Methane Reforming:
Solving the Hydrogen Blues
Improved catalysts and reconfigured reformer designs make steam-methane reforming the most scalable, industry-ready source of ‘blue’ H2
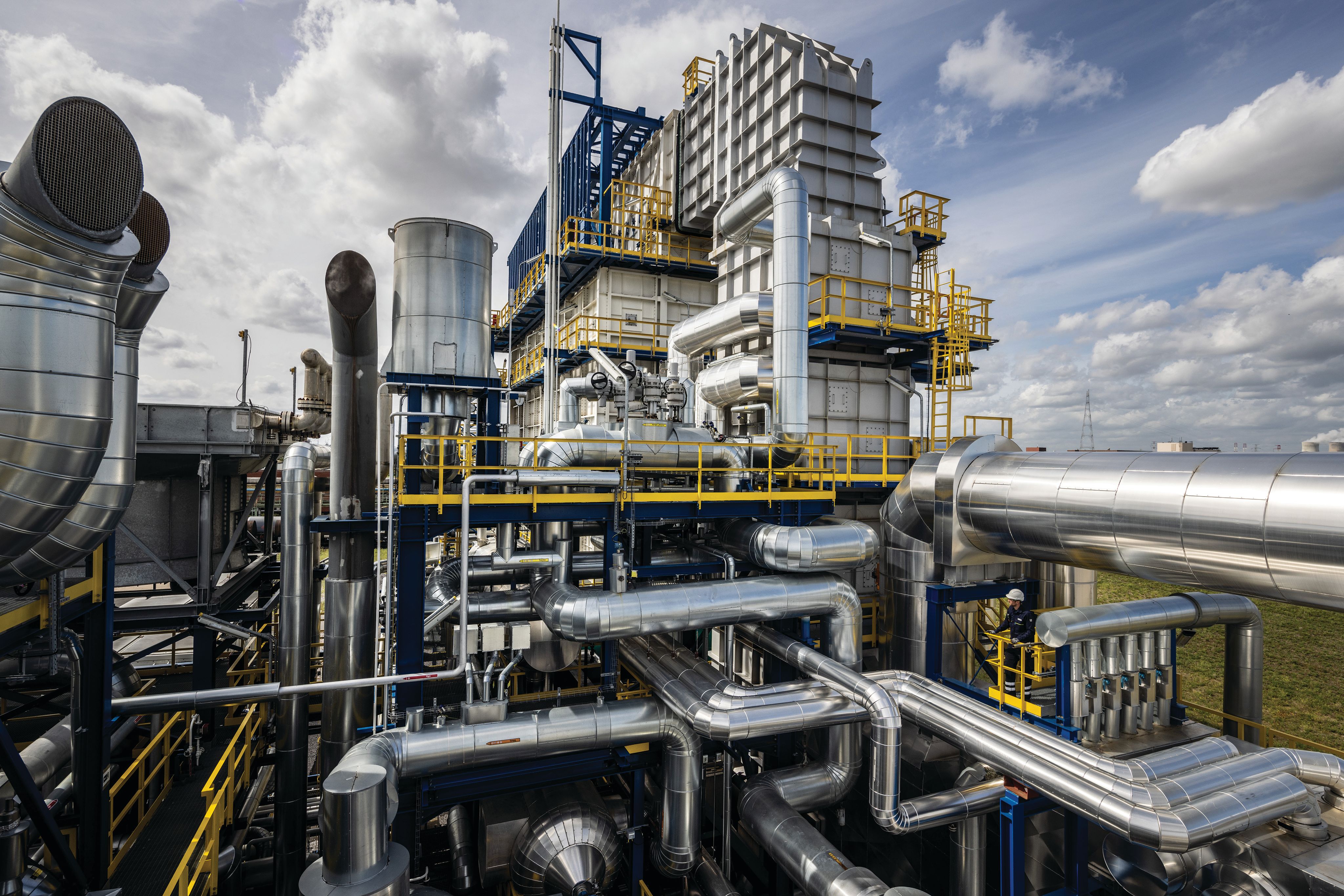
For many decades, steam-methane reforming (SMR) has been, and still is, the technology of choice for the large-scale production of synthesis gas (syngas; a mixture of H2 and CO), which is used for making a large number of chemicals, including ammonia, methanol, acetic acid, liquid fuels and more. When only H2 is desired, such as for ammonia production, steel making and petroleum-refining applications, the CO in the syngas is “shifted” to CO2 using the water-gas shift reaction (WGSR). In the past, the CO2 produced from SMRs — both from the burning of fuel to heat the reformer tubes and the product from the reforming reaction — has been, for the most part, released to the atmosphere.
