Successful dispersion depends on a basic understanding of dispersion equipment and how dispersers should be used
High-shear mixers typically operate at high rotational speeds and are used for mixing applications that are best described as dispersion processes. They can be used in a variety of applications, such as to speed additions, wet powders, break lumps and provide process intensification. Many dispersion problems are caused by incorrect use of equipment, when simple operational changes may give better results. While the inherent intensity of high-shear dispersers sometimes provides limited success even when they are misused, successful dispersion depends on a basic understanding of how the dispersers should be employed. This article focuses on the use of these dispersers during the addition of powders and liquids to liquids. Best practices for successful dispersion and the different types of dispersers are discussed.
Basic Principles
The high rotational speeds of high-shear dispersers are often the motor speeds, including speeds at the electric power frequency. Most dispersers operate at a single speed, although some large dispersers may have variable speed control. The dispersions may be powder dispersions in a low-viscosity liquid, or liquid dispersions of miscible or immiscible liquids. In a few instances, gas bubbles may be dispersed in a liquid for a transport process or to create a foam. The purpose of dispersion is rapid formation of a suitably uniform fluid. For processes involving soluble solids, the equipment may be called a dissolver. With dispersed thickeners or emulsion formation, the fluid viscosity may increase.
This lengthy description is needed because different processes and applications can be accomplished with variations on similar equipment (see section on Types of High-Shear Dispersers). The open impellers for high-speed dispersers may be sawtooth disks, short-bladed impellers or slotted heads. Some rotating impellers are mounted inside a stationary cage having either holes or slots, through which the fluid is forced. These mixers are usually called rotor-stators, but may also be called homogenizers. The primary mechanism causing dispersion is hydraulic shear, although some mechanical shear is also present, especially with rotor-stator mixers. Even within the general category of high-shear mixers, some are used primarily for rapid initial dispersion, while others use multiple recirculation passes for improved dispersion and uniformity. Hydraulic shear is rarely sufficient to grind or reduce the size of individual particles, but it will break agglomerates or lumps. Some particle breakage may occur with weak organic or biologic particles. Other types of mills or grinders are used when particle-size reduction is needed.
Although most of the high-shear dispersers are mounted either on-center or slightly off-center, they may be either top or bottom mounted. To control the fluid swirl created by the rotating impeller, the tanks often have one or more baffles. Too much rotational flow and a surface vortex that draws air into the impeller can reduce dispersion and create unwanted air bubbles in the product. Flow through a stator eliminates much of the rotational flow from the discharge of rotor-stator mixers. Single or dual baffles may be adjustable to control a surface vortex. In other disperser designs, off-center mounting or tanks with square cross-sections are used to reduce the need for baffles. A deep vortex with rotational flow does not provide good mixing (see the boxes for High-Shear Mixing: Do and Don’t, pp. 41–42).
High-speed dispersion
To create “dispersions” of solids, gases or immiscible liquids, a disperser must break the added components into individual particles, gas bubbles or liquid droplets. A high-speed disperser also allows the rapid addition of miscible liquids or soluble solids. Whether the process is batch or continuous, rapid addition usually results in greater productivity and sometimes better quality.
Solids dispersion. For solids dispersion, individual particles need to be surrounded by liquid and initially suspended. To make sure that individual particles are exposed to the liquid, the rate of addition must be controlled. If solids are added too rapidly, clusters of particles will carry trapped air into the liquid and the partially wetted powder may form lumps. If the particles hydrate in the liquid, the particles must be separated and suspended quickly.
If the solids are soluble, the rate of dissolution is determined primarily by equilibrium solubility and particle size. Fluid motion may enhance the external mass transfer around the particle, but concentration uniformity in the fluid provides the most effective driving force for dissolution.
For insoluble solid particles, the typical objective is continued suspension with some degree of uniformity. The degree of suspension and uniformity is determined by the liquid velocity and flow pattern. If rotational flow is not adequately controlled by baffles or off-center mounting, some solids may never be suspended off the bottom of the tank. Since most high-speed dispersion impellers are radial flow, they need to be near the bottom of the tank to create a flow pattern that will lift and suspend settling particles.
