Ethernet-APL: The Future of Field Connectivity
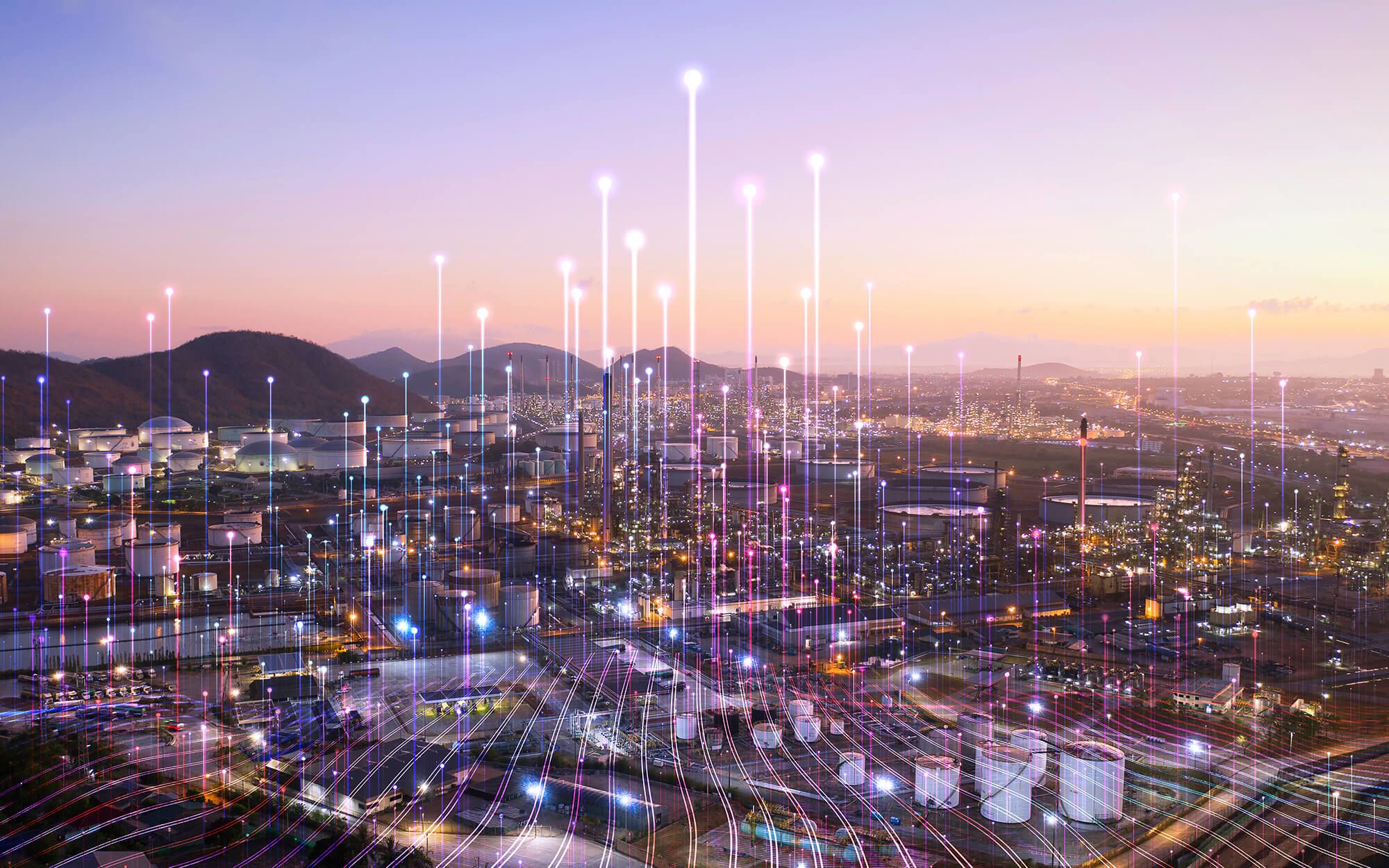
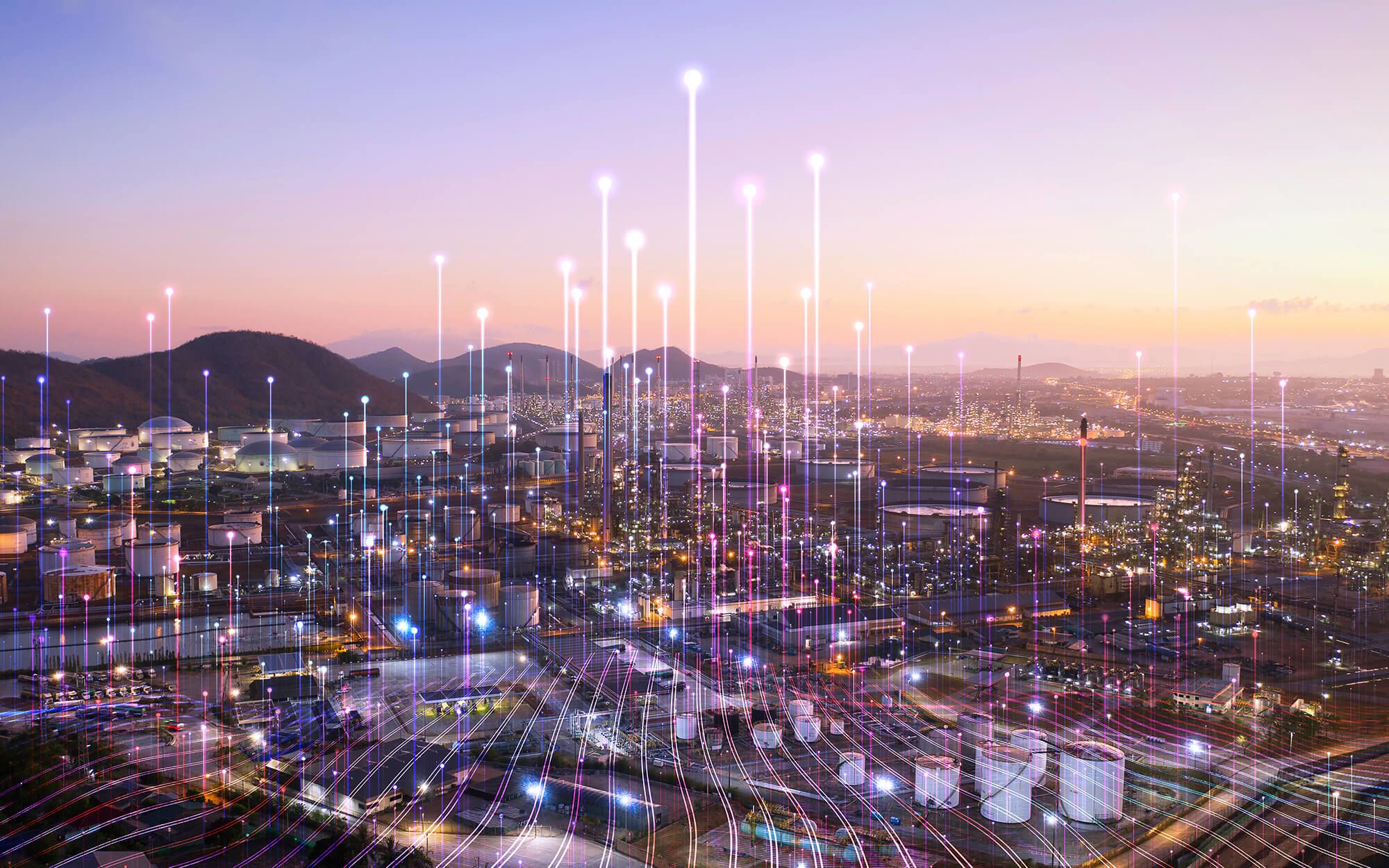
Ethernet Advanced Physical Layer (APL) provides connectivity between field-generated data and enterprise systems. Presented here is information on the design and operation of this rapidly expanding technology
Process plants today have vast amounts of data available at the field level from smart devices. However, these data are hardly accessible to other levels of the organization because of the different communications technologies between the devices at the field level and the Ethernet architecture at the enterprise level. This lack of data access hinders the implementation of digitalization projects and prevents process plants from achieving the maximum benefits of data-driven approaches, such as the use of digital twins or predictive maintenance models.
Ethernet-APL (Advanced Physical Layer) is overcoming these challenges by providing connectivity between field data and enterprise systems at the speed and bandwidth required for higher level applications. This article explains how Ethernet APL is being used, and details its features and benefits.
Ethernet-APL transmits power and data via a two-wire cable and can achieve data rates of 10 Mbit/s with long cable lengths. Ethernet-APL complies with intrinsic safety requirements, and functional safety solutions are under development. Depending on the topology design of the network, up to 50 APL devices or even more than 200 APL devices can exist on an Ethernet-APL segment.
The technology was launched at the Achema Pulse Conference (Frankfurt, Germany; www.achema.de) in 2021 [1] and has been tested in a laboratory at BASF (Ludwigshafen, Germany; www.basf.de). Many benefits have been proven during this evaluation. The technology is expected to expand rapidly with many field devices with APL interfaces already available or soon to be available.
Legacy technology challenges
Industrial instrumentation has progressed from the original pneumatic technology to analog devices, and further, to digital technologies, such as HART, Profibus PA or Foundation Fieldbus. Each new technology has offered benefits over the previous generation, but each still has limitations of its own.
