Commercial Progress on Turquoise Hydrogen
Producing hydrogen via methane pyrolysis – termed ‘turquoise hydrogen’ – has thus far received less attention than ‘blue’ and ‘green’ H2, but it may offer advantages over both
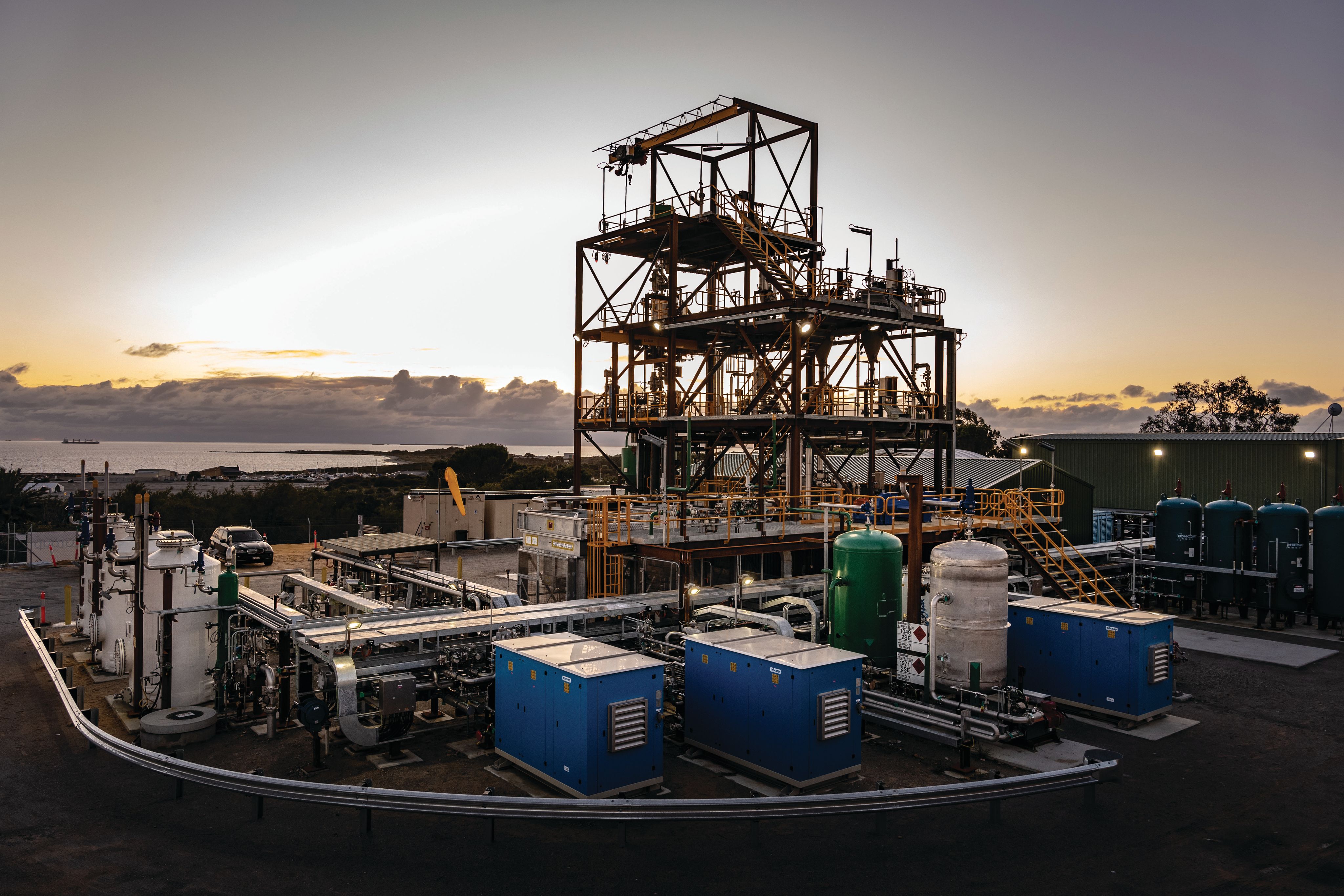
While the vast majority of current hydrogen production occurs by steam reforming of methane, there is an ongoing global effort to increase production of low-carbon hydrogen (hydrogen generated with minimal or zero associated emissions of carbon dioxide). The possibilities for low-carbon H2 include steam-methane reforming (SMR) coupled with carbon capture and storage (CCS) — known as “blue” H2 — and direct electrolysis of water using renewable energy — so-called “green” H2.
Another option for sustainable H2 production without CO2 emissions is methane pyrolysis (MP), the breakdown of CH4 bonds in the absence of air to form H2 and solid carbon. Known as “turquoise H2,” the set of processes being explored around methane pyrolysis have received less attention than green and blue hydrogen thus far, but the technique offers compelling benefits over the other two, including zero or minimal CO2 emissions with lower costs than green H2 and a potentially valuable co-product.
The article titled “Hydrogen Production via Methane Pyrolysis,” describes fundamentals of the methane pyrolysis reaction and some of the main technical challenges with producing H2 in this way. Here, the various approaches to commercializing turquoise H2 are discussed, along with the progress to date. “There are many ways to produce H2 by methane pyrolysis — all differing in terms of the heat-delivery mechanism, catalyst, process conditions and type of solid carbon produced,” says Chingis Idrissov, technology analyst at IDTechEx (Cambridge, U.K.; www.idtechex.com). “And now, a large number of players worldwide are developing this technology, including many startup companies and academic research groups, along with some large companies as well.”
Table 1 provides brief descriptions of several company-led and academic efforts in developing turquoise H2 processes, as found in recently surveyed literature and through contacts with technology developers. An expanded version of the table can be found in the online version of this article at www.chemengonline.com.

Commercial production
Emerging methane-pyrolysis technologies can be categorized by their approach to breaking down CH4. Among the methods are thermal and catalytic reactors employing plasma (hot, warm and cold), molten-media bubble columns, fluidized beds, moving beds and hybrid arrangements. Other developing technologies encompass compression heating using shock waves and pulsed-flow reactors, as well as chemical decomposition employing redox reactions.
Thermal plasma-arc reactor technology has the longest history of development and is the only one being commercially implemented at present. Monolith Inc. (Lincoln, Neb.; www.monolith-corp.com), widely considered to be the leader in commercial development of turquoise H2, purchased and further developed intellectual property from Kvaerner (now Aker Solutions) to produce H2 using a plasma-arc approach.