Now, with goals to reduce the global emissions of greenhouse gases (GHGs) taking center stage, efforts are underway to generate H2 with a low carbon footprint. As a result, there has been a growing interest in water electrolysis as a source for “green” hydrogen. However, electrolyzers are still expensive, are not scalable to meet the large demands for H2, and the availability of a reliable, inexpensive source of “green” electricity to run them is still not a reality. Until these issues hampering the shift to green H2 are addressed, the medium-term solution is “blue” hydrogen — H2 made by conventional reforming technologies, but combined with carbon capture, utilization and storage (CCUS).
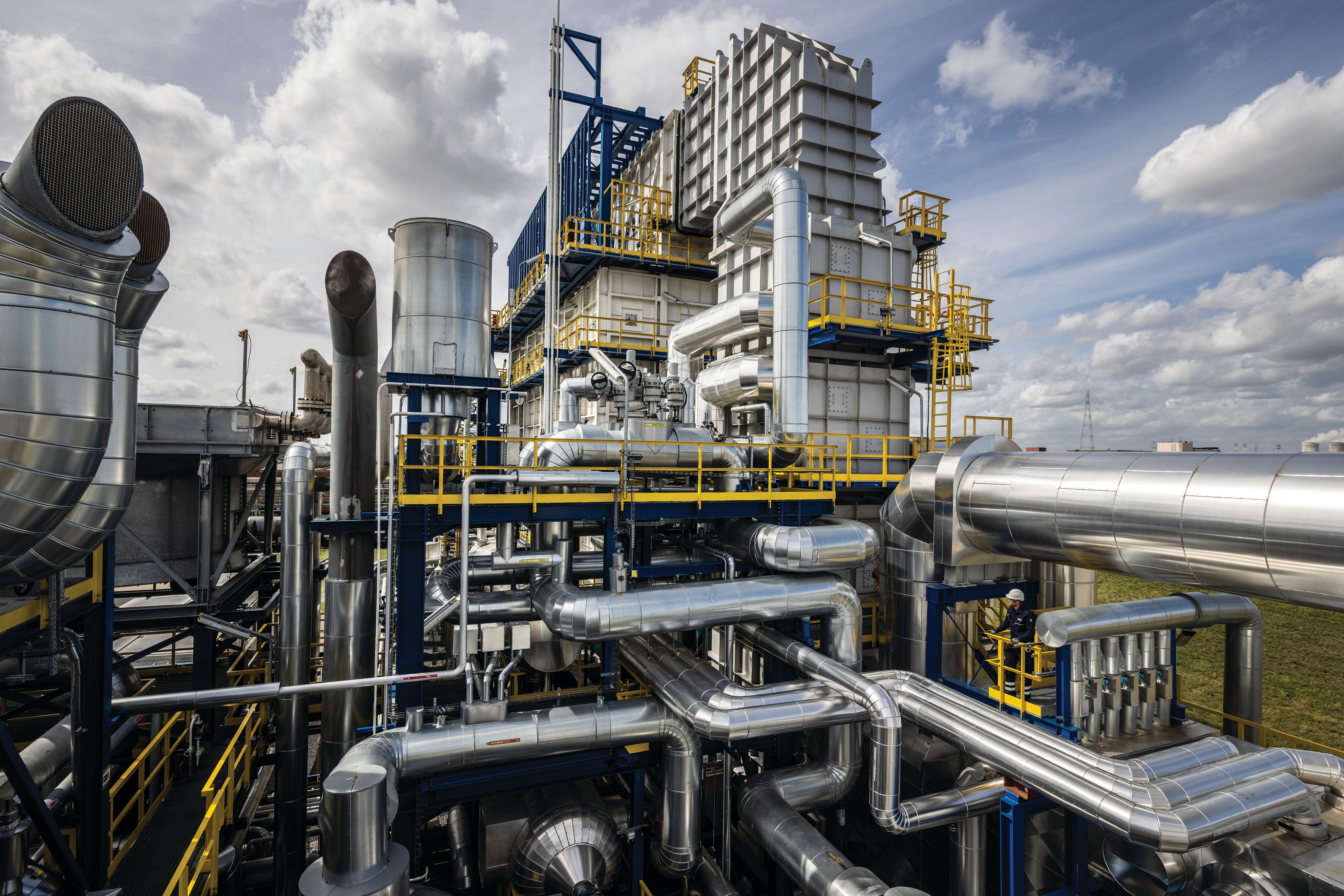
Figure 1. This plant in Antwerp, Belgium is the first to use Air Liquide's SMR-X process. The plant started up in 2021. Photo credit: Air Liquide
Figure 1. This plant in Antwerp, Belgium is the first to use Air Liquide's SMR-X process. The plant started up in 2021. Photo credit: Air Liquide
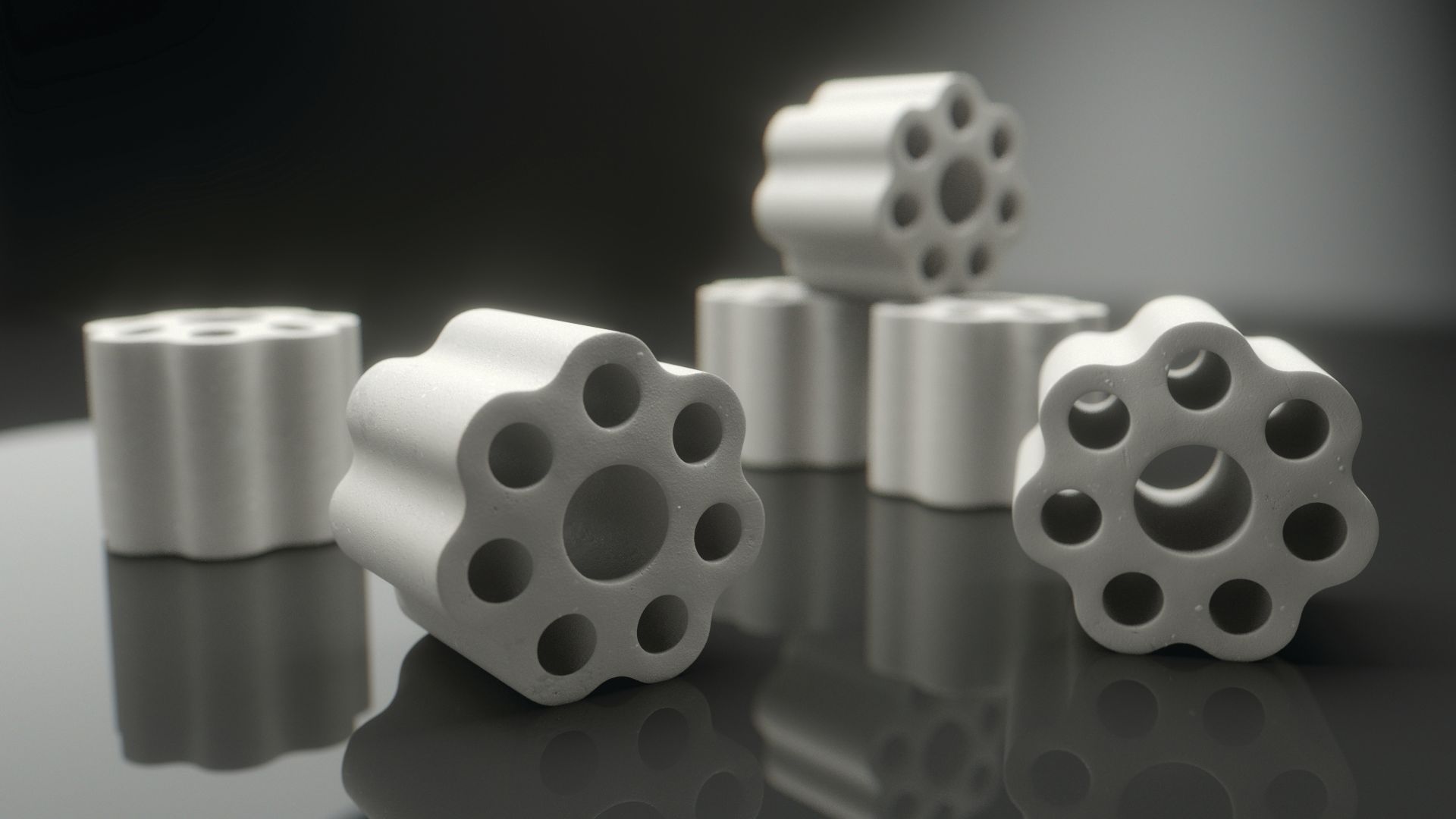
Figure 2. Clariant Catalysts' ReforMax LDP Plus SMR catalyst is said to provide a lower pressure drop than its predecessors. Photo credit: Clariant
Figure 2. Clariant Catalysts' ReforMax LDP Plus SMR catalyst is said to provide a lower pressure drop than its predecessors. Photo credit: Clariant
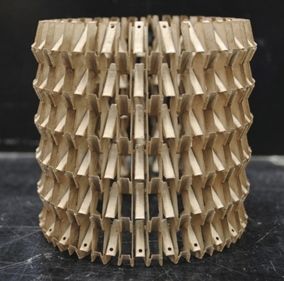
