Regular heat-transfer-fluid monitoring can prevent fluid problems that lead to equipment failure, costly downtime and repairs. Parameters to watch include viscosity, acid neutralization number, moisture, solid or residue content, thermal degradation and flash point. This one-page reference provides information on how to examine these parameters. Representative industry standards are cited with the understanding that comparable BS (British Standard) or DIN (German Institute of Standardization) standards could also be used.
Viscosity
Viscosity value is unique to each fluid and is typically measured at 100°F or 40°C using the industry standard method ASTM D-445. The test can be run in a temperature-controlled bath with calibrated glass capillary viscosity tubes using elapsed time of fluid flow through the tube. Or, the test can be carried out using a Stabinger viscometer, where the kinematic viscosity is calculated by dividing the measured dynamic viscosity by its density. With use, fluid viscosity can shift based upon changes from degradation or contamination.
Acid number
New organic fluids typically have acid numbers of near zero milligrams of KOH per gram of sample. The analysis can be done by potentiometric titration using ASTM D-664. The acid number is found by dissolving some fluid in a mixture of toluene and isopropyl alcohol containing a small amount of water, and then titrating potentiometrically with alcoholic potassium hydroxide to an endpoint pH of 11. An alternative method is to use a color indicator and make the determination calorimetrically. The acid number value can increase with acidic contamination or from heated fluid oxidation.
Moisture
Analysis for moisture concentration in organic fluids can be done by volumetric Karl-Fischer titration using ASTM E-203. Water content is found by titrating the fluid with standard Karl-Fischer reagent to an electrometric endpoint. The method applies to fluids with moisture content in the range of about 50–1,000 parts per million (ppm). A second method is coulometric Karl-Fischer titration per ASTM D4928 in a range of 0.005 to 0.02 mass percent. Moisture in high-temperature heat-transfer-fluid service must be kept low to avoid short-term operational and long-term corrosion concerns.
Solids or residue content
Measurements of solids content can be done by gravimetric separation and quantification of solids (mass) per unit volume of fluid filtered. A second method involves bulb distillation of a fluid sample under extreme vacuum with temperature increasing to 250°C until only non-volatile residue remains. The mass percent of non-volatile residue of fluid is reported. A third technique, known as Conradson Carbon Residue and described in ASTM D189, is sometimes performed to quantify carbon residue in mass percent remaining after evaporation and pyrolysis of an oil sample. This quantity can be an indicator of coking potential of an oil.
Thermal degradation
With measurement by simulated distillation gas chromatography using ASTM D-7213, the oil boiling range can be compared with that of unstressed (that is, unused) fluid to quantify the percentage of low-boiling and high-boiling degradation products present. Critical to accuracy is knowing the boiling range of the same fluid in its unstressed condition.
Flash point
Flash point temperatures are measured using ASTM D-92 (Cleveland Open-cup; COC) or ASTM D-93 (Closed-cup; CC) techniques, reported in Fahrenheit or Celsius. Comparison to the flash point temperature of the unstressed fluid standard can determine the change in fluid condition.
Knowing what the fluid is like in an unstressed condition can help determine what should be done to improve fluid condition. From this analysis, engineers familiar with the fluid’s operating environment can assess what caused the changes and decide on what should be done. Since expertise at a general-service oil-testing laboratory can be more limited, a more detailed understanding of the test results and related action-thresholds, as they apply to specific fluids, is available from the manufacturer (Figure 1). For more on interpreting results, see Ref. 1. For coverage beyond the above tests, see Refs. 2 and 3.
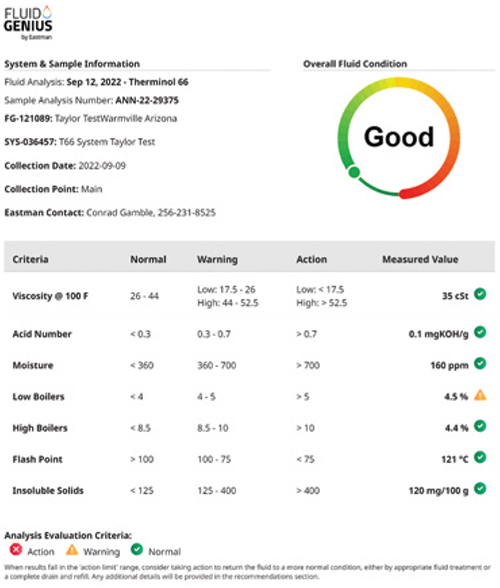
FIGURE 1. Analysis of heat-transfer-fluid parameters, such as acid number, viscosity and solids content, can help identify changes to fluids that are in operation, and determine if action should be taken
Editor’s note: Content for this column was authored by Conrad Gamble, Eastman heat transfer fluids
References
1. Gamble, C. and Schopf, M., Optimizing heat transfer fluid performance: How to avoid costly consequences, Eastman Chemical Co., white paper, www.eastman.com, 2015.
2. ASTM International, ASTM Standard D5372-20: Evaluation of Hydrocarbon Heat Transfer Fluids, ASTM International, www.astm.org.
3. Deutsches Institut für Normung e.V. (DIN) DIN 51529 – Testing of mineral oils and related products: Testing and evaluation of used heat transfer fluids, www.din.de.