Mobile applications for the CPI simplify process engineering challenges and enhance plant optimization
Most everyone recalls the Apple tagline boasting, “There’s an app for that.” It appears Apple was ahead of its time; today, there really is an application (app) or online tool for just about everything, and the world of chemical engineering is not excluded. Mobile engineering apps and online tools exist to help simplify process engineering, provide visibility into systems and optimize asset and plant health. Some of the engineering apps currently finding use in the chemical process industries (CPI) are explored in this article, so read on and it’s likely you will find that there really is an app for the tasks you’re looking to simplify.
Engineering and design challenges
Designing processes and systems can be one of the more challenging tasks in the CPI, so tools that help simplify the task are being created. For example, Explore (Figure 1) from Alfa Laval (Lund, Sweden; www.alfalaval.com) is an online web tool that operates on computers, tablets and smartphones to help chemical engineers investigate whether centrifugal separation is a suitable technology for a specific separation problem. Tom Manelius, business development manager, Energy Separation says, “The online tool allows anyone with a case to screen data and calculate or simulate preliminary performance. The tool also guides users on how to assess key separability data and explains pilot testing with centrifuges.”
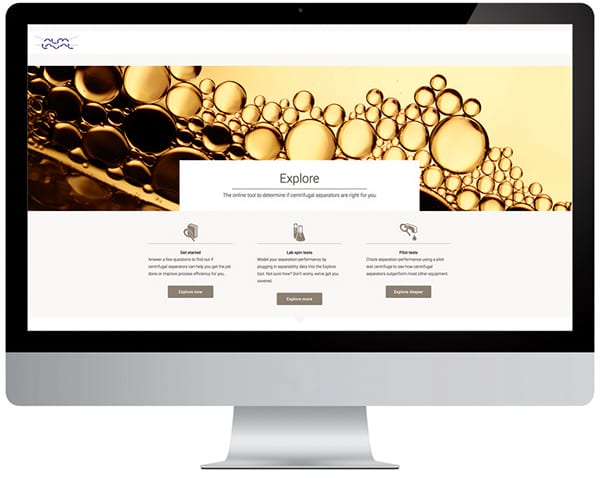
Figure 1. Explore from Alfa Laval is an online web tool that operates on computers, tablets and smartphones to help chemical engineers investigate whether centrifugal separation is a suitable technology for a specific separation problem
Alfa Laval
Explore allows swift evaluation as to whether centrifugal separation technology would be the best way to reach target improvements in existing processes or be the best solution for separation in a new process design. “It empowers process engineers, process development people and utility managers to investigate their case on their own, rather than getting a vendor involved early in the investigations,” says Manelius.
The screening is made through entering data with provided guidance that also explains suitable ranges and why these data are used in screening. Very often the most essential data for separation assessment are unknown. This is the particle or droplet size distribution, and these data are very difficult to measure in a laboratory or process, he says. “However, Alfa Laval has a very robust method to get these data from simple spin testing. This method is now shared online with video tutorials and a built-in calculation tool. The methods of how to evaluate centrifugal technology are well established, but have never been readily available to the industry in an easy format,” says Manelius. “Not only is it now available, but the case can be saved and shared with colleagues, labs and suppliers to facilitate the overall process.”
Designing a heat-trace system can likewise be tricky, so Thermon (San Marcos, Texas; www.thermon.com) offers an online tool for the task. CompuTrace Express was developed to be mobile friendly and leverages the power of the company’s CompuTrace Design Suite database. The online tool allows users to design a system in four steps: create the project; edit the circuit by modifying system defaults, such as changing pipe sizes, circuit lengths and insulation; create the design and, finally, generate a bill of materials.
“We developed this tool in response to requests for an easy-to-use solution that would address smaller heat-trace-circuit requirements — for example, systems that may be part of a larger primary heat trace system, but require new design review for proper operating temperature,” says Lance Bielke, manager of marketing communications
CompuTrace Express can be operated on a local desktop, tablet or mobile device and the design calculations are performed in accordance with generally accepted engineering practices.
Improving operations via visibility
One of the best ways to boost plant productivity and efficiency is to view what’s going on within systems and processes. Again, apps are being developed that can help do exactly that.
DeltaV Mobile from Emerson Automation Solutions (Austin, Tex.; www.emerson.com) allows users, such as operations managers, safety engineers and process engineers, to monitor plant functions that are of concern to them and offers collaborative features that allow streamlined workflows by making it easier for managers and engineers to share critical information, enabling enhanced business results.
