In this exclusive interview, ExxonMobil’s Mark Klewpatinond and Zeeco’s Eric Pratchard discuss the company’s recent strategic alliance surrounding the development and commercialization of an advanced new class of hydrogen-fired burners
As many companies in the chemical process industries (CPI) are embarking on new sustainability journeys, hydrogen comes up again and again as a potential pathway to decarbonization. A new collaboration between ExxonMobil Corp. (Houston) and Zeeco, Inc. (Broken Arrow, Okla.) aims to make 100% hydrogen-ready burners a commercial reality. Zeeco’s new Free Jet Gen 3 burner features a next-generation design that enables ultra-low emissions of oxides of nitrogen (NOx) while extending fuel-firing capabilities to 100% hydrogen — significantly lowering CO2 emissions compared to burning incumbent fuel sources, such as natural gas, for process heating in furnaces and boilers. In a unique partnership, Zeeco is collaborating with ExxonMobil to deploy the new burners at ExxonMobil’s Baytown Complex, a world-scale integrated petrochemicals and petroleum refining site in Texas. “In collaboration with ExxonMobil, we identified a need for a process refining burner that would allow the site to switch to a cleaner hydrogen fuel and provide or produce either similar or improved emissions results compared to what they would typically have had with a more traditional refinery fuel-gas blend,” says Eric Pratchard, director of burner technologies at Zeeco.
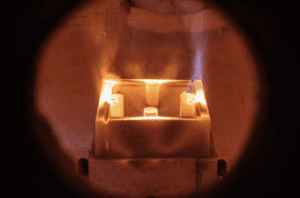
Source: Zeeco
This ambition aligns with Baytown’s goals to reduce greenhouse gas (GHG) emissions by up to 30%. “This burner technology is critical for our site to achieve emissions-reduction goals. If we’re going to switch from an incumbent fuel like natural gas to hydrogen, we need a robust burner we can place into our boilers and furnaces to ensure that we can combust hydrogen whilst remaining within our permit limits with regards to NOx,” says Mark Klewpatinond, hydrogen global business manager at ExxonMobil. NOx reduction has been a front-of-mind concern in the design and deployment of any type of hydrogen-burning equipment. “The real challenge in the hydrogen space is not that you can’t burn hydrogen today. It’s that a lot of the technology does not necessarily allow you to burn hydrogen while managing your NOx levels. That’s where Zeeco comes in with the development of next-generation ultra-low-NOx burners that really enable us to maintain our license to operate within the permissible NOx limits,” he adds.
The design of the burners started with the conventional burner principle of internal fluegas recirculation, where a fuel-gas stream is redirected through an inert stream prior to combustion, effectively creating a leaner fuel mixture that burns more slowly at a lower temperature. “What is different now is that hydrogen is such a robust fuel and it burns at such a wide range of flammability. As an example, methane can burn in an oxygen concentration between about 5 and 15%. Hydrogen burns between 4% and 75% fuel-to-air ratio, roughly, and because of that, it burns at a very rapid rate. And at such a high temperature, more NOx is created compared to methane fuel,” explains Pratchard. The design challenge was clear — how to slow down the rate of reaction to make the fuel more lean, ensuring it doesn’t burn as rapidly or intensely.
“We took the traditional concept of internal fluegas recirculation and we tried to find additional, more creative ways to delay the reaction, both through the interaction of the air with the fuel, and in ways to further lean the fuel out before it reached a certain point. Hydrogen allowed us to do that, because we could craft the delivery of the fuel to different areas of the burner. You may have a point that is very hot that makes sure the burner stays stable, and then an area where the combustion process is being delayed,” says Pratchard.
The installation of the new burners at Baytown makes sense because of the sheer volume of hydrogen that is planned to be available onsite and the fuel needs‚ but there is a balance to consider when using hydrogen as a tool for fuel decarbonization versus consuming it in the site’s myriad processing units. “ExxonMobil is one of the world’s largest producers and consumers of hydrogen today, and that’s all really driven by hydrogen for processing, whether it be hydrotreating, the desulfurization of fuels, hydrocracking or other processes. But what we’re really focusing on with this project is reducing natural gas usage in our furnaces to drive down emissions,” says Klewpatinond. He points out that while many emissions-reduction projects begin with carbon-capture and storage (CCS) as a low-cost decarbonization measure, it is best-suited in cases with a single-point emission source of high-concentration CO2. “The challenge we have with petroleum refining and chemical complexes is that there are multiple sources of what can be considered to be low-concentration emissions. And that’s where hydrogen comes in as a solution. Instead of doing the post-combustion carbon-capture, we are reducing the emissions pre-combustion by being able to replace natural gas with hydrogen to ensure that at the point of combustion, there are no GHG emissions,” he adds.
Since Zeeco’s new burner enables a “drop-in” device capable of 100% ultra-low-NOx hydrogen firing, sites don’t have to fully shut down operations to install them, and Baytown will practically demonstrate this fact with its pilot deployment. “As sites go through turnaround cycles and make plans to install hydrogen-ready equipment, they can know they are safe in utilizing hydrogen. It’s through partnerships like this that we hope to lower the barrier of adoption for organizations to reduce emissions and do it as easily as possible,” says Klewpatinond.