Figure 3. Pilot trials have sucessfully been completed on ZoneFlow's structured SMR catalyst. Photo credit: ZoneFlow Reactor Technologies
Figure 3. Pilot trials have sucessfully been completed on ZoneFlow's structured SMR catalyst. Photo credit: ZoneFlow Reactor Technologies
Improving SMR efficiencies
A first step for reducing CO2 emissions from SMR (or any process) is to improve the overall efficiency. One example of a new-generation SMR developed by Air Liquide Engineering & Construction (Frankfurt, Germany; www.engineering-airliquide.com) is SMR-X technology. SMR-X is a new type of reformer that produces H2 without excess steam, a byproduct that is declining in demand from users. Compared to conventional steam methane reforming, SMR-X features higher thermal efficiency at low steam co-production ratios and emits less CO2.
Some of the notable advantages of this next-generation reforming technology are increases in the overall yield of the H2 production process by roughly 5%, together with an intrinsic reduction of CO2 emissions (pre-capture) of 5%, making it a reforming process with a significantly reduced carbon footprint.
In combination with Air Liquide’s CO2-capture technologies, like Cryocap, the SMR-X technology route can provide the lowest carbon intensities and highest conversion efficiencies, making it a key pillar for the energy transition and decarbonization projects, unlocking attractive H2 routes for small- and medium-production capacities, says the company.
Air Liquide has been operating an industrial-scale plant (Figure 1) with this technology in Antwerp, Belgium since April 2021 and is said to be the first industrial-size greenfield recuperative-reforming plant in the world. The SMR-X technology is currently selected in many ongoing low-carbon H2 concept and technology studies, as well as projects advancing to the front-end engineering and design (FEED) stage.
Catalyst developments are also leading to improved SMR efficiencies. For example, BASF SE (Ludwigshafen, Germany; www.basf.com) developed the Synspire G1-110 catalyst, which reduces the steam demand for SMR (steam-to-carbon ratio down to 1.5) and maximizing the utilization of CO2. BASF’s new formulation is said to increase the coking resistance of the catalyst. Compared to standard SMR processes, the new catalyst can save up to 5% of operating costs, up to 3% of investment costs and decrease the CO2 emission of the process by up to 13% by reducing demand for fuel, steam and electricity, BASF says.
Last month, BASF began construction on its syngas plant at the Verbund site in Zhanjiang, China. Scheduled to start up in 2025, the new plant will produce syngas and H2 using “unique process concepts” to reduce CO2 emissions, compared to conventional syngas plants, the company says.