Liquid dispersion. For liquid dispersion of an immiscible liquid, nearly all of the actual droplet breakage occurs in the fluid velocity gradients near the impeller blades. The rate of addition must be controlled so that the disperser can break the liquid into individual droplets. The ultimate drop size and dispersion uniformity are closely related to the impeller tip speed or peripheral velocity of the disperser. However, viscosity difference and surface tension also influence the drop size. The rate at which a dispersion is formed may depend on how many passes through the disperser are required for uniformity.
Gas dispersion. Gas dispersion by a high-speed disperser is typically less effective than sparged gas dispersion, where the gas enters from below the impeller. Gas dispersion brought from the surface by a vortex may be difficult to control, since it is affected by both liquid-level coverage and baffle adjustment. For dispersion of solids and liquids, gas entrainment should be avoided or closely controlled.
High-shear dispersion
Shear effects are responsible for the creation of dispersions. However, some dispersions are more shear-dependent than others. The dominant shear mechanism for most high-speed impellers is hydraulic shear, resulting from velocity gradients around the impeller. The high velocity of the rotating blades creates locally high fluid velocities in the liquid. The velocity gradients responsible for fluid shear may be associated with trailing vortices near the tips of the blades. Sawtooth blades will create multiple fluid vortices, with one forming behind each blade tip. Sawtooth blades may contribute mechanical shear when large or dense particles strike the blade tips.
High-shear impellers composed of a rotating blade surrounded by a stationary grid, are commonly called rotor-stator dispersers or even homogenizers. The dispersion mechanisms with rotor-stator dispersers are a complicated combination of primarily fluid shear with some mechanical shear. Any significant amount of mechanical shear will wear or damage the disperser head. The rotor of some dispersers looks like a typical bladed impeller. The stator may have either slots or holes, through which the dispersion passes. In other rotor-stators the rotating element is more like a vertically slotted cylinder, which rotates inside a similarly slotted stationary cylinder. However, to control mechanical vibration, the number of slots in the rotor is lower than the number of slots in the stator. The unequal number of slots means that only two or three of perhaps ten to twenty slots are aligned and open at any instant in the rotation.
Several types of flow and mechanisms contribute to the hydraulic shear in a rotor-stator. Some shear occurs with an inrush of flow as a pair of slots begin to align. The shear is caused both by flow through a narrow slot and that flow resulting in a vortex in the stator slot. The flow is caused by a pressure differential between the inner rotor flow and the outer slot flow. Flow through an open slot contributes to the shear effects. As the slot alignment begins to close, the fluid momentum creates another jet of fluid that also swirls in the stationary slot. The small gap between the rotor and the stator creates a velocity gradient and shear effects associated with the differential speed. Some combination of differential velocities, changing directions, and interrupted flow contribute to the hydraulic shear effects.
Shear effects in rotor-stator mixers contribute to the breaking of agglomerates or lumps. Agglomerates often form when particles of thickeners begin to soften and become sticky. If particles are added too quickly or not dispersed well enough, the agglomerates may develop a sticky outer surface that limits penetration of liquid into the nearly dry or only partially hydrated material inside the lump. If rapid dispersion of particles is not sufficient to avoid formation of lumps, then mechanical shear may be necessary to break the lumps. As the particles of thickener continue to hydrate, fluid shear is necessary to stretch and fold the increasingly viscous fluid created by the thickener.
Common Applications
Liquid blending
Most liquid blending applications do not require high-shear dispersers for uniform blending. As with many types of mixing equipment, however, multiple purposes can be served by the same type of mixer. High-speed dispersers may be used simply to achieve rapid liquid addition and blending. Dispersers are often used for a multi-step batch process that may involve both the addition of miscible liquids and dispersion of solids for dissolving. The addition of miscible fluids with differing viscosities may require dispersion to effectively combine the fluids. The high power requirements of high-speed dispersers may not be energy efficient, unless the rate of addition or the heat added by power are important to the overall process.
Formulations and chemical reactions
Some applications for high-speed dispersers involve only the physical combination of ingredients or components. Such formulation applications may not involve any chemical reactions and only involve forms of blending for a uniform composition. Dispersions may be composed of liquids with solids, gases or immiscible liquids. The quantities of added powder or liquid should not exceed the capacity of the base liquid to disperse, suspend or dissolve the additions.
