Tackling the challenge of plastic pollution and waste remains at the forefront of corporate and government sustainability strategies. In fact, the United Nations (UN) has committed to delivering a legally binding agreement by the end of the year to transform how the world produces and disposes of plastics.
According to the Organisation for Economic Co-operation and Development (OECD; Paris, France, www.oecd.org), global plastics use will triple between 2019 and 2060, from 460 million tons to 1.3 billion tons, with almost half of this amount going to landfill. What’s more, only 9% of the plastic ever produced has been recycled and 19% has been incinerated, further highlighting the need for urgent action.
Looking at industries that are major users and consumers of plastics, the chemical process industries (CPI) come to mind quickly. From chemical storage and ventilation to packaging and cleaning, the chemicals sector is one of the biggest manufacturers of plastics today.
The process of plastics manufacturing in the chemicals industry is very carbon-intensive — in fact, the sector uses around 28% of all industrial energy and 10% of global final energy. This energy-intensive process highlights how crucial it is for the industry to reduce its energy usage in plastic production if the sector wishes to make production more efficient and sustainable.
To combat this, the chemical industry must seek innovative ways to build a truly circular economy — and among the keys to success are digitalization and software-defined automation.
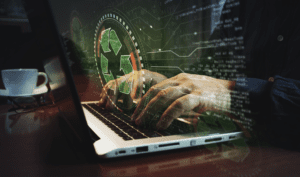
Digital technologies provide an essential pillar for the implementation of more sustainable processes and products
Why the sector has a vital role to play
A world without plastics is unrealistic. There will always be a need for plastics if we wish to keep hospitals running, our food system thriving and our homes insulated. For the chemicals sector in particular, plastics are a vital resource, as they are non-reactive, making them ideal for storage, packaging and insulation.
Being such a desired resource, the CPI have a responsibility to address recycling inefficiencies and make their processes more sustainable. As such, the sector has a duty to prioritize automation and invest in digital technologies that make production and processes more streamlined and environmentally friendly. Looking ahead, the CPI must overhaul its existing recycling ecosystem and processes to achieve a truly circular economy. So, what does best practice look like?
Making circularity a reality
For the chemicals sector, transitioning to more circular recycling models should include building a seamless connection between recycling facilities, infrastructure and the supply chain. Additionally, there is a need to sort techniques with innovations such as artificial intelligence (AI) and embedded digital product watermarks. Next, the development of new chemical recycling methods and improved mechanical recycling will prove crucial.
Finally, plastic products should be designed with circularity in mind. Industry leaders must consider sustainable designs and the circular economy of plastic products to not only extend their life and improve their recyclability, but also to provide safer options for people and ecosystems.
Success here will depend on digitalization, forging cross-sector partnerships and setting up a reverse supply chain. For instance, to de-risk operations and reduce costs, chemical companies can look to integrate process and electrical simulation to create more sustainable product designs.
Industry leaders could also use digital-twin software in the product design process and modular design for process, electrical, automation and digital systems to further optimize costs, enhance speed of deployment and increase operational efficiency. Businesses can even use open automation platforms that enable multiple project stakeholders to collaborate, minimizing error.
Then, to help end users reduce their consumption, it is important to establish relationships quickly and work closely with suppliers of recycled material to test recycled plastic and to encourage them become an early adopter of more sustainable production. This is especially true for high-performance plastic products for electronics and electrical applications, as well as for medical and construction applications. On the software and automation side, picking partners that specialize in circular transformation is crucial to successful planning and implementation.