Monolith currently operates the first commercial MP facility for turquoise H2, known as Olive Creek 1 (OC1; Figure 1), in Hallam, Neb. The first-of-its kind commercial facility is designed to produce hydrogen and up to 14,000 metric tons of carbon black per year with virtually zero emissions from operations. Monolith will begin construction on Olive Creek 2 at the same site in 2024. The expanded facility will have 12 additional MP reactors. To allow for the expansion of clean H2 production, along with carbon black and NH3, Monolith received conditional approval for a $1.04 billion loan from the U.S. Department of Energy in December 2021.
OC1 has allowed the company to make significant improvements to the process prior to the planned scaleup in OC2. Monolith co-founder and CEO Rob Hanson says making the scaled up plant work reliably for commercially relevant periods of time required diligent work, but they company has made hundreds of tweaks to improve production. OC2 will add an ammonia plant that will make approximately 300,000 ton/yr of ammonia from the hydrogen generated.
Two major areas of focus at Monolith have been to develop a highly detailed understanding of the methane pyrolysis reaction, and to control the properties of the solid carbon to suit particular applications, while effectively controlling carbon deposition. “We’ve really been working at the forefront of science on the chemistry of methane pyrolysis, which is not fully understood,” notes Hanson. “Monolith engineers have worked with partners on shock tubes to probe the kinetics of the reaction. Careful investigation of reaction mechanisms and kinetics allows us to address the technical challenges of the process,” he says.