Meanwhile, Clariant (Pratteln, Switzerland; www.clariant.com) recently introduced its new generation of ReforMax LDP Plus catalyst formulation (Figure 2) with high activity and 20% pressure-drop reduction. The reduced pressure-drop, without penalty on performance, leads to lower overall compression needs for the H2 product gas and, hence appreciable energy savings, says Clariant Catalysts.
In addition, Technip Energies N.V. (T.EN; Zoetermeer, the Netherlands; www.technipenergies.com) and Clariant have introduced a new heat-recuperative reformer concept called enhanced annular reforming tube for hydrogen (EARTH, a tradename of T.EN) to improve the efficiency, capacity and sustainability of SMR. EARTH consists of an innovative concentric tubular structure and a tailor-made structured catalyst, which can be applied as a simple drop-in solution in existing or new reformer tubes. This unique setup results in superior heat recovery, higher throughput, and significantly lower pressure drop compared to conventional SMR.
EARTH can reduce CO2 emissions by up to 10% and increase capacity by up to 20% compared to conventional SMR. EARTH has been successfully implemented at Ak-Kim’s syngas plant in Turkey, resulting in fuel savings of 38%, higher radiant efficiency, lower steam export, and 20% lower CO2 emissions. With the addition of process and fluegas carbon capture and other synergistic design changes, such as increased reaction severity to maximize hydrocarbon conversion and supplemental hydrogen firing, a CO2 footprint reduction of more than 99% is achievable, says Clariant Catalysts.
Clariant also notes that, in the case of fluegas carbon capture, recuperative reforming brings significant advantages, because it directly translates into a smaller energy consumption and capital investment for the carbon-capture unit.
By investing in R&D and performing fundamental studies of the different carrier systems and their properties, Topsoe A/S (Lyngby, Denmark; www.topsoe.com) developed a new and more robust carrier system, which forms the basis for its Titan series of steam-reforming catalysts.
The Titan series of SMR catalysts, launched in 2020, is said to offer improved performance and longer catalyst lifetime thanks to the hibonite-rich composition. Prior to the launch, selected users experienced benefits of the Titan series, including 8% reduction in pressure-drop and 25% higher catalytic activity when compared to conventional catalysts available on the market.
The hibonite-rich composition of the catalysts provides a remarkable performance boost, which becomes especially evident after long operation. The addition of titanium promoters adds exceptional mechanical strength while a seven-hole cylindrical shape yields both a very low pressure drop and a high surface area. The catalyst’s high activity and low pressure-drop leads to lower operating costs, increased profit margins and reduced energy usage, Topsoe says.
Meanwhile, “there has been an increase and more volatility in natural gas prices,” says Ken Chlapik, market manager, Low Carbon Solutions, Johnson Matthey plc (London, U.K.; www.matthey.com). “This has increased the interest in pre-reforming applications, for which Johnson Matthey has developed Katalco 65-3X. This catalyst provides the same feedstock flexibility as other pre-reforming catalysts, enabling it to operate with a range of feeds, including ROG [refinery offgas], natural gas, LPGs [liquefied petroleum gas] and naphthas, however the catalyst uses new proprietary promotors to provide enhanced thermal stability. This enables the retention of a high catalyst activity deeper into the operating cycle, thereby enabling plants to confidently move to longer changeout cycles.”
Also, because of higher natural gas prices, investment in new large plants has been scaled back and hence a shift to smaller projects including the revamp of existing units, Chlapik continues. “Structured catalysts, such as Catacel SSR, provide a perfect option for a low-cost means to improved efficiency and intensification of existing SMR. The structured form of Catacel SSR provides a step change in performance, where fundamental science limits further improvements in the design of randomly packed pellets. The structured catalyst is higher in voidage and GSA [geometrical surface area], thus providing a higher activity, but at a lower pressure drop. The catalyst is also designed to actively disrupt the boundary layer at the inner of the reformer catalyst tube by jetting the process gas towards it, thus increasing the heat transfer coefficient. Together these features have provided our customers a 15% performance/throughput benefit, as well as a 15% saving in required firing fuel over a full catalyst lifecycle,” says Chlapik (Catacel SSR technology was a finalist for the 2019 Kirkpatrick Chemical Engineering Achievement Award; see Chem. Eng., January 2020, pp. 23–26).
