Advances in next-generation materials and assembly techniques have enhanced membranes’ effectiveness in numerous applications
Membranes are one of the primary technologies used for separations. While they may be best known for their use in water-treatment operations, advances in membrane technologies have expanded their use into many areas, including the mining, oil-and-gas, petroleum-refining and industrial-gas sectors. These advances have also allowed for membranes to better address the myriad challenges faced in water-treatment facilities. This article examines several new membrane technologies used across a range of chemical process industries (CPI) sectors.
Olefins separation
Advances in membrane materials have enabled their use in complex separations applications, including those involving various industrial gases and olefins. For instance, with the development of a proprietary, silver-facilitated membrane, Compact Membrane Systems (CMS; Newport, Del.; www.compactmembrane.com) aims to provide an efficient technology for separating olefins from paraffins. The intent is that these membrane systems, called Optiperm, can be installed alongside distillation columns or reactors for debottlenecking, retrofits and capacity expansions to augment production yield by separating and concentrating olefins, and reduce waste and losses from small offtake streams or purge gases. “The benefit of the technology is that it allows customers to capture value they can’t get now from streams they already have,” says Erica Nemser, chief executive officer at CMS. For instance, by installing a membrane system in a polypropylene reactor system, excess propylene, which would otherwise be lost, can be recovered from the purge gas stream and fed back to the reactor, reducing both feedstock costs and waste. “This has significant economic benefits for a modestly sized system,” says Nemser. In August 2017, CMS began operating a pilot Optiperm system on an overhead stream consisting of propylene and propane at Delaware City Refining Co., which is the first application of this type of technology at this scale.
The Optiperm membrane is made from a custom, amorphous fluoropolymer chain embedded with silver (Figures 1 and 2). “The silver actually acts as a facilitating agent to allow the olefin to cross the polymeric membrane,” explains Bill Charlton, olefin specialist at CMS. “The olefin’s double bond has an affinity for the silver, so it latches onto each silver site sequentially as it crosses the membrane. It doesn’t just work by permeation, it is accelerated by the presence of the silver,” he adds.
The Optiperm membrane is set apart from previous silver-based membranes by its custom fluoropolymer chemistry, which enables silver to be embedded directly into the polymer structure prior to casting the membrane. The polymer structure offers protection of the silver against deactivation, which would render it unable to attract olefins. Typically, silver sites are vulnerable to deactivation by common species present in petrochemicals and petroleum-refining processes, such as sulfur and acetylene. According to Charlton, Optiperm’s unique chemistry also instills several other advantages. “We see significantly higher olefin-permeation rates than have been seen in the past, our olefin/paraffin selectivity is much higher as well, and most importantly, our longevity is much greater than has been previously reported,” says Charlton.
Currently, the membranes are most effective at separations involving two-, three- and four-carbon molecules, but CMS believes that they could also handle C5 separations. Future work will include investigation of liquid-phase separations for C5 and C6 streams. The current iteration of Optiperm requires that the feed be in the vapor phase and that system’s relative humidity be maintained at around 85%, so a backend drying step may be recommended. Also, depending on system operating conditions, re-compression may be required.
Another technology aimed at olefins separation introduces new levels of selectivity by integrating metal-organic framework (MOF) materials into membrane complexes. A research team from Eidgenössische Technische Hochschule Zürich (www.ethz.ch) has developed a method to create MOF composite membranes that are capable of extremely fine separations. “MOF composite membranes have been shown to allow efficient separation of molecules that vary in size by only a fraction of one angstrom, such as propylene and propane,” explains Samuel Hess, lead researcher on this project. In creating composite membranes, a key aspect is determining a combination of materials that will instill mechanical stability while also remaining cost-effective to produce at industrial scales. Hess’ team developed a polymeric precursor membrane with zinc oxide seed-nanoparticles present at the pores. “This precursor membrane allows the growth of pore-directed MOF crystals without requiring any additional seeding or counter-diffusion steps,” says Hess. This procedure avoids the formation of rigid MOF crystal layers and maintains the polymer’s intrinsic mechanical flexibility, which is required for integrating such membranes into industrial spiral-wound membrane modules.