A large market for carbon black produced via MP is vehicle tire manufacturing, and Monolith has carefully engineered the process to control carbon deposition for commercially viable time periods, while also ensuring that the carbon black produced has the properties required by the tire industry, Hanson says.
In May 2023, Monolith and Goodyear Tire and Rubber Co. announced that Monolith’s carbon black will be used in an all-season passenger-vehicle tire. Tires containing Monolith carbon black have already passed U.S. Dept. of Transportation safety and performance testing. The tires will become available in Q4 2023.
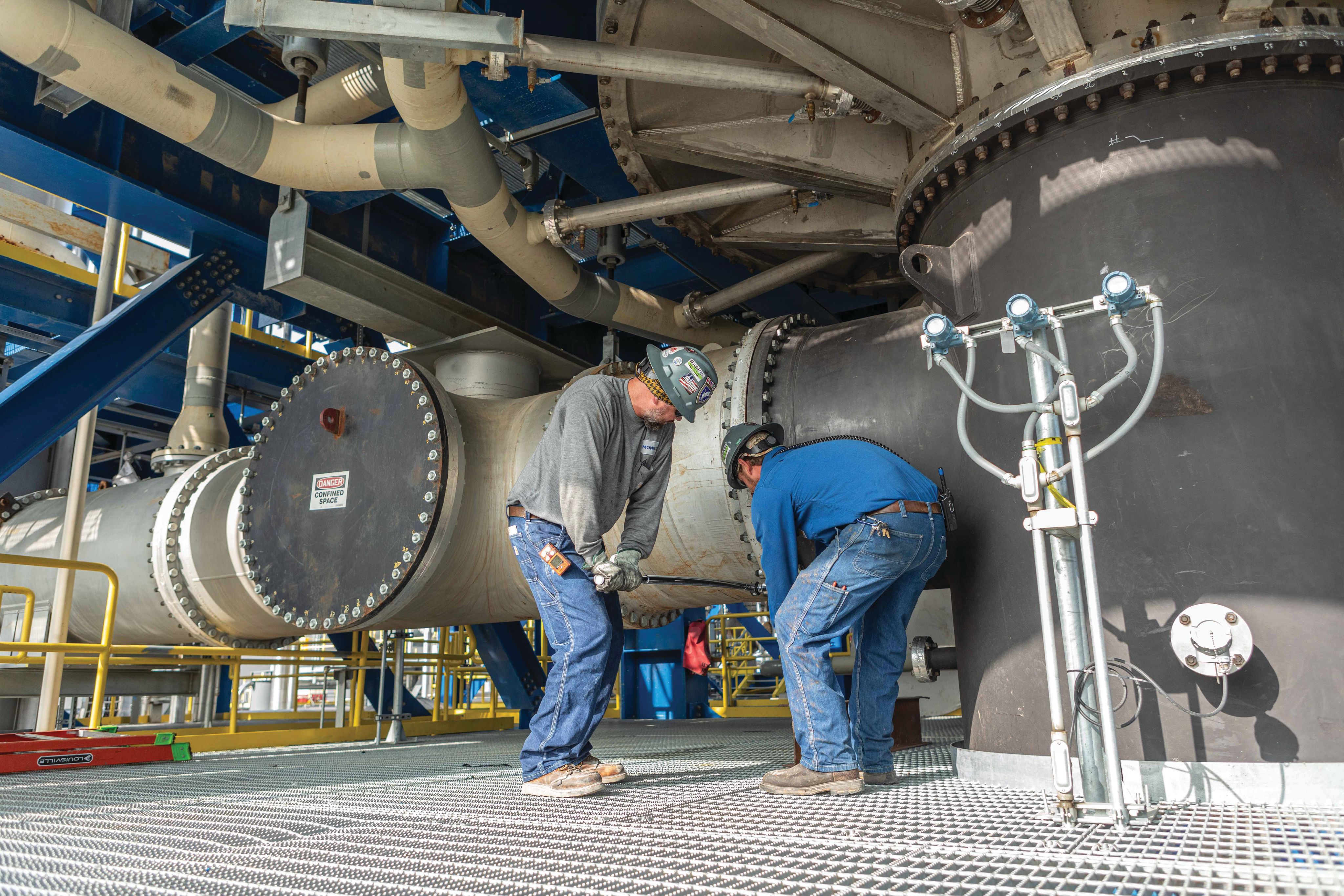
Figure 1. Monolith’s Olive Creek 1 facility is currently producing H2 and carbon black in Nebraska Photo credit: Monolith
Figure 1. Monolith’s Olive Creek 1 facility is currently producing H2 and carbon black in Nebraska Photo credit: Monolith
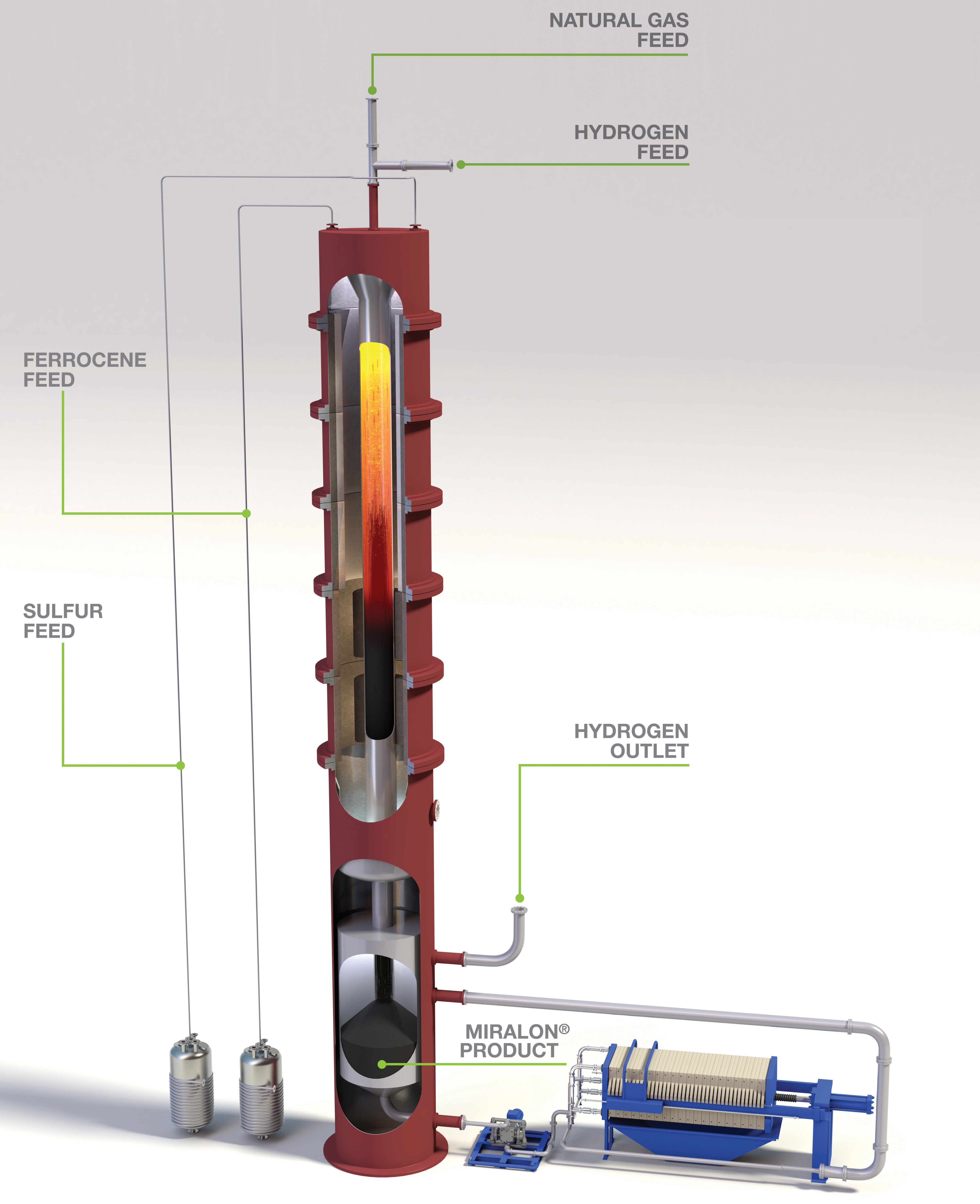
Figure 2. Huntsman’s Miralon process generates carbon nanotubes, which can be high-value additives for several applications. Photo credit: Huntsman
Figure 2. Huntsman’s Miralon process generates carbon nanotubes, which can be high-value additives for several applications. Photo credit: Huntsman
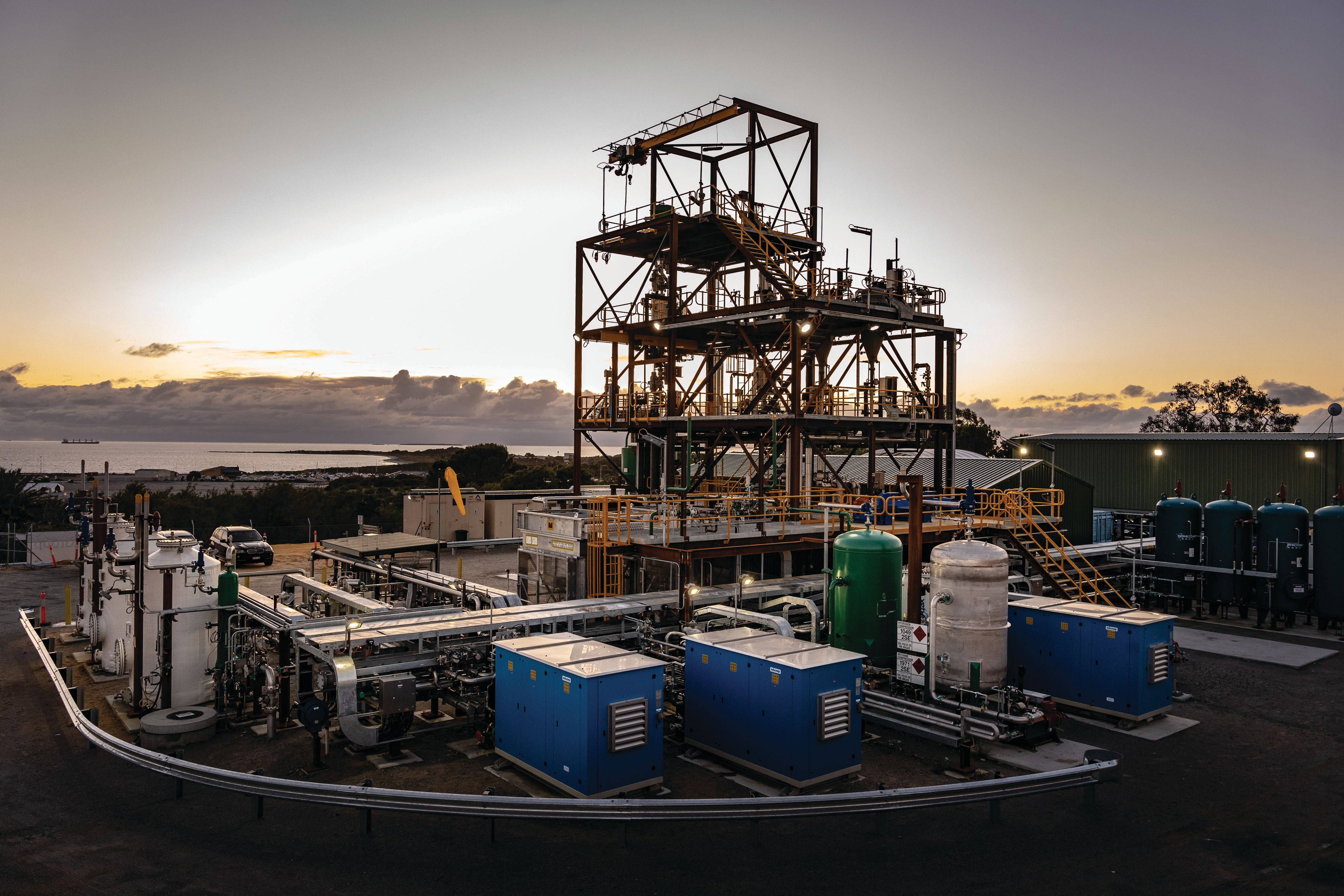
Figure 3. Hazer Group has developed a methane pyrolysis process that uses raw iron ore as a catalyst material. Photo credit: Hazer Group
Figure 3. Hazer Group has developed a methane pyrolysis process that uses raw iron ore as a catalyst material. Photo credit: Hazer Group
Catalytic reactor approaches
Other approaches to methane pyrolysis employ catalysts for breaking down CH4 and target the production of high-value forms of carbon, such as carbon nanotubes (CNTs), graphite and others. A number of companies are pursuing this route, including Hazer Group Ltd. (Perth, Australia; www.hazergroup.com.au), Hycamite TCD Technology Oy (Kokkola, Finland; www.hycamite.com) and Huntsman Corp. (The Woodlands, Tex.; www.huntsman.com).