The HART protocol is extremely slow. Troubleshooting and parameterization must be performed locally at the device. Wiring is expensive, and the system requires complex protocol conversions for remote access. HART technicians are required to scale measurements manually during initial device setup, as well as for device replacement. This technology is primarily used for parameterization and troubleshooting and very rarely for process control.
Fieldbus technologies also have a slow data-transfer rate, although it is faster than the HART protocol. However, fieldbus systems are complex in terms of their protocol conversions for remote access, engineering of segments, and troubleshooting. There is some industry resistance to widespread adoption of fieldbus technology due to the complexity associated with its use.
Existing industrial architecture has an electronic or fieldbus layer for field devices, a plant Ethernet network for supervisory and control layers, and an enterprise Ethernet for management and planning. However, to enable the seamless data access across all layers, a single network technology is required. Making vast quantities of data available in real time for optimization and analytical models, while meeting the requirements of the harsh environments in process plants, has been one of the primary drivers leading to the development of Ethernet-APL. (Figure 1).
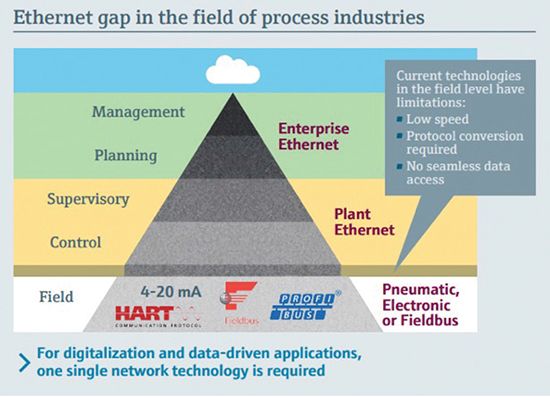
FIGURE 1. An Ethernet “gap” exists at the field-device level
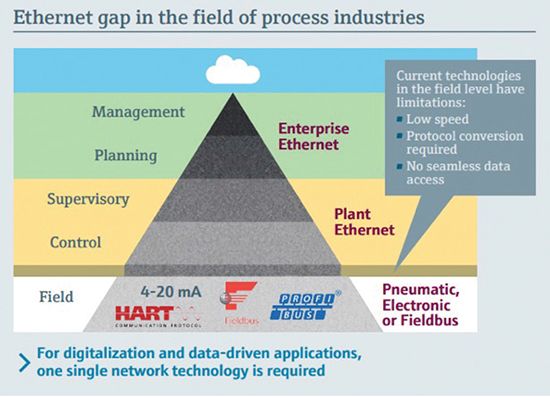
FIGURE 1. An Ethernet “gap” exists at the field-device level
FIGURE 1. An Ethernet “gap” exists at the field-device level
Standard Ethernet limitations
Standard Ethernet seems to offer many of the features needed for the next generation of industrial field instrumentation. However, there are some drawbacks that make it impossible to implement directly into industrial settings. For example, 100BASE-TX Ethernet has a data rate of 100 Mbit/s full duplex, but cable lengths are limited to 100 m.