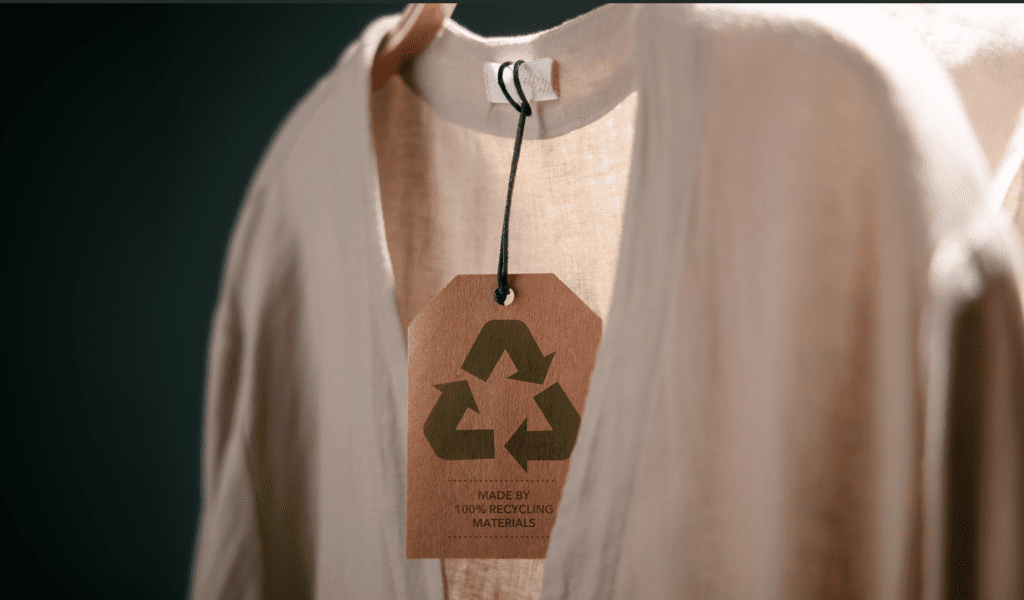
Manufacturers of consumer goods benefit from close partnerships with plastics processors in the adoption of recycled materials into their products
Vendors who provide modular, agnostic software can be valuable partners, providing organizations the freedom to choose the optimal technology for their plant and easily scale to new sites.
Finally, building a reverse supply chain means taking back products from regional operations, customers and partners to reuse and recycle. This is not possible without a digitalized, fully-connected supply chain that ensures the quality and availability of materials and products.
The role of software-defined automation
As the industry continues to innovate in plastic production and processing, the fresh solution set to make monumental changes is software-defined automation.
Software-defined automation systems decouple hardware from software, allowing devices and equipment to be freely connected across architecture layers, regardless of the manufacturer. It acts as the digital backbone of industrial operations, providing the foundation to make more informed decisions. This new generation of automation systems intertwines operational technology and information technology (OT and IT), enabling the exploitation of advanced functionalities for operations management and data analytics — crucial to find future ways to evolve plastics production, recycling and reuse.
This approach allows industry leaders to effectively de-risk operations and push the boundaries of their technology. It allows leaders to reconfigure systems quickly when they see opportunities to improve efficiency, while avoiding supply chain issues due to the hardware agnostic nature of the system.
For instance, in March 2024, GR3N S.A. (Lugano, Switzerland) successfully demonstrated how this technology will be used to transform plastic recycling processes. Working in partnership with Schneider Electric (Paris), GR3N expects to treat over 40,000 tons/yr of polyethylene terephthalate (PET) waste, making it the first plastic recycling plant to use the shared automation runtime managed by Universal Automation, based on the IEC 61499 standard. The modular design of their control software, supported by digital continuity across the whole plant lifecycle with automation-focused decision making happening at conception, reduces human error at the development stage by 40%. What’s more, GR3N can expect a 30% reduction in engineering costs linked to automation thanks to the software-defined approach.
Ultimately, in an era of monumental changes to how we deal with plastics, new technologies like software-defined automation will be what is needed to make advanced plastic recycling a reality at scale. Only by using plastics better, longer and again can we start to see a real difference made in the way we drive plastics circularity and in order to do that we need a more digitalized way of working. This innovative technology can be a catalyst for not only more environmentally responsible operations, but more profitable ones too. ♦
Edited by Mary Page Bailey
Author
Delphine Largeteau is the global sustainability consulting director for energies and chemicals at Schneider Electric (www.se.com). Prior to her current assignment, she held several director-level roles at Axens. She holds chemical engineering degrees from Université de Technologie de Compiègne in France.