“DeltaV Mobile allows users to get realtime data, not just from Emerson’s DeltaV system, but from other historians and systems, as well as trends and alarms, and view operator station displays of critical control systems,” explains Mariana Dionisio, DeltaV product manager, with Emerson.
Operations managers use the app to maintain visibility of operations, even when they are off site. They monitor critical process values, key performance indicators (KPIs) and alarms and receive notifications for critical alarms while communicating with other personnel. Safety engineers may monitor safety-critical data and alarms specific to plant safety, maintain situational awareness by receiving notifications and viewing alarms in real time, as well as monitoring safety-instrumented functions. Process engineers can access and view critical realtime data, alarms and trends to diagnose issues, evaluate what happened by getting alarms in context with process information, get notifications for critical alarms, even when off site, and communicate issues and troubleshoot with operators and remote experts.
According to Dionisio, DeltaV Mobile is unique in its ability to easily create views that are customized for the individual. “With other mobile solutions, engineers have to sort through a lot of information to find the information they need. With DeltaV Mobile, they can create filtered, customized lists that only show critical information that is important to them,” she says. “Getting relevant information to the appropriate people allows them to make better decisions in a more efficient manner, and sharing that information with other experts in a secure, read-only, mobile environment enables them to have important information wherever and whenever they need it.”
Also within a chemical facility, Opto 22’s (Temecula, Calif.; www.opto22.com) groov View (Figure 2) can be used to monitor and control automation systems and other components associated with plant floor equipment and process units. Users can securely view the operator interface screens on smartphones and computers to monitor, control and troubleshoot systems while untethered from a traditional human-machine interface (HMI), says Arun Sinha, engineer, with Opto 22. Operators can also view KPIs or other process data to help improve plant operations, efficiency and safety.
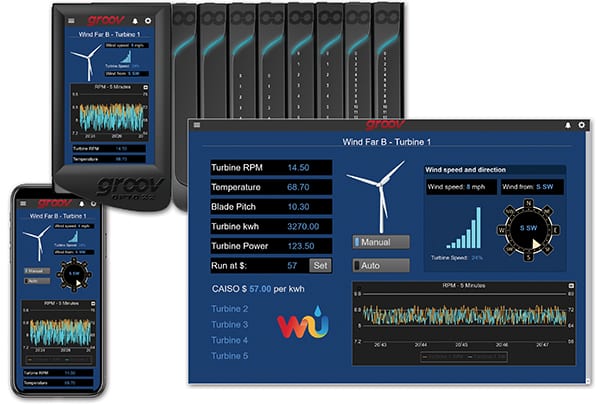
Figure 2. Opto 22’s groov View can be used to monitor and control automation systems and other components associated with plant floor equipment and process units
Opto 22
The app is built in a browser and runs in a browser or in the free mobile app. It connects to Opto 22 programmable automation controls, Modbus-TCP devices, databases, online services and other data sources. “Users can drag and drop gadgets from a built-in library, then tag the gadgets to configure an application,” says Sinha. “Users can also set user permissions and security, configure realtime trends up to five years, log events and set up email and text notifications.”
He continues to say that groov View can add value to different departments and disciplines, such as operations, engineering, management and information technology (IT). Besides levels of access, the app can be configured to have separate user groups access only the information pertinent to them for their job function. “For example, operations technicians could be exposed to process and sensor level data, engineers to production data, IT to network performance information and management to overall business-related data from within the plant, as well as outside sources,” explains Sinha.
Another app designed for better visibility is IDEC’s (Sunnyvale, Calif.; fc6a.idec.com) WindEDIT Lite app (Figure 3), which provides two-way access to its family of MicroSmart FC6A PLCs. Don Pham, senior product marketing manager at IDEC, says: “With the WindEDIT Lite app, users can monitor any PLC [programmable logic controller] parameter and change set points and other values. Data register, input, output, times and count values can be monitored and controlled using the standard dialog interface. The app also has a custom dialog interface, which the user can configure to allow only certain PLC parameters to be monitored and controlled. Trending is supported within the app, with users able to plot multiple register points for graphical views.”