Standard Ethernet uses CAT5/6 cables that have four internal wires. This is incompatible with industrial installations, which require a two-wire solution for field instrumentation. It is vital for an industrial Ethernet solution to integrate with the existing two-wire infrastructure to prevent the need for rewiring whole plants, which would not be financially justifiable.
Many field instruments are loop-powered, meaning that they receive the power supply from the same pair of wires that transmits their data. Standard Ethernet is not designed to supply power at this scale, and therefore cannot be used on many field instrument installations.
One of the most critical features of industrial field instrumentation in process plants is compliance to intrinsic safety requirements. Devices, switches, wiring and terminals found in hazardous areas must be certified as explosion proof or non-sparking depending on the area classification. Standard Ethernet does not meet these intrinsic-safety requirements for industrial applications.
Ethernet-APL is designed to overcome these limitations without losing the benefits of Ethernet technology for industrial use.
Field connectivity
Major user organizations and leading manufacturers worked together over the last years to develop an Advanced Physical Layer for Ethernet that meets the requirements of process plants. The requirements for this new technology were aligned with the NAMUR organization (User Association for Automation Technology in the Process Industries; Leverkusen, Germany; namur.net) and noted in an official NAMUR recommendation [2]. The following standards and guidelines are the most important documents in the context of Ethernet-APL:
IEEE 802.3cg-2019. This new IEEE standard 10BASE-T1L defines the full duplex 10 Mbit/s data transmission via a two-wire cable for long cable runs. It is mainly relevant for the PHYs (the PHY layer defines the physical and electrical characteristics), which are integrated in the APL devices.
IEC TS 60079-47. This technical specification for a two-wire, intrinsically safe Ethernet ensures the installation of two-wire Ethernet devices in hazardous areas. The concept is derived from the well-known FISCO (Fieldbus Intrinsically Safe Concept) and provides a simple installation without Ex calculations.
APL Port Profiles. This specification defines the power supply via the same two-wire cable with different power profiles. In addition, the preferred cables and connection technology is defined.
APL Engineering Guideline. This user-centric document supports end users during planning, installing and commissioning of APL networks. It provides many useful information in terms of topologies, shielding, cables and so on.
APL Conformance Tests. Via these mandatory conformance tests, it is ensured that APL components are interoperable with each other
Ethernet-APL topologies
Ethernet-APL can be designed using different topologies to match the requirements of each process plant. “Star” topologies suit plants with a compact layout, while “trunk-and-spur” topologies are similar to fieldbus architectures (Figure 2). Depending on the switch variant, it is possible to mount APL field switches in Zone 2 or Zone 1 areas and to connect APL field devices in different Ex zones, including intrinsic safety (Ex ia).
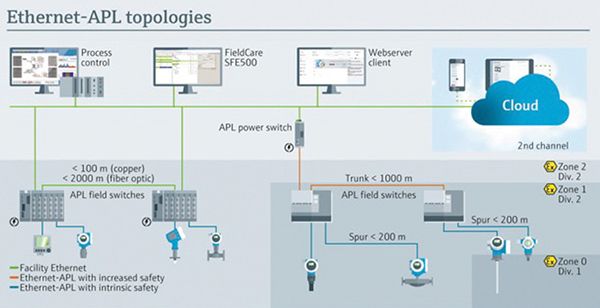
FIGURE 2. Several examples of potential network topologies are possible with Ethernet-APL
FIGURE 2. Several examples of potential network topologies are possible with Ethernet-APL
Star topologies require externally powered APL field switches. These switches supply power to each APL field device connected on the spur line in a point-to-point configuration. Several APL field switches can be connected in line or in a ring formation using copper cables or fiber-optic lines.
Trunk-and-spur topologies require an additional APL power switch, which supplies power from the central control room to the field via a powered trunk line. Both APL field switches and APL field devices are powered via this APL trunk. No other field-level power supply is needed.
There is no general rule about which topology shall be preferred. It always depends on the plant design, communication requirements and the environment. In general, the star topology provides more flexibility in terms of redundancy and number of devices per segment. The trunk-and-spur topology might be more relevant if additional power supply in the field requires a lot of effort.
Ethernet-APL offers a path for migrating a brownfield plant to this new technology. Power conditioners, junction boxes and field barriers must be replaced with APL switches. Any existing cable that does not meet the specifications for Ethernet-APL will have to be replaced as well. The well-known Fieldbus Type A cables, which meet the required APL cable characteristics, are the preferred cable type for Ethernet-APL installations. Specific SPE cables for 10BASE-T1L are also suitable.
APL switch vendors are providing the possibility to connect devices using either Profibus PA or Profinet-APL at the same APL field switch. This means that the Ethernet-APL technology can be installed on site even if some instruments are not yet available with an APL interface.