In a related development, Honeywell UOP LLC (Des Plains, Ill.; uop.honeywell.com) and ZoneFlow Reactor Technologies, LLC (ZFRT; Windsor, Conn.; zoneflowtech.com) successfully conducted pilot plant testing of the ZoneFlow Reactor (Figure 3) in ZFRT’s large-scale pilot plant at Université Catholique de Louvain in Louvain-la-Neuve, Belgium. The near-commercial-level testing validated increased steam reforming capacity by at least 15% in terms of feed flow compared to conventional state-of-the-art pellets, with no higher methane slip and without increasing the maximum tube skin temperature or pressure drop. This increased production of hydrogen allows for the SMR to convert hydrocarbon feeds, such as natural gas or naphtha, and steam into syngas.
In 2021, the two companies signed a joint development agreement to grow and commercialize the ZoneFlow Reactor technology (Chem. Eng., December 2021, p. 5). This technology can provide a significant improvement in the productivity and cost-effectiveness of SMR for H2 and syngas production. “The combination of Honeywell’s domain expertise and ZoneFlow’s reactor technology is geared to provide high value creation for both new and existing SMR units. There are over 800 SMRs worldwide for H2 generation and a similar number employed for ammonia and methanol production. The successful testing can allow for significant capital savings for new steam methane reforming plants and higher productivity for existing plants,” says Ted Faiella, vice president and general manager of Equipment, Honeywell UOP Process Technologies. “As ZoneFlow’s reactors can increase hydrogen production with existing assets, this ready-now technology can play a major role in the energy transition as refineries look to burn hydrogen instead of natural gas to lower their carbon emissions.”
Blue hydrogen
In addition to improvement in energy efficiency, SMR technology providers have also been busy developing new concepts for making blue H2. These innovative engineering designs have made it possible to capture 95% or more of the CO2 from SMR units, compared to 60% achievable in older designs. As a result, “blue hydrogen is the most scalable and readily available low-carbon hydrogen technology on the market right now,” according to a recent podcast of the John Wood Group plc (Wood; Aberdeen, Scotland; www.woodplc.com).
Last year, Wood introduced its BlueSMR technology, which revolves around the company’s terrace-wall reformer, the core of its hydrogen technology, says Richard Spires, director of Technology Development at Wood. “With this technology, there is an even distribution and good control over how the heat reaches the reformer, and is the driver for improved efficiency,” he explains. “For the reaction of steam and methane to give syngas, SMR is the closest to the thermodynamic optimum,” he says.
A second point is integrating pre-combustion carbon capture with Wood’s gas-heated reactor (GHR) design. “When done properly, it is possible to achieve greater than 95% carbon capture.”
Wood offers three variants of its BlueSMR technology: BlueSMR, which introduces a number of upgrades including pre-combustion carbon capture, a GHR and a pre-reformer to significantly enhance unit performance. Hydrogen-rich gas firing will also displace the CO2 emissions from the combustion side of the process; BlueSMR+, which is similar to the previous option, but with an improved catalyst-tube geometry in the reforming furnace, potentially leading to reduced operating costs; BlueSMRp, which involves installing a separate, parallel H2-production unit with pre-combustion carbon capture to provide low-carbon fuel for the existing unit; and BlueSMRe, which integrates renewable electric power to decrease fuel consumption and CO2 production.
In the past two years, approximately 90% of Air Liquide’s SMR-based studies and projects requested from customers either included CO2 capture or were partly fed by biogenic feedstock, so low carbon, the company says. Air Liquide is involved in a multitude of SMR-based, low-carbon H2 studies, many of them moving towards FEED or project implementation phase.
One example is Air Liquide and TotalEnergies SE (Courbevoie, France; totalenergies.com) conversion of TotalEnergies’ Grandpuits site into a biorefinery to produce and valorize renewable and low-carbon H2. This H2-production unit (20,000 m.t./yr capacity) will partly use biogas from the biorefinery built by TotalEnergies, and also leverage Air Liquide’s Cryocap carbon-capture technology. These innovations will prevent emissions amounting to 150,000 metric tons of CO2 a year compared to current processes, the company says.