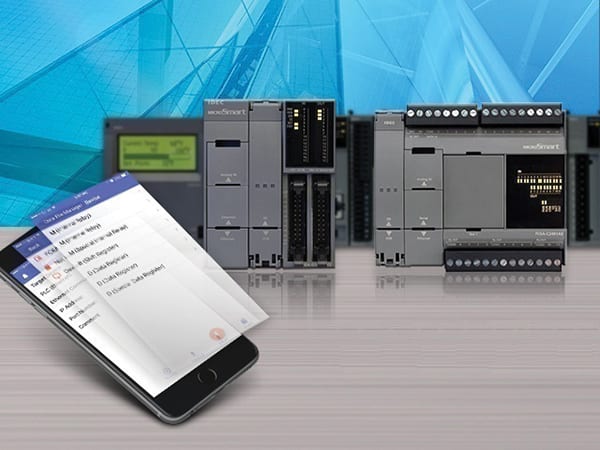
Figure 3. The WindEDIT Lite app from IDEC allows users to monitor any PLC parameter and change set points and other values. Data register, input, output, times and count values can be monitored and controlled using the standard dialog interface
IDEC
The app provides access to an SD memory card installed in the PLC, so logged information stored in the memory card can be easily accessed. The app is often used by plant operators, maintenance techs and engineers to perform various tasks. For example, if a plant operator needed to send production status to the plant manager at the end of a shift and to store these data in a historian, he could use the app to retrieve the logged data from the MicroSmart FC6A PLC via Bluetooth and then attach the logged data to an email and send it to the plant manager and a cloud-based historian via Wi-Fi. Maintenance techs can use the app to interact with the PLCs as required. Also, engineers can use the app to monitor key PLC parameters and make adjustments as necessary to keep each parameter within its target range.
Also using Bluetooth to enhance visibility, MSA (Lake Forest, Calif.; www.msasafety.com) offers the X/S Connect app with Bluetooth-enabled fixed gas detectors (the Ultima X5000 and General Monitors X5000), which allows users to securely connect their devices to the detectors so they can be quickly configured (Figure 4).
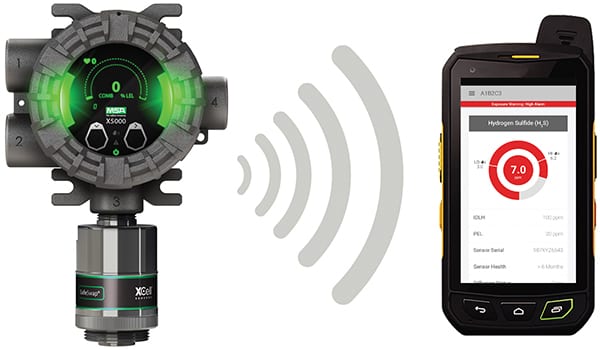
Figure 4. MSA offers the X/S Connect app with Bluetooth-enabled fixed gas detectors, allowing users to securely connect their devices to the detectors so they can be quickly configured
MSA
“Workers can see the status at a glance on their mobile device, change alarm set points and relay options and check the status of the last calibration, including ‘as found’ and ‘as left’ values,” says Carrie DuMars, product line manager, Detection.
The app is helpful for maintenance and instrument technicians faced with tending gas monitors located in difficult-to-reach locations or crowded equipment areas near piping, valves and other installed equipment where gas leaks can potentially occur. “With the X/S Connect app, workers no longer need to perform ladder climbs, stand on temporary scaffolds or work in awkward positions to perform routine gas detector tasks on these monitors,” DuMars says. “Wirelessly accessing the gas monitors from up to 75 ft away enables safety and convenience and the realtime availability of the gas detector data helps workers rapidly set up, operate and maintain the equipment for better efficiency and use of their time.”
Analytics for plant optimization
Asset health is essential to efficient processes, so knowing and analyzing exactly what’s happening with assets is key to plant and process optimization. Fortunately there are apps for that, too.
Emerson Automation Solutions offers its Plantweb Insight and Plantweb Optics for this purpose. “Plantweb Insight [Figure 5], enabled by wireless sensors and networks, consists of a suite of applications for analyzing plant and facility data using pre-configured algorithms, helping transform raw data into actionable insights. These applications facilitate improved decision making related to specific asset classes, components or equipment,” explains Brian Joe, wireless product manager. “The app is designed to help maintenance, reliability, safety and energy personnel improve overall operations.”