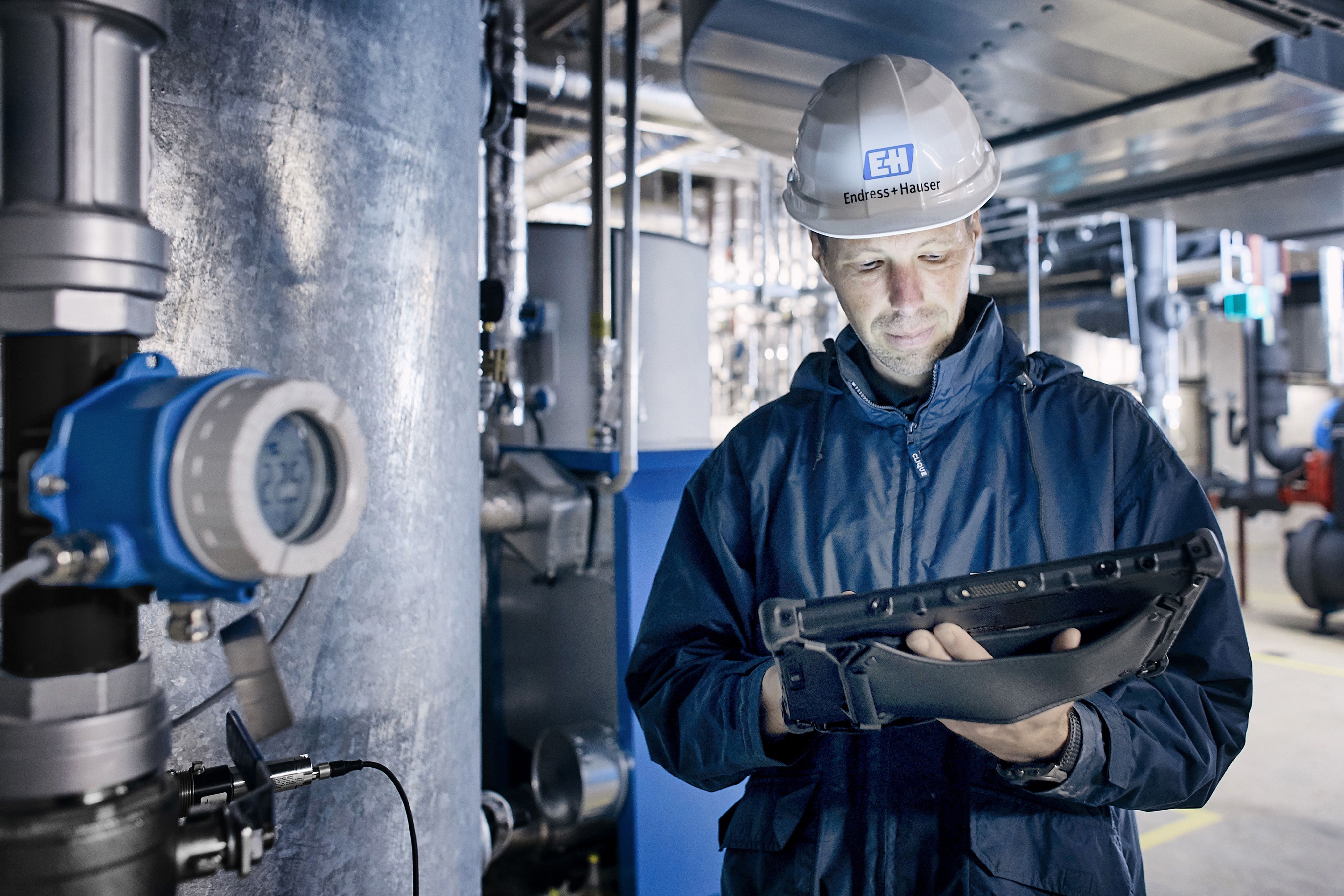
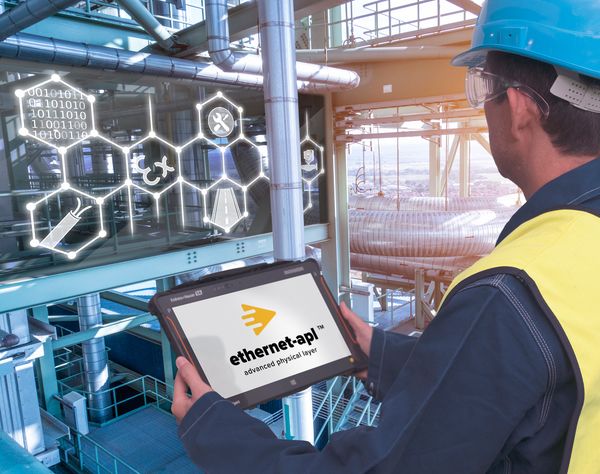
Integration into higher applications
Profinet.
Profinet is a well-established industrial Ethernet protocol used in many industries already. In combination with Ethernet-APL, Profinet will also fully enter the process industries. The GSD (general station description) file is the Profinet device driver that is used for the integration to distributed control system (DCS). This file is stored on each device, which makes it easy to integrate new devices onto the network. Profinet PA Profile 4 offers additional benefits, such as harmonized integration and diagnostic messaging. It supports vendor-independent device exchange because parameters are automatically downloaded after exchange without any other system adaptations.
Profinet features like S2 System Redundancy and the Media Redundancy Protocol (MRP) ensure a very high plant availability. This is because the system can cope with both cable failures and controller failures without interruption.
All process variables of a device are available via Profinet in digital form and without conversion losses.
Parameterization, troubleshooting, asset management.
These use cases are possible remotely via the network and in parallel to the process control system because information is available at a much higher speed and performance using Ethernet-APL. This means that maintenance personnel can troubleshoot field devices remotely and efficiently by accessing the cause and remedy information for the device. They can also troubleshoot the Ethernet network itself by accessing the frames and packages information without the use of oscilloscopes.
Cloud / IIoT / data-driven applications.
An edge device on the facility Ethernet provides an interface to the cloud. This means that field data can be accessed directly by higher-level applications without passing through via a process control system. This setup fulfills concepts like NAMUR Open Architecture (NOA) [3, 4] and related use cases. Edge devices make high volumes of data available in real-time. The technology opens the door for the implementation of digital twins for equipment monitoring and optimization.
Functional safety and cybersecurity
Safety infrastructure is normally built separately to process control infrastructure. This physical separation increases diversity and independence, which improves safety system availability. Safety applications are traditionally equipped with 4–20-mA technology. However, the bandwidth and reliability of Ethernet-APL is creating an opportunity to unify the infrastructure for safety and process control applications, while still meeting the most stringent safety standards. The next logical step is to enable the use of Ethernet-APL in safety applications. There is no limitation to the use of Ethernet-APL for safety applications. The relevant adaptations are mainly on the level of Ethernet protocols.
In the context of Profinet as an industrial Ethernet protocol over Ethernet-APL, PROFIsafe is already available as an additional layer that acts according to the black channel principle. PROFIsafe is a well-established technology that has been used in factory automation for many years. This means Ethernet-APL, in combination with Profinet and its black channel layer PROFIsafe, will be the solutions to bring digital communication even into functional safety applications.
Connecting field devices to the Ethernet network introduces security concerns. There are three areas where security must be taken into account:
- At the device
- At the point of integration to the Ethernet network
- During development
IEC 62443 is the standard governing cybersecurity of industrial automation and control systems. Manufacturers must certify their development lifecycle against this standard [5]. As a further safeguard, organizations belonging to bodies like computer emergency response teams (CERT) and VDE (Association for Electronic, Electrical and Information Technologies) vulnerability management show that they have systems in place to manage issues that may arise.
