engineering how-to |
Column Revamps: From Outside to Inside
By Mike Resetarits, Tim ReBeau and Terry Thurber
Petroleum refineries, chemical-processing plants, natural-gas purification plants and other facilities in the chemical process industries (CPI) all contain columns. These columns perform distillations, regenerations, strippings and absorptions. Column diameters range from 12 in. to 50 ft, and column heights range from 10 to 350 ft. Prior to about 1970, the majority of the column work performed in the U.S. was the building and installation of new grassroots, columns. Subsequent to that, the workload shifted, with many existing columns being revamped to achieve performance improvements or maintenance targets. When columns are revamped, some columns are revamped on the outside; some, on the inside; and some, both. Associated with columns are heat exchangers, reboilers, condensers, receivers, pumps, valves, tanks and instrumentation. Most column revamps necessarily include evaluations and modifications of this ancillary equipment. Unfortunately for us, no two real column revamps are identical. They are never easy. And column revamps cannot be boiled down to a step-by-step procedure that can be applied to most columns. Instead, this article presents some of the many considerations that are involved in column revamps. » |
 |
Waterhammer In Condensate Return Lines
By Wayne Kirsner
There is a temptation that steam design engineers find difficult to resist — to put condensate from high-pressure (HP) steam mains directly into the low-pressure (LP), pumped condensate-return (CR) mains. After all, the CR main is so convenient — it is generally laid right next to the outgoing steam main in the same tunnel, trench or racks as the CR main returning to the steam plant. And, the good practice alternatives to dumping the condensate directly into the pumped CR (such as running a dedicated separate HP condensate-return pipe back to the steam plant; or if a user’s flash tank is not nearby, flashing the condensate in a small vented tank at each trap then pumping it back into the CR main), seem like swatting a fly with a sledge hammer. This article discusses what causes waterhammer-related failures, and gives engineers a criterion for determining if a pumped condensate-return line will hammer when high-pressure and high-temperature condensate is inserted into it. » |
|
 |
|
latest news |
|
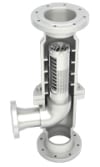 |
ADVERTISEMENT
Instant hot water at precisely controlled temperatures is at your fingertips
Energy efficient and reliable, Pick direct steam injection process heaters deliver hot water on demand at your set temperature. Pick is the perfect choice for heat transfer applications such as condensate mixing, waste water treatment, brackish water heating, jacketed heating, and boiler feed water heating. Contact us to find out how Pick Heaters can reduce not only your energy bills, but your total operating costs. |
|
facts at your fingertips |
Distillation Column Modeling |
Process simulation methods are used to evaluate the performance of proposed distillation systems and improve the performance of existing ones. The most common approaches for modeling distillation processes can be broadly divided into equilibrium and non-equilibrium methods. This article provides information about the differences between the two approaches and outlines their advantages and disadvantages. [more] |
|
 |
|
TECHNOLOGY PROFILE |
 |
This month's Technology Profile covers styrene-butadiene rubber production from butadiene and styrene via a cold emulsion-polymerization process. |
|
from our bookstore |
Improving Plant Operability: Focus on Safety - Volume Two |
This guidebook gives broad, plant-wide recommendations for improving plant safety and reducing risk to personnel, plant operation and the environment. There is focus on specific engineering topics including proper monitoring and control of high temperatures, managing static electricity, reducing fire and explosion risk, reducing risks in laboratories, proper waste-handling procedures, selection guidance for personnel-protective gear, reducing the risk of dust explosions, managing MSDSs, proper chemicals-handling techniques and more. Focus is on specific engineering components, such as rotating machinery, vacuum systems, burners and flares. [more] |
|
 |
|
|
 |
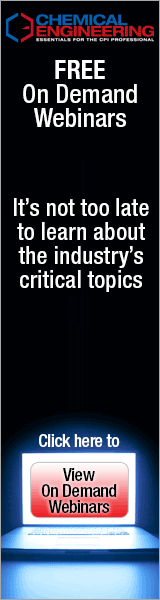
|
|