Step changes in condition-monitoring technology to achieve operator-driven reliability can be a reality for organizations of any size
The chemical process industries (CPI) are like all others in that they must negotiate the twin challenges of maximizing productivity and opportunities for growth, while driving down operational costs and striving for sustainability. They also have to achieve these priorities in complex and potentially hazardous operational environments.
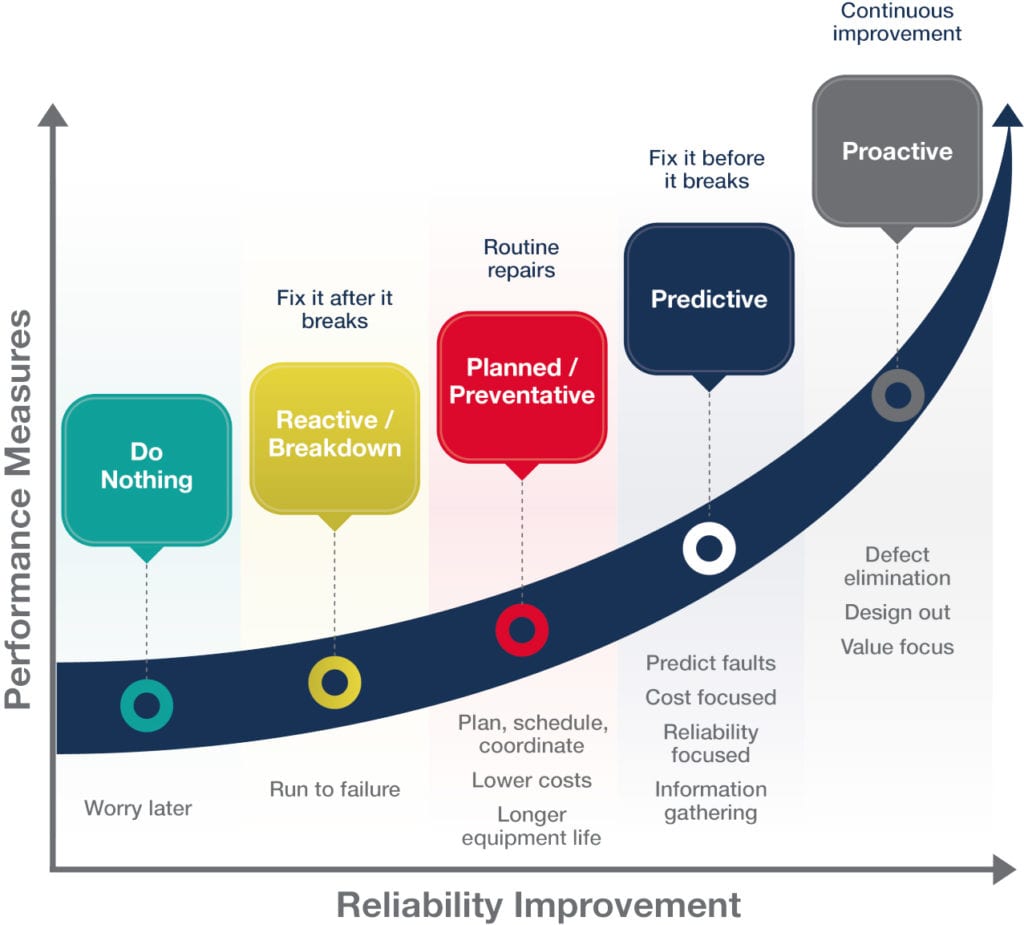
FIGURE 1. Evolving maintenance strategies leads organizations to better predict and avoid equipment failures
The advent of smart devices, the Industrial Internet of Things (IIoT) and Industry 4.0 has presented proven opportunities to optimize reliability and cost-efficiency for those willing to embrace change, and it is fair to say that the CPI fare well in comparison to some industries on this front. This is particularly true of those organizations operating across multiple sites, where the benefits of a move towards greater connectivity and consolidated data are more tangible. It may also explain why it tends to be the bigger companies that demonstrate a greater inclination to reassess their maintenance procedures in light of the efficiencies offered by digitalization.