Huntsman has developed the Miralon process using technology from Nanocomp Technologies, a New Hampshire-based startup it acquired in 2018. Miralon produces H2 and CNTs as a co-product. CNTs can be used as conductive additives for batteries and thermoplastics, and as mechanical performance enhancers for concrete, rubber and composites.
The Miralon process pyrolyzes methane in a high-temperature H2 atmosphere in the presence of an iron-based catalyst and adjuvant in a technique known as floating-catalyst chemical vapor deposition (FC-CVD; Figure 2). “The technique drives the CNT growth reaction in a flowing gas stream to avoid the complexities of fixed-bed systems,” explains John Fraser, commercial director for Miralon technology and material at Huntsman.
The pyrolysis reaction takes place at temperatures well above 1,000˚C. Raw materials are injected into the hydrogen atmosphere in carefully controlled ratios, using the heat to drive the pyrolysis. As the temperature of the gas flow cools, CNTs begin to grow as the free carbon interacts with the catalyst and adjuvant.
The energy to the reactors is delivered using electrical heating. When renewable electricity is available, the resulting H2 has a carbon footprint up to 95% lower than the current SMR reactors, says Fraser.
The iron “catalyst” used to generate Miralon CNTs is ferrocene, an organometallic compound. The adjuvant is a sulfur compound. Academic studies are underway to examine alternative catalysts, which could potentially increase the carbon-conversion efficiency. “By carefully controlling the stoichiometry of the reactants, as well as temperature and flowrate, the Miralon process preferentially forms CNTs over other carbon forms,” Fraser explains.
The reactor uses proprietary methods to keep the carbon away from the reactor walls as much as possible to prevent deposition, he says.
A unique aspect of FC-CVD is the way the product aggregates in the gas phase as it proceeds through the reactor. “It forms a ‘sock,’ or aerogel, which flows to the reactor exit for collection. The collection process collapses the aerogel, degassing the product and gradually reducing temperature of the carbon,” Fraser says. Once the entrapped gas has been removed, the solid carbon is collected using a proprietary technique.
Miralon CNTs form elongated bundles, rather than individual tubes, and aggregate more than other CNTs. These interconnected bundles give rise to the electrical and thermal conductive properties and deliver improved mechanical properties. Huntsman says the main advantage of the Miralon process over other turquoise H2 approaches is the properties and value of the carbon product.
Miralon facilities can be co-located where H2 is used, eliminating transport costs, and sales of CNTs reduce the net cost of the H2, Fraser says.
He notes that pilot-plant installation is ongoing and is expected to be completed in late 2023. After optimization at pilot scale, Huntsman plans to build a commercial-scale plant, producing kiloton amounts of both Miralon CNTs and H2. This larger facility is expected to constructed for operations in 2025–2026.
In the case of Hazer Group, research focused on a low-cost, readily available catalyst: raw iron ore, ground to a specific particle size fraction and moisture content. The basic process configuration involves feed gas preheat, followed by injection into the reactor. “Iron ore catalyst is also injected into the reactor and is first reduced predominantly by H2, then cracks methane into H2 and carbon,” explains Hazer chief technical officer Tim Forbes. “The carbon dissolves in the iron catalyst until it super saturates and precipitates as graphite.” Graphite and H2 are cooled and separated with conventional cyclone and filtration technology.
“The catalyst promotes pyrolysis at lower temperatures than would be achieved thermally,” Forbes says. “Lower-temperature pyrolysis reduces the risk of reactor-wall carbon formation compared to other thermal processes.” Although H2 production costs will be location-specific and driven by gas and power prices, Forbes says Hazer expects to be competitive with H2 production via SMR+CCS, and expects to produce H2 at lower costs than electrolysis, due to drastically lower energy required to split CH4 compared to H2O.
Hazer reports that it is nearing the final stages of construction on its commercial demonstration plant, which is anticipated to start up this year (Figure 3). The plant will allow Hazer to validate the performance of its commercial-scale reactor design, and to produce sufficient quantities of graphite for product-qualification activities for applications such as steel production, water purification, batteries, thermal energy storage, and concrete and asphalt blending, Forbes says.
Meanwile, Hycamite has developed its own family of proprietary catalysts that allow the production of H2 and what the company calls TCD Carbon, a mixture of carbon nanofibers and CNTs, using a carbon-neutral thermocatalytic process that operates at lower temperatures than other pyrolysis processes. Hycamite’s process involves gas pretreatment, followed by a reactor for methane breakdown, as well as gas circulation, catalyst regeneration processes, filtration and carbon processing. Hycamite founder Matti Malkamäki says “We have had a pilot plant operational for more than two years, and are now building an industrial-scale demonstration unit with a nominal capacity of 2,000 ton/yr of H2.” Hycamite recently announced an agreement with NW Natural, a gas utility in Oregon, under which the company plans to replicate the demonstration unit in the U.S.
