Hydrogen’s Growing Role for Clean Energy
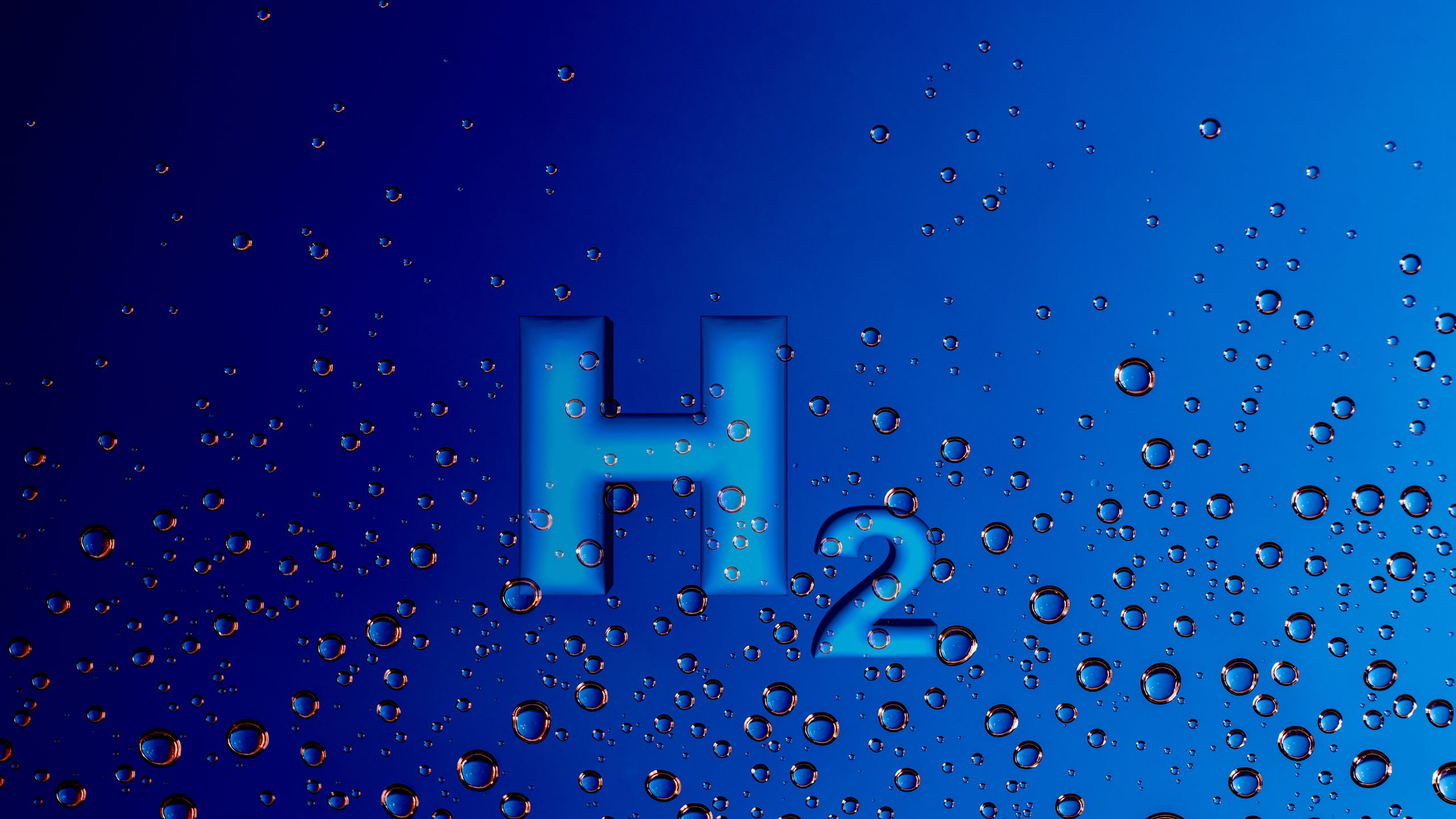
Hydrogen’s potential to play a significant role in the global search for clean, secure energy is gaining momentum as more industries and governments invest in projects toward that goal. Driven by concerns about climate change, investors as well as policy makers are pushing for aggressive carbon reductions. While hydrogen has received attention as a clean energy source in the past, the current momentum fueled by decarbonization targets and improved technologies shows greater promise for realizing its potential.
As a fuel, hydrogen offers the advantage of producing no carbon dioxide upon combustion. The bulk of the world’s hydrogen supply, however, is currently produced from fossil fuels and used industrially mostly for the petroleum refining and fertilizer industries. According to the International Energy Agency (IEA; The Future of Hydrogen: Seizing today’s opportunities, June 2019, www.iea.org), the production of hydrogen generates about 830 million metric tons per year of CO2 emissions. There is however, a surge in projects to create “green” hydrogen via electrolysis, from water.
Hydrogen produced by water electrolysis generates only hydrogen and oxygen, and therefore does not contribute to greenhouse gas emissions. Renewable energy sources such as wind and solar energy, can be used to generate hydrogen, making it an attractive option for storing the variable output from these sources. According to the IEA report, “The time is right to tap into hydrogen’s potential to play a key role in a clean, secure and affordable energy future”.
The following two articles examine some of the activities centered on advancing the production of “green” hydrogen as a next-generation fuel, as well as for industrial use. The first article focuses on electrolyzer technologies, while the second article offers a snapshot of activities around hydrogen production, its use in transportation and more.
- Dorothy Lozowski,
Editorial Director, Chemical Engineering and POWER
Electrolyzer Technologies for Green Hydrogen
Hydrogen is poised to be a cornerstone of the global energy transition
and its production via electrolysis has ignited demand for high-performance electrolyzer units
by Mary Page Bailey
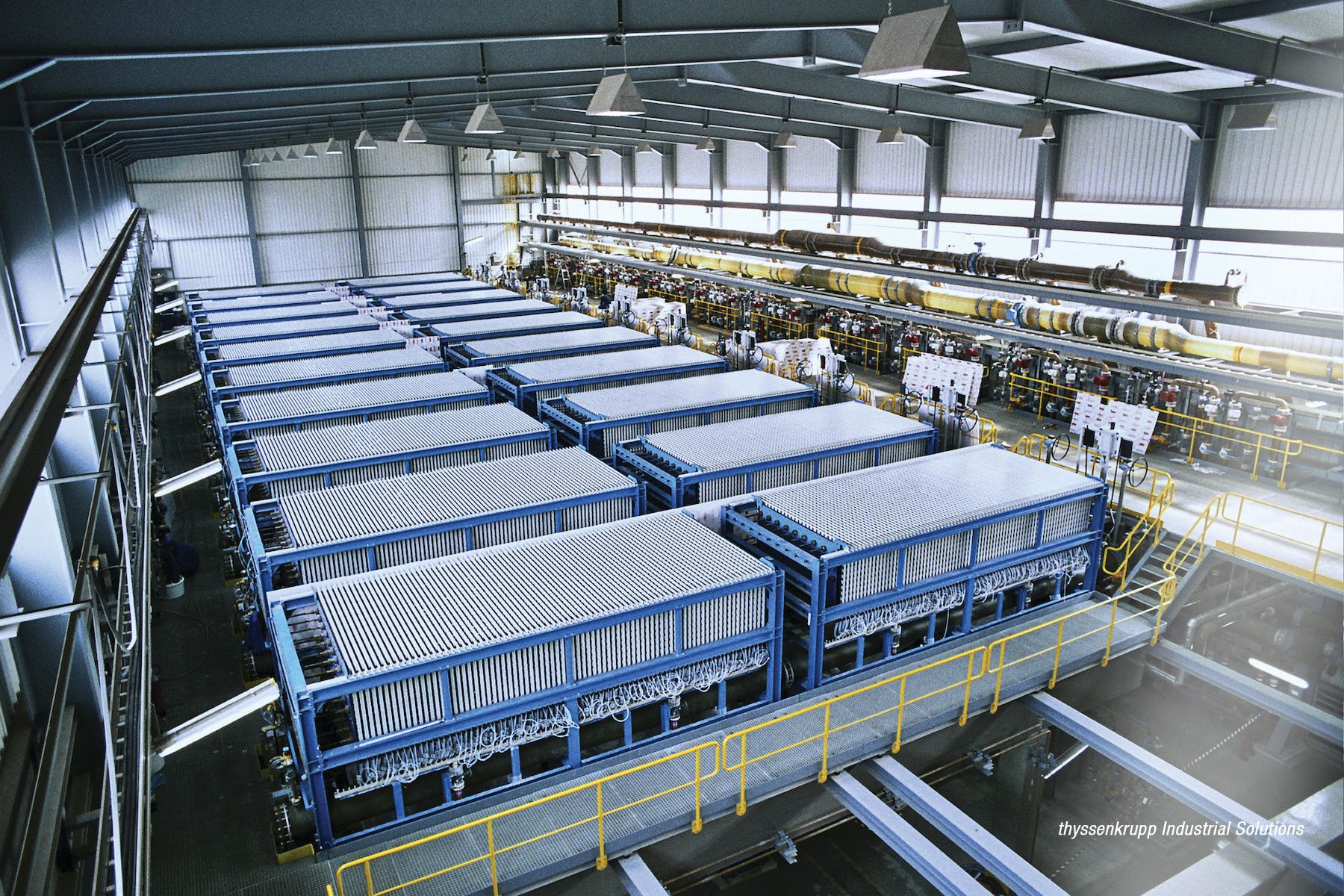
Technological and economic advances have brought hydrogen to the forefront of sustainability strategies in many industries, with end users hoping to capitalize on the promise of significantly reducing, or altogether eliminating,
CO2 emissions.

Much of the activity surrounding hydrogen today involves electrolyzers, which are modular processing units wherein electrical current is applied to split water molecules into hydrogen and oxygen. When powered by renewable electricity sources, such as wind or solar power, electrolyzers produce emissions-free, or “green” H2.
In recent years, production of electrolyzers has ramped up significantly to meet global demand for green H2. In June 2020, thyssenkrupp Industrial Solutions AG (Essen, Germany; www.thyssenkrupp-industrial-solutions.com), in partnership with De Nora S.p.A. (Milan, Italy; www.denora.com), expanded its manufacturing capacity for electrolyzer units (Figure 1). “We now have the capability to build electrolysis plants with an annual capacity of 1 gigawatt, and we will expand our capacities even further,” explains Christoph Noeres, head of energy storage and hydrogen at thyssenkrupp. These electrolyzers are offered as prefabricated skid-mounted modules (Figure 2), which can be combined to easily scale up production capacity. Scaling up the electrolyzer capacities, says Noeres, will help to realize economically promising value chains, not just for the large-scale production of green H2, but also for the subsequent manufacture of sustainable chemicals, such as ammonia and methanol. “Green H2 will play a central role in achieving greenhouse-gas neutrality, as well as the establishment of a closed-loop economy,” adds Noeres. On the horizon, thyssenkrupp is focusing its development projects on regions with favorable conditions for power-to-x applications. Earlier this year, the company announced that its electrolysis plants will be able to link to the German electricity market via E.ON’s virtual power plant, effectively acting as large-scale buffers to stabilize the power grid. For this ambitious milestone, the electrolyzers had to meet several load-change qualification criteria detailed in the grid codes of transmission operators, demonstrating that they exhibit sufficient response speed and flexibility to participate in the energy- balancing market.
There are two primary types of electrolyzers on the market — alkaline and proton-exchange membrane (PEM). Other emerging electrolysis technologies, which are still primarily in the development phase, include anion exchange membrane (AEM), solid-oxide electrolyzer cell (SOEC) and photoelectrochemical (PEC) water splitting. In an alkaline electrolyzer, the water is split into its constituents in the presence of a caustic electrolyte solution — frequently potassium hydroxide (KOH). The water-splitting reaction in a PEM electrolyzer gleans its electrolytes from a catalyst that is applied to a polymeric membrane.
Alkaline electrolysis is the more established technology, and alkaline electrolyzers typically are more affordable, but PEM electrolyzers bring some added value via a more rapid response to changes in power. Furthermore, PEMs are often seen as a safer option, since the membrane provides a physical barrier between the produced H2 and O2.