Autothermal reforming
Conventional SMR utilizes a fired heater to produce the energy that enables the reaction to take place. This fired heater combusts natural gas and creates a low-concentration stream of CO2 at atmospheric pressure. Although this can be captured, it requires large and expensive equipment and is harder to capture than CO2 at process pressure, explains JM’s Chlapik.
In comparison, autothermal reformer (ATR) technologies use oxygen to drive the reforming reaction instead of burning natural gas in a fired heater, Chlapik continues. This means in an ATR, there is not a separate low-concentration and low-pressure CO2 stream from natural gas combustion and CO2 can be removed from the process side at relatively high pressure and purity. This removal can be done with well-established CO2 separation technologies and requires significantly smaller and, therefore, cheaper equipment. “Process side removal can be done in a conventional SMR, but would only provide CO2 reductions of around 50–60% as it misses the additional combustion CO2, he says. “In an ATR-based flowsheet, this technique can enable CO2 reductions of up to 99%.”
This means to produce CCS-enabled blue hydrogen, where reducing the maximum amount of CO2 will be key to meeting stringent carbon-intensity standards, ATR-based flowsheets are a better fit than SMR. Johnson Matthey’s Advanced Reforming technologies include ATR and gas-heated reforming (GHR), which are optimal for low-carbon hydrogen production. In particular, Johnson Matthey’s LCH GHR-ATR flowsheet (Figure 4) is adept at producing hydrogen with very low CO2 emissions. The exceptional efficiency of this flowsheet means it uses 10% less natural gas per unit of hydrogen compared to an SMR and therefore produces less CO2 to be stored, which also enables a lower levelized cost of hydrogen, Chlapik says.
The high efficiency of the LCH process originates from the use of a GHR, which reduces the amount of combustion needed for the conversion of hydrocarbons and minimizes the size of thermal gradients in the flowsheet by transferring heat back into endothermic reforming reactions in the GHR rather than eroding high-grade energy by using it for steam production. By doing this, the fundamental energy efficiency of the flowsheet is maximized, Chlapik explains.
According to Air Liquide, ATR technology is particularly suitable for large capacities, whereby smaller capacities tend to favor SMR. The company sees clearly in the market a strong interest for ATR technology for these larger-scale projects, mainly driven by the following:
- Project capacities — often exceeding SMR single-train capacities
- Ease of decarbonization of ATR process (simpler decarbonization via a single pre-combustion capture unit)
- Large-scale low-carbon H2 and NH3 co-production schemes, where an ATR-based setup is the most competitive route
