Presented here is a fast and flexible solution that removes solids, traces of water and gel in a single operation, therefore significantly reducing the time it takes to perform the process during silicone production
Reliable silicone manufacturing operations depend on a complex network of process technologies, including, among other things, the removal of solids as well as traces of water and gels from the intermediate silicone product. Traditionally, this activity has been a two-stage operation. However, there is a single-stage filtration technique that combines the removal of solids, water and gels that can enable a manufacturer of silicone products to streamline its production activities and enhance operational efficiency.
Silicone products
Specialty silicones are used in a broad range of industries. From adhesives to aerospace, textiles and transportation, different types of silicone are crucial to numerous production processes. Silicones are contained in a wide variety of end-user products — cosmetics, toiletries, lubricants, adhesives and protective coatings, to name a few.
To meet such widespread applications, silicone products come in many different grades, being produced at highly integrated manufacturing plants that use multi-stage processes to deliver consistency and repeatability. The manufacturing process is complex and carefully refined. Silicates in sand or rock are first processed to obtain silicon. Chemical reactions then produce silanes (any of a series of covalently bonded compounds containing only the elements silicon and hydrogen) and, in further steps, polysiloxane precursors (a group of silicon-based polymers), which are the basis for different grades of silicone products.
These precursors contain a silicon-oxygen backbone along with other organic components, and can be processed into silicone oils, resins and elastomers, among other materials. The composition of silicone offers several desired performance characteristics, such as thermal and oxidative stability, chemical inertness and excellent dielectric strength.
Silicone production processes
During the production process, which involves hydrolysis of organohalosilane (carbosilanes derivatized with a hydroxy group on the silicon atom [1]) and condensation of chemical compounds forming salts, among other things, silicone manufacturers have to ensure that any unwanted residues and particles are removed, to protect the quality of the finished product. This requirement is met through the use of advanced filtration techniques, which have to be performed without having any adverse impact on volume throughput on the production line. Filtration has to be carried out to exacting standards, using equipment that is reliable and easy to maintain.
Stringent production techniques
One of Europe’s silicone manufacturers came to Eaton Corp. (Bloomfield, N.J.; www.eaton.com) with a requirement for a more effective means of carrying out solid separation, as well as liquid traces separation at one of its large production plants. The company was producing about 6,614 lb of intermediate silicone oil at 22 gal/min on a regular basis. The production process involved a carbonation technique using sodium carbonate to neutralize hydrochloric acid. This process resulted in the generation of water residue and solids that need to be removed in an effective way. Failure to do so can increase the viscosity of the final product through the creation of gel in the silicone — identified as a highly undesirable outcome.
Historically, a two-stage process is used. In this process, solids are separated from the silicone intermediate, and water residues are removed using chemical additives. However, the silicone manufacturer wanted to implement a more advanced system that could offer highly controllable removal of solids, traces of water and gel particles in a single-stage operation. By implementing such a unique approach, the company would be able to simplify its production processes, saving time and reducing by-product waste.
Single-stage filtration process
Engineers from Eaton’s Filtration Division forged a strong customer relationship with the silicone manufacturer, working with its technical team to devise an effective solution. The answer came with the combination of BECO depth filter sheets, fitted to a BECO Compact Plate plate-and-frame filtration system, allowing for the removal of nearly all water residue and solids through adsorption, without causing any significant pressure drop on the production line.
In laboratory tests with different types of depth filter sheets, an optimized solution was jointly developed. BECO depth filter sheets have a nominal retention rate ranging from 0.1 to 40µm, and the analyses identified BECO KD 7 depth filter sheet (Figure 1) as the most suitable grade for the task at hand. In terms of specific performance characteristics, it has a nominal retention rating of 1.5µm, making it suitable for filtration of highly deformable particles. The tests showed that the use of 108 ft² of this depth-filter sheet could effectively filter about 6,614 lb of the initial product with approximately 154 lb of cake and less than 2% of residual water.
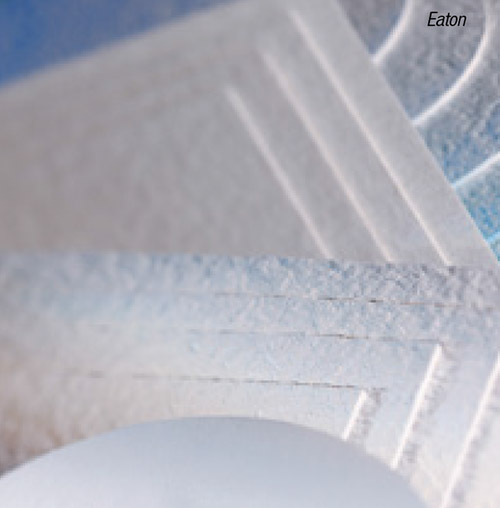
FIGURE 1. BECO KD 7 depth filter sheets consist of finely fibrillated cellulose fibers from deciduous and coniferous trees that provide an especially high water-retention capacity
Such an excellent level of performance was a result of the specific composition of the BECO KD 7 depth filter sheets. This product range is made of pure natural materials and cationic charge carriers. It combines finely fibrillated cellulose fibers from deciduous and coniferous trees with precisely dosed quantities of high-quality diatomaceous earth. A key property of the cellulose fibers is the water absorption capability. In addition, the ideal pore structure of the depth filter sheet allows a reliable retention of gel particles. This enables the BECO KD 7 depth filter sheet to provide the optimal ratio of performance and throughput.