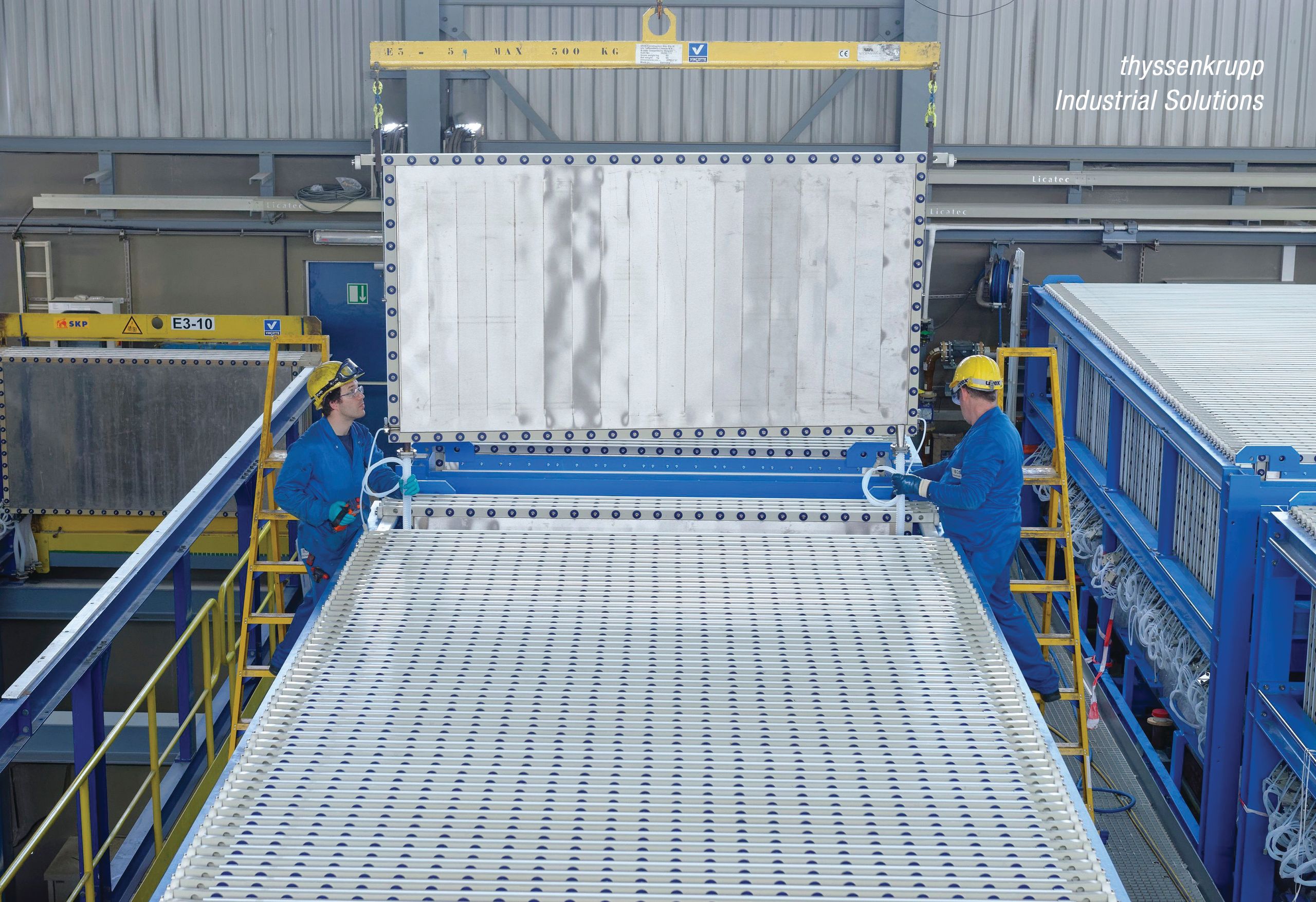
FIGURE 2. Their modular nature makes electrolyzers suitable for installations both large and small
FIGURE 2. Their modular nature makes electrolyzers suitable for installations both large and small

Although electrolyzers are not new, recent development work and industry trends have made them much more attractive when compared to conventional H2 production from natural gas via steam-methane reforming (SMR), says David Bow, senior vice president, corporate business development & strategy, Nel Hydrogen (Wallingford, Conn.; www.nelhydrogen.com). “The electrolyzer industry has dropped its capital costs by as much as 75% in the past 2 to 3 years, which has been driven mainly by market need for larger systems and innovation in system design and manufacturing,” explains Bow. The proliferation of low-cost renewable energy is also an enormous driving force, alongside pressure to meet corporate and government sustainability targets. “An SMR will produce 10 to 12 tons of CO2 per ton of H2 produced. Now, low-cost renewable electricity can be supplied to make green H2 with zero CO2 emissions,” says Bow. A major goal for electrolyzer providers is to achieve “fossil parity” — meaning the electroyzer can produce green H2 for the same price as using an SMR with natural gas (“gray” hydrogen).
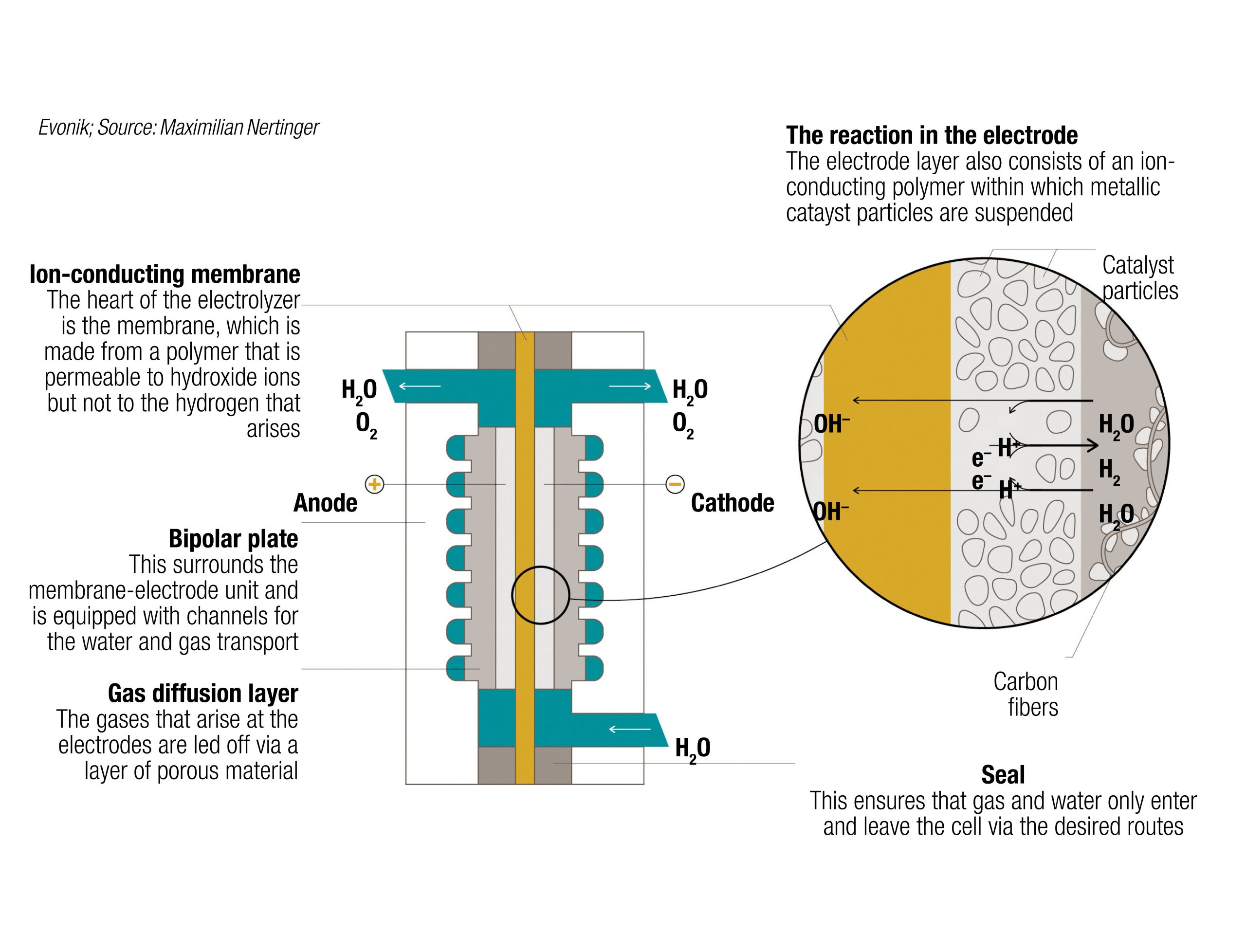
FIGURE 4. AEM electrolyzers are poised to combine the benefits of alkaline and PEM electrolyzers, which are currently the dominant technologies on the market
FIGURE 4. AEM electrolyzers are poised to combine the benefits of alkaline and PEM electrolyzers, which are currently the dominant technologies on the market
After achieving considerable cost reductions, Nel is now focusing more of its developmental efforts into improving electrolyzer efficiency and performance, including work to decrease the amount of precious metals (like platinum and iridium) in PEM catalysts, and advancements in electrode technology for alkaline systems.
Geography is an important factor when comparing the economy of SMRs with electrolyzers. In some areas, where natural gas feedstock for SMR units is scarce, natural gas needs to be shipped; or H2 transported via tube trailers or in liquid form in tank trucks, which is very inefficient and CO2-intensive. “Since H2 is such a light molecule, a full tube trailer truck can carry only around 350 kg. Furthermore, there are considerable losses when storing hydrogen as a liquid, since it vents off as temperatures change,” explains Bow. This makes onsite generation of H2 a much more attractive proposition for major hydrogen consumers, such as ammonia plants, methanol plants and petroleum refineries.
While SMRs are by far the dominant technology, many chemical processing sites are turning to electrolyzers to help augment SMR capacity and increase plant flexibility, since electrolyzers can operate efficiently over a large turndown ratio and are readily scalable. Bow mentions an example of a large chemical manufacturer who was purchasing H2 from a nearby SMR unit and found that their demand had outgrown the SMR’s capacity. “They looked at buying another SMR unit versus transitioning to electrolyzers or transporting liquid H2 in tanker trucks and found that electrolyzers in series provide more efficiency at a lower cost,” says Bow.
Nel has undertaken a variety of pilot-scale tests for different H2 applications, helping sites to transition from gray to green H2. “Many, if not all, major ammonia producers are looking at some level of electrolysis testing. We have a wind-to-ammonia project in Minnesota that has been running for several years and many more in the pipeline. We’ve also sold a number of large-scale alkaline electrolyzers for production of ethylene and sugar alcohols, both of which consume large amounts of H2 in the process,” says Bow.
Nel Hydrogen is one of several recipients of funding under the H2@Scale initiative funded by the U.S. Department of Energy (DOE; Washington, D.C.; www.doe.gov), through the Office of Energy Efficiency and Renewable Energy’s (EERE) Hydrogen and Fuel Cell Technologies Office (HFTO). In July, $64 million in funding was awarded to 18 projects supporting H2@Scale’s goals of advancing the U.S. hydrogen economy. Nearly $15 million of the most recent round of funding went to projects focused specifically on manufacturing electrolyzers. “An advantage of electrolyzers is their suitability with intermittent renewable-power sources, such as wind and solar. Instead of curtailing power, electrolyzers can be used to make H2 for either energy storage or for other value-added end-use applications, such as manufacturing chemicals or steel,” explains HFTO director Sunita Satyapal.
For electrolyzers, H2@Scale’s main goals involve improving efficiency and durability while reducing overall costs. As electrolyzer technologies have progressed, Satyapal points out a trend toward more holistic and collaborative development projects. “Instead of looking at specific components, like catalysts or membranes, much of the current work deals with the integration of materials and manufacturing processes, and how we might be able to integrate them to be manufacturable at scale,” she says. “An example of a unique area we have been funding is quality-control methods. Ideally, if we are going to ramp up electrolyzers to gigawatt scale, the components wouldn’t be manufactured in batch processes, so we are looking at higher-throughput continuous processes, such as roll-to-roll, as well as high-speed inspection over large-area components to find defects that could impact durability.” Some of the other major areas of development include: membrane-coating techniques and simplifying membrane fabrication; optimizing the porous transport layer; and reducing precious-metals content. In addition, H2@Scale is working on two first-of-their-kind nuclear-to-H2 projects in the U.S.
H2@Scale is focusing on multiple hydrogen production, storage, distribution and utilization needs, including PEM electrolyzers, which are gaining traction in the market, but still have potential for major cost reductions. Feedwater quality is another emerging area of research for the project, says Satyapal. “We have a few early-stage projects investigating the ability to use dirty water or salt water, as opposed to requiring high-purity water for electrolysis,” she adds. “We also have a first-of-its-kind project in the U.S. where we are producing H2 with an electrolyzer and using a biological system to make renewable methane with H2 and CO2,” says Satyapal.
Synergy with natural gas is another area with significant interest, specifically in blending H2 and natural gas, with the potential to inject hydrogen into natural-gas pipelines. However, with H2 blending, materials compatibility can be a major concern depending on materials used, and much research activity involves the effects of hydrogen on embrittlement and its impact on both metals and polymers, as addressed by DOE’s H-Mat consortium.
A significant milestone in H2 blending took place in July 2020, when Baker Hughes (Houston; www.bakerhughes.com) and Snam (San Donato Milanese, Italy; www.snam.it) completed testing of the world’s first “hybrid” hydrogen turbine designed for a gas network, with the ultimate goal of injecting H2 blended with natural gas into Snam’s current transmission infrastructure.