Other applications may involve composition changes associated with chemical reactions. Some chemical reactions may only take advantage of the rapid and intense mixing in the impeller region. Other chemical reactions may involve mass transfer between dispersed solids, immiscible liquids, or gas bubbles. For multi-phase reactions, the effects of the dispersers promote both dispersion and rapid mixing for chemical reaction.
Quality checks
When additions to a batch are finished, some observational checks may be made. First, the disperser must be stopped for safety. Then a screen might be used to scoop material from the surface to check for lumps. If the liquid is clear, a check for undissolved particles may be possible. Bubbles or foam on the surface will show that dispersed gas is present. If large bubbles come to the surface, dispersed gas may have accumulated around the impeller. Drawing a vacuum on a batch may aid in the removal of air bubbles, but only if fluid with dissolved gas is circulated to the surface. Any other non-uniformities on the surface may be signs of mixing problems. Continued operation of the disperser may be sufficient to reduce some problems.
Types of High-Shear Dispersers
Most high-shear dispersers are top-mounted on cylindrical tanks. The tanks may be baffled, partially baffled, or unbaffled depending on the process and fluid viscosity. At low viscosity as an alternative to baffles or to improve vortex control, the disperser may be off-center mounted. The off-center location is typically from 15 to 40% of the radius from the center of the tank.
Vortex formation is difficult to predict and strongly dependent on liquid level. To control the vortex formed with a high-shear disperser effectively, adjustable baffles may be used. Figure 1 shows three different types of adjustable baffles, all of which can be adjusted while the tank is filled. Some baffles can be adjusted while the disperser is operating.
High-shear sawtooth disks
Sawtooth disks are the simplest high-shear dispersers. Typical examples are shown in Figure 2. Sawtooth blades are usually bolted to the bottom end of the mixer shaft. Sometimes the mixer drive can be raised and lowered while the disperser is operating to more effectively mix all of the tank contents.
Most of the dispersion by a sawtooth disk is a result of hydraulic shear. Trailing vortices that are shed from the teeth on the blades contribute to high local velocity gradients. Some agglomerates may be dispersed by physical contact with the teeth on the disks. Abrasive wear on high-shear disks is common and requires periodic disk replacement. Most of the flow patterns generated by high-shear disks are rotational or radial. Disks with angled blades or flow pockets may create some axial flow.
High-shear disks may be used in high-viscosity fluids or emulsions. Viscous drag across the disk surface creates a radial discharge and flow pattern. The high-power input associated with the high-speed blades overwhelms the resistance to flow in high-viscosity fluids. High power input adds heat to the fluid, resulting in a temperature increase.
Rotary-head dispersers
High-shear, rotary-head dispersers are typically mounted in baffled or partially baffled tanks and may also be offset from the center. Figure 3 shows an offset-mounted rotary-head disperser in a tank with an adjustable baffle.
Rotary-head dispersers, also called closed-rotor dispersers, like those shown in Figure 4, create more local flow through the impeller than sawtooth disk impellers.
Because the rotary-head-style dispersers typically operate at lower tip speeds in lower viscosity fluids than sawtooth disks, they are less susceptible to mechanical wear. The lower tip speeds may not provide as intense dispersion as is possible with the sawtooth disks. The rotary-head dispersers are often used for addition of miscible liquids, soluble powders or viscosity modifiers.
Bottom-mounted dispersers
Many high-shear dispersers are manufactured and sold as disperser-in-tank packages, because the sizes are transportable and the combination simplifies purchasing and installation. Some tank and mixer combinations have a square cross-section with rounded corners, like the one shown in Figure 5.
Many different types of bottom-mount high-shear blades are available for different applications (Figure 6). Some of these impellers are designed to chop frozen foods or create emulsions.
Bottom-mounted high-shear dispersers can create a deep vortex, even with baffles in the tank (Figure 7).
Rotor-stator dispersers
Rotor-stator dispersers have an impeller, with blades or slots, rotating inside a stationary cylindrical housing. The stationary housing may have either slots or holes depending on the type of dispersion required for the process. The impeller typically draws incoming flow primarily from below the head to limit vortexing. Figure 8 shows a slotted rotor inside a slotted stator. The flow pattern is between the rotating slots and through the stationary slots.
Unequal numbers of slots in the rotor and the stator allow flow through only a few slots at a time. The partial alignment of slots limits noise and vibration caused by flow pulsed through the slots.