The team has synthesized these membranes at laboratory scale, and recently succeeded in fabricating the precursor membrane via roll-to-roll coating. Currently, they are working to scale up production to develop industry-scale prototypes containing several square meters of membrane material. “We are optimistic that the synthesis protocol is adaptable to larger membrane areas and that the process can be implemented to produce MOF-composite membranes continuously,” says Hess. The next step for this patent-pending technology is commercialization — the team is seeking collaborators to implement the composite membranes in industrial operations.
Lithium recovery
Increasing demand for energy-storage solutions has forced lithium producers to seek alternative processing techniques, and membranes are proving to be quite promising in this area. Neometals Ltd. (West Perth, Australia; www.neometals.com) has developed a pair of corresponding technologies: one that directly extracts LiCl from brine without evaporation using adsorption and nanofiltration (NF) —known as the Dexter process; and one that applies an electrolysis cell to produce high-purity LiOH (known as the ELi process). LiOH is a major precursor material in the production of lithium-ion batteries. The combination of these processes would enable efficient consolidated-site production of LiOH from lithium brine deposits. The ELi process also offers an alternative to lithium production from hard rock deposits.
The ELi process’ electrolysis cell is based on the chlor-alkali process with specially adapted membranes (for more information about chlor-alkali technology, see The Greening of Chlor-Alkali Production, Chem. Eng., October 2017, pp. 16–20). “By adapting the chlor-alkali process with alternative membranes, we’ve been able to make LiOH directly from spodumene concentrate at a very low cost of production,” says Mike Tamlin, Neometals’ chief operating officer. Since the stream entering the electrolysis cell must be extremely pure, the company developed an integral purification process that is capable of removing impurities down to the parts-per-billion (ppb) level. Neometals also determined the optimal set of operating conditions to allow conventional chlor-alkali equipment to be used for LiOH production through semi-pilot testing. By utilizing a chloride-based environment in the electrolysis, rather than, for example, inputting lithium sulfate, higher current efficiency is possible since a sulfate medium does not have the ionic mobility of chloride. “We have incentive to create the most pure solution possible, because the higher the purity, the higher the current efficiency, resulting in a higher-purity end product, which benefits the electronics industry,” says Tamlin. Neometals will next pilot the technology, and expects to produce LiOH at commercial scale by 2021 initially via the conventional process while final detailed design on ELi is completed, according to Tamlin.
The company also saw an opportunity to improve upon the environmental footprint of extracting brine water in lithium processing. Typical brine extraction requires removing large amounts of water from water tables and evaporating it, which is particularly problematic in water-stressed communities. “As lithium production increases, we realized that finding a better way to extract lithium from brine without extracting the water from the ground permanently was a worthwhile goal,” says Tamlin. The company’s Dexter direct-extraction process involves pumping brine from an aquifer, processing it in an absorption phase with a proprietary sodium-titanate nanotube absorbent followed by very selective NF to produce a concentrated LiCl stream. The adsorbent material has very high surface area and durability, and is extremely selective against sodium, which is predominant in the brine, but is a contaminant to the LiOH production process. The NF step uses specially developed membranes to concentrate the lithium and provide purification. The brine water is pumped back into the aquifer once lithium is removed. “By using relatively standard equipment, and adapting a new type of membrane to the process, we’re able to take lithium out of a saline solution and create an upgraded solution without using reagents,” says Tamlin. Eliminating reagents is particularly important for operations in remote locations, where transporting materials over long distances via trucks could be dangerous or prohibitively expensive. Also, adds Tamlin, extracting the brine and re-injecting it directly after removing the lithium avoids the generation of the large salt stockpiles that result from solar evaporation, which can be an environmental concern, particularly in windy climates. “The entire lifecycle of lithium production is enhanced,” he emphasizes.