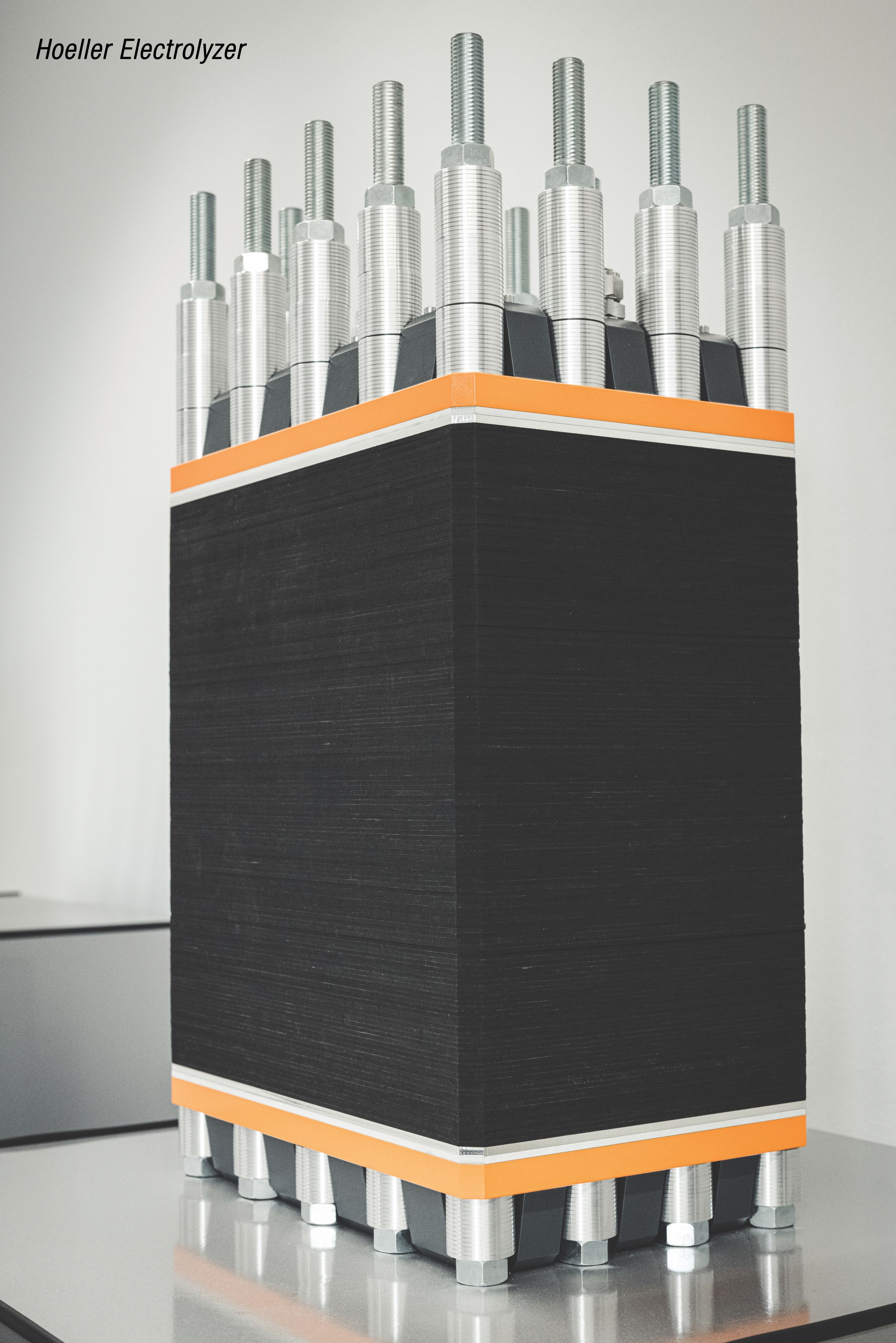
FIGURE 3. These compact electrolyzer units are designed for installation in challenging locations, such as the head of a wind turbine, for streamlined energy storage
FIGURE 3. These compact electrolyzer units are designed for installation in challenging locations, such as the head of a wind turbine, for streamlined energy storage

Hoeller Electrolyzer GmbH (Wismar, Germany; www.hoeller-electrolyzer.com) has developed an optimized cell-surface technology for compact PEM electrolyzers (Figure 3) that reduces the amount of precious metals required and increases operating pressure. Hoeller is designing its PEM cell stacks with demanding installations in mind, such as integrating the stack directly into the head of a wind turbine. “The key advantage of PEM electrolysis is that the H2 production almost instantaneously changes with the energy provided, so processes with a changing need for H2 are an ideal match,” says Matthias Kramer, chief financial officer at Hoeller. According to Hoeller, its stacks can handle load changes from 0 to 100% of nominal load within seconds. While PEM is versatile in the face of shifting demand, Kramer also emphasizes its ability to operate continuously. Furthermore, the stack is capable of pressurization to 50 bars or higher, making direct storage more convenient. Hoeller’s proprietary PEM technology was demonstrated in a proof-of-concept at the Fraunhofer Institute for Solar Energy Systems (ISE; Freiburg im Breisgau, Germany; www.ise.fraunhofer.de), and Kramer says that the company expects to install a prototype unit by the end of 2020. Discussions are also in place regarding a pilot project for the new PEM stacks at a wind farm in Schleswig-Holstein, Germany.
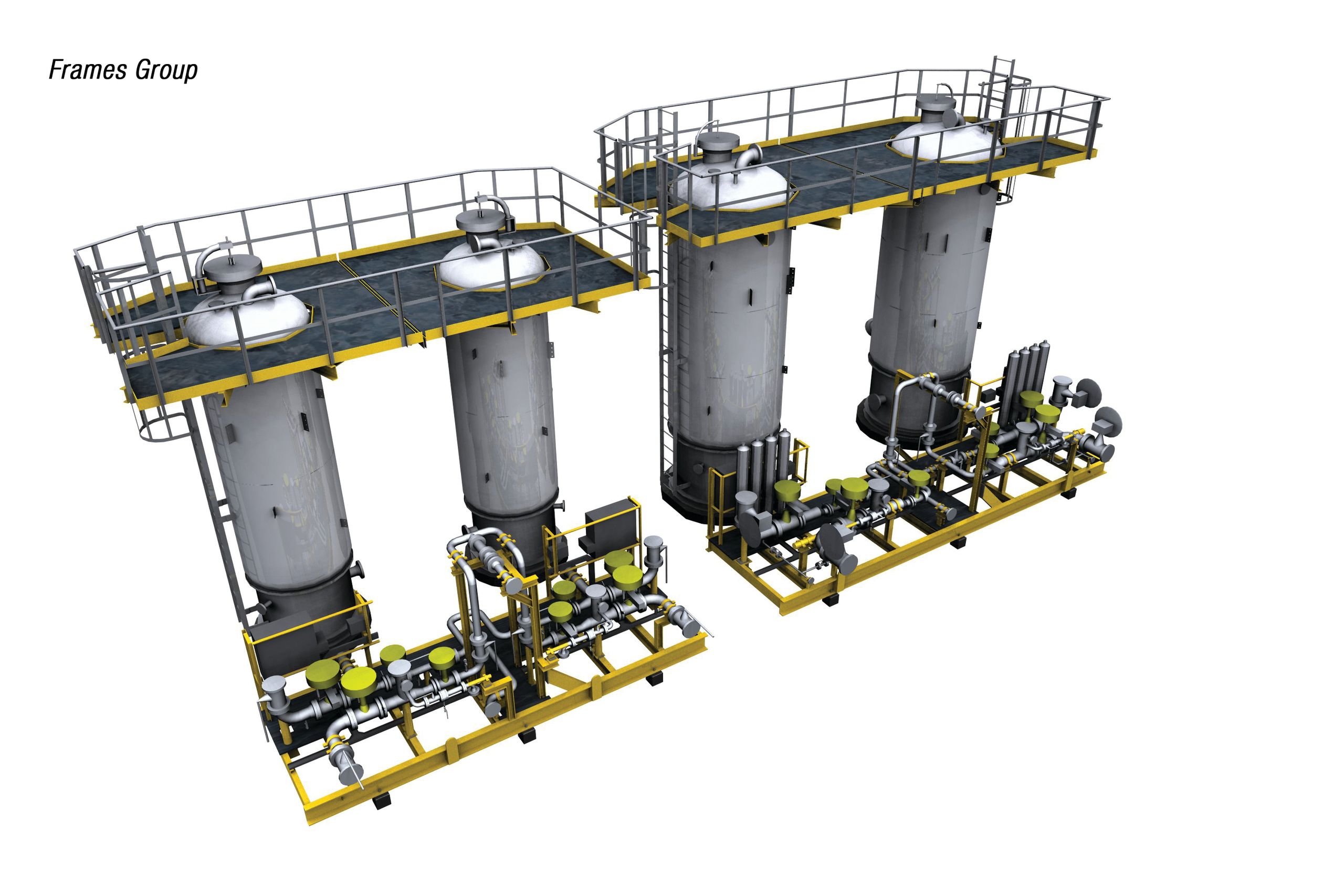
FIGURE 5. A molecular sieve unit may be installed downstream of an electrolyzer for dehydration purposes
FIGURE 5. A molecular sieve unit may be installed downstream of an electrolyzer for dehydration purposes
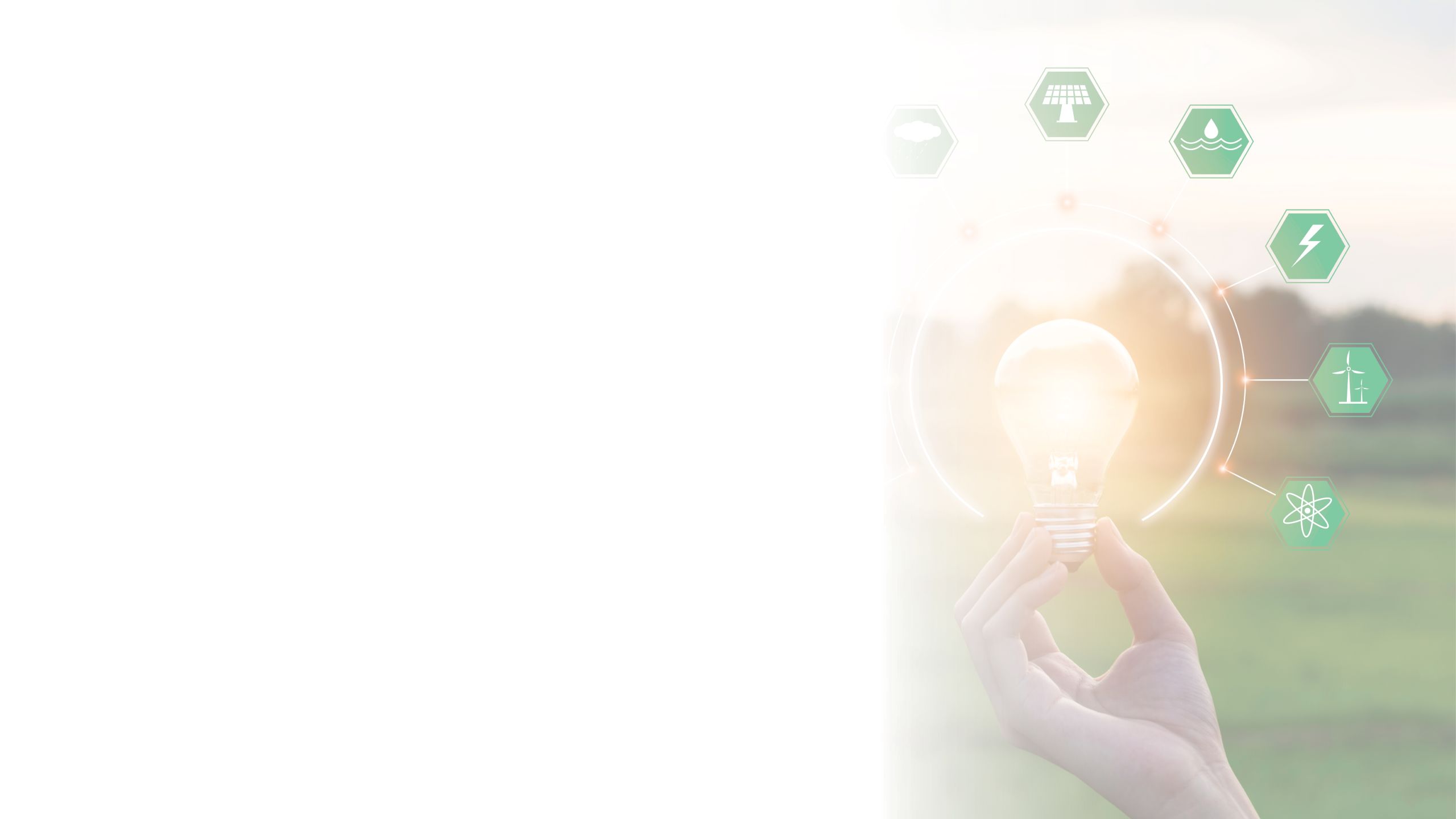
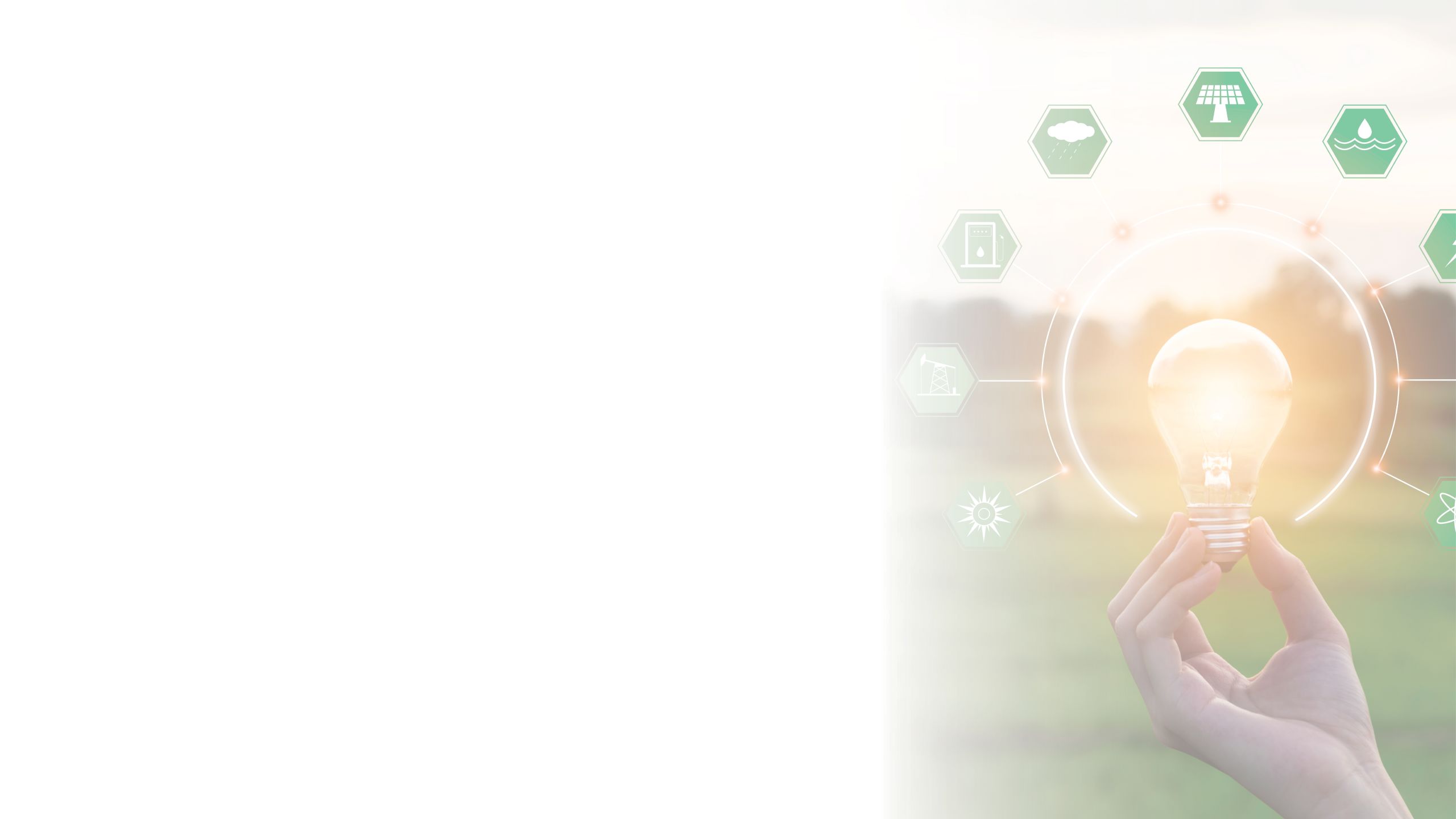
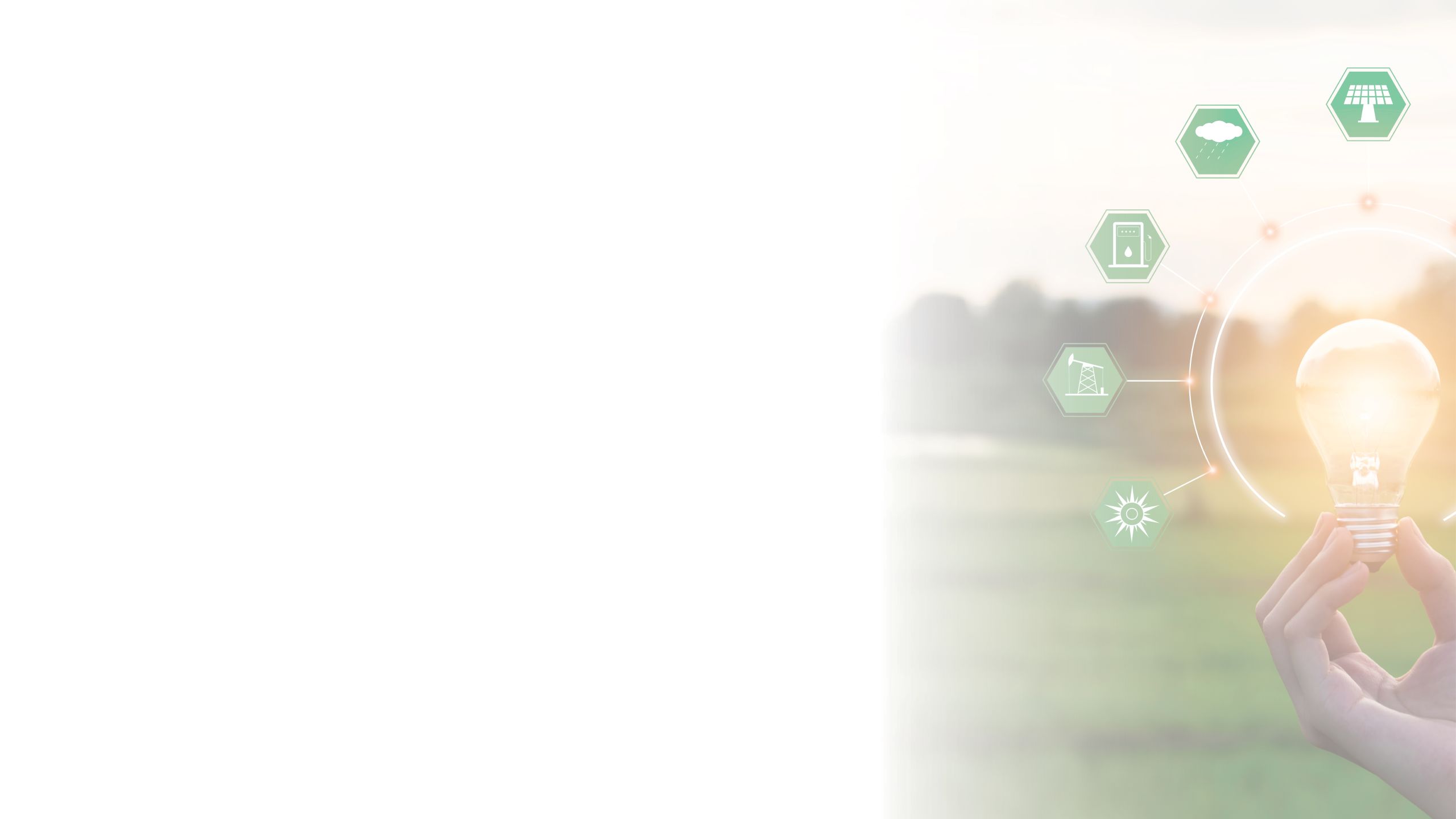

One emerging technology for H2 production is anion-exchange membrane (AEM) electrolysis (Figure 4). AEM is somewhat of a hybrid solution combining the benefits of PEM and traditional diaphragm-based alkaline electrolysis, explains Oliver Conradi, who specializes in membrane research at Evonik Industries AG (Essen, Germany; www.evonik.com). “Alkaline electrolysis obviously involves very basic conditions, while PEM involves an acidic environment. These respective pH values require certain materials. In alkaline conditions, you can use cheaper materials, such as stainless steel and nickel, whereas with PEM, you must use platinum or other precious metals for the catalyst, and the electrochemical cell must be based on titanium, so the investment cost for PEM is much higher,” explains Conradi. However, PEM systems overcome some of the fundamental limitations of traditional alkaline electrolysis — due to the specific cell design in alkaline systems, current density and efficiency are limited, and it is more difficult to pressurize an alkaline system, meaning that an additional compression step is typically required. “In PEM units, the dense membrane makes it easier to pressurize the whole system. With AEM, you can fundamentally combine the advantages of both state-of-the-art technologies, while you compensate for their drawbacks,” says Conradi, noting that the primary hurdle in developing an effective AEM system is developing a suitable polymeric membrane material that can withstand alkaline conditions.