Some rotor-stator dispersers have an impeller with blades rotating inside a stator with slots or holes (Figure 9). Many different types of stators are available to create dispersions of different-sized particle agglomerates or immiscible liquids (Figure 10).
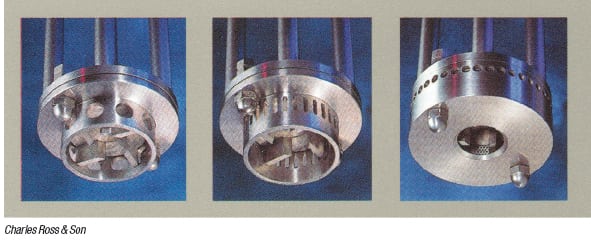
Figure 9. Some rotor-stator dispersers have an impeller with blades rotating inside a stator with slots or holes
Flow through the stator is strictly radially outward, with no rotational flow in the discharge. The only rotational flow comes from the inlet side of the rotor or additional impellers mounted on the rotating shaft above the rotor-stator. To create vertical motion in a rotor-stator mixed tank, axial flow impellers can be attached to the rotating shaft. Reversing the direction of the mixer rotation can either draw liquids and powders down from the surface or draw flow up from the bottom (Figure 11).
Laboratory dispersers
Various types of laboratory high-shear dispersers are available for accomplishing small-scale tasks similar to the large-scale dispersers (Figure 12).
Inline dispersers
Not all high-shear dispersers are mounted in tanks. Some are installed in a line feeding a tank or in a recirculation loop connected to a tank. A few applications may use the inline disperser only to combine ingredients and send them to other equipment for further processing. Many inline dispersers are designed to draw in powdered ingredients and disperse them immediately into a liquid (Figure 13).
Powdered ingredients may be soluble materials or thickening agents that hydrate in the liquid. Rapid and intense contacting helps wet particles quickly and reduces the chance of lumps forming.
The heads for inline dispersers are similar to other rotor-stator heads (Figure 14).
Choosing equipment
The high-shear dispersers discussed in this article are not the only types of equipment that can be used for dispersion. Turbine impeller mixers, with conventional or special purpose impellers, will be effective in some dispersion processes. For difficult emulsions inline rotor-stators, high-pressure homogenizers, and colloid mills will create finer dispersions. These inline or pressure-driven dispersers also require an external pump. Some dispersers are an integral part of a system with other types of impellers, including turbines or sweeps to handle a range of viscosities. Inline dispersers can be used in an external loop connected to a conventionally mixed tank. The primary purpose of dispersers used in multiple-impeller systems is to provide intense mixing at a point in the process.
No matter what a vendor’s sales representative can tell you about your process and available equipment, testing is an essential part of high-shear disperser selection. Actual materials, process objectives, and quality controls are all factors in the selection of appropriate high-shear dispersers. Any equipment or process must be sufficiently robust to handle expected upsets, process variations and ingredient changes. Few processes or products are so well controlled and defined as to remain completely unchanged for long periods. Some knowledge of high-shear dispersers only comes from experience. ■
Edited by Dorothy Lozowski
Related stories, such as Ten Things You May Not Know About Liquid Mixing Scaleup, Chem. Eng., August 2013, Increase Productivity Through Better Gas-Liquid Mixing, Chem. Eng., October 2007, and Mixing Systems: Design and Scaleup, Chem. Eng., April 2006, can be found online at www.chemengonline.com
High-Shear Mixing: Do
Submerge the impeller.The disperser impeller should remain fully submerged, unless gas dispersion is the purpose of the process. When the disperser remains fully submerged, it provides maximum energy input with the greatest amount of hydraulic shear. When gas passes through a rotating impeller, the power input and liquid flow are drastically reduced. The power and flow loss may be continuous or cyclical. In either case, vibration or surging place additional mechanical loads on the disperser and reduce the effectiveness of powder or liquid dispersion. When gas passes through the impeller, it creates a rumbling sound and mechanical vibration.
Control vortex depth and rate of addition. In cases where the mixing equipment is designed to handle the vibration of air going through the impeller and air bubbles do not adversely affect the process, a tradeoff exists between vortex depth and rate of powder addition. A deep vortex may allow for more rapid liquid or powder addition, but blending and dispersion will be reduced. The balance between vortex depth and rate of addition is too often left to the discretion of the production operator. To achieve consistent product quality and mixing results, both vortex depth and rate of addition must be controlled.
