Despite the urgent need for decarbonization of industrial processes, carbon dioxide emissions from the industrial-scale manufacture of chemicals often prove difficult to abate and are on track to increase over the next decade. Some industrial sectors, such as power generation and transportation, are able to decarbonize with solar, wind and battery-storage technology. But chemical processes have been intricately optimized around fossil fuels, which are used as feedstocks and for process fuel. This reliance is so extensive that the chemicals sector accounts for 10% of global fossil fuel consumption, generating over 3 billion metric tons of CO2 equivalent every year (Figure 1).
As a result, the chemicals industry is under shareholder, customer and regulatory pressure to reduce carbon dioxide emissions and other forms of air and water pollution. Despite the pressure, major chemical manufacturing players are struggling to develop economically viable sustainability roadmaps. The authors’ company anticipates that this challenge will come into clearer focus later this decade, as chemical companies fail to achieve their 2030 emissions targets, while other sectors make substantial decarbonization progress. To effectively address emissions, we must ask: Does combustion chemistry have a place in a clean chemicals sector? And if not, what process technologies can effectively replace the traditional thermochemical processes?
We envision three major process technologies growing within a clean chemicals industry: 1) electricity-derived heat to power thermochemical processes, 2) biological pathways, and 3) direct electrification via electrochemistry. Our view is that as the market matures, these three approaches will co-exist, each centered around certain processes for which they are best suited. Within this solution landscape, electrochemistry has multiple advantages depending on the product, including: 1) health and safety benefits beyond decarbonization (specifically, the ability to avoid dangerous intermediates and harsh reagents); 2) better feedstock utilization (for example, controlled partial oxidations and reductions and coupled reaction systems); and 3) the ability to deliver modular production (that is, not requiring world-scale factories to achieve competitive economics).
Electrochemistry is an old technology that is now going mainstream
Despite a long history of successful high-volume production of certain chemicals (for example, Nylon-6,6 intermediate adiponitrile and the chlor-alkali process to produce chlorine and caustic soda), industrial electrochemistry has recently attracted renewed attention surrounding the investment in green hydrogen production. Over the past five years, interest in green hydrogen has grown dramatically, with tens of billions of dollars put towards R&D, manufacturing, and deployment of water electrolyzers. These massive investments are driving electrolyzer manufacturing down the learning curve and laying the foundation for the efficient, low-cost production of electrochemical reactors at scale. However, green hydrogen faces challenging economics, and cannot address the emissions associated with most chemical processes.