A particular area of focus is on the cationic moiety, which is responsible for transporting the hydroxide ions from the cathode to the anode. In addition to stability in an alkaline environment, the polymer must also provide high ion conductivity and stability under pressurized electrolyzer conditions. Inspired by an existing membrane technology for gas separation, Evonik has developed a new polymer chemistry featuring a proprietary ion-conducting cationic moiety. As part of the AEM-focused Channel consortium, Evonik is expanding production of the polymer and also scaling up membrane fabrication on a pilot coating line. “The consortium is building an AEM electrolyzer to demonstrate that the membrane and other components work under challenging conditions,” explains Conradi. The group’s first AEM demonstrator unit is at the laboratory scale, where test protocols are being run to reflect real-world conditions. “The next milestones will be proving system reliability and scaling up the stack sizes, while also scaling up membrane processing,” he continues.
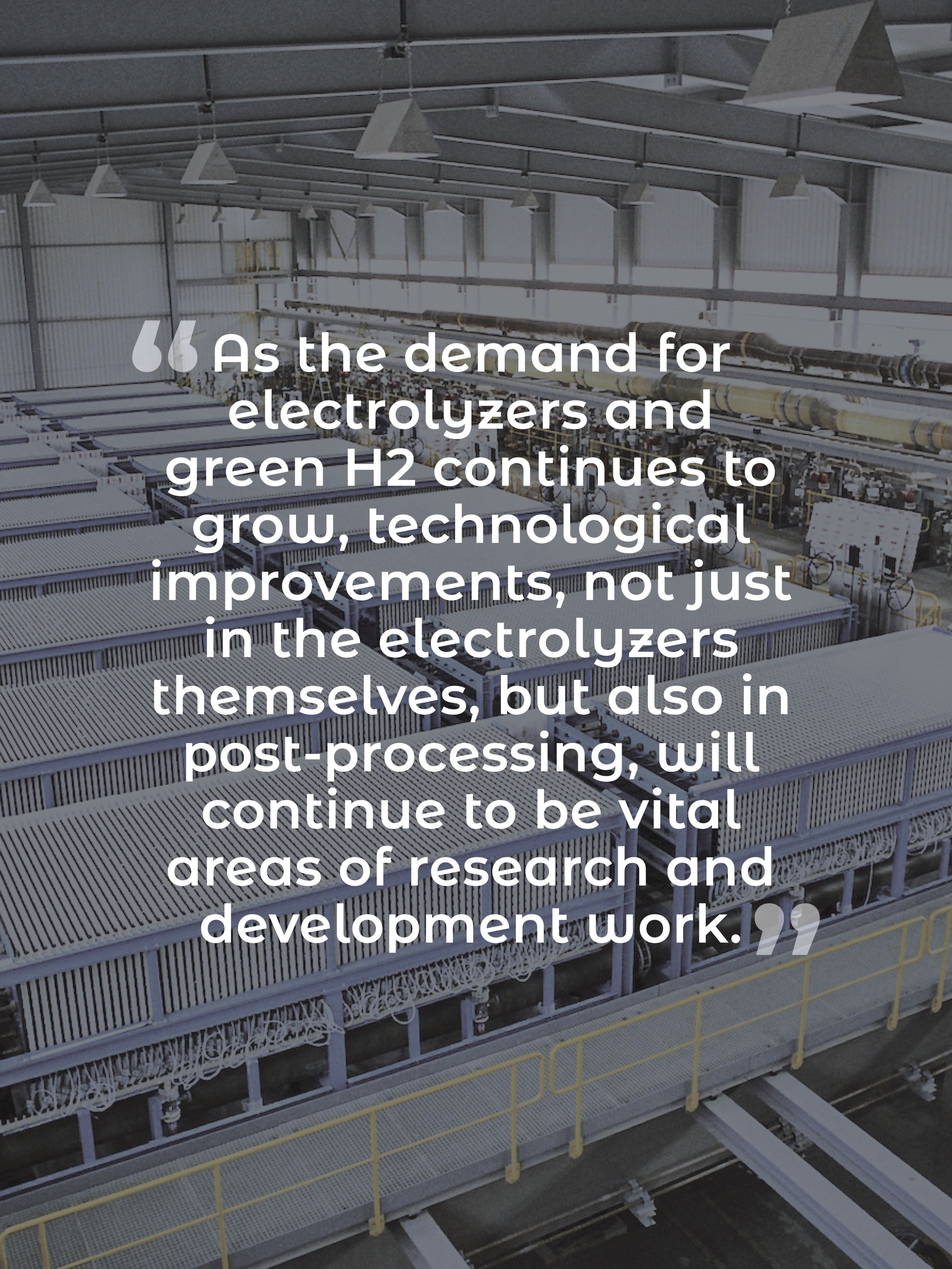

Although electrolyzers have made strides in efficiency and cost, the produced H2 still often requires post-processing steps, such as compression, dehydration or purification. “Electrolysis stacks usually do not produce hydrogen that is directly suitable for use. If you want to store, distribute or utilize the produced hydrogen, contaminants need to be removed,” says Jordi Zonneveld, manager of the hydrogen portfolio at Frames Group (Alphen aan den Rijn, the Netherlands; www.frames-group.com). “Since PEM technology uses only ultra-pure water, the only contaminant is water, and potentially a very small amount of oxygen. Alkaline electrolysis uses a KOH solution as the process fluid, and therefore traces of KOH in the produced hydrogen need to be removed, as well.”
Depending on the gas flow and purity requirements, there are several steps that may be required to prepare H2 for its end-use applications. For instance, says Zonneveld, knock-out drums with demisting internals and optional gas-cooling equipment are generally used as a first step to bring hydrogen purity up to 99.9%. Then, if higher purity is required, a molecular-sieve unit (Figure 5) may be required. He also mentions that dehydration using triethylene glycol — a common technology for natural-gas processing — has shown potential for H2 purification, but there have not yet been any large-scale H2 applications.
Compression of H2 also introduces unique challenges. “H2 has a very high energy density per mass, but a very low density, so compressors are needed downstream of electrolyzers to compress the H2 for efficient storage and transportation,” says Stefanie Peters, managing partner at Neuman & Esser Group (NEA; Übach-Palenberg, Germany; www.neuman-esser.de). The low molecular weight of H2 also poses issues. “Turbomachinery faces significant problems in capturing the H2 in the compression chamber, and only positive-displacement machinery like piston and diaphragm compressors are suitable for efficient compression to required H2 discharge pressures,” add Peters. For instance, dry-running piston compressors can achieve discharge pressures up to 300 bar. When equipped with lubricated cylinders, the discharge pressures are potentially as high as 700 bar, but this option introduces trace amounts of oil contamination, so in cases where no contamination is acceptable, oil-free diaphragm compressors are the preferred high-pressure option, as they can achieve more than 5,000 bar discharge pressure.
As the demand for electrolyzers and green H2 continues to grow, technological improvements, not just in the electrolyzers themselves, but also in post-processing, will continue to be vital areas of research and development work.