Alternative approaches
Ekona Power Inc. (Burnaby, B.C.; www.ekonapower.com) has taken a different approach. Ekona’s patented xCaliber reactor uses the energy from combustion to dissociate feedstock methane into H2 and carbon. Products of combustion are injected directly into the feedstock chamber to drive the needed heat transfer, temperature and pressure for pyrolysis.
The result is a reactor design that is catalyst-free, low-cost, scalable, and mitigates carbon fouling, according to Gary Schubak, Ekona vice president of business development. The company is currently executing a multi-year development program that will commercialize the technology later this decade. “We have already built and tested a proof-of-concept reactor to validate the design,” he says. “Now, we are testing a scaled-up (~200 kg/day H2) reactor at our facility, which is integrated with key system components for carbon separation, H2 purification and thermal management.” In 2024, Ekona plans to scale up to a 1-ton/day of H2 pilot plant with five reactors working together. Ekona’s technology targets large industrial applications requiring 100–300 ton/d of H2 or more. It can be deployed wherever there is natural gas infrastructure, since it does not rely on water, clean electricity or CCS.
Schubak notes that Ekona carried out techno-economic analyses of the process from the beginning to ensure the technology scales and meets industry’s priorities. “We believe our solution can produce turquoise H2 at costs comparable to conventional grey-H2 processes, while significantly reducing greenhouse gas emissions. Selling the carbon and taking advantage of clean H2 incentives can significantly improve economics.”
Other technologies that are nearing pilot or demonstration stage include molten-media processes, such that from C-Zero (Goleta, Calif.; czero.energy), a chemical redox process from ETCH Inc. (Baltimore, Md.; etchmaterials.com), a plasma torch with molten-metal reactor (HiiRoc; Hull, U.K.; www.hiiroc.com), and a moving-bed reactor (BASF; see Table 1).
The ETCH process employs Ni-based redox reactions and is projected to produce H2 at $1.00–1.50/kg of H2 without any carbon sales or carbon offsets revenue, which compares favorably to SMR. The process has a high H2 yield (>99%), voiding the need for H2 purification and hydrocarbon recycle.
The molten-media bubble-column reactor design by C-Zero employs an external chamber filled with molten salt to combust H2, thus generating heat for the pyrolysis reaction.
TNO Netherlands (The Hague, the Netherlands; tno.nl) is an example of a research-stage, laboratory-scale project using molten metal. The TNO process uses dry-reforming to obtain synthesis gas, from which olefins and sustainable aviation fuel can be made. A key hurdle with molten metal is preventing carbon contamination of the metal. TNO has developed a molten-salt wash section that removes metal from the solid carbon.
Looking forward
Green, blue and turquoise H2 processes will likely each work better under different sets of circumstances, conditions and geographic regions, and all three types will continue to develop and be deployed, but in the opinion of Monolith’s Hanson, turquoise H2 is the most broadly applicable approach to making H2 and carbon with minimal CO2 emissions.
Research groups and institutes will continue to be highly involved in the methane pyrolysis space, with new spin-outs from research groups expected to emerge in upcoming years, says IDTechEx’s Idrissov.
For additional information on the commercial development of turquoise H2,, see below.
Scott Jenkins and Carl Fromm
MP benefits and drawbacks
Turquoise H2 processes exhibit a host of benefits over alternative hydrogen production routes, but also have some challenges. Methane pyrolysis produces no direct CO2 and requires only 59% of the reaction heat needed by the incumbent SMR process, and only 13% of the reaction heat needed for H2 production via water electrolysis. While SMR releases 8-12 kg CO2 per kg of H2 produced, turquoise H2 processes would generate less than 1 kg CO2 per kg H2 using conventional grid electricity and zero CO2 emissions if using renewable electricity. The use of biogas or renewable natural gas as a feedstock could make the process carbon-negative.
MP processes also generally are able to operate with flexible feedstock compositions, because high temperatures enable pyrolysis of other light hydrocarbons present in natural gas (ethane, propane). Further, MP processes are thermodynamically much less energy intensive than electrolysis. “Some players report up to seven times lower electricity consumption than electrolysis per mole of H2 produced, leading to lower operating expenses,” says Idrissov.
Another potential benefit of MP processes is the generation of potentially valuable carbon co-products. Specialty carbon black, carbon nanotubes, graphite and other carbon materials can be produced, along with hydrogen, to provide an additional potential revenue stream. And finally, MP processes could lend themselves more to modular assembly than blue hydrogen plants, so they may be able to be placed close to or on the customer site.
Among the potential drawbacks are that the methane pyrolysis reaction is endothermic and slow, often requiring relatively long residence times to achieve acceptable CH4-to-H2 conversion yields. Further, reactor approaches need to avoid fouling by carbon deposition and require effective solids handling for the carbon. The electricity requirement per ton of H2 product is still higher than for traditional SMR (without CCS). In addition, in some areas, such as Europe, natural gas supply is a concern.
Hydrogen production via MP is not yet at cost parity with traditional SMR, but is expected to compete with blue H2 after further commercialization, explains Idrissov from IDTtechEx. Many technologies are less developed than blue H2, so there is still a need to prove the turquoise H2 projects at large scale. The nature of the carbon black product also has questions, such as “can demand and offtake agreements materialize for carbon, especially if it is of lower grade?” “Further optimization of reactor conditions and separation systems for solids is needed,” says Idrissov.
Process economics
The cost of turquoise H2 produced by methane pyrolysis is currently $1.80-4.00/kg H2 without any carbon sales or revenue from carbon offsets. This is not yet cost-competitive against grey hydrogen produced by SMR ($0.90 to 3.00/kg), but may compete with blue hydrogen ($1.40 to 2.50/kg). Newer technologies, such as ETCH, promise to produce hydrogen at $1.00-1.50/kg. Commercial success of MP technology is highly dependent on the ability to sell carbon co-products into existing and emerging markets, and to take advantage of carbon offsets or carbon tax avoidance.
New markets for solid carbon
There are several possible avenues for carbon co-products produced by turquoise H2 processes.