New membrane technologies from Membrane Development Specialists (MDS; Escondido, Calif.; www.mdsamericas.com) enable the recovery of lithium from two diverse sources: lithium clay and recycled batteries. Due to the dilute lithium concentration of clays, achieving efficient recovery is quite challenging. MDS’ patent-pending process (Figure 3) involves acid digestion of clays with proprietary NF, ultrafiltration (UF) and reverse-osmosis (RO) membrane processes.
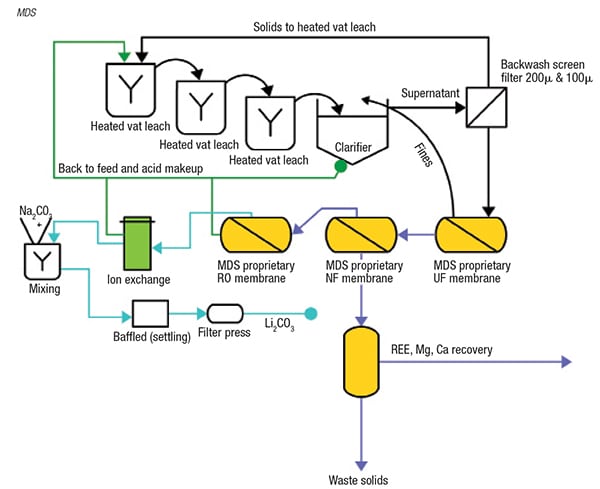
FIGURE 3. Several membrane steps enable the recovery of a concentrated lithium stream
from dilute clay
“In this process, we are concentrating lithium as a sulfate. The permeate will contain 50–80% of the acid that is used, which is recycled back into the process,” explains Larry Lien, managing director of MDS. The technology enables the use of lithium deposits that previously were viewed as too dilute for feasible recovery. The technology has been demonstrated at bench scale, and MDS is currently working with stakeholders to develop it for larger-scale operations. Since the process is based on established technologies, and requires no underground mining, Lien is confident in the scaleup potential. Lien projects that a 1,000-gal system could produce 5 tons of lithium carbonate per day.
After acidifying the clay, a UF unit removes the suspended solids. Next, a specialized NF membrane removes divalent cations like calcium and magnesium, and in some cases, rare-earth elements (REE) that can be concentrated in this step as well. The resulting permeate is a relatively pure stream of lithium sulfate, chloride or nitrate, which is concentrated with acid. “We concentrate the lithium stream up to 1,000 to 2,000 ppm, depending on what the osmotic pressure will allow,” explains Lien. “We can recover up to 96% of the lithium that is leached out of clays, so it is a pretty attractive solution,” he adds.
End-of-life batteries are another potential source of lithium. Since the lithium used in batteries is already quite pure, the process is somewhat simpler than recovering lithium from other sources, and MDS has already commercialized an analogous process for lead-acid batteries. For lithium recovery, batteries are first acid-digested, and the carbon and suspended solids are removed using a specialized hollow-fiber UF membrane. Then, subsequent NF and RO steps concentrate and separate lithium from cobalt and other components, while 75% of the acid and 90% of the water are recycled for reuse. “You end up with a highly concentrated lithium sulfate or chloride solution that can be precipitated out,” says Lien. The process can be configured as a permanent, fixed installation, or as a mobile, fully contained skid.
According to Lien, the challenge lies not in the extraction or purity of the lithium, but in the logistics of collecting a sufficient number of batteries to make the process economically sustainable. Here, the infrastructure for efficient, large-scale recycling is critical to the project’s feasibility. MDS is currently working to license this technology in China, where specific recycling mandates have been implemented. According to Lien, the recovery of cobalt, and other battery materials, such as graphene, may further contribute to the economics of the process.