At the device level, security is affected at different touchpoints. Firmware update files must be certified as authentic before loading on a device. Authentication and authorization prevent unauthorized access to field devices. Security is a major area of focus for the industry and continues to receive significant investment for future developments.
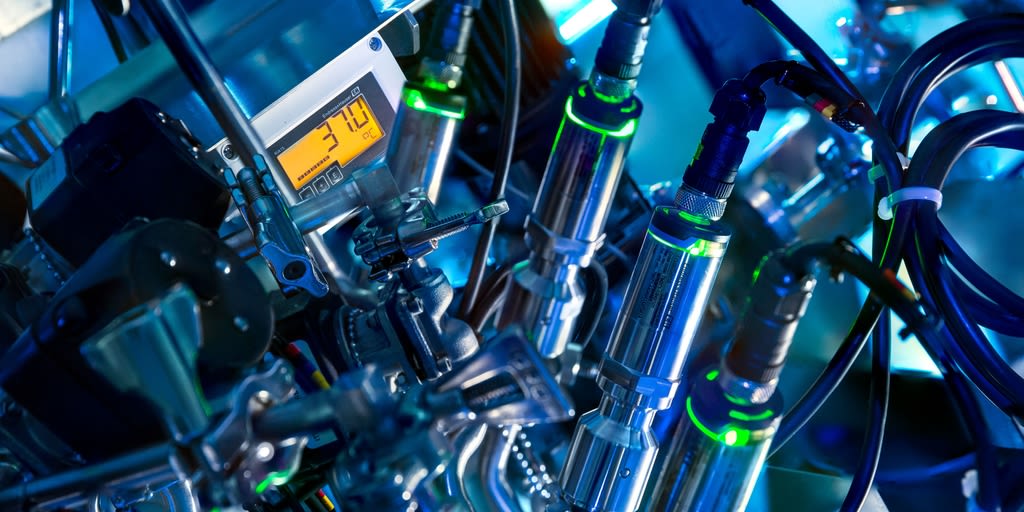
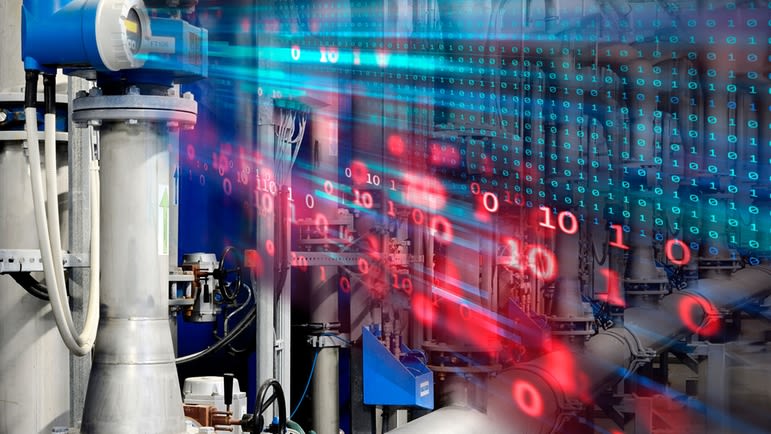
Enjoying the article? Read more here:
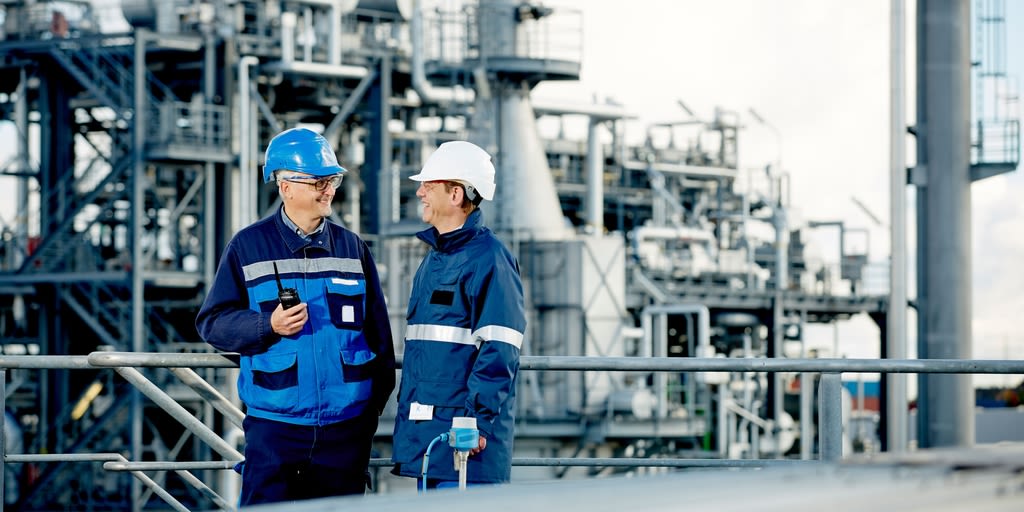
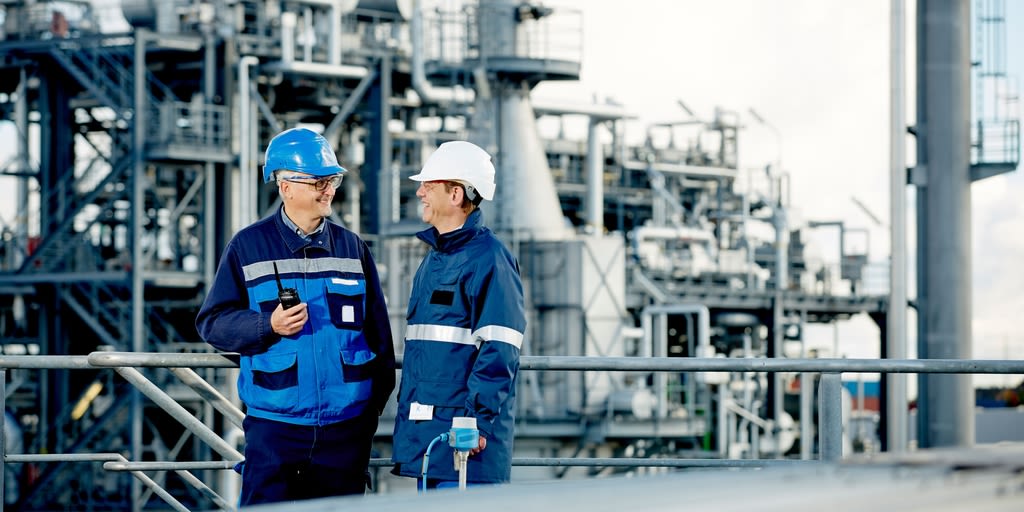
Features and benefits
Implementing Ethernet-APL is cost effective at each lifecycle stage of a plant. During engineering, APL components might be more expensive, but the complete network infrastructure, the absence of EX-calculations and the fully extendable architecture speed up the engineering process and reduce costs. Installation is error-free and the commissioning stage benefits from fast and remote access for parameterization. This means shorter commissioning times and earlier startup of production. During operation and maintenance, the availability of data enables improved optimization and predictive maintenance.