However, it is also fair to say that a reluctance to move away from traditional methods and approaches remains a trait among many within the industry. And for some, there is a resistance to invest in any condition-based maintenance (CBM) program at all, most typically among independent, single-site operators. There are myriad reasons for this — financial constraints and staffing concerns for certain, but also lack of awareness and, to be blunt, simple force of habit. The mindset that says “wait for something to fail and then tackle the problem” is a serious barrier to achieving longterm reliability.
Yet if even the greatest skeptic took a clear-sighted look at what a genuinely proactive maintenance program (Figure 1) can achieve in terms of plant reliability, operational efficiency and cost-effectiveness — and considered the affordable digital options now available to facilitate it — they could not fail to be persuaded of its value.
What causes downtime?
Take a look at the root cause of unscheduled downtime in a chemical plant and there is a very high chance that vibration fatigue, bearing failures or inadequate lubrication will be repeat offenders.
Vibration
Vibration is a norm in most rotating equipment, but any change in the levels of that vibration is an important indicator of a developing fault that — if left unchecked — is likely to lead to failure and unplanned downtime. In rotating equipment, any number of issues can cause excessive vibration. It can be a sign of wear, incorrect equipment installation causing misalignment, unbalance or laxity in the systems, bearing deterioration or worn gear teeth. Identifying what is causing excessive vibration is therefore crucial.
Bearing failure
Bearings are highly sensitive to external factors. Particle contamination, pressure changes on the impeller or shaft, misalignment or poor lubrication can all be the instigator that results in premature bearing failure and brings repeat stoppages to a plant. With bearing failure accounting for 40% of all rotating equipment failures [1], these really do represent a significant threat to overall reliability and should be a central focus of any CBM plan.
Lubrication
Significant problems often arise from comparatively small issues, and lubrication is a classic case in point. It is frequently treated as an afterthought, lumped in with other maintenance activities or not planned at all. Where routine lubrication is carried out, data are often not captured, and guidelines fail to specify what, how and when it should be used. With poor lubrication accounting for more than 10% of all bearing failures [1], a carefully considered lubrication program really can, and should, be part of the bedrock of any maintenance program.
These issues are common knowledge within the CPI. But for those with aging assets and no CBM plan in place, while they will always know that a particular piece of equipment is prone to repeated failure, they will never discover precisely why. This situation is compounded by the fact that so much focus is placed on getting operations back up and running in the short term that these failures become routine, and the root cause is never properly investigated.
It stands to reason therefore that facilitating a shift from “wait until it fails” to a proactive reliability program requires a two-pronged approach: demonstrating the concrete benefits of CBM technology and altering the mindset of the people tasked with putting it into practice.
Technology for reliability
Many CPI companies have aging assets that are subject to frequent premature failures. Identifying the root cause of those failures enables a seismic shift away from them representing a “necessary evil” that must be factored into routine operations. This is where advanced technology which, crucially, is scalable to any industrial setting, comes into play.
Motion amplification
Motion amplification is a useful technique to help understand any complex vibration modes and to identify any adverse differential movements and identify areas of inadequate stiffness.
Motion amplification is an optical video-based technique, where every pixel in a digital video image effectively becomes a sensor. Following processing, the relative movement between all features on the video are amplified to exaggerate movements, providing a clear indication of any vibration issues.
Additionally, data from any point on the image can be extracted in the form of a calibrated time series or frequency spectra, which can be used as part of a root-cause analysis.
Ultrasound
Ultrasound is a well established technique that can be used to diagnose many types of equipment faults. The technique can be used as part of a condition-monitoring program to support many activities, such as bearing-lubrication monitoring, leak detection, electrical inspection, steam-trap inspection and valve condition monitoring.
Connectivity is key
Connectivity may be a buzzword for larger chemical companies, but its value is not limited to multi-site operations. Realtime management of critical assets is relevant to any operator.
The most advanced technologies offer high-speed, online, realtime management of safety- and business-critical assets. These systems can consolidate readings as diverse as vibration data and oil analysis on one platform, which can be securely accessed from anywhere in the world via a standard web browser.