Helium production
A membrane-focused collaboration between Linde Engineering Division (Munich; www.linde-engineering.com) and Evonik Industries AG (Essen, both Germany; www.evonik.com) has led to the commercial implementation of a new helium-recovery process (Figure 4) that combines selective permeation with pressure-swing adsorption (PSA) at a plant in Saskatchewan, Canada operated by Weil Group Resources LLC (Richmond, Va.; www.weil-group.com). By employing membranes, rather than cryogenic gas separation, the technology boasts reduced costs and a much smaller equipment footprint. Membranes’ high selectivities also contribute to the commercial feasibility of the process. “Membranes are easy to operate, especially in remote locations, and they have a good economy of scale, especially in the lower capacity range,” says Tobias Keller, head of the Adsorption & Membrane Plants product line at Linde’s Engineering Division. These benefits enable cost-effective helium-recovery plants to be engineered at a smaller scale. According to Linde, this plant is an industry-first achievement, with regards to the energy efficiency and scale combined with the quality of helium produced.

FIGURE 4. In this hybrid helium-recovery process, hollow-fiber membrane units concentrate a crude gas stream that is subsequently fed to a pressure-swing adsorption process, which purifies the stream to 99.999% helium
Linde Engineering
The Weil Group’s helium plant, which started up using the new membrane technology in August 2016, processes 250,000 m 3 /d of crude gas, producing 99.999% pure helium, with an overall helium yield higher than 95%, according to Linde. The membranes themselves have been developed by Evonik and optimized for gas separations using polymeric hollow fibers embedded in stainless-steel cylindrical cartridges. The number of cartridges can be adjusted based on the required processing capacity or the gas composition. The concentrated gas stream from the membrane unit is then passed into the PSA system for additional purification. Although the Weil Group facility is the first to implement this technology, Linde is also working with a partner in South Africa to supply a similar hybrid membrane-PSA helium plant.
In addition to helium, Evonik is continuing to focus on developing membranes for challenging separations. “Membranes are one of six innovation growth fields we are concentrating on,” says Ulrich Küsthardt, chief innovation officer at Evonik, highlighting several areas where the company has developed new membrane technologies. Sepuran Green membranes for biogas upgrading were launched in 2011. Since then, the product range has been supplemented with the Sepuran Noble membrane technology for hydrogen processing as well as a new hollow-fiber membranes for on-site nitrogen generation — Sepuran N2. Evonik will continue to intensify the partnership with Linde to further optimize membranes for industrial-gas applications.
Membrane mechanical stability
Large-volume separations, such as desalination, and other applications of crossflow filtration demand that membranes are not only capable of precisely selective separations, but are also sturdy and durable enough to withstand high pressures and shear stresses. A new membrane technology (Figure 5) developed by the Global Aqua Innovation Center at Shinshu University (Nagano, Japan; www.shinshu-u.ac.jp/coi) and Penn State University’s Materials Research Institute (State College, Pa.; www.mri.psu.edu) enables the creation of membranes that leverage the desirable separations properties of graphene oxide (GO) while maintaining mechanical stability. Previously developed GO-based membranes have required integration of carbon nanotubes to overcome structural weaknesses, or the creation of GO-polymer composites, which dilute GO’s separation abilities.
