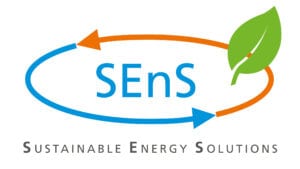
Source: GEA
The Sustainable Energy Solutions (SEnS) offering from GEA (Düsseldorf, Germany) integrates processes and utilities (refrigeration and heating) solutions, allowing GEA experts to develop optimization strategies for customers in diverse industries. Potential energy savings of up to 30% and a significant reduction in CO2 emissions by as much as 90 or even 100% are possible, says the company. Numerous successfully completed SEnS projects from GEA show that these optimizations reduce the customer’s energy footprint and running costs, without compromising output or the bottom line.
According to the United Nations, energy efficiency offers a potential 40% of the emission reductions required to help meet global climate goals. Due to a growing number of rules and regulations and its own climate targets, there is an absolute need for the industry to reduce its carbon footprint and become more energy efficient overall. With cooling and heating traditionally accounting for anywhere between 50 and 90% of a plant’s entire energy consumption, it’s the ideal starting point for GEA’s SEnS initiative.
GEA’s unique SEnS offering is a culmination of a broad processing portfolio and years of industry know-how combined with extensive refrigeration expertise. “SEnS supports customers in the food processing, dairy and beverage industries, helping them achieve their climate goals by making them more sustainable,” comments Kai Becker, since February 1, 2021, CEO Refrigeration Technology Division. As a global industrial technology provider, GEA will continue to strengthen its SEnS offering in 2021. Using the SEnS approach, GEA will promote the increased adoption of sustainable solutions which drive down energy consumption and reduce carbon emissions while helping customers from diverse industry sectors slash their operational costs.
Typically, process plants are designed in a way that separates processes from utilities (cooling and heating), rather than considering them as a whole. Customers often place tremendous focus on the design or optimization of a particular process, overlooking the bigger picture. GEA combines these two parts and ensures that they work well together.
“GEA has developed a structured holistic and proven approach that begins with analyzing the customer’s precise energy requirements, then making process optimizations and including utilities in the equation. By connecting heat pump technology to manufacturing processes, the GEA experts ensure energy is moving circularly, rather than being wasted”, says Ulrich Walk, chief service officer (CSO) – Refrigeration Technologies.
Each GEA SEnS project includes a single point of contact enabling customers to achieve genuine and proven reductions in energy consumption and their carbon footprint. The SEnS process is backed up by a cross-functional engineering team with experts from dairy, food or beverage processing as required, as well as team members with refrigeration (heating & cooling) expertise in diverse processing industries. Each project considers the customer’s business parameters and ambitions, formulated as measurable KPIs, against which the installation must deliver.
When it comes to plant upgrades, GEA recommends that customers should integrate the GEA experts as early as possible in the design process. Doing so can mitigate potential frustrations later on as the solution will be more closely aligned with expectations at a very early stage. Another big advantage: This early involvement will lead to more cost-efficiency. “GEA has decades of experience helping customers improve the efficiency of their plants – and now the process has been made even easier,” concludes Becker.