Maintain liquid levels. The primary and preferred means used to prevent gas entering the impeller region is adequate liquid coverage. Mixing tanks designed for use with high-shear dispersers are sometimes taller than the tank diameter, to as much as 125% of the tank diameter. Adequate liquid coverage may be at least one-third the tank height or often half the tank height. The off-bottom location of the rotating impeller will influence the minimum liquid level for mixing and coverage to maintain submergence.
Make additions carefully. Any additions on the surface should be made about halfway between the tank wall and the mixer shaft, away from solid surfaces. Additions near the tank wall or mixer shaft are likely to accumulate on the equipment surfaces and be difficult to dislodge and disperse. All powder additions should be slow enough that individual particles have time to wet and air between particles is allowed to escape. Rapid powder addition will carry gas bubbles into the liquid. Some liquids may be added along a tank wall to reduce splashing and possible foaming, but any material sticking to the wall should be washed into the batch.
Tips For Successful High-Shear Dispersion
- Good surface motion with some swirl and strong flow toward the center is necessary to add and disperse powders or liquids successfully. A controlled surface vortex will assist the addition of floating powders.
- To avoid air entrainment, a surface vortex should not extend more than halfway from the surface to the impeller. Most high-speed dispersers have only a single rotational speed with an impeller near the bottom, so surface motion must be controlled by liquid level and baffle adjustment. To prevent a vortex from reaching the impeller, the liquid level and/or baffle effect need to be increased.
- The liquid level usually needs to be at least one third of the tank diameter, but may be greater than the tank diameter.
- A periodic or continuous rumbling with vibration means that air is being sucked into the impeller. Air drawn from the surface or added with powders will form bubbles that will be difficult to remove. The formation of air bubbles should be avoided if possible.
- Controlled addition of powders is a good way to get rapid dispersion and avoid lump formation. The addition point for powders or liquids should be approximately midway between the side and the center of the tank.
- If additions of powders or liquids change the liquid level or viscosity, the baffles may need to be adjusted to maintain surface motion.
- The quantities of powders or liquids should not exceed the capacity of the liquid to disperse, suspend or dissolve them.
- Stopping the disperser at the end of a batch will allow an opportunity to check the quality of the dispersion. A screen may be used to scoop material from the surface to check for lumps. In a clear liquid, a check for undissolved particles may be possible. Large air bubbles coming to the surface show that dispersed air has been trapped around the impeller.
High-Shear Mixing: Don’t
Allow deep vortices. Don’t allow a surface vortex to extend all of the way to the rotating impeller, except in some very forgiving processes. The presence of dispersed air usually does not add value to a liquid product and can be difficult to remove, especially from a viscous liquid. Often mistaken for “good mixing” a deep surface vortex is usually a sign of “poor mixing.” If the surface vortex reaches the impeller, power and flow are lost. Rumbling and vibration are signs of air entrainment. When a deep vortex is present, the primary flow pattern in the remainder of the tank may be rotational, with insufficient radial and vertical mixing. In rotational flow, the fluid moves in solid-body rotation, which neither mixes liquids nor suspends solids.
Bypass the impeller. The purpose of tank baffles is to control the surface vortex and promote vertical mixing. While vigorous surface motion aids or speeds the addition of powders and liquids, the direction of motion must include flow across the surface and toward the center of the tank. If a vortex reaches the impeller, surface additions will go through the impeller without wetting by the bulk liquid. Initial bypassing of the impeller by surface additions means that additional recirculations are required to obtain the desired dispersion. That additional circulation time may allow agglomerates or lumps to form. The presence of adjustable baffles is intended to allow vigorous surface motion without having the vortex reach the impeller. If additions to a batch increase the liquid level or fluid viscosity, adjustment of the baffles may be necessary.
Author
David S. Dickey has run his own consulting business called MixTech, Inc. since 1998 (Website: www.mixtech.com; Email:[email protected]). He has more than 35 years experience designing mixing equipment and solving process or mechanical problems with most types of fluid and powder mixing equipment. He received his B.S.Ch.E. from the University of Illinois and completed his M.S. and Ph.D. degrees in chemical engineering at Purdue University. He is a fellow of the AIChE, and is a past president of the North American Mixing Forum (NAMF).