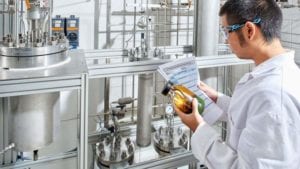
Source: EDL Anlagenbau
EDL Anlagenbau GmbH (EDL; Leipzig, Germany; www.edl.poerner.de) sold a license for its two-stage extraction technology to the Middle East in the 4th quarter of 2018. With this technology process, oils are produced in an efficient and eco-friendly way. These oils play an important role as high-quality tender oils for the production of automobile tires, for example.
The new solvent-extraction plant for the production of eco-friendly, high-quality process oils (TDAE, Treated Distillate Aromatic Extract) based on the EDL license allows users to meet the latest environmental and quality requirements and to expand their product portfolio. The new solvent extraction plant will be designed under consideration of new resource-saving technologies.
As part of the licensing, EDL carries out the required laboratory tests and pre-pares the PDP (Process Design Package) for the plant and the FEED (Front End Engineering Design) for the extractor section.
The required process parameters and the optimum process conditions are determined in EDL’s own test facilities (photo) based on customer and product requirements, as well as the hydraulic data of extractor internals. This allows a safe design of the plant for the entire range of feedstock available at the customer.
The basic principle of EDL’s technology to obtain high-quality base and process oils from vacuum distillates (lube cuts) and deasphalted oil (DAO) is a two-stage extraction process. As a first step of extraction the aromatic compounds are removed as so called DAE (Distillate Aromatic Extract) or RAE (Residual Aromatic Extract). NMP (or furfural) is used as solvent. At the same time aromatic-rich oils are obtained that can be used to produce high-quality base oils. In a second extraction stage using a proprietary solvent mixture, DAE and RAE are transformed into high-quality process oils such as Treated Distillate Aromatic Extract (TDAE) and Treated Residual Aromatic Extract (TRAE) having a low level of polycyclic aromatic hydrocarbons (PCA).
DAE and RAE are required as tender oils to produce rubber products, such as tires, hoses, belts, cable insulation, floor coverings and shoe soles. Due to the high percentage of PCA being carcinogenic, mutagenic and reprotoxic DAE and RAE are no longer used today. With further processing of DAE and TAE to TDAE and TRAE resp. in the second extraction stage the limit value for PCA clearly falls below 3% by mass as required by European Directive 2005/69/EC without impairing the excellent properties as tender oil. Thus, a decisive contribution to the protection of humans and the environment is made.