Rupture disks are non-reclosing pressure-relief devices that protect vessels, such as reactors, from damaging over-pressurization (or vacuum) conditions. Temperature can affect rupture-disk burst pressures in ways that users should understand before ordering them (Figure 1). This one-page reference provides an overview of the issues that temperature effects can cause for rupture disk selection and performance.
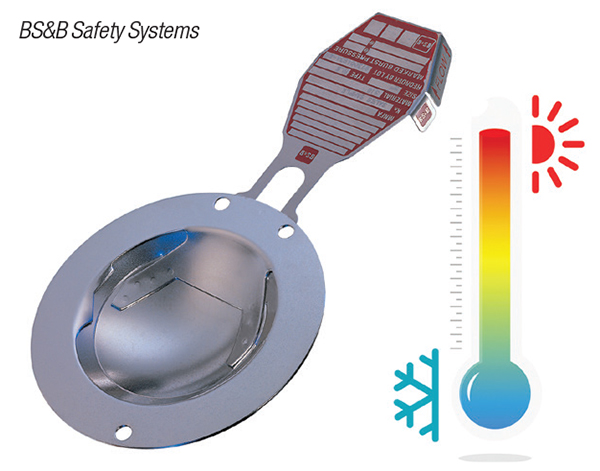
FIGURE 1. The environment on either side of the rupture disk determines the coincident temperature
Rupture disks are available in various designs, sizes, shapes and set pressures. Reverse-buckling rupture disk designs are generally the first choice for overpressure protection because they have greater longevity, accuracy and reliability over time. Reverse-buckling rupture disks are also designed for non-fragmentation, which is recommended when using rupture disks to isolate downstream pressure-relief valves from a process. When used in this way, rupture disks typically allow for higher operating pressures while ensuring inlet-side leak tightness, lower valve maintenance expenses, and frequently the use of lower-cost valve trim.
Coincident temperature
Prior to ordering a rupture disk, design engineers must specify several characteristics of the disk to satisfy the overpressure protection requirement. One of these is the specified temperature of the disk, often called the “coincident temperature.” This term is defined as the stable temperature of the rupture disk when it is required to activate (burst).
Since a rupture disk is typically manufactured from metal foils, the environment on either side of the disk determines the coincident temperature. While a precise temperature can be difficult to determine, the relief-system design engineer should consider the conditions on either side of the disk and specify the disk at a temperature as close to the coincident temperature as possible.
For rupture disks to meet the requirements of consensus standards, burst-pressure accuracy is validated through destructive testing of samples from a batch (lot) of disks that are manufactured from the same material at the same time and at the temperature specified for that particular rupture disk description. If the stable temperature of a disk at the time of rupture is not properly selected, the disk is incapable of bursting at its marked burst pressure.
Specification errors
Designers often erroneously specify the disk temperature at the “flowing temperature” of the discharged media. That value is rarely correct and is usually the result of “relief-valve mentality” — the rupture disk doesn’t “care” what flows through it … only the environment and conditions that exist when it bursts. It is likewise inappropriate to specify the rupture disk at the process operating temperature or ambient (72°F or 22°C) temperature.
If the disk is specified at a temperature higher than its true coincident temperature at the time of activation, that rupture disk should be expected to activate at a pressure higher than its marked burst pressure, possibly creating an unsafe condition. If the disk is specified at a temperature lower than its true coincident temperature, it will typically activate below its marked burst pressure, resulting in unnecessary lost production time. For example, if a disk is installed 20 feet downstream of the process, past two elbows, the intervening pipe acts as a heat sink, and the coincident disk temperature is significantly below the process temperature.
On the other hand, a rupture disk specified at a dramatically lower temperature than the true coincident temperature, or if the process encounters considerably higher temperature than the specified temperature of the rupture disk, the high-temperature environment can actually “stress relieve” the disk, resulting in a permanent shift in the temperature/burst pressure curve. Occasionally, that condition can result in disks activating critically higher than the marked burst pressure of the lot (batch). Accordingly, in addition to the specified temperature of the rupture disk, the maximum operating temperature of the process should be communicated to the manufacturer to ensure thermal stabilization of the rupture disk up to and including the maximum exposure temperature while in service.
The deviation from the marked burst pressure of a disk resulting from improperly specified coincident temperature is a function of the type (model) of the disk, as well as the material(s) of construction.
Since almost all rupture disk designs have more than one manufacturing variable, the temperature influences on burst pressure alone cannot be accurately predicted. Additionally, each “batch” of material has slightly differing mechanical properties, which significantly limit the reliability of standardized temperature correction data for any given rupture disk type and material.
Disks may be tested at two or more different temperatures (upon request) and documentation accompanying the disks may show the burst pressures at temperatures other than those defined as the specified temperature. However, for rupture disks to comply with the relevant ASME code, the specified coincident temperature of the rupture disk and corresponding pressure can only be marked at one temperature. Any additional temperature testing and corresponding burst pressures determined and validated is not specifiable and will not appear on the rupture disk tag as a marked burst pressure.
Department Editor: Scott Jenkins
Editor’s note: the material contained in this column was contributed by Steven S. Palmer, BS&B Safety Systems, LLC (Tulsa, Okla.; www.bsbsystems.com).