Driving Toward a Hydrogen-based Economy
Technology developments are progressing towards large-scale production of ‘green’ hydrogen, along with improved methods for storage and transportation
by Paul Grad
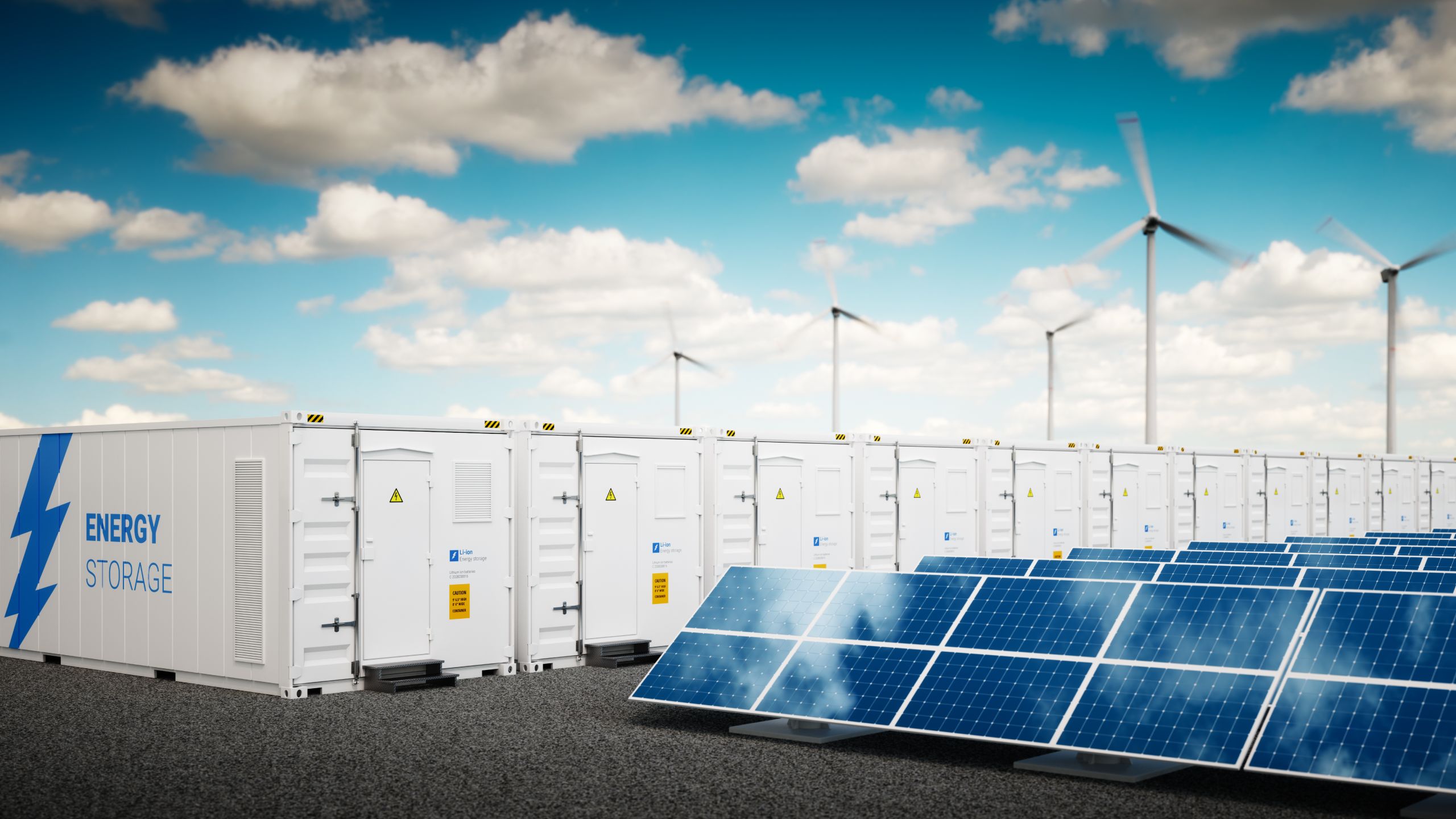
The world has an important opportunity to tap into hydrogen’s vast potential to become a critical part of a more sustainable and secure energy future,” according to an in-depth study launched by the International Energy Agency (IEA; Paris, France; www.iea. org) on the occasion of the meeting of G20 energy and environment ministers in Karuizawa, Japan, on June 15–16, 2019.
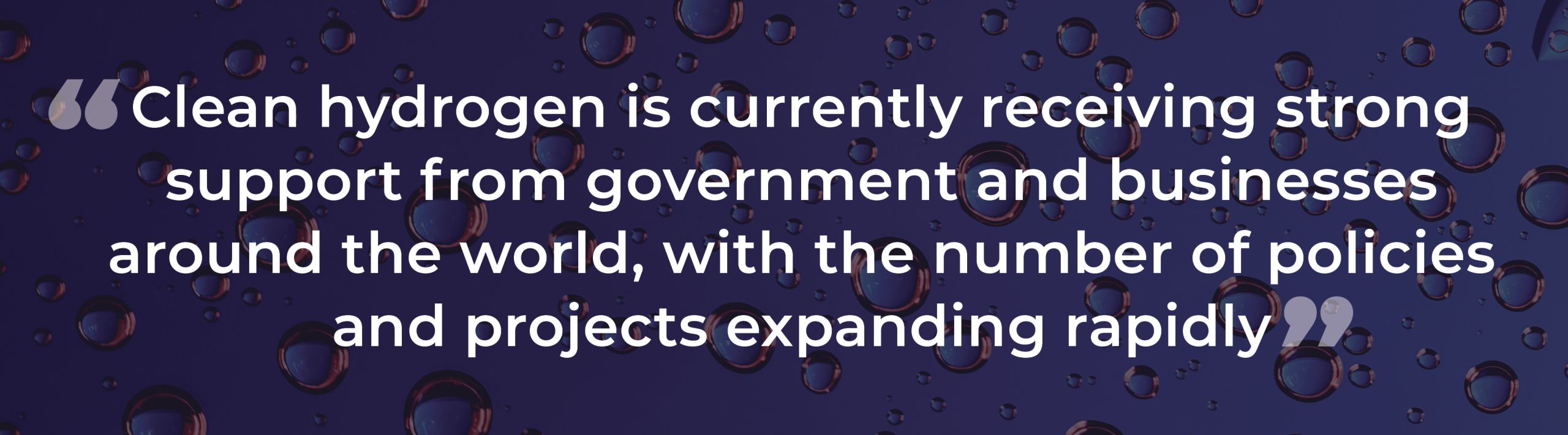
“Clean hydrogen is currently receiving strong support from government and businesses around the world, with the number of policies and projects expanding rapidly,” the study says. Titled The Future of Hydrogen: Seizing Today’s Opportunities, and launched by the IEA’s executive director Fatih Birol, and Japan’s minister of economy, trade and industry Hiroshige Seko, the study says hydrogen offers ways to decarbonize a range of sectors, including chemicals manufacturing and iron and steel production, and it can be transformed into fuels for cars, trucks, trains, ships and aircraft.
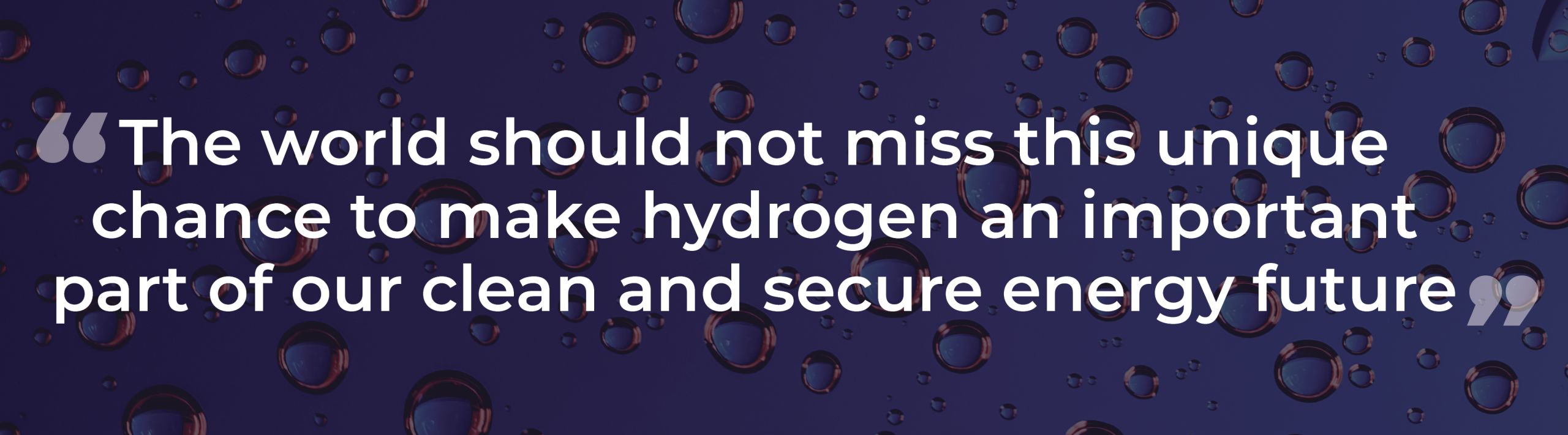
“The world should not miss this unique chance to make hydrogen an important part of our clean and secure energy future,” Birol says.
There are, however, people who believe H2 fuel cells will never be widely used, because they present high costs and low efficiencies when compared with batteries, such as lithium-ion batteries (LIBs), and it would take too long to overcome the technical issues involved. Nevertheless, efforts are ongoing to improve the technology and economics of a hydrogen-based economy.

As a fuel system for cars, buses, trains and so on, hydrogen is stored in a tank within the vehicle. H2 is fed to a fuel cell, which produces electricity for an electric motor that moves the vehicle. Unlike fossil fuels, hydrogen combustion produces no CO2 or other pollutants — just water vapor.
As far as a fuel system for motor cars is concerned, the main contender of H2 fuel cells is LIBs. Today most electric vehicles use batteries, often based on Li-ion or lead-acid chemistry. Each individual fuel cell produces low currents and voltages and, like LIBs, the cells need to be stacked together to reach the target voltage and maximum current required by the vehicle.
One of the advantages of H2 used in fuel cells is that it has an energy-to-weight ratio (specific energy) much greater than that of LIBs. The specific energy of LIBs is 0.36 to 0.875 MJ/kg, and the specific energy of hydrogen is 120 to 142 MJ/ kg. H2 in fuel cells thus permits much greater range while being lighter and occupying smaller volumes. Another major advantage of H2 fuel cells is that they can be recharged in a few minutes. In contrast, full charge times for LIB electric vehicles is typically measured in hours.
However, H2 also entails serious drawbacks. One of them is that it combines well with other elements and therefore has to be isolated, before being usable as fuel, by means of processes that are expensive and energy consuming. Also, storing H2 is expensive and energy intensive, either when it is stored as a gas at high pressure, or even more so, as a liquid at cryogenic temperatures. H2, which is also highly flammable, is difficult, dangerous and expensive to produce, store and transport.
In spite of the problems presented by H2 fuel cells, and in spite of the negative predictions by some experts, a large number of projects are ongoing and a significant amount of R&D dollars are being invested in H2 fuel cells around the world. There are already many vehicles running on hydrogen fuel cells, including motor cars, buses and trains, although they have not yet attained wide market acceptance. According to the IEA, there are currently about 11,200 H2-powered cars on the roads worldwide.
The oldest hydrogen cars commercially available in selected markets are: the Toyota Mirai, the Hyundai Nexo and the Honda Clarity. In 2013 the Hyundai Tucson fuel-cell electric vehicle (FCEV) was the first commercially mass-produced H2 FCEV in the world. It had a range of nearly 600 km. Hyundai Nexo (Figure 1) succeeded it in 2018. Toyota launched its Mirai at the end of 2014. It has a range of about 500 km and it takes about 5 min to refill its H2 tank.
Although many automobile companies have introduced demonstration models in limited numbers, many of those companies have switched to battery electric vehicles.
Late last year, the world’s first passenger train powered by H2 fuel cells began operating in Germany (Figure 2). Called Coradia iLint, it was developed by Alstom (Paris, France; www. alstom.com). The train is capable of maximum speeds of 140 km/h.
