuses on maintaining the required UPW quality and removing any final traces of contaminants. TOC-destruct UV, polish ion exchange, critical sub-micron CF or UF modules are necessary to meet particle removal needs. This system runs continuously at a higher flowrate than the primary system to maintain velocity to the piping distribution loop and laterals that provide water to all factory points of use.
Ramifications of water impurity
Depending on the intended use for high-purity water and the industry, the consequences of water impurity are significant. For the medical, pharmaceutical or personal-care industries, poor water quality can put a patient’s health at risk, result in plant shutdowns or cause important drug products to be destroyed.Furthermore, the usage and lifespan of medical equipment and laboratory testing relies on high-purity water. It can impact the longevity of equipment and potentially skew results or disrupt testing practices. Impure water can lead to issues with medical devices and test results in laboratories, which can lead to costly replacements, equipment downtime or delays in care.
Manufacturing and microtechnology rely on ultrapure water to make sure the smallest pieces of electronics and technology run as they should. Issues with impure water can cause disruptions in manufacturing, costing the manufacturer time and resources to solve the problem. Furthermore, it exposes the manufacturer to possible widespread product defects and recalls, depleting resources even further.
Servicing a UPW system
Proactively avoiding issues with a water purification system is just as important as selecting and installing the system in the first place. A well-planned and maintained system is extremely important to protect both the manufacturer and the end user.
Ultimately, the manufacturer is responsible for establishing the specific water-quality standards that it needs to build into its process to ensure the water being used meets industry and safety guidelines. As a result, manufacturers often look to water-treatment technology providers to understand water standards and assist with system design, installation and ongoing service to maintain water quality and reliability.
Since a water-purification system is as complicated as it is important, requiring a sophisticated knowledge base encompassing mechanics, physics and chemistry, partnering with an expert can prove to be very valuable. To ensure that high-purity water flows without any problems, a service provider should offer an understanding on meeting water-purity industry standards, know-how to design and build an appropriate water-treatment system and have the capability to provide timely and reliable maintenance and repairs. ■
Edited by Mary Page Bailey
Authors
Jeff Holland is the director of health sciences at Evoqua Water Technologies (Email: jeffrey.holland@evoqua.com). He has over 15 years of experience in water treatment, specializing in healthcare, clinical and laboratory applications. He has a B.S. in civil engineering (construction engineering & management) from North Carolina State University and an M.B.A. with concentration in healthcare from the University of North Carolina at Chapel Hill. Holland is also a member of the American Society for Healthcare Engineering (ASHE), the Association for the Advancement of Medical Instrumentation (AAMI), the International Association of Healthcare Central Service Material Management (IAHCSMM) and the American Association for Clinical Chemistry (AACC).
Rich Jarrett is the pharmaceutical market director at Evoqua Water Technologies (Email: richard.jarrett@evoqua.com). In this role, Jarrett leads efforts related to water-treatment solutions and product requirements for the pharmaceutical industry. He has more than 14 years of experience working with the pharmaceutical industry in developing products and services for improved quality, reduced cycle time, enhanced manufacturing and regulatory compliance. He earned a B.S. degree from Cornell University and an M.S. in business administration from the Kellogg Graduate School at Northwestern University.
Alan Knapp is the microelectronics market director for Evoqua Water Technologies (Email: alan.knapp@evoqua.com) and is responsible for identifying industrial ultrapure/wastewater challenges and developing solutions for customers in the semiconductor, nanotechnology and solar energy markets. He has been active with ultrapure water and wastewater solutions in the industrial market since 1984. Knapp has a mechanical engineering technologist diploma from Conestoga College in Kitchener, Ontario, Canada, along with several accreditations with ASME and ISO. He is also an active member of the International Roadmap for Devices and Systems (IRDS) committees and a member of the SEMI organization and a co-moderator at the GWI Ultrapure Micro Conference. He has published several papers for Ultrapure Water Magazine and the International Water Conference.