Evonik Industries AG (Essen, Germany) is building a pilot plant in Marl, Germany, for the production of its anion exchange membrane (AEM), marketed under the name DURAION.
A central element in AEM water electrolysis, DURAION membranes support the cost-competitive production of green hydrogen. Evonik is investing a low double-digit million euro amount in the AEM plant, which is scheduled to go online at the end of 2025.
“This strategic investment ties in with our business goals of further growing our pioneering membranes into a true enabler of the burgeoning green hydrogen economy,” says Goetz Baumgarten, head of the Membranes & Fibres product line at Evonik’s High Performance Polymers business line.
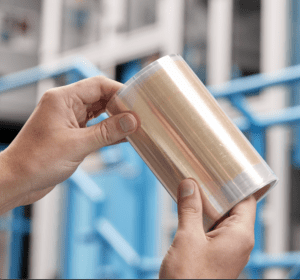
Evonik’s AEM material (Source: Evonik)
The DURAION® membranes produced at the AEM plant in Marl will be at a quality suitable for use in commercial electrolyzer systems. Once fully online, the plant will be able to produce enough membranes each year to provide 2.5 GW of electrolysis capacity for hydrogen production. In addition, the plant will be able to produce reinforced membranes, directly addressing growing customer interest in this new technology.
Compared to conventional electrolysis processes, AEM technology promises lower investment costs due to the use of less expensive materials for the cells. In addition, the technology enables high current densities and very good efficiency.
“The successful development of our DURAION® membrane was possible thanks to the joint efforts of Evonik’s wide-ranging expertise and technology,” says Christian Däschlein, head of the New Growth Area Hydrogen Economy at Creavis, Evonik’s strategic innovation unit and business incubator.
The membrane is a polymer and a high-tech product: on the one hand, it has to allow anions to pass through, but on the other hand, it has to be impermeable to the gases produced in the electrolysis, such as hydrogen. It also has to be able to withstand high pressure and high temperatures.
“Across our many disciplines, we were able to combine polymer design and synthesis, engineering, membrane manufacturing as well as customer and market feedback,” says Christian Däschlein.
In the last twelve months, Evonik has steadily increased the production capacity of the intermediate products used in DURAION® membranes. The construction of the plant in Marl capitalizes on this higher capacity, and is the next step for the company in the planned expansion of its membrane business.