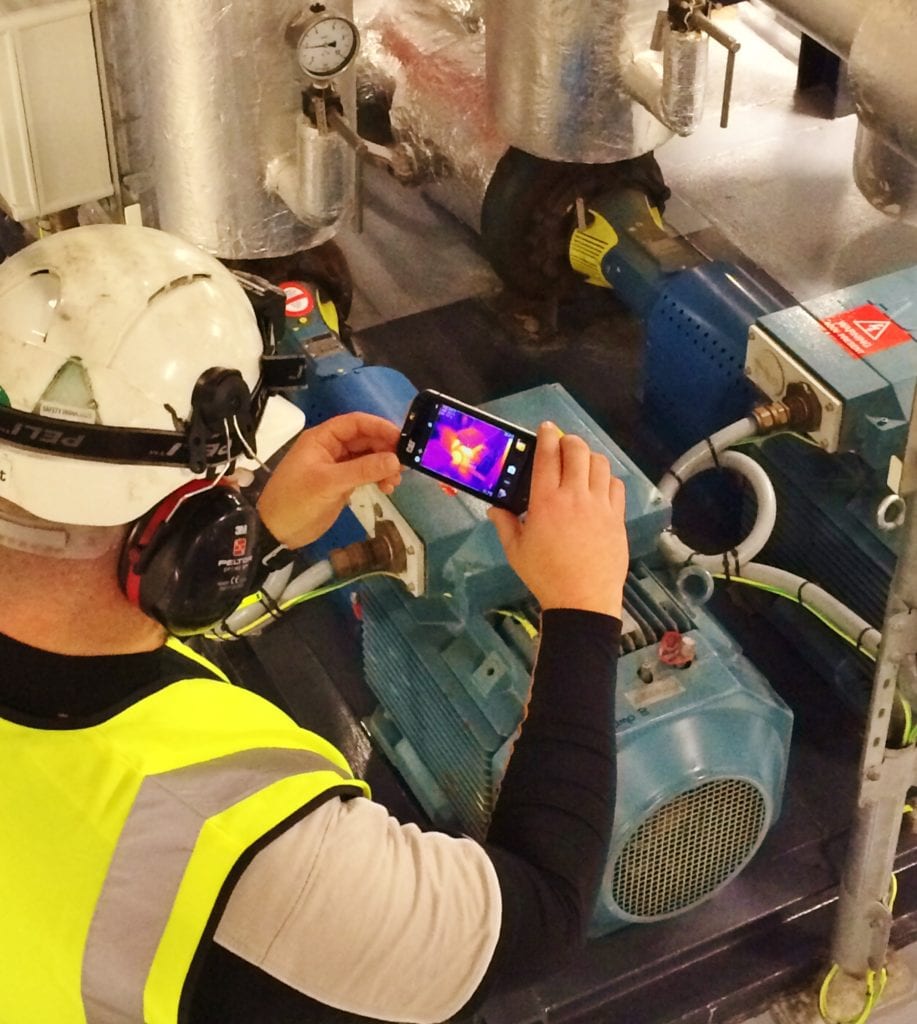
FIGURE 2. Handheld devices that can conduct condition-based analyses hold many benefits in terms of operator safety and efficiency
Low power consumption and high storage capability make connectivity both affordable and scalable. Multiple web-connectivity options and the ability to access diverse data in one place mean that continuous monitoring, asset management, failure detection and troubleshooting can become one seamless operation. Realtime insight into, and analysis of, the condition of business-critical assets facilitates intelligent decision-making, which invariably results in improved productivity and cost-efficiencies.
With cloud–based technology, there is no need for expensive hardware, making this an affordable and accessible option. A key feature of this technology is its ease of use — there is no need to employ highly skilled operators.
The ability to employ wireless technology across multiple sites may be particularly pertinent to bigger organizations, but safety is a business priority regardless of scale. Consider the traditional method of collecting vibration or temperature data: a wired accelerometer that must be navigated around collection points that are often difficult to access, for example behind guards. Then compare that with a wireless handheld device (Figure 2), which can collect data from a distance of 50 m. The improved safety of that operation is incontrovertible.