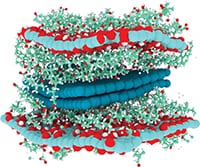
FIGURE 5. Membranes coated with graphene oxide have the mechanical stability to withstand high pressures
Aaron Morelos-Gomez
This new method begins with a porous polymer support onto which an adhesive is coated. Then, a water-based surfactant solution of GO and few-layer graphene (FLG) is spray-coated onto the membrane structure. This water-based solution is treated with divalent ions to increase its stability, and can be mixed with other components in order to tailor the membrane properties, says Aaron Morelos-Gomez, lead researcher on the project. “After optimizing the ratios and conditions, we could obtain a shear-resistant membrane with good salt rejection,” he explains. In addition to salts, the research also looked at the removal of dyes from water in crossflow filtration operations. The research team has created a membrane 20 × 20 cm 2 in area and conducted several trials at laboratory scale. Morelos-Gomez is confident in the potential to scale up this technology. “Since we are spray-coating a water-based solution, the deposition does not have limitations on area size and is easy to implement,” he says. Other methods for fabricating GO-based membranes employ vacuum filtration equipment, which can be more difficult to scale up. “We will keep improving this technology so we can match the performance of commercial reverse-osmosis membranes and implement a scaled-up technology,” Morelos-Gomez says. As the work progresses to commercialization, the team is investigating additional applications and applying for patents.
Looking to water reuse
Although membrane systems have been used for over 30 years in water-treatment facilities to remove turbidity, bacteria and viruses, among numerous other contaminants, water reuse and conservation efforts are driving operators to look at new process schemes to maximize recovery, according to Harold Fravel, executive director of the American Membrane Technology Association (AMTA; Stuart, Fla.; www.amtaorg.com). Fravel lists several examples, including modularization and closed-circuit desalination. “A closed-circuit desalination system is run in a semi-batch mode with scheduled purges, which allows for very high recovery,” he says. Other plants have employed a scheduled switch in flow direction or changes to the process water to minimize buildup of potential foulants and scale. These efforts reportedly improve recovery rates from around 75–80% to as high as 90–95%.
The byproduct streams from membrane plants — whether the concentrate from a RO plant or the backwash flow from a low-pressure system — also present opportunities for water reuse, explains Fravel. “A few facilities are blending their concentrate with wastewater discharge for reuse applications,” he says. Often, the RO concentrate may contain a host of minerals, and may present opportunities for recovery. A new plant installed in El Paso, Tex. (Figure 6) is the first to employ a proprietary minerals-recovery process developed by Enviro Water Minerals Co. (EWM; Houston; www.envirowaterminerals.com). The new facility, which was completed in April 2017 and is currently in final commissioning stages, treats a stream of brackish water and waste brine concentrate from an adjacent desalination plant to recover minerals for sale and return over 2 million gal/d of treated water back to the desalination plant. This effectively eliminates the need for wastewater disposal, which can be costly and create environmental concerns.
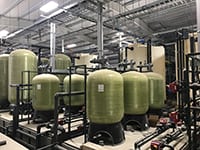
FIGURE 6. At this plant, minerals are recovered from desalination waste streams, resulting in an economical water-reuse scheme
EWM
Hubble Hausman, EWM’s chief executive officer likens the process to a petroleum refinery, in that several different process units are used in a specific configuration to recover individual components. “Each stage is targeting certain ions to extract. It’s incremental processing using the whole gamut of different types of membranes,” he continues. EWM uses not only RO membranes, but also NF, electrodialysis, and bipolar membranes, as well as other processes such as ion exchange and more. In order to ensure continuous operations that can handle the throughput requirements coming from the upstream desalination plant, EWM has built extensive redundancies into the system, so that all units can be regenerated or cleaned as needed.
The next step for EWM will be to adapt this process for seawater desalination, and Hausman cites that the industry faces several challenges in this arena that EWM’s technology mitigates, including environmental regulations surrounding seawater intake and discharge. “Since our process is full-recovery desalination, there are no discharge concerns,” he mentions. Furthermore, since EWM’s process also creates a large amount of salable products from recovered minerals, Hausman believes it is feasible for the company to build robust seawater intake and docking and transport systems to be compliant with stringent regulations. “Most other standalone treatment plants wouldn’t be able to afford such costly intake systems,” he says. Looking forward, EWM also wants to adapt this process to treat cooling-tower blowdown water and produced water from hydraulic fracturing — two areas where solutions for effective treatment and reuse are increasingly critical. ■