Milling is commonly used for particle-size reduction and control of particle-size distribution (PSD) for crystalline solids. Mills are effective for generating consistent solids properties, through size reduction and surface-modification mechanisms [1]. This one-page reference outlines the mechanical forces involved in size reduction and the important material properties for selecting milling equipment.
Forces for size reduction
In comminution, solids are fractured by mechanical force delivered to particles by the milling machine. This is achieved in a myriad of ways, depending on the mill type. Seven different types of stresses can be imparted to achieve size reduction, as listed below [2]:
1. Compression between two rigid surfaces
2. Compression between two rigid surfaces and against an adjacent bed of solids
3. Shearing (tearing, cutting, shredding and cleaving) mechanically
4. Shearing forces due to surrounding media
5. High-velocity impact against a rigid surface (particle impacting a stationary surface or a moving surface impacting a particle)
6. Particle-particle impact causing breakage and shattering
7. Abrasion during particle-wall and particle-particle impacts
Desired performance of size reduction can be achieved by matching the machine design with particle properties and mode of operation.
Key material properties
The following properties of the material must be evaluated for suitable selection of equipment and to understand its size-reduction behavior.
• PSD in the feed material
• Particle shape
• Bulk density
• Flowability, cohesiveness or adhesiveness
• Corrosivity and composition
• Moisture content
• Hardness, brittleness, friability
• Toxicity
• Abrasiveness
• Shock sensitivity or explosivity
• Elasticity, plasticity ductility
• Dust-explosion characteristics
• Temperature sensitivity — degradation, stickiness, phase change
• Fibrous morphology
• Oil or fat content, especially those released during grinding
• Reactivity or release of gases
• Stickiness
Milling equipment
The choice of milling equipment for an application depends on the performance capabilities relative to the properties of the feed material, as well as constraints of the mill type.
Broadly, mills can be separated into wet and dry mills, and these two categories are each further subdivided by how comminution is achieved, such as rotor-stator mills, jet mills, pin mills, hammer mills, media (ball) mills and cavitation mills. Wet mills use liquid as their working fluid, whereas dry mills use gas. Figure 1 (adapted from Ref. 2) shows how various milling techniques are categorized. Each type of mill is characterized by an energy input mechanism.
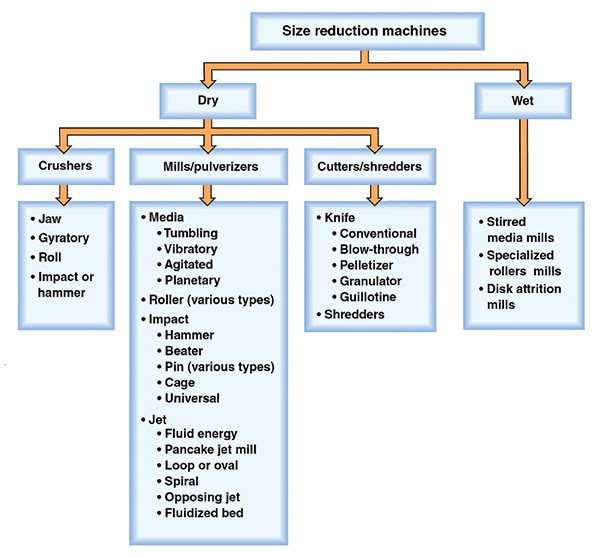
FIGURE 1. Milling technologies are divided into wet and dry methods and impart a range of forces on solid particles
Effects on solids properties
Milling processes have several general effects on solid particles. Several are outlined here:
Particle size reduction. The mechanical forces imparted by the mill reduce particle size.
Particle-size distribution changes. Generally, milling results in narrower PSDs, and is intended to provide normalization (a similar size distribution of product is obtained for various size distributions of feed materials). Theoretically, a milled product is predicted to have a log-normal or Weibull distribution, a probability distribution best fit by a function with two or more parameters [1]. The function is related to the probability of a particle fracturing and the nature of the fragment as a function of its original size. Practically speaking, this means that milling does not typically give symmetrical Gaussian distributions. Skewness and tails are common.
Increased surface area. Milling generally increases total surface area as solid particles are broken.
Surface property changes. Particle surfaces are altered as solids are milled, and this can affect how particles behave with regard to mixing, compacting, dissolving, aerosolizing and interacting with moisture.
Particle shape changes. Milling also impacts particle shape, or morphology, particularly for high-aspect-ratio “needle-” or “rod-”type particles. The comminution fracture mechanism often operates along the length of these crystals, effectively chopping them along the length scale into shapes with lower aspect ratios. This breakage gives rise to consequent change in the physical attributes, such as bulk density, as well as formulation behavior, such as flow properties.
References
1. Lee, I., Sirota, E., and Moment, A., Milling in the Pharmaceutical Industry, Chem. Eng., October 2022, pp. 27–33.
2. Dhodapkar, S. and Theuerkof, J., Maximizing Performance in Size Reduction, Chem. Eng., June 2011, pp. 45–48.
3. Rajkovich, S., Advances in Pin Mill Technology, Chem. Eng., February 2017, pp. 60–63.