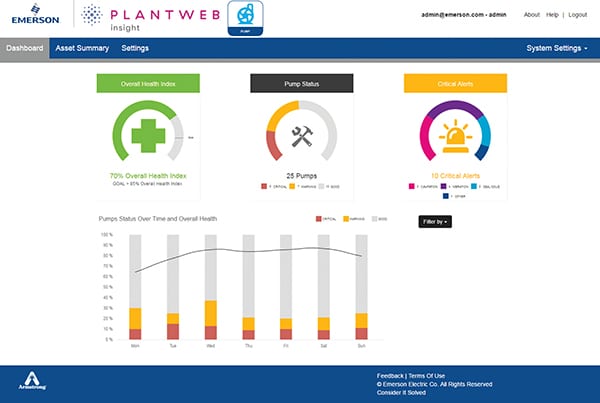
Figure 5. Emerson’s Plantweb Insight, enabled by wireless sensors and networks, consists of a suite of applications for analyzing plant and facility data using pre-configured algorithms, helping transform raw data into actionable insights. These applications facilitate improved decision making related to specific asset classes, components or equipment
Emerson Automation Soltuions
He says the app accesses process equipment data from key assets from numerous sources, including wireless devices and OPC UA servers. “By providing realtime analytics on important plant assets, such as pumps, heat exchangers, steam traps and pressure-relief valves, actionable information is created and used for predictive maintenance and proactive approaches, enabling faster decision making to help facilities improve operational performance. Timelier and educated decisions can be made on equipment to help extend asset life and reduce downtime, as well as reduce excess energy use and emissions. Manual inspection rounds can also be reduced or eliminated with the help of these apps.”
Emerson’s Plantweb Optics is an asset performance platform that centralizes data from different asset sources to provide a holistic view of asset health in a view that is customized to deliver what is relevant to personnel, such as safety engineers, plant managers or maintenance managers, in a relevant context, says Mani Janardhanan, vice president, Plantweb, with Emerson.
It aggregates data from various predictive intelligence applications to create a holistic picture of asset health and make that available anytime and from anywhere. Plantweb Optics combines the data from multiple applications into asset-centric information, and then delivers personal-based alerts and KPIs for improving the reliability of rotating equipment, instruments and valves. The latest iteration of the app allows collaboration and can be integrated with enterprise resource planning (ERP), SAP or a computerized maintenance management system (CMMS) systems to create work orders.
In a similar vein, Voith Digital Solutions (York, Pa.; www.voith.com) offers OnCumulus (Figure 6), a cloud-based industrial internet of things (IIoT) platform that uses an open and agile philosophy for rapid development, deployment and integration with other third-party enterprise systems and data sources to leverage data from sensors and instrumentation to support the objectives of the organization, says Brent Ward, solutions expert. “For example, in some chemical operations, sensors can monitor flow, temperature, pressure and other parameters to detect anomalies in the operation before they lead to failure. Additionally, process parameters are monitored against the desired outcomes/output and are then used to generate a virtual sensor that can be used to further monitor and optimize the process,” says Ward.
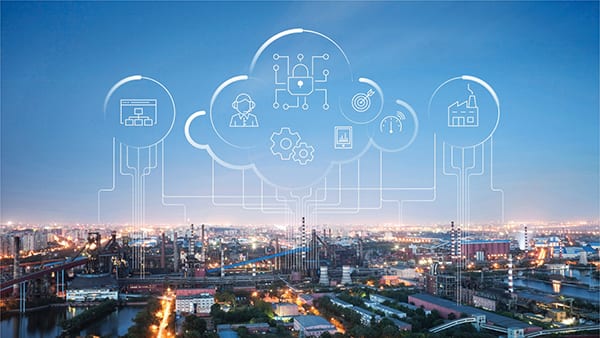
Figure 6. Voith’s OnCumulus is a cloud-based industrial internet of things (IIoT) platform that uses an open and agile philosophy for rapid development, deployment and integration with other third-party enterprise systems and data sources to leverage data from sensors and instrumentation to support the objectives of the organization
Voith Digital Soluitons
The app also provides some basic tools for data visualization, monitoring, dashboarding and alerting. Voith has included a “coordinator” feature to capture the best practices for checklists of items, diagnostics processes, maintenance procedures and other routine items that help save significant time, materials and scheduling. “Most importantly, Voith’s cloud architecture enables the development and use of advanced analytics that allow for optimized algorithms and machine learning across equipment and facilities,” says Ward. “This forms the foundation for leveraging learning at a global scale.”
The app is intended to improve plant operations by visualizing the data, having a central source of data and providing access to comparative data across operations. “At a deeper level, advanced analytics and algorithms can directly impact efficiency of operations, such as energy, raw inputs, materials, identification of anomalies and early warning of failure,” he continues. “And, at the deepest level, leveraging realtime and historical data across operations can support improved maintenance — proactive, prescriptive and, in the future, predictive.”
The apps discussed in this article are just the tip of the iceberg. Chances are good that if there’s a challenge in your chemical facility, there may be a mobile engineering app that can help solve it.