Digitalization is doable
A key fact, often overlooked, is that digital technology has progressed significantly in recent years, while the cost of it has decreased considerably. The scalability of digitalization makes it a very real option for CPI companies of any size. Take the example of a company with one hundred assets and just one maintenance engineer, who is very likely to be struggling to keep track of all the required monitoring tasks. Investing in a combination of fixed and mobile sensors (Figure 3), and one tablet would certainly be a worthy investment. That lone maintenance engineer can use the new technologies to safely collect and store a whole range of valuable data, from vibration measurements to lubrication-oil analysis, on one platform. That database can then be readily accessed to inform a maintenance plan from a position of in-depth knowledge. Informed decisions can be made about what action is needed to pre-emptively deal with issues that could otherwise lead to failures.
Of course, any data is only of value when it is analyzed and used to inform a proactive CBM program. While this analysis can be done in-house, for those companies without the necessary skills to do it, remote access creates the opportunity to employ external analysts. These often come at little additional cost for all assets when compared to the traditional model of a technician traveling to site to carry out just one aspect of condition monitoring, such as vibration analysis.
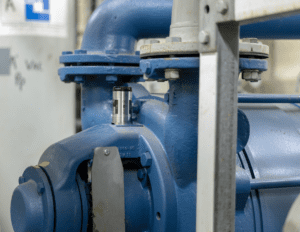
FIGURE 3. The investment to install fixed sensors onto equipment enables safer collection of more comprehensive operational information
When data analysis is judiciously carried out, the shift from reactive to proactive maintenance can be instant, and the issue of never properly tackling problems because engineers are too preoccupied tackling the consequences can become a thing of the past.
Empowering staff
The number is likely surprisingly high for engineers who have participated in manual “pen and paper” inspections, only to realize they have no idea if the information collected was ever actually used to inform operational decision-making.
The fact is that a considerable number of checks carried out in the name of condition monitoring are put to precisely no use whatsoever, in terms of predictive or preventive maintenance. This is where a digital approach to CBM can facilitate a cultural shift that empowers staff and creates a culture of operator-driven reliability.
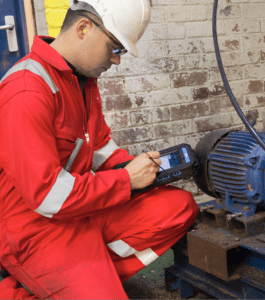
FIGURE 4. Digital technologies can bring about a change in mindset that puts more value onto developing useful insights from collected data
A tablet (Figure 4) is a much simpler, faster and safer approach to data collection. The beauty of it is that users do not need to be an expert to use it accurately and effectively. Where staff are given the autonomy to raise an action based on the information collected — it might be as simple as replacing a missing bolt or fixing a guard — they are more likely to consider their task more valid, more enjoyable even. That can instill a sense of greater value as an employee and promote personal investment in the overall management of assets. The benefits of operator-driven reliability include the following:
- Improved asset health and reduced maintenance costs
- Improved asset performance, availability and life
- Improved production efficiency and maintenance resource availability
- Cost-effective digital tools with controllable and manageable costs
- Scalable deployment for smaller operations and potential future expansion
- Expert support readily available
If these are clearly evident to those responsible for asset maintenance, it can create a virtuous circle where colleagues at every level are invested in the efficient management of assets, and have a clearer understanding of how proactive maintenance impacts positively on the plant as a whole.
With the scalable, cost-efficient digital options available to even the smallest independent chemical company, the time has never been better to swap a “wait till it fails” approach for the longterm reliability offered by a proactive, operator-driven strategy. ♦
Edited by Mary Page Bailey
References
1. Bloch, H.; “Pump Users Handbook: Life Extension,” 2011.
Author
Oliver Pogmore is a sales director with AVT Reliability (Unit 2, Easter Court, Europa Boulevard, Warrington, Cheshire, WA5 7ZB, U.K.; Email: [email protected]; Website: www.avtreliability.com). He earned a B. Eng. Degree in aerospace engineering at Sheffield Hallam University and spent a year in the aerospace industry before being appointed to the Innovation Team of global mechanical seal manufacturer AESSEAL, after which he was seconded to AESSEAL’s sister company AVT Reliability. As sales director of AVT Reliability, Pogmore’s focus is on the successful expansion of the Machine Sentry suite of CBM products and solutions.