Fortunately, there is much more that electrochemical reactors can do beyond hydrogen production. Indeed, there are many chemical pathways for which researchers have demonstrated the technological feasibility of “electrosynthesis,” yet today they are largely not cost-competitive with legacy fossil-powered processes. However, with rigorous optimization of the electrocatalytic reaction environment within electrolyzers, we can drastically expand their functionality and reduce the cost of low-carbon chemicals.
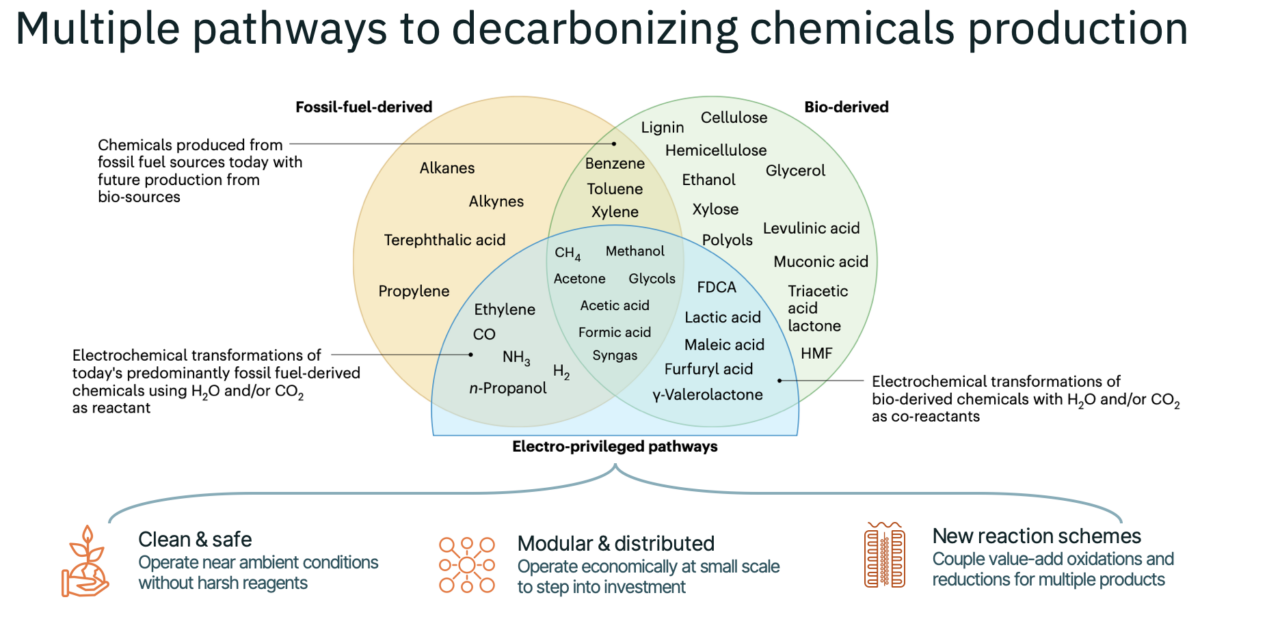
Figure 1. Electrochemical syntheses allow a pathway to decarbonization of the chemicals industry that complements fossil-derived and bio-based chemicals
There is much more we can do with electrochemistry beyond hydrogen
In addition to the commercial production of adiponitrile and the chlor-alkali process, as mentioned earlier, there have been laboratory demonstrations of hundreds of molecules that are accessible via electrosynthesis. The most widely studied of these (excluding hydrogen production) is the conversion of carbon dioxide to products like carbon monoxide, formate, ethylene, ethanol, methanol, monoethylene glycol (MEG) and others. Similarly, electrochemical nitrogen reduction to ammonia has attracted significant attention over the past decade. However, these products represent very large markets, and it will be challenging for new process technologies to compete at the scales and price points to effectively serve them in the near term. As we collectively develop and deploy efficient and low-cost electrochemical reactor technologies, many other processes have attractive economics and can significantly reduce greenhouse gas emissions.
To understand the opportunity, we must dig deeper into the engineering of electrochemical systems. Electrochemical reactions occur via electron transfer, often coupled with proton transfer (that is, oxidations at the anode, reductions at the cathode), and in addition to temperature and pressure, applied voltage acts as a critical knob we can turn to engineer efficient chemical transformations. A typical water electrolyzer runs at approximately 80°C and 1.8 V full cell potential, evolving oxygen at the anode and hydrogen at the cathode. In this example, voltage enables the disassociation of water at far lower temperatures than you would otherwise be able to achieve. Although this is not done in practice, reactors would need to be operated at temperatures in excess of 2,500 °C to generate hydrogen from water using heat alone. Accordingly, it is clear that electrochemistry provides new tools in chemical synthesis. But what specific advantages do they unlock for industrial manufacturing?
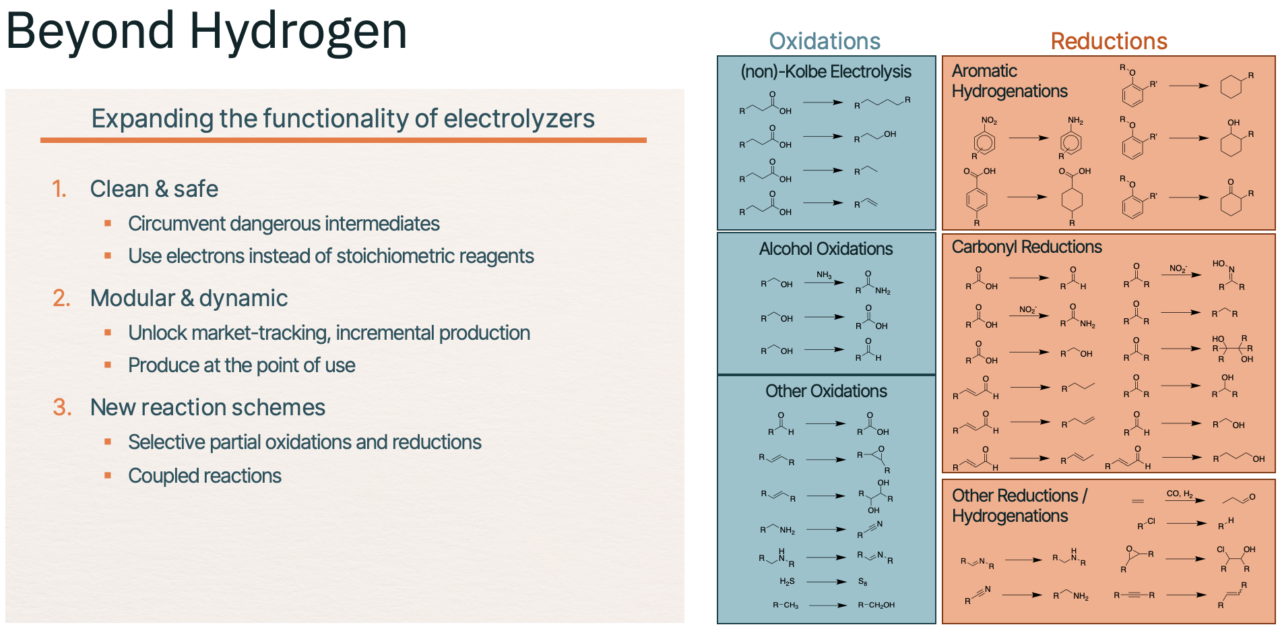
Figure 2. Electrochemistry has multiple uses in industry aside from the electrolysis of water to generate hydrogen
Advantages of electrochemistry
Electrochemical approaches to commercial chemical manufacturing can have advantages that go beyond decarbonization. Some of the areas are discussed below:
Health and safety benefits. Industrial thermochemical processes are typically run at high temperatures and pressures, often require harsh stoichiometric reagents, and can lead to over-oxidation or reduction to undesired products (carbon dioxide, for example). Conversely, electrochemical reactions typically operate at ambient pressures and temperatures, requiring no additional reagents, and fine-tuned control over potential and current densities can limit over-oxidation and over-reduction.