• Carbon black. The market for carbon black is now 17 million ton/yr and growing at 4% per year, so there is room for a substantial amount of carbon from methane pyrolysis, according to Monolith’s Hanson.
• Carbon nanomaterials. These currently sell at more than 10 times the market price of carbon black and include CNTs, carbon fibers, and graphene which are used as filament or filler for lightweight structural polymer composites, high-performance building and paving materials, longer-lasting tires, and as battery electrodes.
• Metallurgical coke. Carbon from methane pyrolysis processes could replace metallurgical coke derived via coal pyrolysis for pig iron and steel production.
• Soil amelioration. Amorphous carbon can be added to soil to promote seed germination, slow release of fertilizers, growth of microbial population, water retention, UV protection, and atmospheric CO2 sequestration.
• Concrete. Use of carbon in electrically conductive concrete for snow and ice melting pavement, cathodic protection systems, electromagnetic shielding, structural health monitoring, and traffic detection.
• Road asphalt. Use of carbon in road asphalt to improve strength and reduce UV degradation and related organic vapor emissions.
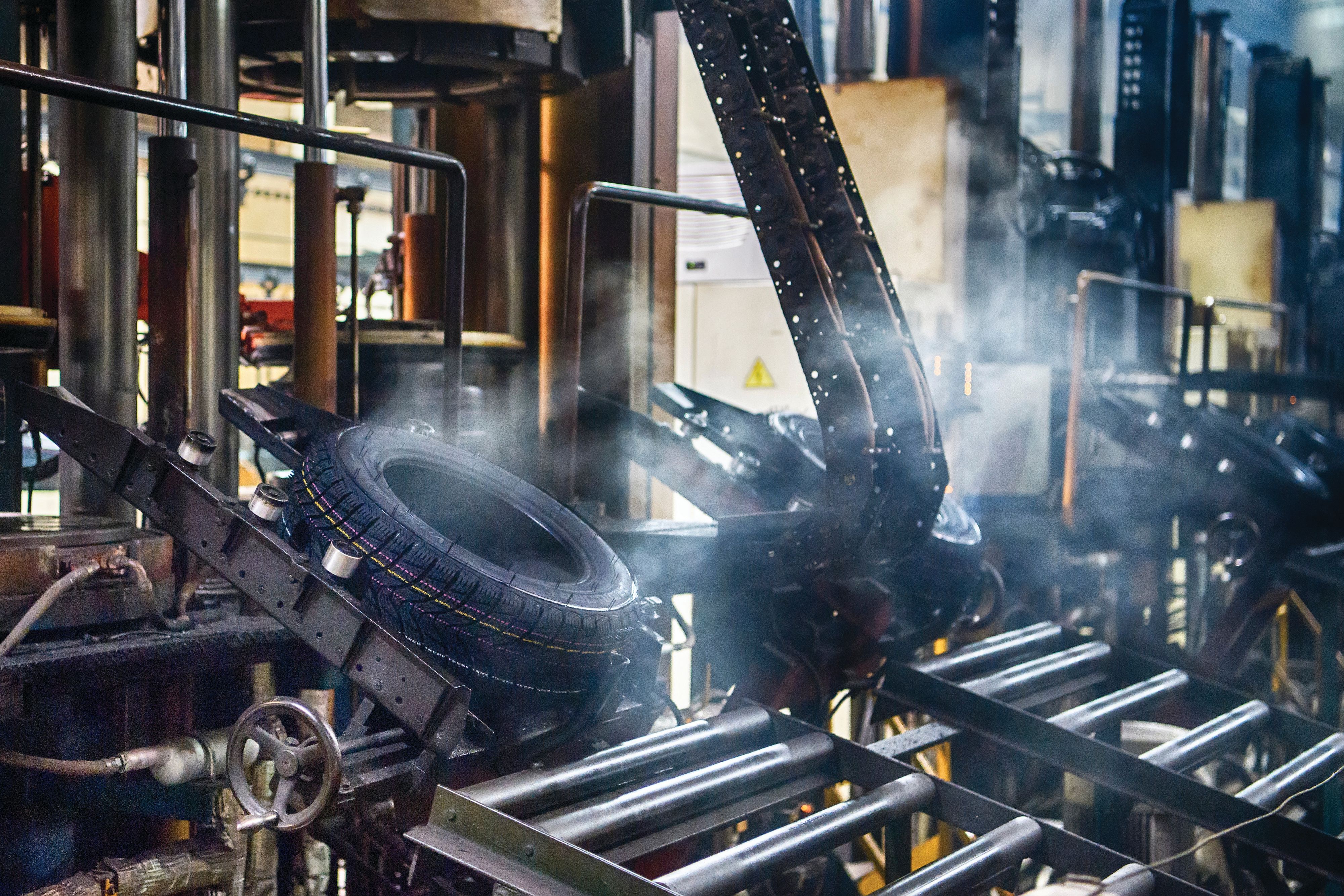
Figure 4. Tire manufacturing is a key market for carbon black produced via methane pyrolysis