The depth-filter sheets need to be inserted in a reliable filtration system. After assessing available options, the company selected the BECO Compact Plate A600 system (Figure 2). This multi-sheet filter system comes with either an electrically or pneumatically operated hydraulic system.

FIGURE 2. The BECO Compact Plate A600 premium multi-sheet filtration system enables silicone manufacturers to increase their product quality and reduce downtimes
Quality was an important consideration for the silicone company. The company wanted a reliable filter system that would not cause any unnecessary downtime. This requirement was met through the use of a solid chassis design, with robust filter frames, that ensure that the hydraulic pressure is effectively directed onto the depth-filter sheets. The components of the system are designed to withstand maximum operating temperatures of 249.8°F (121°C), ensuring reliable performance even during extended periods and at high temperatures. The silicone manufacturer also needed a solution that was flexible enough to fit within the restricted space parameters of its production line. The BECO Compact Plate A600 filtration system met this requirement too, offering a highly flexible filter area from 7.10 to 745.94 ft², which allows for customizable solutions for individual applications.
Ease-of-maintenance was also placed high on the specification list. An automatic re-tightening function monitors the actual tightening pressure during operation, because once the depth filter sheets become wet, their thickness deviates, so the system needs to re-press to ensure leak-tight performance. The BECO Compact Plate A600 filtration system can detect changes immediately and automatically adjusts the hydraulic pressure if it falls below a threshold value. Meanwhile, ease of handling and excellent cleanability is achieved thanks to ergonomic design and the use of smooth surfaces. At the same time, a wide range of accessories, such as fittings and riser pipes, meant the system was ready for quick and secure connection.
Enhancing production efficiency
From the outset, the silicone manufacturer wanted to implement a filtration operation that could remove solids, traces of water residues and gel particles in a single-stage process. This has been successfully achieved with the combination of the BECO KD 7 depth filter sheets and the BECO Compact Plate A600 multi-sheet filter system. Now, solids, water residues and gel particles can be reliably removed in a much shorter space of time than was previously achievable with the two-stage process.
According to Fabrice Doignie, regional sales manager — EMEA within the fine chemical and pharmaceutical sales unit of Eaton’s Filtration Division, the project represented a hugely successful collaboration between the technical teams at Eaton and the silicone manufacturer, delivering an excellent result. “It was all about meeting the customer’s exacting requirements,” Doignie says. “The laboratory screening tests showed that the BECO KD 7 depth filter sheets offered just the right level of filtration, meaning that effective removal of water residues and solids could be achieved at specific volume and flowrates. Meanwhile, the flexibility of the BECO Compact Plate system meant that we could adapt the size of the frames to meet the specified dimensions of the production line. In both cases, the depth of Eaton’s product range and the skills of our people meant that we were able to meet the customer’s requirements. The project was a true testament to the power of partnership.”
Since the installation, Eaton and the silicone manufacturer have forged a successful business relationship, with the company now using other filtration products from Eaton within its production facilities. These include Becopad depth-filter sheets, Becodisc stacked-disc cartridges, and Becodisc activated carbon stacked-disc cartridges. “In each case, we have worked with the customer’s development team to provide a solution,” Doignie adds. “Ultimately, Eaton has become more than just an equipment supplier. We are now viewed as a manufacturing partner that provides valuable input into production processes, using our engineering knowhow to suggest technology solutions that deliver true added value.”
Looking to the future, Eaton believes that the specific properties of the BECO KD 7 depth filter sheet mean it is sure to find further application in the silicone manufacturing industry. “It is a truly unique product solution,” Doignie confirms. “The ability to remove water quickly and reliably from another liquid is a highly desirable characteristic. That means we are confident of applying this technology in other production facilities and other market segments across Europe and further afield.” ■
Edited by Gerald Ondrey
References
1 IUPAC, “Compendium of Chemical Terminology,” 2nd ed. (the “Gold Book”), 1997. Online corrected version: https://doi.org/10.1351/goldbook.S05664