Ethernet-APL overcomes the limitations of current field level technologies. Ethernet-APL with 10 Mbit/s is 300 times faster than fieldbus technology and even 8,000 times faster than the HART protocol. This speed offers significant benefits during commissioning, operation, and maintenance. A parameter report, for example, can be created within seconds — even remotely, instead of within several minutes — locally at the device.
Speed is not the only advantage of Ethernet-APL. The number of devices per loop is significantly increased. Using a trunk-and-spur topology, up to 50 field devices can be connected to an Ethernet-APL segment. This is a substantial improvement on the 16-device limit for an equivalent Foundation Fieldbus segment. If you adopt a star topology, you can connect several APL field switches in line and add APL devices up to the limit of a controller. This limit can be further extended by adding another Ethernet interface within the controller.
Ethernet-APL is based on the Fieldbus Intrinsically Safe Concept (FISCO) for two-wire fieldbus solutions, which is already known in process plants. For Ethernet-APL, the same electrical parameters are used and specified in 2-WISE (two-wire intrinsically safe Ethernet). In this way, it does not require any Ex calculations, which significantly reduces the engineering effort when implementing intrinsic safe solutions.
The volume and speed of data transfer available using Ethernet-APL is making possible some higher-level applications that the industry has been demanding for some time. Condition monitoring and predictive maintenance are prime examples where the comprehensive data available from smart devices can be monitored, analyzed and used to determine equipment health. Predictive maintenance techniques enable users to identify issues before they affect device performance so that equipment can be repaired before it has a negative impact on production (Figure 3).
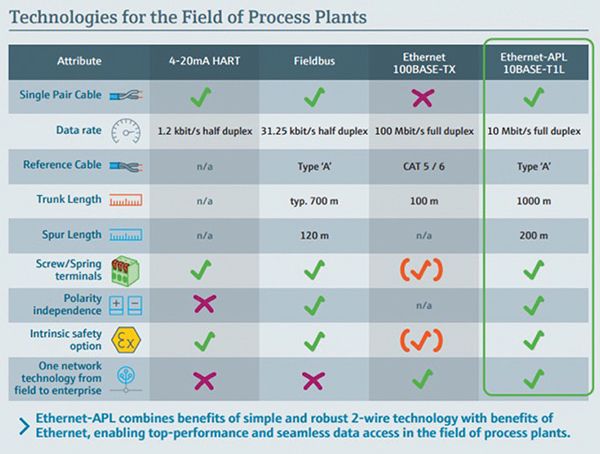
FIGURE 3. The chart shows a comparison of field-level technologies in process plants
FIGURE 3. The chart shows a comparison of field-level technologies in process plants
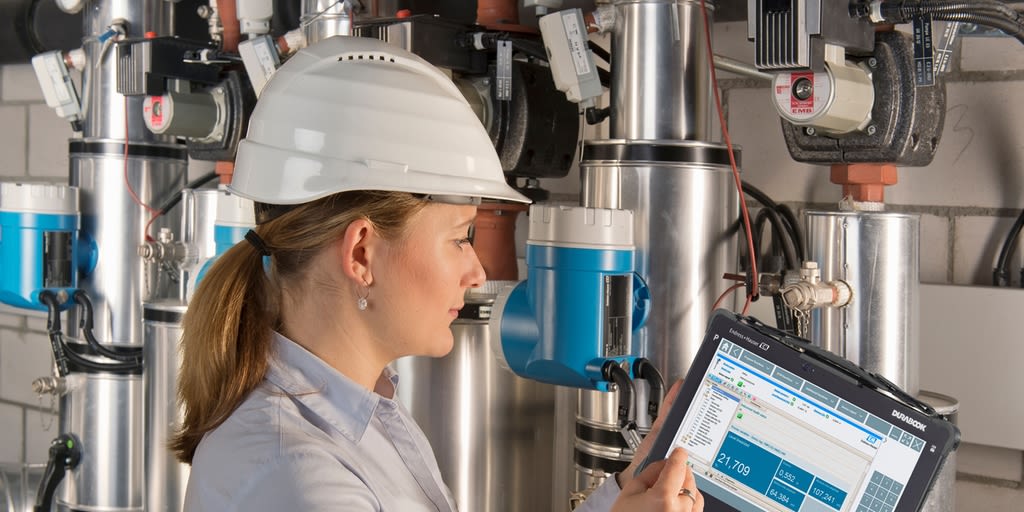
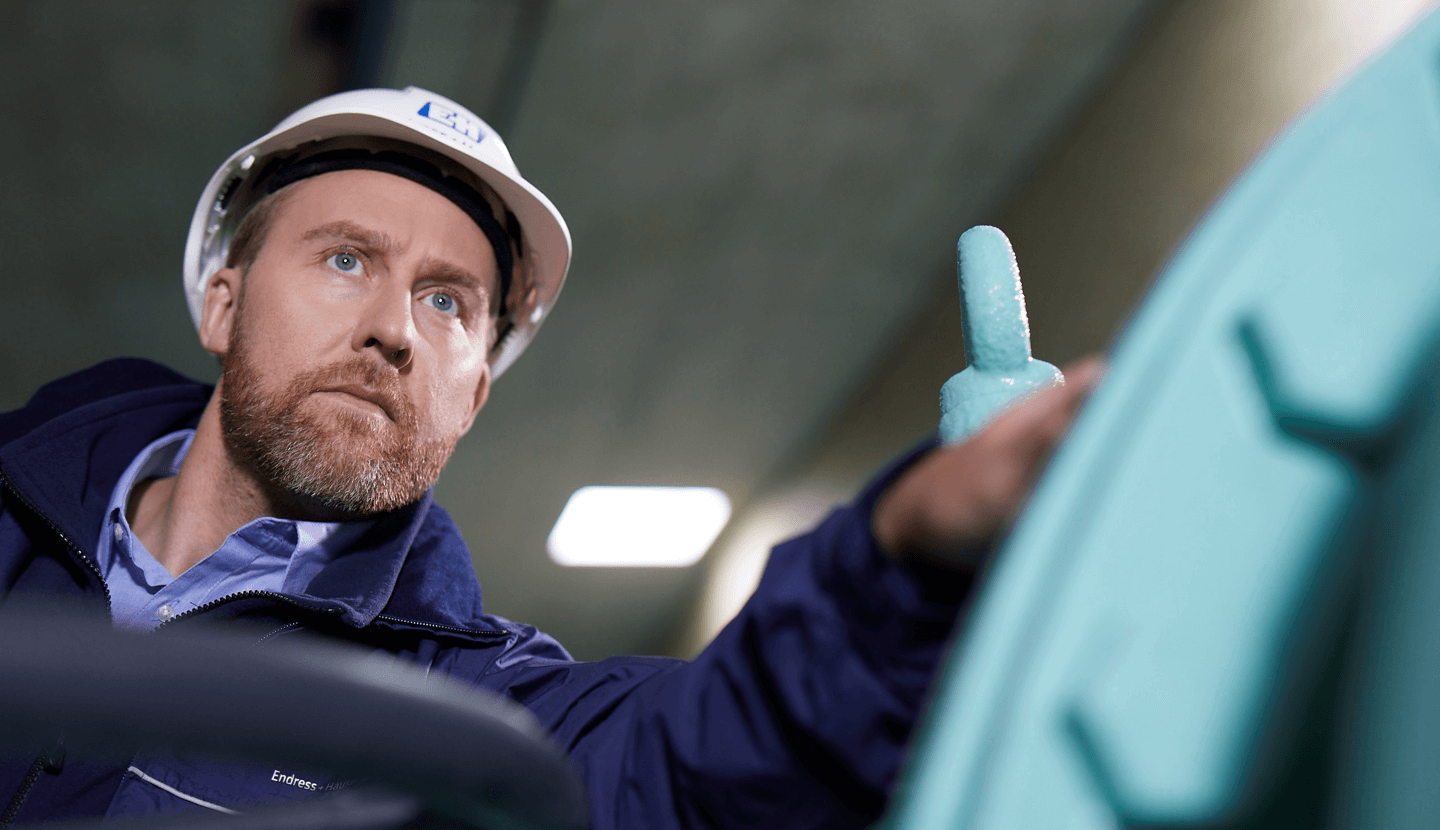
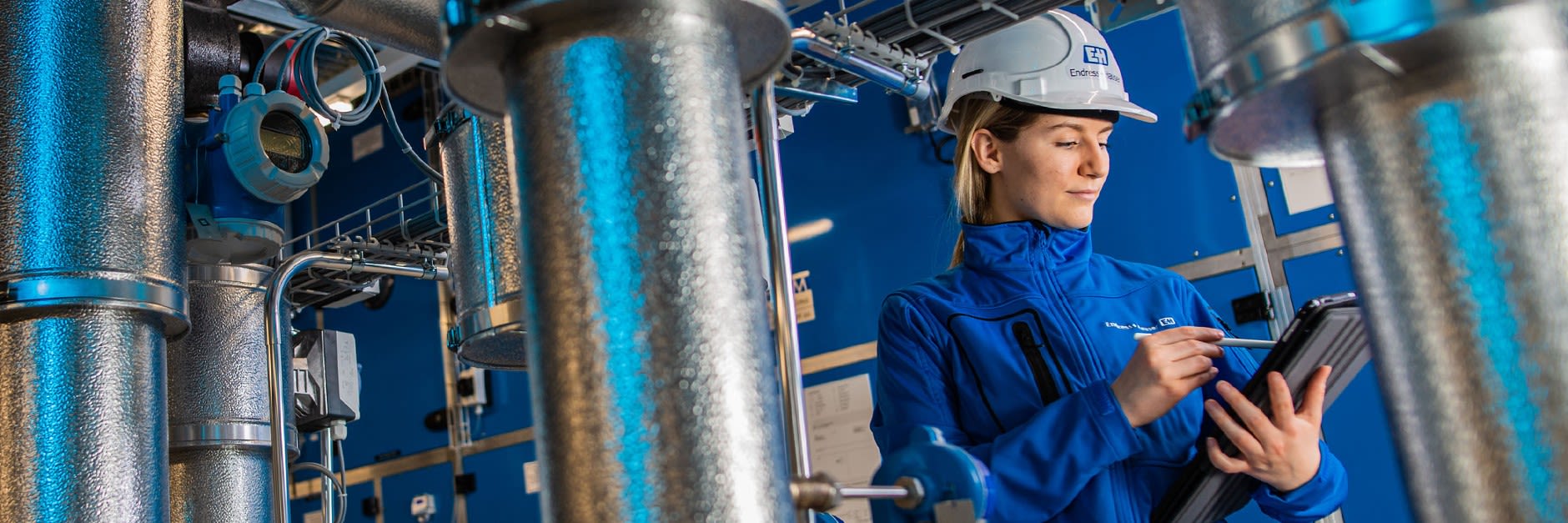
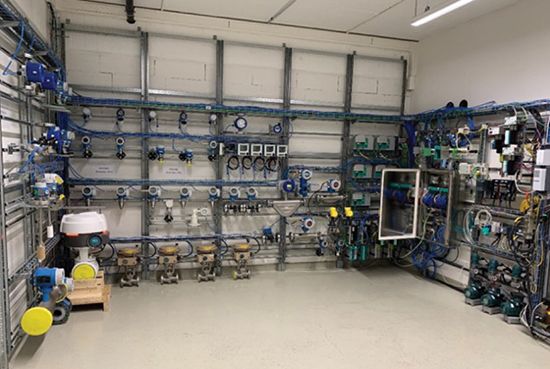
FIGURE 4. The BASF APL evaluation laboratory is shown here
FIGURE 4. The BASF APL evaluation laboratory is shown here
BASF case study
Historically, new product development happened in secret and with a small group of researchers and developers. However, a modern approach includes pilot customers, product managers, market specialists and salespeople. It is with this approach in mind that BASF implemented an APL laboratory to participate in the development of Ethernet-APL. This APL evaluation laboratory is led by the electrical, instrumentation and automation specialists Mathias Koch and Philip Kling, under the supervision of one of the authors (Niedermayer).