Figure 4. Tire manufacturing is a key market for carbon black produced via methane pyrolysis
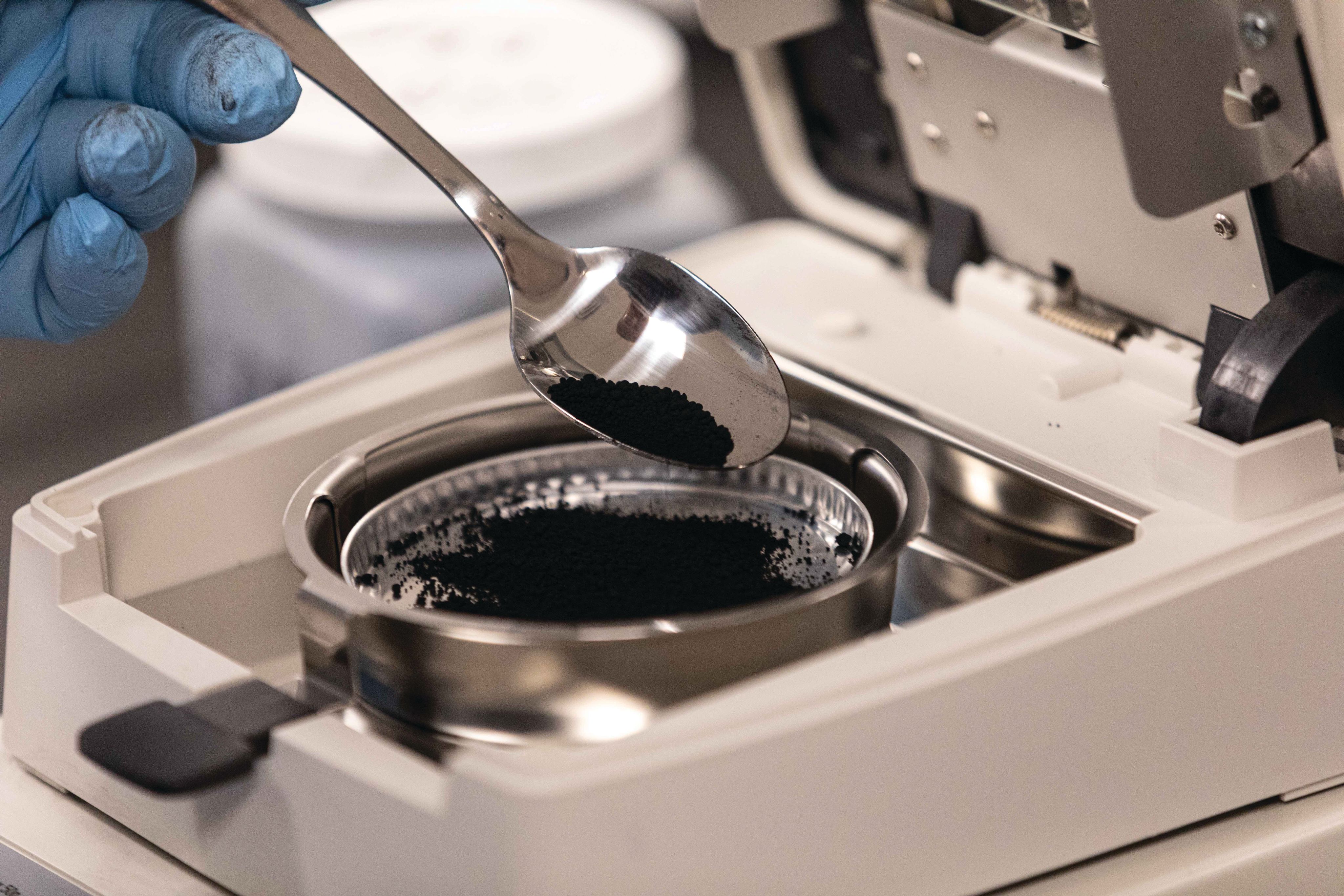
Figure 5. Carbon black needs to have specific properties to be used in vehicle-tire applications
Figure 5. Carbon black needs to have specific properties to be used in vehicle-tire applications
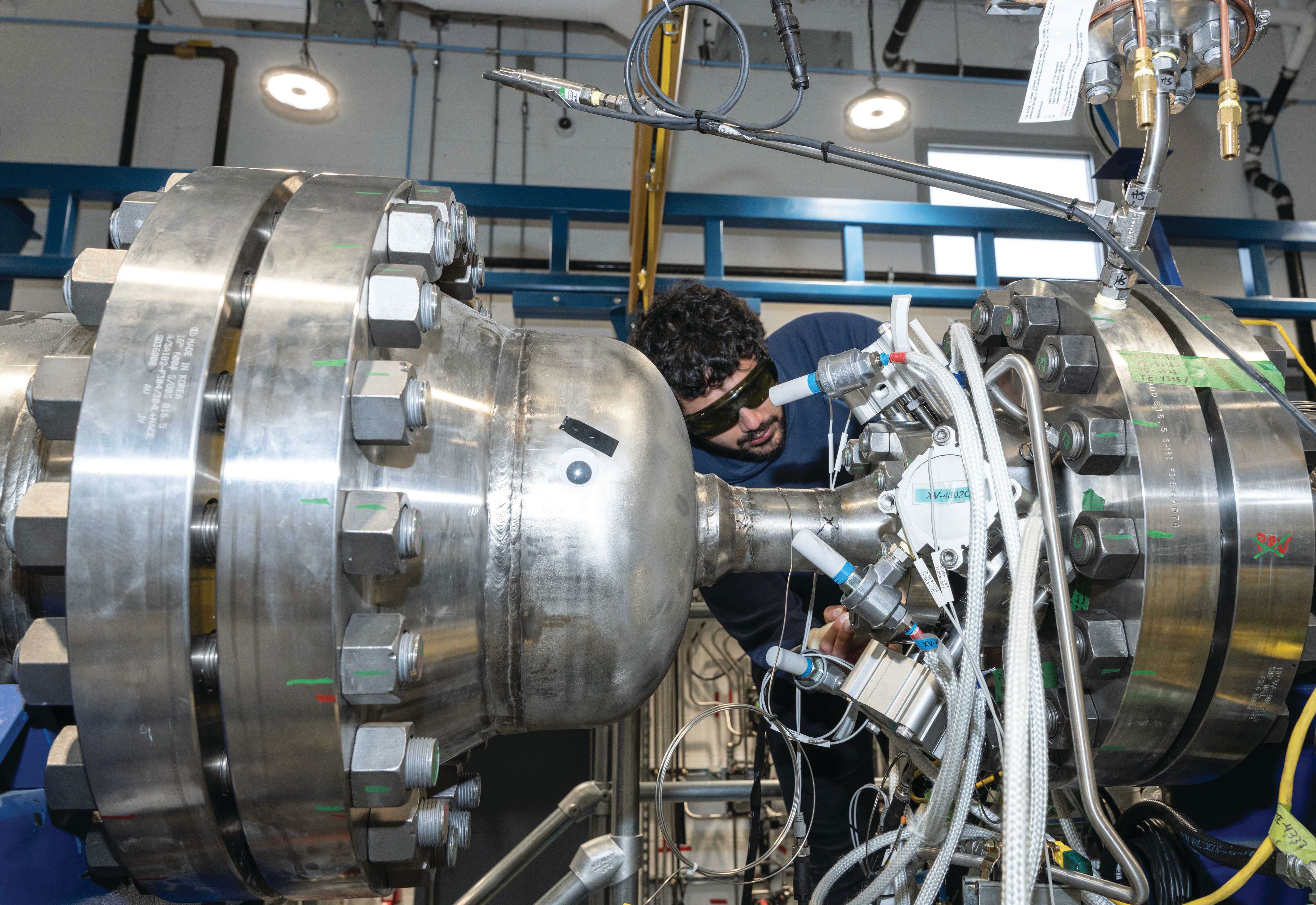
Figure 6. Ekona's methane pyrolysis technology uses pulsed combustion to break down methane molecules
Figure 6. Ekona's methane pyrolysis technology uses pulsed combustion to break down methane molecules
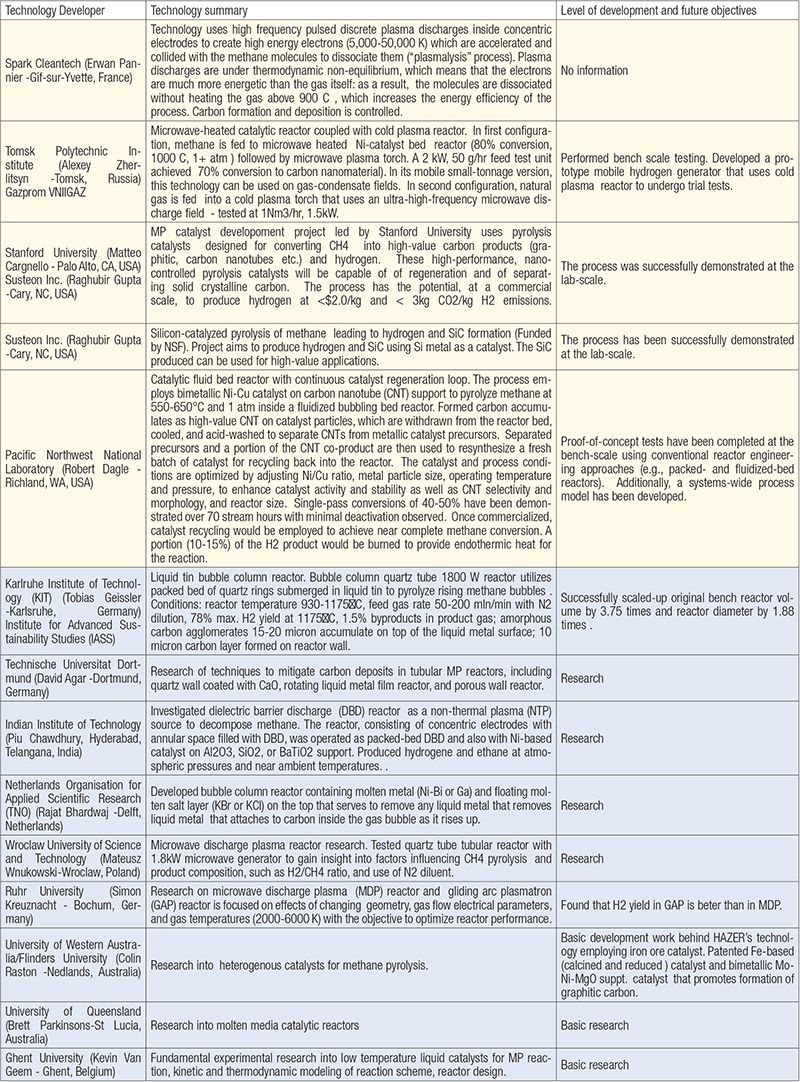
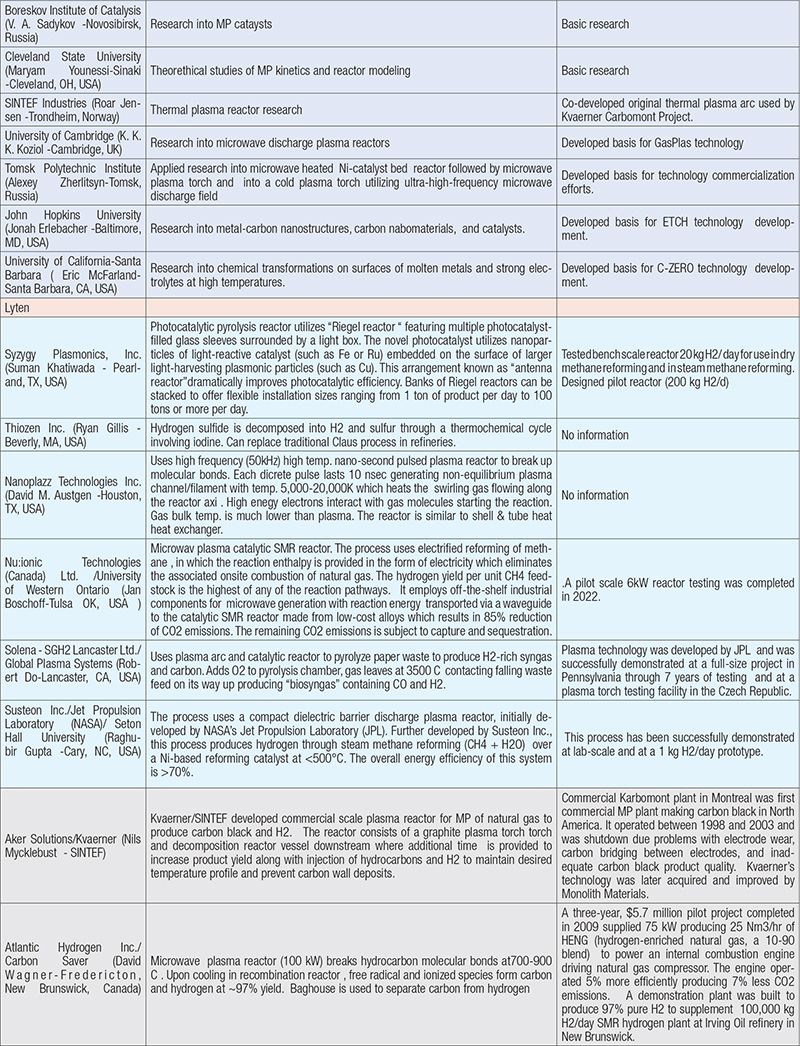
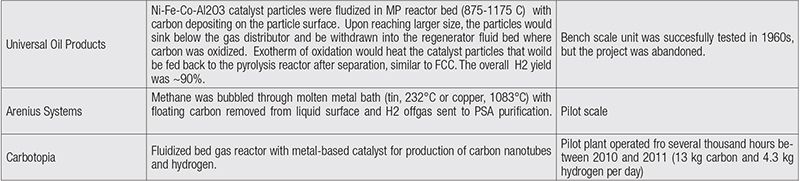