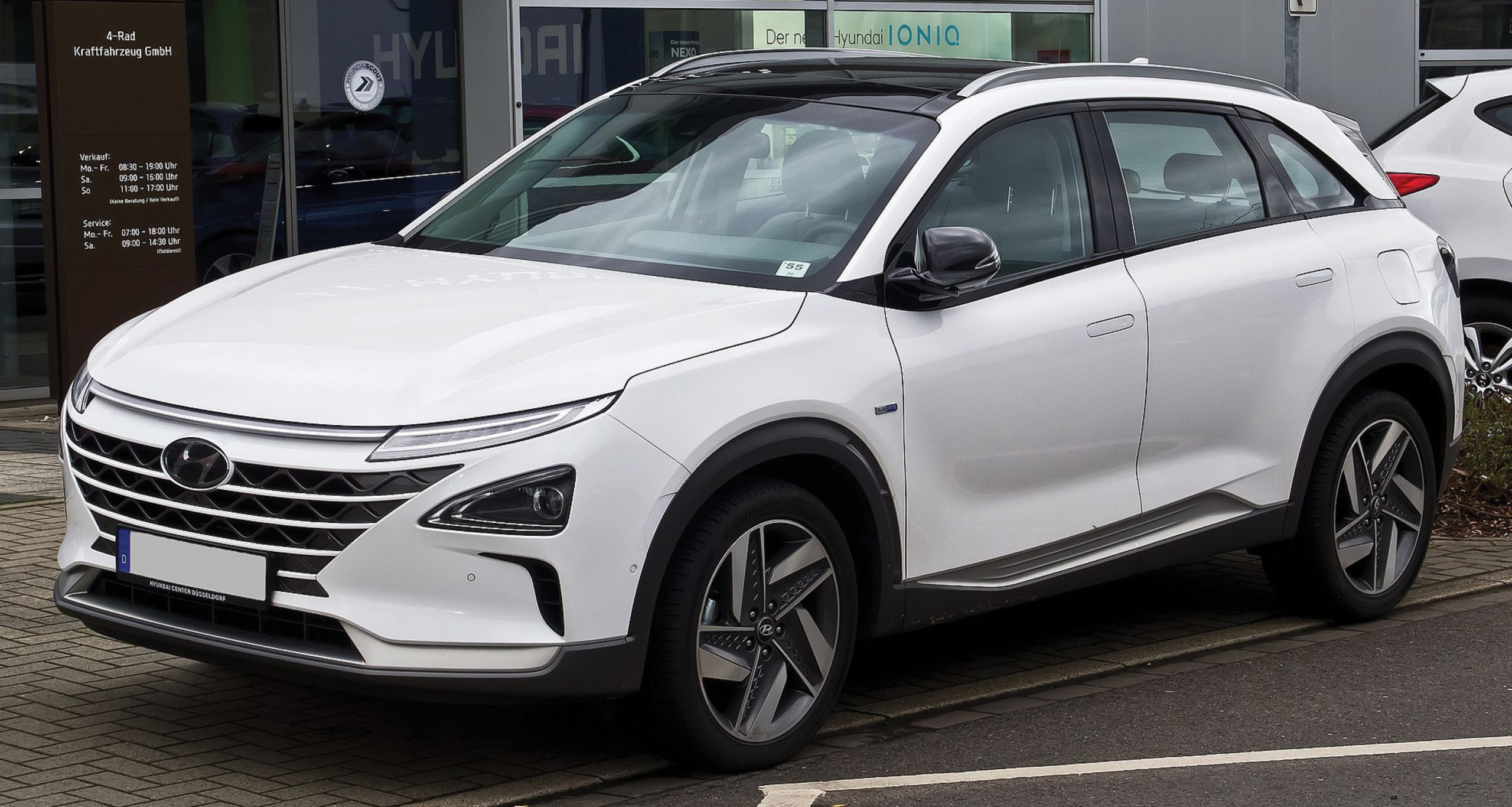
FIGURE 1. One of the latest hydrogen-fueled automobiles is the Hyundai Nexo
FIGURE 1. One of the latest hydrogen-fueled automobiles is the Hyundai Nexo
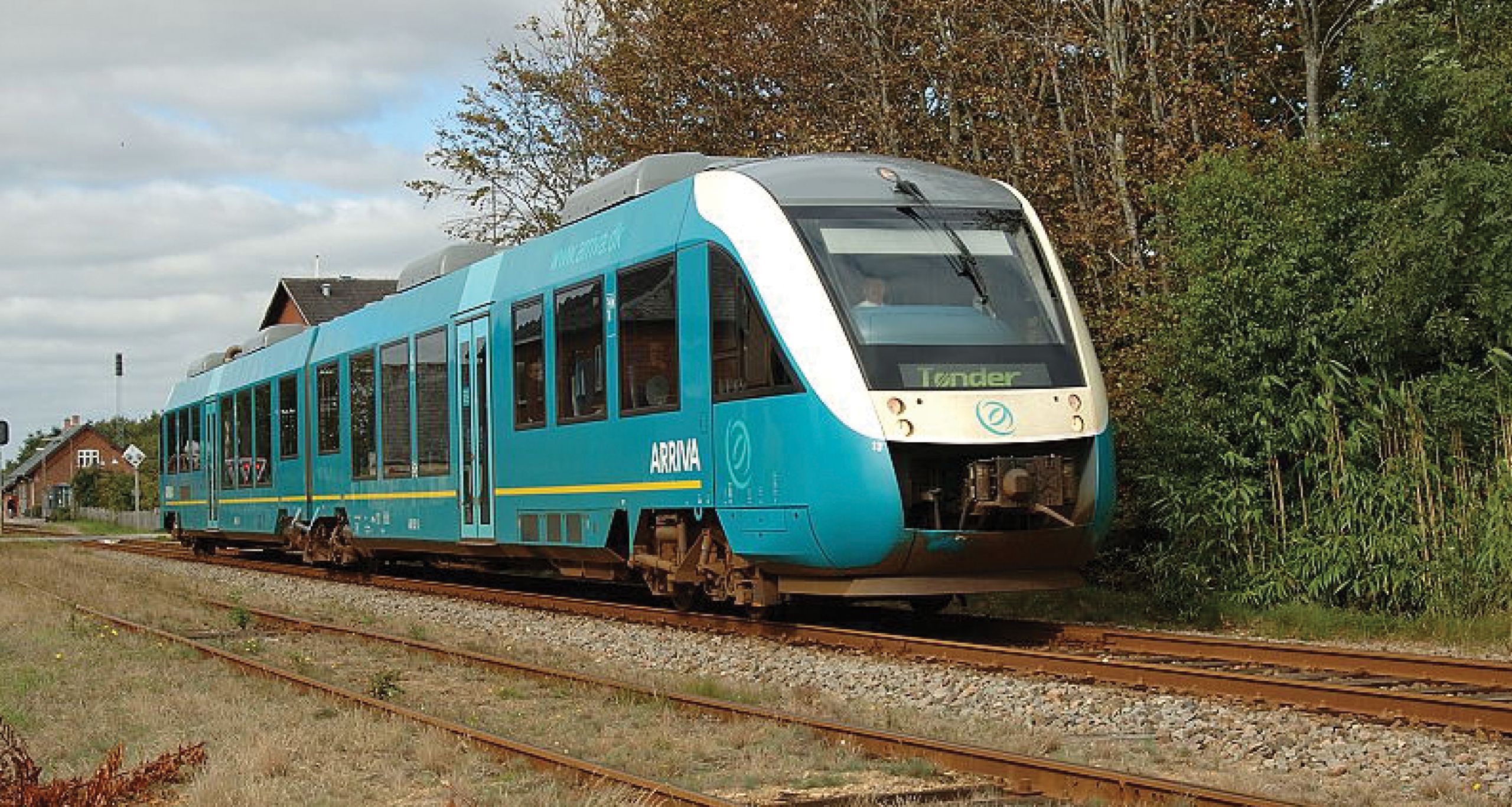
FIGURE 2. The world's first hydrogen-fueled passenger train started operating last September in Lower Saxony, Germany
FIGURE 2. The world's first hydrogen-fueled passenger train started operating last September in Lower Saxony, Germany
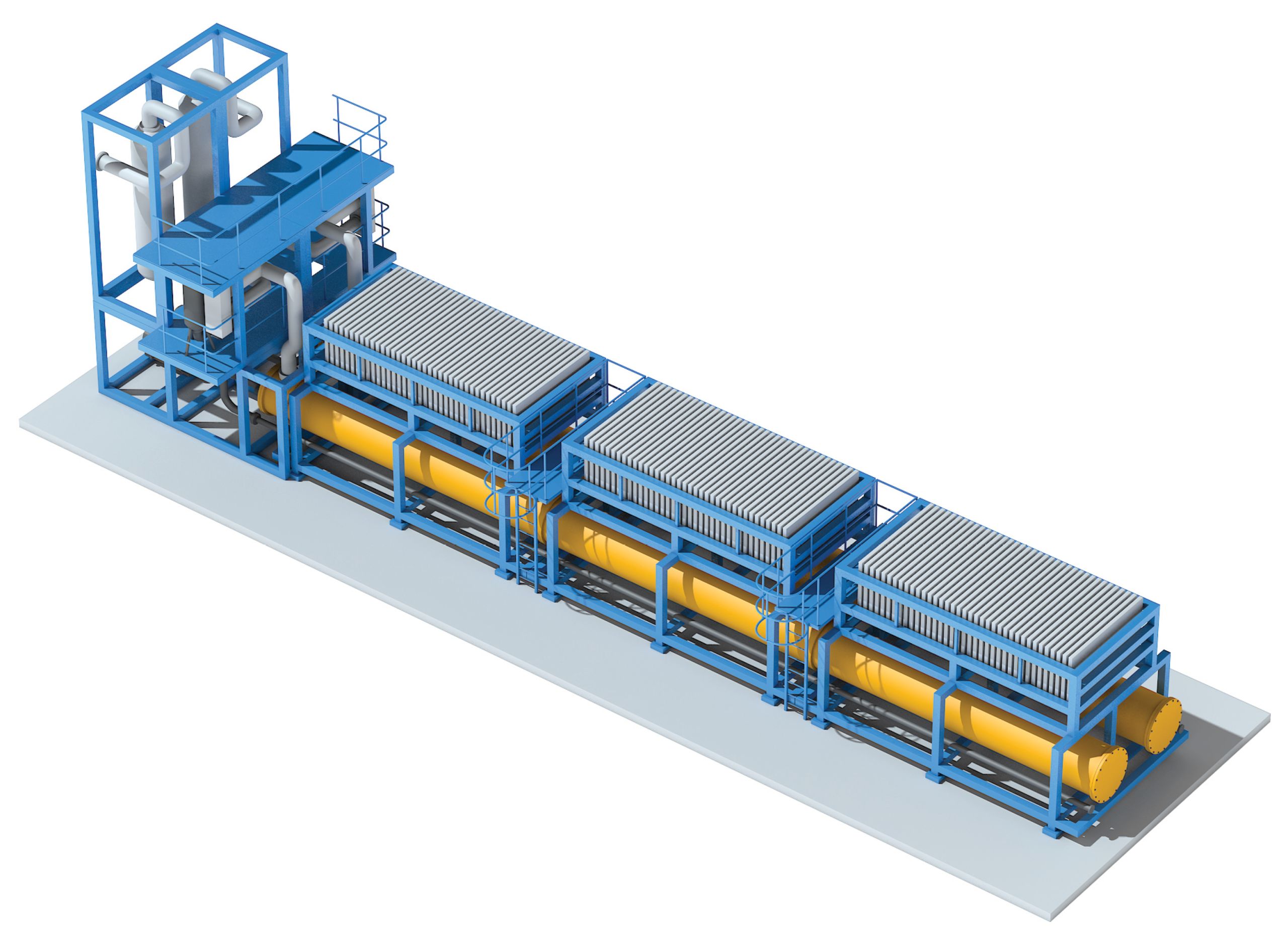
FIGURE 3. Based on technology well-established in the chloralkali sector, this water-electrolysis system can be scaled up to 10 MW
FIGURE 3. Based on technology well-established in the chloralkali sector, this water-electrolysis system can be scaled up to 10 MW

Currently, almost all of the world’s H2 is supplied from fossil feedstocks in processes that emit CO2, unless the CO2 is adequately captured and stored. Clean H2 production is achieved by the electrolysis of water using electricity obtained from renewable sources, such as solar and wind. Presently, however, only about 5% of the world’s H2 is produced via water splitting. The process within the fuel cell is essentially the reverse of the electrolytic process for producing H2 from water.
Recently, thyssenkrupp AG (Essen, Germany; www.thyssenkrupp.com; Figure 3) and Siemens AG (Erlangen, Germany; www.siemens.com) have developed new, large-scale electrolyzers in order to decarbonize the production of H2 (Chem. Eng., January 2019, pp. 14–17).
Siemens’ electrolyzers were initially capable of turning kilowatts of renewable energy into clean H2, and the company is now building larger scale devices. Siemens will soon deliver a 1.25-MW unit to the Tonsley Innovation District of South Australia. It is also offering a unit capable of scaling up to 10 MW, with plans to scale further by another order of magnitude.
The largest solar-powered green hydrogen plant in the world is planned for the Burrup Peninsula in Western Australia by Yara Pilbara age, refueling, and fuel cell microgrid demonstration project would be operated by the company in the Boston area. More recently, the company has developed what it claims to be the world’s first all-in-one H2 refueler.
Last October, a Japanese consortium started construction of the Fukushima Hydrogen Energy Research Field (FH2R; Chem. Eng., October 2018, p. 10). FH2R will produce (using renewable energy) and store up to 900 ton/yr of H2. It will use a new control system to coordinate overall operation of the H2 energy system, the power grid control system, and the H2-demand-forecast system, so as to optimize H2 production, H2-based electricity generation and H2 gas supply.
The system will use H2 to offset grid loads, and deliver H2 to locations in Tohoku and beyond, and will seek to demonstrate the advantages of H2 as a solution in grid balancing and as a H2 gas supply. Compressed
H2 will be transported in trailers and supplied to users.

The U.S. Dept. of Energy (DOE; Washington, D.C.; www.energy.gov) Hydrogen and Fuel Cell Program conducts research and development in H2 production, delivery, storage and fuel cells. Its technical targets are: biomass-derived liquid reforming, electrolysis, biomass gasification, thermochemical water splitting, photoelectrochemical water splitting, photobiological processes, and microbial biomass conversion.
Meanwhile, research is being conducted at a water purification plant in Sendai, Miyagi Prefecture, Japan to incorporate H2 into renewable energy systems. The city of Fukuoka is engaged in a project to produce H2 with biogas extracted from sewage sludge. The H2 produced will be used for fuel cell vehicles.
“Sewage treatment plants across the nation have the potential to power up to 1.86 million fuel cell vehicles with hydrogen,” says Masaki Tajima, a professor of environmental energy at Tottori University (Tottori City, Japan; www.tottori-u.ac.jp).
Also in Japan, Toshiba Corp. (Tokyo; www.toshiba.com) has developed its 100-kW H2 Rex pure hydrogen cascading fuel cells, which increases the utilization rate of hydrogen. The fuel cells can generate power at a temperature of 80°C, which is much lower than the operating temperature of other types of fuel cells, eliminating the need for a heating process.
Researchers at the Center for Sustainable Chemical Technologies at the University of Bath (U.K.; www. bath.ac.uk), have developed an improved method for using sunlight to split water. They used perovskite solar cells. Since these cells are unstable in water, which limits their use for the direct generation of clean H2 fuels, the researchers used a waterproof coating from graphite. While perovskite solar cells produce a higher voltage than silicon cells, the voltage is still not enough to split water. To solve this problem, the researchers added catalysts.
Another way to boost H2 production from electrolysis has been recently discovered by a team from the Institute of Chemical Research of Catalonia (Tarragona, Spain; www. iciq.org), led by José Ramón Galón- Mascarós. The researchers achieved H2 production at low voltages just by approaching a permanent magnet to the anode, which results in immediate energy savings.