BASF started the digital communication journey for field instrumentation in 2005, with Foundation Fieldbus and Profibus PA. But it was only in 2016 that Ethernet was first proposed as a realistic alternative for digital field connectivity through the development of Ethernet-APL. By 2019, BASF had established a test laboratory for Ethernet-APL using prototype equipment from several vendors (Figure 4). The purpose of the laboratory was to evaluate Ethernet-APL technology for communication between distributed control systems and field transmitters and valves. These tests were very successful and many benefits with Ethernet-based communication could be identified.
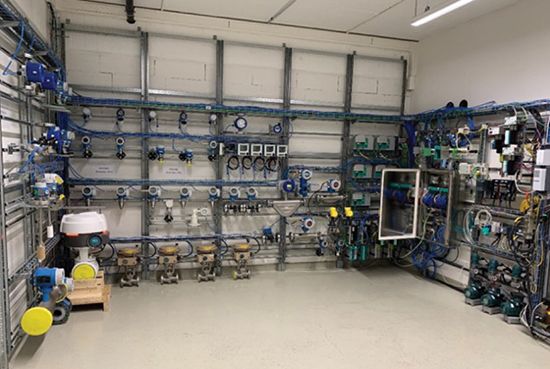
FIGURE 4. The BASF APL evaluation laboratory is shown here
Laboratory tests show that Ethernet-APL offers substantial improvements compared to analog technology and Profibus PA or Foundation Fieldbus. It is possible to upload and download sensor information in a variety of formats, including PDF, with a speed which is 300 times greater than what BASF could achieve with fieldbus technologies.
Using the two-wire technology of Ethernet-APL simplifies installation and maintenance activities for field technicians. There is no difference between connecting an analog transmitter and an Ethernet-APL device. Polarity is irrelevant, so the wires can be connected to either terminal without affecting the reading. Motor controllers and frequency converters can also connect to the same (or to a separate Ethernet ring), meaning that all instrument and electrical devices use the same network technology.
Profinet as the industrial Ethernet protocol over Ethernet-APL, including PA Profile 4, offers many advantages to fulfill the requirements of standardization and high availability.
Changing a faulty device on an Ethernet-APL network with Profinet protocol is simply a matter of disconnecting the old device and connecting the new device. The DCS will write the configuration to the device, allowing it to communicate with the DCS directly after booting up. This even works for a device exchange across vendors.
Profinet systems automatically compensate for wire breaks using media redundancy. If a wire breaks in the field, the device will still have a path to transfer the information to the DCS. Controller redundancy is also built into the Profinet solution. If a controller goes down, the redundancy partner will take over and devices will automatically communicate with the alternate controller. This feature satisfies the high availability requirement of process plants.
Several types of APL field switches were tested in the BASF laboratory leading to some recommendations to vendors. For example, proxies within the APL field switches allow for the connection of PROFIBUS PA devices to the switch, which makes the transition to Ethernet-APL even easier.
BASF is enthusiastic about the capability that Ethernet-APL offers for predictive maintenance. Fast data transfer means that more information can be processed by higher-level applications to analyze equipment health and identify issues before they cause a failure. Edge devices connect to an Ethernet-APL ring and transfer data directly to the cloud. This means that field data becomes almost instantaneously visible from anywhere in the world.
Future developments for Ethernet-APL will expand the use of this technology into functional safety applications. There are substantial benefits to be gained from this approach, including the single-network technology, increased flexibility in plant design, and lower inventory requirements, because the same device could be used for safety and non-safety functions. BASF is already experiencing the advantages of digital measurement, like increased output and product quality, increased maintenance efficiency due to detailed diagnostic information, and increased plant availability. The organization is working with vendors to unlock the benefits of Ethernet-APL for functional safety, too [6].
Concluding remarks
Ethernet-APL is a rapidly expanding new technology that will shape the future of field data architecture. The high speed and bandwidth offered by Ethernet-APL enables digitalization initiatives like digital twins and predictive maintenance. The first APL devices are already available, and further APL devices for other measurements including flow, level, pressure and temperature, will be available this year. This means that projects using Ethernet-APL can be realized now.
Security for Ethernet-APL systems and devices will also continue to expand in future developments. Standards are regularly being updated to reflect new threats and to address gaps in the technology. As such, vendors will continuously be adding new security features to their devices and solutions over time.
Functional safety solutions are also under development, so that Ethernet-APL devices can be used for either safety or non-safety applications. This has several advantages for the industry, including the simplification of field networks into a single layer and the reduction in spares-holding requirements.
The simplicity of installation and the benefits of data integration from the field to the enterprise level makes Ethernet-APL a key technology for the future of the industry.
Edited by Scott Jenkins
Learn more about Endress+Hauser:
References
Authors
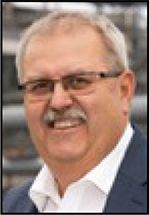
Gerd Niedermayer is the senior electrical and instrumentation (E&I) engineering manager in the Plant Engineering Department of BASF SE (Ludwigshafen, Germany; Email: [email protected]). Niedermayer graduated from the University of Karlsruhe with a focus on electrical systems and automation technology and then started working in the global plant engineering department of BASF SE as an electrical, instrumentation and control engineer. Shortly after, he was responsible for E&I engineering and execution of global plant engineering projects of BASF in Europe, North and South America and Asia.
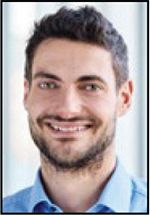
Benedikt Spielmann has a degree as M.Sc. in Business Administration and Engineering. He works as Marketing Manager Industrial Communication at Endress+ Hauser in Reinach, Switzerland. Since 2019, he has coordinated the Ethernet-APL activities within Endress+Hauser and is an expert in industrial Ethernet protocols like Profinet.