As an existing industrial example, Nylon-6,6 intermediate adiponitrile is produced both thermochemically and electrochemically. The thermochemical route involves the hydrocyanation of butadiene, typically requiring stoichiometric volumes of a highly toxic cyanide-based feedstock. The electrochemical route involves dimerizing C3 acrylonitrile molecules to C6 adiponitrile, which does not require other hazardous reagents. This represents a significant operational benefit due to the lowered health risks.
We can realize a similar benefit elsewhere in the Nylon-6,6 value chain. The status quo production of adipic acid results from the oxidation of KA oil (a mixture of cyclohexanone and cyclohexanol) using stoichiometric nitric acid. Both this process and the separate production of nitric acid generate significant nitrous oxide emissions; nitrous oxide is the third-leading contributor to greenhouse gas emissions after CO2 and methane. With ~273 times the global warming potential as CO2, nitrous oxide is considered a super-pollutant. Instead, we can use electrochemistry to oxidize KA oil to adipic acid, circumventing the need for nitric acid and completely eliminating nitrous oxide emissions associated with this process. In this way, we think of electrons as “clean reagents” that substitute for harsh oxidants or reductants and dramatically reduce the environmental impact of certain processes.
Extreme heat requirements represent another health and safety concern for plant operators. For example, the hydroprocessing of sour crude oil and gas generates large quantities of H2S, a highly toxic gas. Refineries typically use the Claus process to oxidize H2S to sulfur and water, but this requires furnaces that operate in excess of 1,000°C. Instead, we can leverage electrochemistry to achieve two major benefits: 1) treating H2S near ambient temperature (that is, less than 100°C); and 2) regenerating usable hydrogen from the process, as opposed to water. These benefits convey significant safety, sustainability and economic value.
Further, electrochemistry can unlock pathways that circumvent dangerous intermediates. Conventionally, ethylene glycol is produced from ethylene via explosive, carcinogenic, and EPA-regulated ethylene oxide intermediate. Alternatively, we can directly oxidize ethylene to ethylene glycol using electrochemistry, reducing the associated safety risk and regulatory burden.
Improved feedstock utilization. In addition to the environmental, health, and safety benefits noted above, electrochemistry enables improved feedstock utilization, both via 1) coupled value-add oxidations and reductions and 2) more selective partial oxidations and reductions than can be achieved via thermochemical processes. This can result in superior economics for electrochemical processes compared to the status quo.
In every electrochemical reactor, two reactions occur simultaneously: an oxidation at the anode, and a reduction at the cathode. A conventional water electrolyzer produces oxygen at the anode (which is typically vented, resulting in no value capture) and hydrogen at the cathode. However, many organic feedstocks can be electrochemically oxidized in place of water at the anode, while still producing hydrogen at the cathode. For example, we can convert bio-ethanol into acetic acid, opening up opportunities to create sustainable adhesives, paints and plastics. Ethanol’s lower oxidation potential enables operation at lower cell voltages, resulting in nearly a 50% step-change reduction in electricity consumption per unit of hydrogen output, while simultaneously making a valuable product at the anode.