However, there is still a strong market demand for SMR-based H2 production technology (coupled with a strategy of decarbonization), mainly for: small- to mid-sized H2 production linked to hydrotreated vegetable oil (HVO)/ sustainable aviation fuel (SAF) production, with a recycle of biogenic feedstock to the SMR for green H2 production.
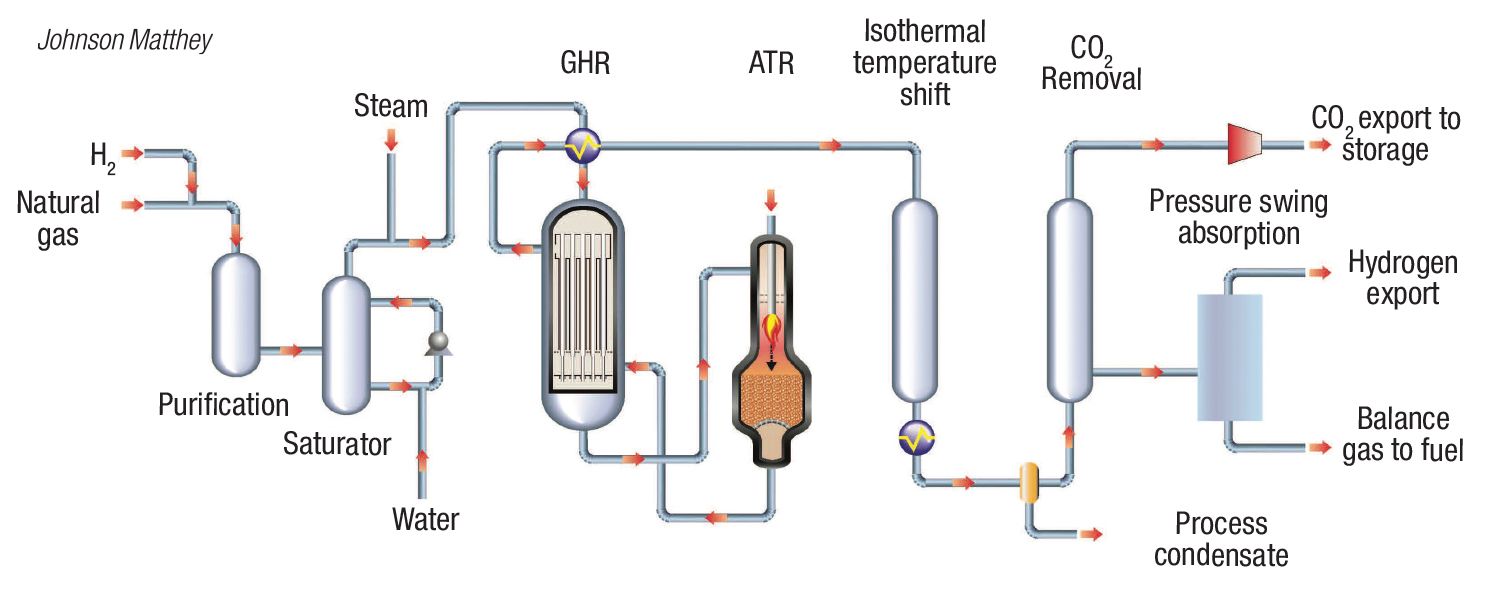
Figure 4. Johnson Matthey’s LCH GHR-ATR flowsheet is said to be adept at producing hydrogen with very low CO2 emissions. Photo credit: Johnson Matthey
Figure 4. Johnson Matthey’s LCH GHR-ATR flowsheet is said to be adept at producing hydrogen with very low CO2 emissions. Photo credit: Johnson Matthey
Other news
In July, KBR Inc. (Houston; www.kbr.com) and Air Liquide (Paris, France; www.airliquide.com) announced that they are now offering fully-integrated and flexible ATR technology for the production of low-carbon ammonia at mega scale. The offering combines KBR’s ammonia-synthesis technology with Air Liquide’s experience and proprietary ATR for large-scale syngas production.
When combined with carbon-capture technology, the KBR and Air Liquide technology solution will allow users to achieve “outstanding” energy efficiency and reliability, a simplified single-train production process, and up to 99% carbon capture in a highly integrated industrial facility.
Last month, Technip Energies, in partnership with Casale (Lugano, Switzerland; www.casale.ch), added Advanced ATR technology to Blue H2 by T.EN — the company’s suite of fully-integrated, low-carbon H2 solutions. It is part of Capture.Now, T.EN’s strategic platform for CCUS.
BlueH2 by T.EN was launched last year (Chem. Eng., December 2021, p. 5). Casale’s ATR combined with Technip Parallel Reformer (TPR) and carbon capture is a cost-effective way to produce low-carbon hydrogen at large-scale with optimized steam production.
ATR is a game-changing technology as it breaks the upper capacity limit of traditional hydrogen plants, which were economically constrained by the size of the SMR, and enables large-capacity, ultra-blue hydrogen production with up to 99% carbon-capture rate.
“Our partnership with Casale means that Technip Energies, as a top-tier player with advanced ATR and SMR technologies, can provide its clients with a fully integrated solution to meet their decarbonization and performance goals at any scale and type of hydrogen plant,” comments Loic Chapuis, senior vice president Gas & Low-Carbon Energies of Technip Energies.
In August, Lummus Technology LLC (Houston; www.lummustechnology.com) and Biohydrogen Technologies Ltd. (BHT; London, U.K.) established an agreement to develop and deploy advanced syngas reactor technology primarily for the production of blue H2.
Lummus’ Green Circle business unit will provide BHT its expertise in H2 and syngas plant design, reactor scaleup and design, and proprietary equipment supply. The technology is said to have the ability to capture more than 99% of the CO2 at pressure.
Gerald Ondrey