Effective measurement of corrosion on process equipment and plant structures offers several benefits to plant operators. These include providing early warnings about damaging process conditions that could lead to corrosion-induced failures, establishing correlations between changes in process parameters and their effects on corrosivity and evaluating the effectiveness of particular corrosion-control and prevention strategies, among others. This one-page reference provides basic information about a common type of corrosion monitoring used at industrial process plants: weight-loss analysis using corrosion coupons.
Metal coupons
Weight-loss analysis using metal coupons is the longest-established method of estimating corrosion losses in plants and equipment. In this approach, weighed samples (coupons) of metals or alloys under investigation are exposed to process conditions, then removed after a certain time interval (Figure 1). Corrosion products are cleaned off the coupon’s surface and the sample is reweighed to determine metal lost due to corrosion.
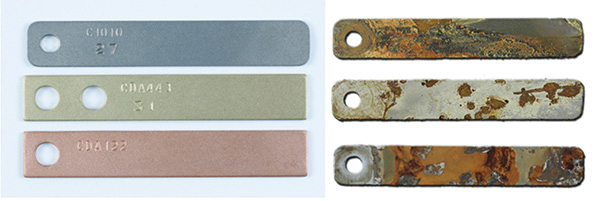
FIGURE 1. Corrosion coupons, such as those on the left, are weighed, then exposed to a process to determine the corrosion rate. At right are coupons after exposure (photo courtesy of Metals Samples Company)
The simplicity of the measurement offered by the corrosion coupon is such that the coupon technique forms the baseline method of measurement in many corrosion-monitoring programs [1].
The coupon’s weight loss is converted to a corrosion rate (CR) according to the following relationship:
CR = [Loss in weight (g) x K] ÷ [Alloy density (g/cm3) x Exposed Area x Time (h)]
The term K (K-factor) is a constant that is chosen according to the desired units for the CR (often either mils per year or mm per year).
Typical corrosion-monitoring programs involve the coupons being exposed to process media for 90 days before being removed for laboratory analysis, allowing plant sites to obtain four corrosion measurements per year. Weight loss of a coupon that results from this exposure is considered to be an average value across the duration of the exposure.
Coupons are usually oriented parallel to the process fluid’s flow direction to more closely reflect the conditions experienced by a vessel wall.
Coupon preparation and cleaning
The initial preparation of the coupon surface, and cleaning the coupon after use, are critical in obtaining useful corrosion data. Coupons should be cleaned before weighing and exposure to ensure they are free of contaminants that could affect test results. Both the relevance and reproducibility of weight loss data are highly sensitive to the inherent suitability of the cleaning techniques, and to the care with which they are executed [1].
Surface finishing methods include blasting with glass beads, sand or other aggregate, as well as sanding with abrasive belts. Surface or double-disc grinding with abrasive stones can also be used. Relevant standards for surface finishing and cleaning of weight-loss coupons include ASTM International Standards G-1 and G-4 and the AAMP Recommended Practice standard 0775 [2, 3].
Advantages and limitations
Corrosion monitoring using coupons has several advantages, as well as some limitations, as described below:
Versatility. Because weight-loss coupons can be fabricated from any commercially available alloy, the technique is very versatile. It can be applied to cases of gases, liquids and solids flow. Different geometric designs can be used to investigate a range of corrosion phenomena, including: stress-assisted corrosion; bimetallic (galvanic) attack; differential aeration; and heat-affected zones [1].
Visual inspection. Corrosion coupons can be visually inspected upon completion of the test, so corrosion deposits can be observed and analyzed, and localized corrosion can be identified and measured. Localized corrosion phenomena, such as pitting, can also be assessed.
Simplicity. A direct corrosion measurement is obtained, without the need for theoretical assumptions or approximations, and no electronic monitoring equipment is required.
Time delay. Because coupons are exposed for three-month (or longer) time periods before laboratory analysis, indications of a corrosion event may not be observed until significantly after the event occurs [4]. In case of a specific corrosion event, the timing of the event is not possible to determine exactly.
Averaged CR. Evaluation of coupons is not able to provide information about changes in corrosion rates (such as peak corrosion rate or short-term corrosion events), which might not register increased weight loss.Therefore, coupon monitoring is most useful in environments where corrosion rates do not significantly change over long time periods.
References
1. Alabama Specialty Products Inc., Corrosion Coupons & Weight Loss Analysis, Web resource, www.alspi.com, accessed Feb. 2025.
2. ASTM International, Standard Practice for Preparing, Cleaning and Evaluating Corrosion Test Specimens, ASTM International Standard G1-03, 2017, www.astm.org.
3. Association of Materials Protection and Performance (AMPP), Recommended Practice 0775, Preparation and Evaluation of Metal Corrosion Coupons, 2015.
4. Asset Integrity Engineering (AIE), Introduction to Corrosion Coupons, Blog post, March 1, 2022, accessed Feb. 2025, URL: www.assetintegrityengineering.com.