Further, electrochemistry enables the fine-tuning of reaction conditions such that we can achieve more selective partial oxidations and reductions. One example is the partial oxidation of methane to methanol, circumventing the syngas intermediate – a longtime target of the chemical industry. Efforts to unlock this chemical pathway via thermal processes have not resulted in high enough selectivities for commercial production, as it is easy to over-oxidize methane to CO2 at elevated temperatures. In contrast, electrochemistry’s additional design tool – voltage – opens the door to greater control over reaction progress, and therefore to lower cost methanol production.
Finally, we can similarly take advantage of greater reaction control to run partial reductions. In particular, naphtha-derived ethylene typically contains >1 wt.% acetylene impurity. This impurity must be removed prior to downstream conversion to polyethylene, as acetylene poisons the polymerization catalysts. A typical semi-hydrogenation process requires separate production and storage of hydrogen, followed by a thermal hydrogenation step, where it is challenging to avoid over-reduction to undesired ethane. Conversely, a direct electrochemical hydrogenation enables 1) in situ production of protons from water within the reactor, precluding the need for independent infrastructure for hydrogen generation and storage, and 2) more selective semi-hydrogenation to reduce ethylene losses.
Improved economics for incremental production of chemicals. As in any business, increased demand for a product will bring additional manufacturing capacity online. Conventional chemicals production, however, substantially relies on economies of scale to achieve attractive unit economics, and as a result, total production capacity for a certain chemical can significantly exceed demand as soon as a new, large plant begins operation. This leads to 1) the need for infrequent but extremely large (nine-figure) investments to construct economically viable chemical plants, and 2) major fluctuations in market prices and the notable cyclic nature of the chemicals industry.
Electrochemical systems scale differently – they are more economical than thermochemical systems at small scale, but do not enjoy the same gains at massive scale. This presents an attractive opportunity for electrochemical systems to first penetrate chemical markets through their incremental increases in demand, precluding the need to build a new thermochemical plant with an order of magnitude more production capacity than the market is asking for. The inherent compatibility of electrochemical reactors with a modular approach to project development enables manufacturers to step into their investment and reduce off-take risk.
Electrochemistry is a versatile process technology with far-reaching potential
Beyond the brief case studies described above, chemical engineers have demonstrated numerous functional group transformations to be run efficiently via electrochemistry. Electro-oxidations include alcohol oxidations, carbonyl oxidations, amine oxidations, alkene oxidations, and certain oxidative coupling reactions, to name a few. Electro-reductions include carbonyl hydrogenations, nitrile hydrogenations, aromatic hydrogenations, reductive cross-couplings, alkene/alkyne hydrogenations, and dehalogenations, among others.
We are building a comprehensive roadmap of electrochemical solutions that solve pain points in chemical manufacturing – and can deliver economically attractive products. We believe that electrochemistry will play a critical role in chemical manufacturers’ sustainability roadmaps, as the industry establishes additional proof points and validates key value propositions.
Building new industrial ecosystems to foster this vision to reality
For electrochemistry to meaningfully contribute to the cleanup of the chemicals sector, achieving competitive production costs at scale is imperative. A “green premium” may be acceptable in the short-term, but long-term success requires electrochemistry to be cost-competitive without incentives. This is achievable — but only by constructing collaborative partnerships that streamline new technology development and deployment.
Significant challenges must be overcome before we can deploy new process technology at scale, as the chemicals industry has made massive investments into optimizing existing assets to produce chemicals at low cost. At the same time, the long-term financial performance of modern electrolyzers remains unproven.
The long history of successful high-volume production of some chemicals is encouraging, with industrial electrochemistry attracting renewed attention from the major investments in the green hydrogen ecosystem. However, green hydrogen alone is not enough for a sustainability roadmap; the DOE projects that the two leading technologies for chemicals decarbonization, green hydrogen and electrified process heat, can address up to 40% of chemicals-related emissions – but what about the remaining 60%? We believe that this is a moment with unique momentum for industrial electrochemistry beyond hydrogen production, and an excellent opportunity to produce a wide array of green chemicals in a way that is consistent with shareholder expectations.
Collaboration between industrial manufacturers, which have deep expertise and scale, startups, which have the means to rapidly develop technology, and government, which can offer catalytic capital, is essential to realize the potential of clean electrochemical systems. To accelerate the deployment of electrochemical solutions, we must identify the optimal chemical reactions to initially focus on based on economic, technical, and competitive criteria, before scaling up financial capital.
