In crossflow membrane filtration (CMF), feed flow is parallel to the filtration surface (rather than perpendicular to it, as in conventional filtration). During a given pass, a portion of the feed permeates the membrane, while a larger portion is retained as retentate. Most of the retentate is returned for multiple passes, by a circulation pump. CMF is common across many industry sectors, and applications and offers advantages in its ability to impart shear onto the filtration surface. This reduces fouling by particulate matter or retained molecules. Several module configurations and membrane types are available. This one-page reference reviews common filter-module configurations and membrane materials.
Membrane materials
Modern CMF membrane materials include polysulfone (PS), polyethersulfone (PES), polyvinylidene fluoride (PVDF), polyacrylonitrile (PAN), polyamides, polytetrafluoroethylene (PTFE) and polypropylene (PP).
Most CMF membranes are asymmetric, with a thin selective layer on top of a more open support layer. The tight selective layer does the actual filtration, while the open support layer minimizes resistance to flow and provides mechanical integrity.
Inorganic membranes include ceramics, such as α-alumina, zirconia and metal oxides (notably, titanium dioxide), sintered stainless steel and graphite. More robust than most polymers, inorganic membranes can withstand strong acids and bases, as well as high temperatures and pressures. Such membranes are particularly useful for high-fouling applications that require aggressive cleaning.
Module configurations
Available CMF module configurations are described here.
Hollow fiber. This module contains a bundle of polymeric tubes (hollow fibers), potted at both ends and encased in a shell. The geometry is analogous to that of a shell-and-tube heat exchanger, and the tube wall is the membrane. Feed enters the tubes at the bottom, retentate leaves at the top, and permeate passes through the tube walls, then exits through the shell side. A typical module is 10–20 cm in diameter by 1–1.6 m in length. The main advantage of the hollow-fiber configuration is the ability to tightly pack the fibers, allowing a high membrane area per unit volume (as high as 16,000 m2 /m3). Another advantage is the ability to backwash for more effective cleaning.
Spiral wound. This design consists of membrane envelopes wound around a perforated central core. Each envelope contains two rectangular membrane sheets facing away from each other, separated by a porous spacer. These spaces provide a path for the permeate, which flows around the spiral to the central core, then exits the module. The spaces between adjacent envelopes, separated by grids, serve as flow channels for the feed and retentate. Each envelope is sealed with adhesive on three sides, and the fourth side is attached to the central tube. Typical channel width, module diameter and length are 0.25–0.5 mm, 10–40 cm and 1–1.5 m, respectively. Spiral-wound modules are commonly used for water purification. Advantages are lower energy consumption compared to other designs, and high area per unit volume. Spiral-wound units are not suitable if fibrous solids are present, because these will clog the grids.
Tubular. Like the hollow-fiber design, tubular modules have a shell-and-tube geometry, but the tubes are larger, with the inner diameter ranging from 2.5 to 25 mm (Figure 1). The tubes consist of a porous support, such as fiberglass-reinforced epoxy, with the active layer formed on the inside surface. The shell is made from stainless steel or a hard polymer. Tubular modules are chosen for difficult-to-handle feeds that are not suitable for hollow-fiber or spiral-wound designs. These include high-viscosity feeds and those with high undissolved solids content, large particles, or highly compressible or gelatinous solids. In addition to handling challenging streams, other advantages of tubular design include high resistance to fouling and ease of cleaning. Disadvantages are low packing density; high energy consumption; and the inability to backwash. Applications include wastewater treatment, paint recovery and juice clarification.
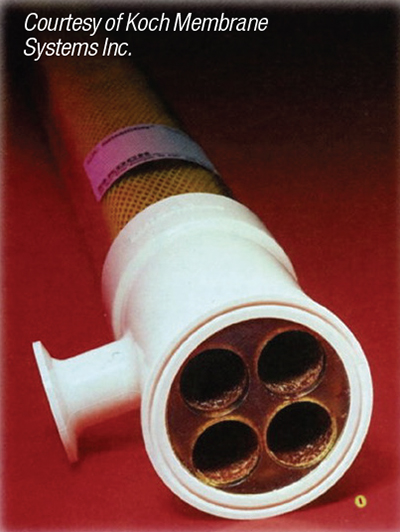
FIGURE 1. Tubular modules are useful for difficult-to-handle feeds
Plate-and-frame. These modules contain a series of flat membrane sheets arranged in a plate-and-frame assembly. The membrane side of each sheet faces a feed channel, with the space between the opposite sides providing a flow path for permeate. This assembly, reminiscent of a traditional filter press, is situated between two end plates, with gaskets placed as needed to direct flow (Figure 2).
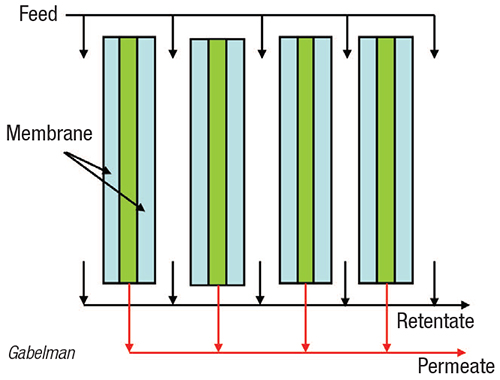
FIGURE 2. In plate-and-frame modules, the space between opposite sides provides a flow path for permeate
Ceramics. A ceramic module consists of a porous ceramic material, called a monolith, through which parallel flow channels have been formed. The separation is performed by a thin active layer of smaller particles deposited onto the inside surface of the channels. The active layer is usually α-alumina, zirconia or titanium dioxide, while the monolith is typically α-alumina or other metal oxide.
Editor’s note: This material was adapted from the following article: Gabelman, A., Crossflow Membrane Filtration Essentials, Chem. Eng., April 2017, pp. 49–59.