The team also used catalysts based on earth-abundant metals like nickel and iron. The team claims it can increase the H2-producing efficiency using an electrolyzer by 100%. In an industrial setting the team would expect efficiency gains of 30 to 40% (Chem. Eng., July 2019, p. 12).
Researchers at the Indian Institute of Science (Bengaluru, India; www. iisc.ac.in), led by professor Prabeer Barpanda, have developed a low-cost catalyst to speed up the splitting of water to produce H2.
One of the two major reactions involved in this process — the oxygen evolution reaction — is slow, limiting the process’ overall efficiency. The most efficient catalysts normally used are made of expensive metals, such as Pt and Ru. The Indian researchers have developed a catalyst by combining cobalt oxide with phosphate salts of sodium (metaphosphates). The researchers claim this catalyst is more than two hundred times less expensive than the current state-of-the-art RuO2 catalyst, and the reaction rate is also faster.
To make the catalyst, the researchers roasted sodium metaphosphate and cobalt oxide in an argon atmosphere. This creates a sheet of partially burned carbon onto which crystals made of cobalt oxide framed by sodium metaphosphate are spread out. The metaphosphates form a strong framework to hold the cobalt oxides intact, showing high stability. This treatment allows the catalyst to retain its activity over multiple cycles.
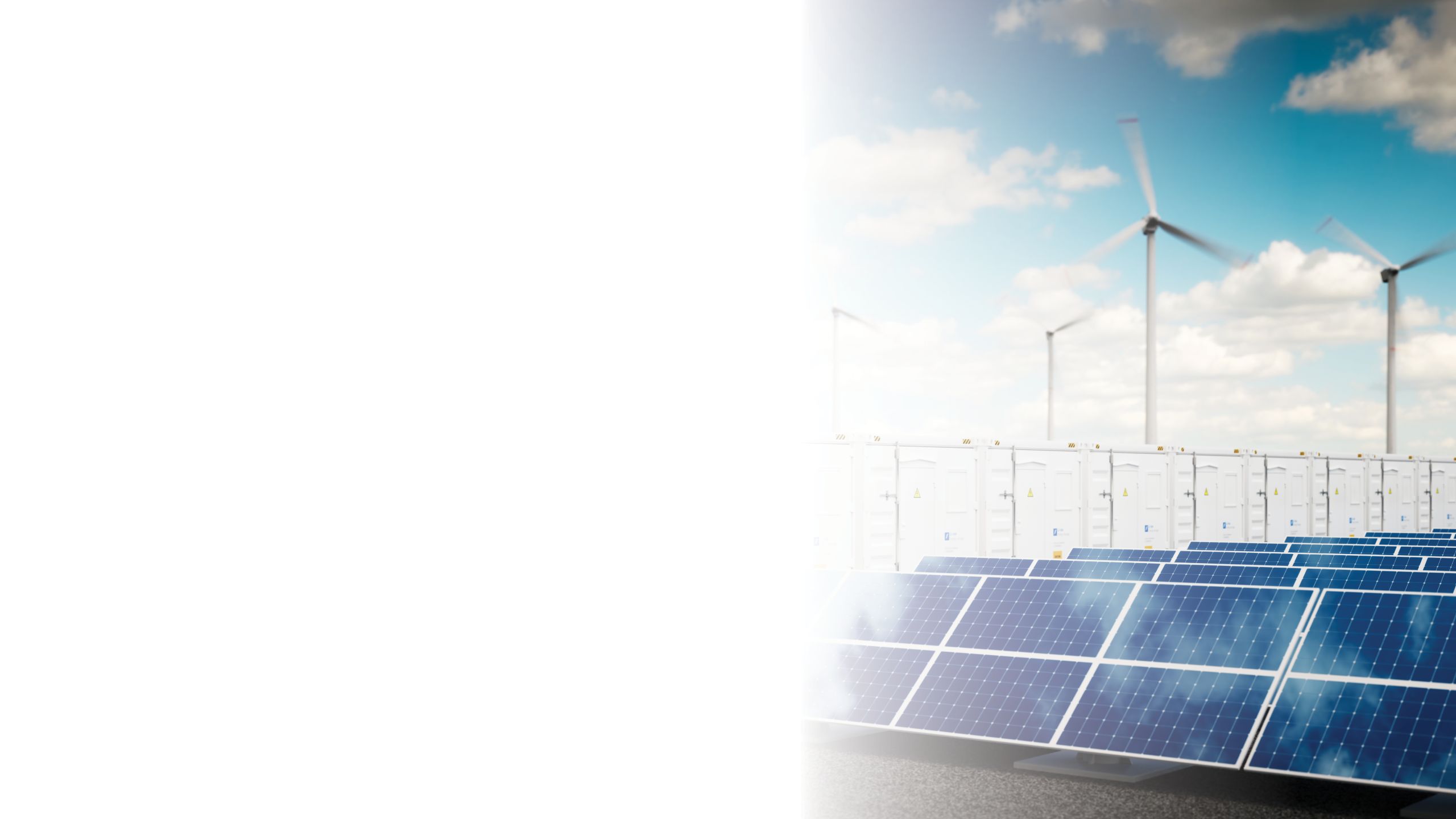
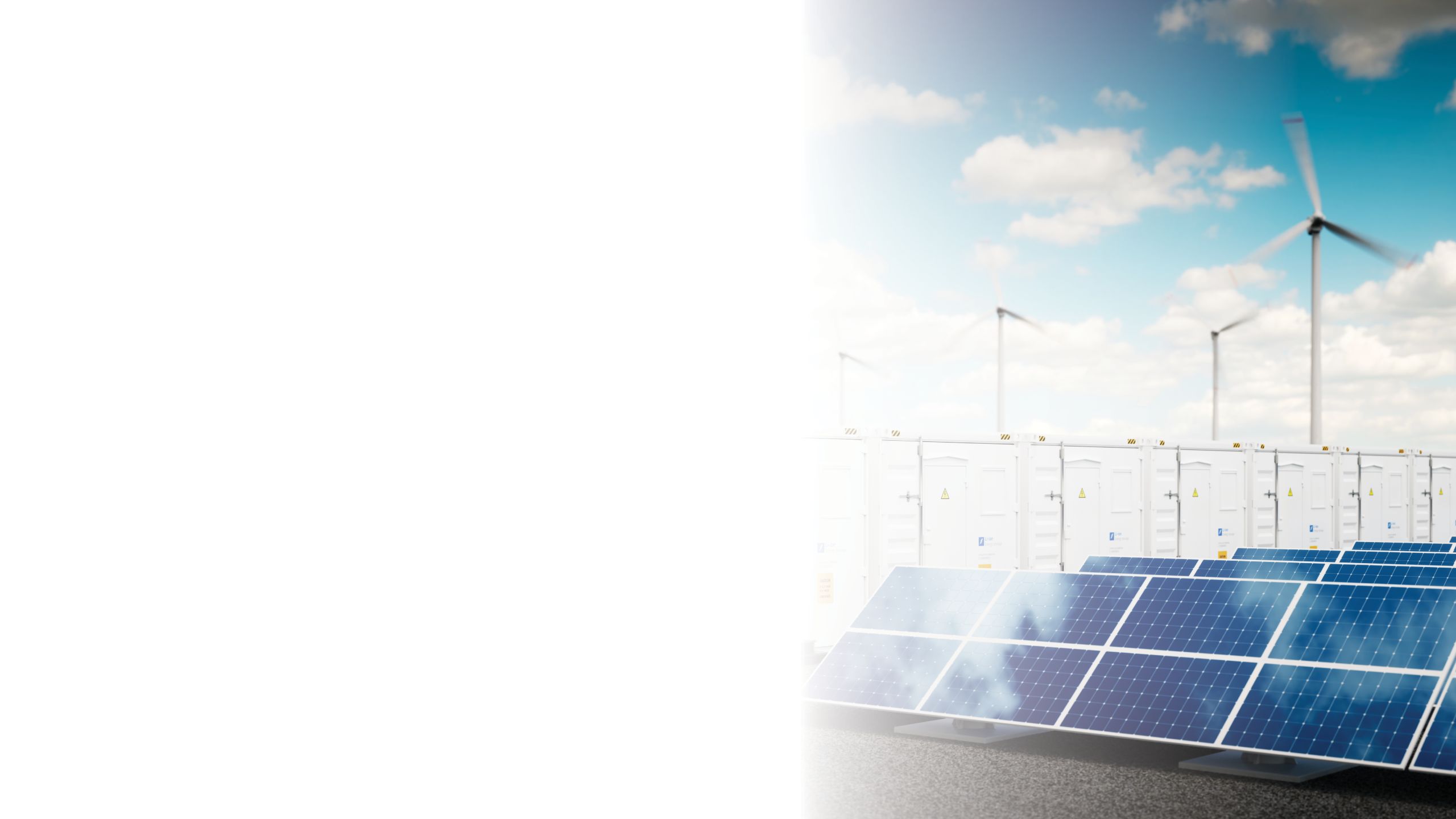
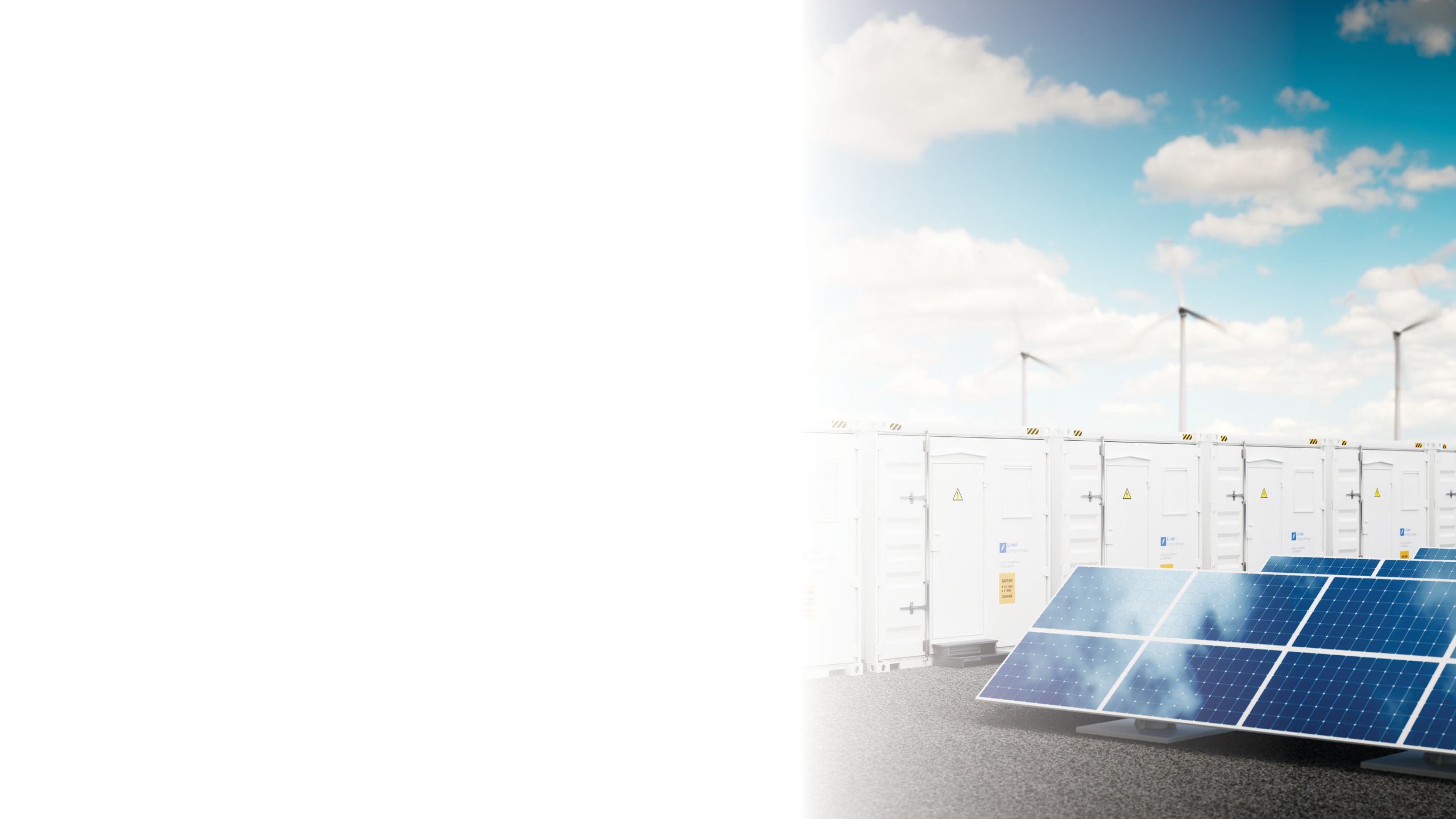

A team from the University of Michigan (Ann Arbor; www.umich.edu), led by professor Don Siegel, has identified ways to cram more H2 than ever before into metal-organic frameworks (MOFs), increasing the energy density, and therefore the projected driving range of fuel cell vehicles.
The team created a database on MOFs, and used computer simulations to screen nearly 500,000 MOFs for those best suited to store H2. Three MOFs were identified that would surpass previous records for H2 storage. Siegel says that by increasing the quantity of H2 that can be stored in a MOF adsorbent, the pressure needed to store it can be reduced, and the size of the tank can also be reduced.
In another way to store and transport H2, Chiyoda Corp. (Yokohama, Japan; www.chiyodacorp.com), in association with JXTG Nippon Oil & Energy Corp., the University of Tokyo and Queensland University of Technology, has developed the SPERA Hydrogen system. This system is kept in a liquid state at ambient temperatures and pressures, and can therefore be stored in existing tanks for a long time and transported by existing tankers.
The system is a liquid called methylcyclohexane (MCH). It is produced using the organic chemical hydride (OCH) method, whereby toluene and hydrogen are catalytically reacted. The volume of MCH is a small fraction of the volume of gaseous H2.