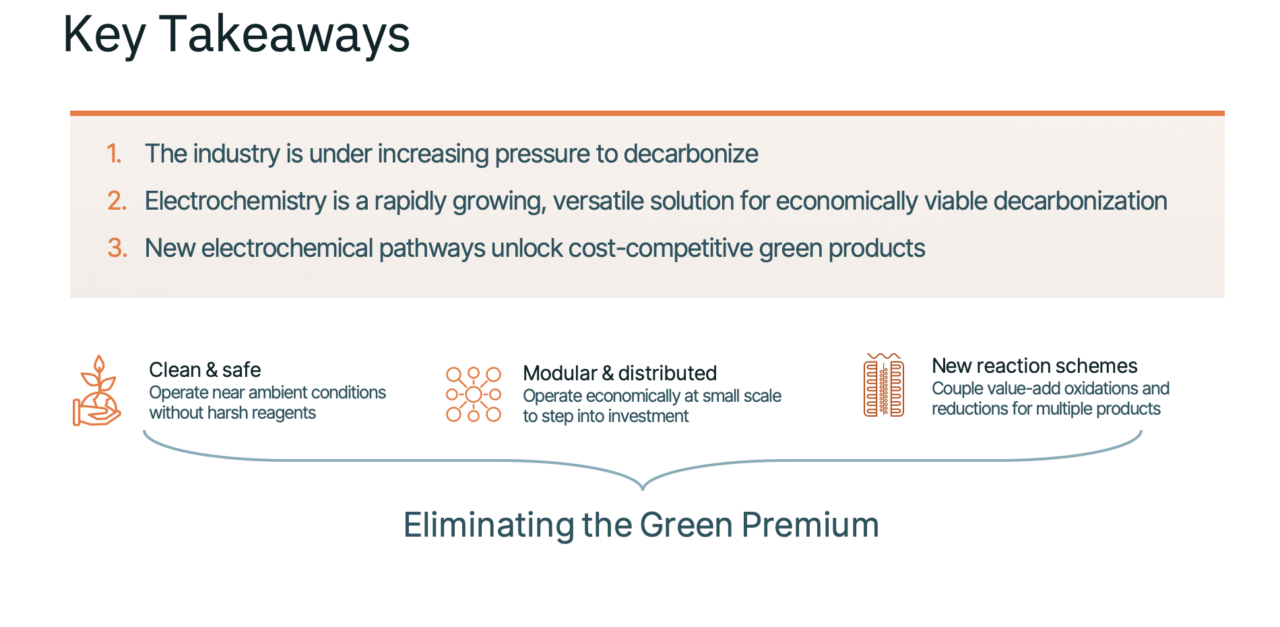
Figure 3. Electrochemistry is an approach to industrial decarbonization that has several other benefits
Decarbonizing chemicals is one of today’s most difficult and pressing climate challenges. Chemical companies understand this, but to deliver, they need clean chemistry solutions that can benefit their share prices — and an ecosystem of partners that can support them amidst a rapidly evolving landscape.
Edited by Scott Jenkins
Authors
Jeff Erhardt
With deep expertise in the global commercialization of disruptive technologies, Jeff’s leadership experience spans executive and board roles at high-growth private companies as well as large public enterprises. Before joining Mattiq, Jeff led AI-powered implementation at Intelligent Systems at General Electric for some of the company’s most critical businesses, including Aviation, Power Generation, Renewable Energy, and Oil & Gas. Jeff joined GE via the acquisition of Wise.io, a machine learning company, where he was CEO. Before joining Wise, Jeff was COO at Revolution Analytics, where he built the company into the leading disruptive provider of advanced analytics based on the open source language R. Jeff holds more than 30 patents, an engineering degree from Cornell, and an MBA from the Wharton School.
Mike Ashley
Dr. Michael Ashley is a versatile climate tech professional, having worked in roles ranging from laboratory research to clean power infrastructure project development. Since joining Mattiq in early 2021, Mike has helped build Mattiq’s go-to-market and product strategies, which strive to accelerate the profitable decarbonization of the chemical industry. Mike received his PhD in Chemical Engineering and certificate from the Kellogg School of Management at Northwestern University.
Jordan Swisher
Dr. Jordan Swisher is a leading expert in the fields of precision polymers, electrocatalysis, and, most notably, catalyst synthesis, having authored one of the seminal works on nanoreactor technologies for catalyst synthesis. As the Director of Chemistry at Mattiq, he leads design and development efforts for novel electrochemical systems. Named a ‘Mover and Shaker’ by the Catalyst Review, Jordan has been involved in the development of Mattiq’s key technologies for over four years and is the lead on several federally funded grants and author on a number of patents related to Mattiq technology. Before joining Mattiq, he was an International Institute for Nanotechnology Postdoctoral Fellow at Northwestern University. Jordan received his BS in Chemistry from Case Western Reserve University and his PhD in Chemistry from the University of Pittsburgh.