Although the OCH method using MCH has been known for a long time, no commercial catalyst has been developed for producing H2 from MCH in the dehydrogenation process. Chiyoda developed a dehydrogenation catalyst that continuously delivers stable high performance for more than 10,000 h at the laboratory scale.
In yet another approach, a team from the University of Newcastle (Newcastle-upon-Tyne, U.K.; www. ncl.ac.uk), led by professor Ian Metcalfe, has developed what it claims is the first thermodynamically reversible chemical reactor capable of producing H2 as a pure product stream.
The reactor avoids mixing reactant gases by transferring oxygen between reactant streams via a solid-sate oxygen reservoir. The reservoir is designed to remain close to equilibrium with the reacting gas streams as they follow their reaction trajectory and thus retains a “chemical memory” of the conditions to which it was exposed. The H2 is thus produced as a pure product stream, eliminating the need for costly separation of the final products. “Whereas conventional H2 production requires two reactors and a separation, our reactor accomplishes all the steps in one unit,” Metcalfe says.
Researchers from Pohang University of Science and Technology (Pohang, South Korea; www.postech. ac.kr) and the Colorado School of Mines (Golden, Colorado; www. mines.edu), led by Pohang’s Kun- Hong Lee and Bo Ram Lee, have introduced a new concept for improving hydrogen storage capacity inside the structure formed by water molecules called gas hydrates.
Gas hydrates are ice-like solid compounds including gas. The main problem in storing hydrogen in gas hydrates has been lowering the energy required. The researchers studied the metastability of gas hydrates, which is determined by a stable state that can be changed by the addition of a small amount of energy. They succeeded to keep the hydrogen hydrates stable at very mild pressure (0.5 to 1MPa) and demonstrated increased H2 storage in the hydrates (up to 52% larger amount).
“If an appropriate process is designed to trap the system in this metastable state with a high concentration of gas, coupled with the benefits of hydrate self-preservation, a new paradigm will be born for gas storage in clathrate hydrates,” says Kun-Hong Lee.
Meanwhile, the CSIRO (Melbourne, Australia; www.csiro.au) has conducted a study on the “Round-trip Efficiency of Ammonia as a Renewable Energy Transportation Medium.” The study says that NH3 is an excellent proposition for converting renewable energy to H2, transporting it to locations with low renewable energy intensity and converting the NH3 back to H2 for local consumption. The round-trip efficiency of electrical energy storage can be higher than 80%, the study says.
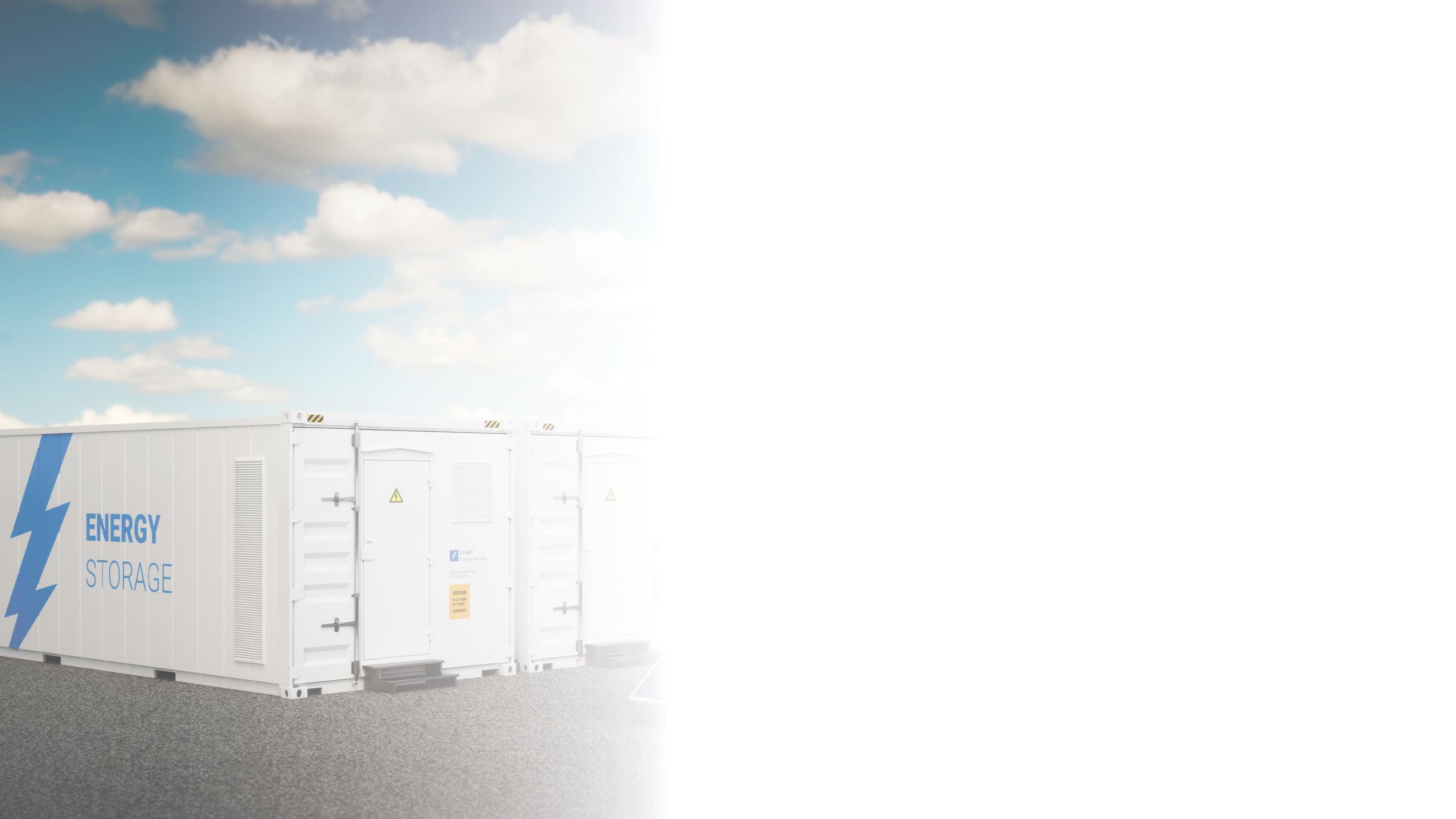
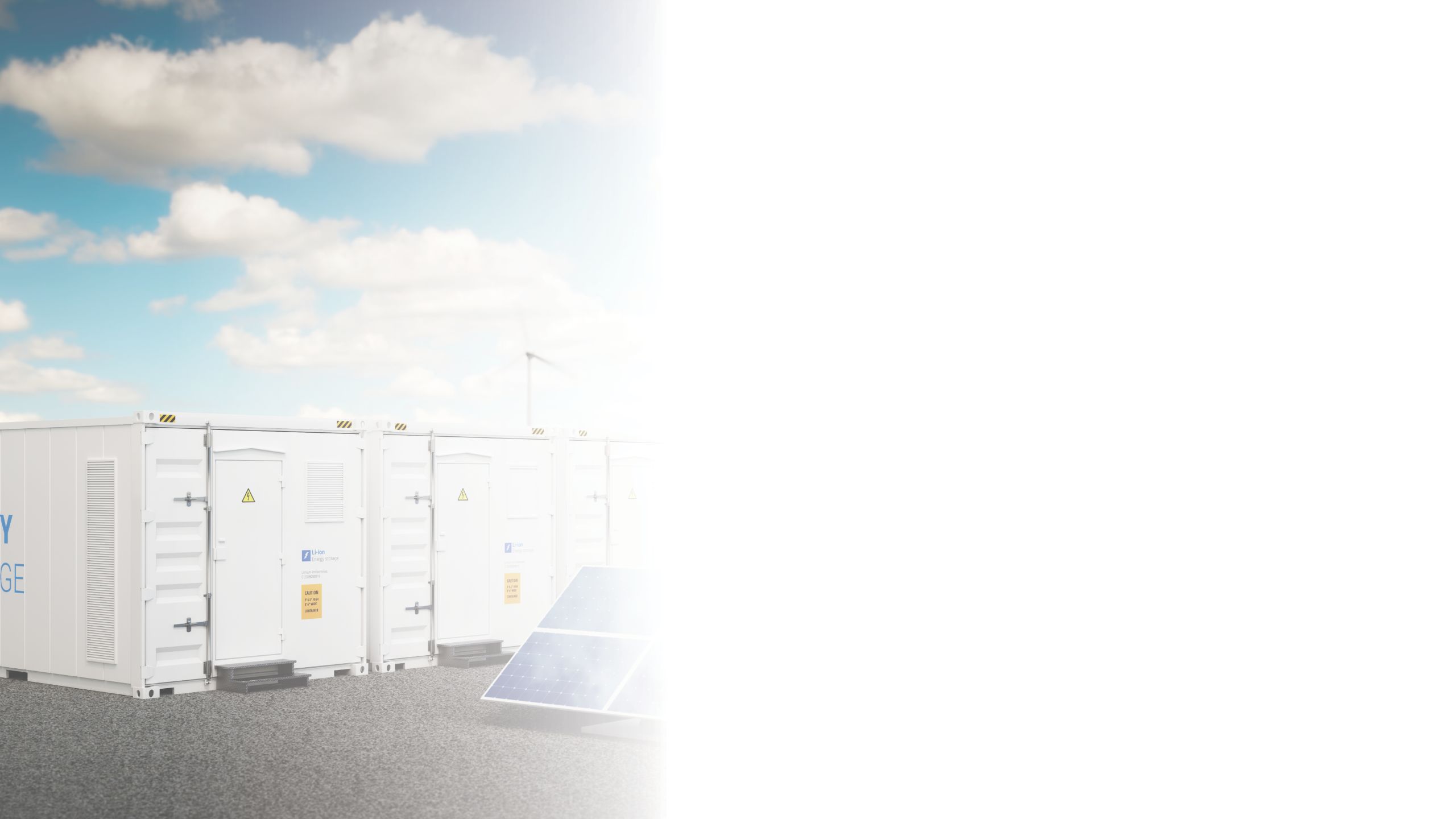
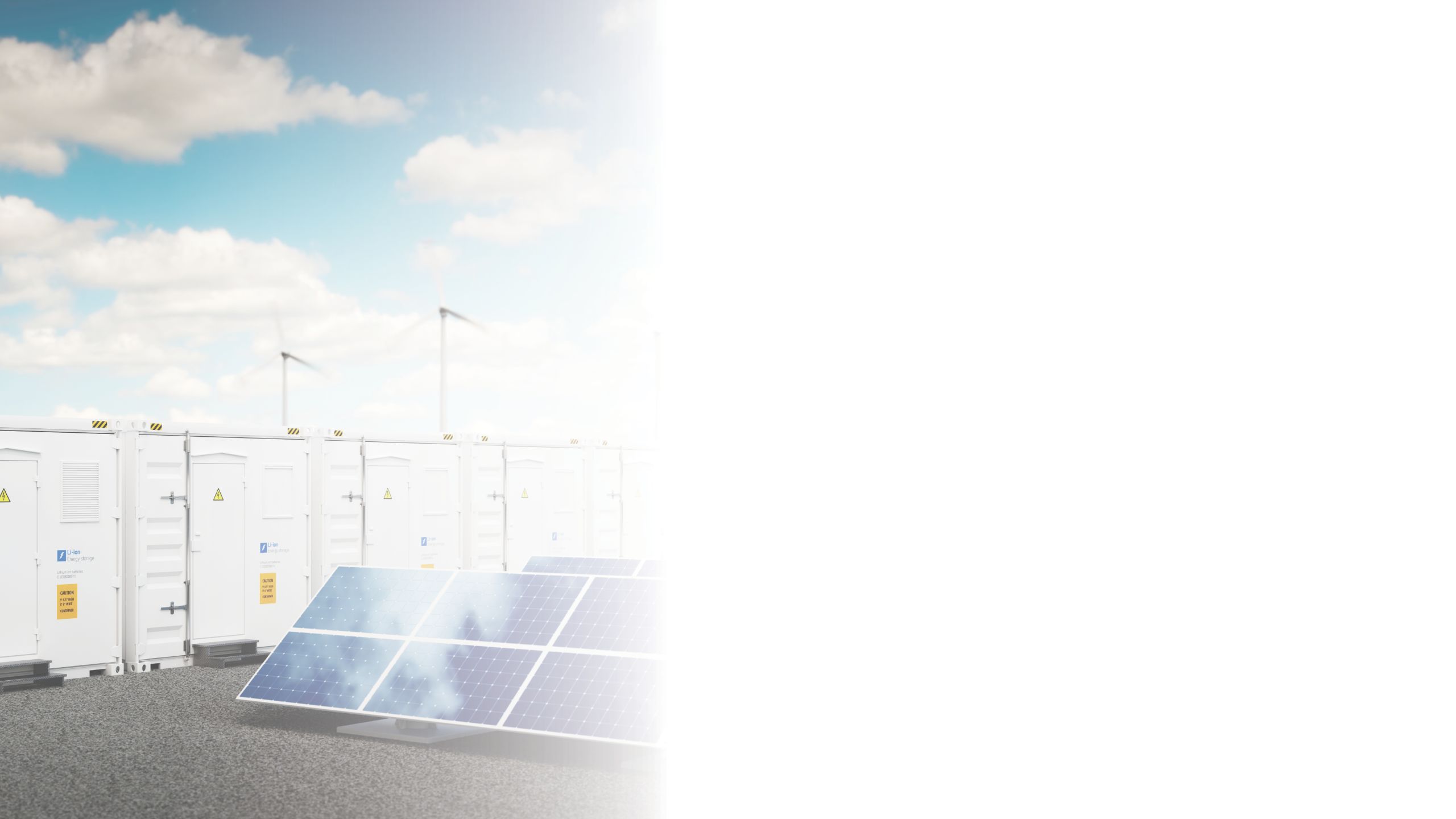