Last month, the chemical engineering profession began to feel its first aftershocks from an explosion that occurred nearly two years ago at a plant that most of you would be hard-pressed to recall. The delivery came in an accident report issued by the U.S. Chemical Safety Board (CSB; www.csb.gov). The report determined that the massive December 2007 explosion and fire at T2 Laboratories in Jacksonville, Fla. was caused by a runaway chemical reaction that likely resulted from an inadequate reactor-cooling system.
Concluding that T2 did not recognize all of the potential hazards of the process for making a gasoline additive, the report calls for improving the education of chemical engineering students on chemical reactivity hazards. In fact, the American Institute of Chemical Engineers (AIChE; New York; www.aiche.org) and the Accreditation Board for Engineering and Technology (ABET; Baltimore, Md.; www.abet.org) have been specifically petitioned to work together to include reactive chemical education in baccalaureate chemical-engineering curricula across the country.
Chemical testing by the CSB found that the recipe used by T2 created two exothermic, or heat-producing, reactions; the first was an intended part of producing MCMT but the second, undesired reaction occurred when the temperature rose above 390ºF, slightly higher than the normal production temperature. The cooling system likely malfunctioned due to a blockage in the water supply piping or a valve failure. Consequently, the temperature and pressure inside the reactor began to rise uncontrollably in a runaway chemical reaction. Approximately ten minutes after the initial cooling problem was reported, the reactor burst and its contents exploded. “This is one of the largest reactive chemical accidents the CSB has investigated,” said Chairman John Bresland.
The CSB found that although the two owners of T2 had undergraduate degrees in chemistry and chemical engineering, they were likely unaware of the potential or the consequences of a runaway chemical reaction. The CSB noted that most baccalaureate-level, chemical-engineering curricula in the U.S. do not specifically address recognition or management of reactive hazards. The CSB has released a nine-minute safety video, “Runaway: Explosion at T2 Laboratories,” containing a description of the causes, consequences, lessons and recommendations resulting from the accident.
In a statement issued by AIChE in reaction to the report, Scott Berger, executive director of AIChE’s Center for Chemical Process Safety (CCPS) said, “As this terrible tragedy emphasizes, we agree with CSB that chemical engineering students should learn more about process safety and about chemical reactivity, in particular.” Berger noted that CCPS produces prepared lectures and teaching materials on process safety for U.S. universities through its Safety in Chemical Engineering Education (SACHE) program. Professors can obtain educational materials from a Website to use in their classrooms. Meanwhile, SACHE offers an online process-safety-certification program directly to chemical engineering students.
While the heat of the report is being focused on academia, the reality is that the existing training deficit for practicing chemical engineers could take decades to flush itself out of the workforce. Meanwhile, recent staff reductions and the expanded responsibilities for each ChE raise the chances for additional gaps in process safety expertise. That being the case, it’s up to each of us to be proactive and make sure that chemical engineers, young and old, stay current with the training they need. Our effort in that vein continues with a new article on Preventing Dust Explosions.
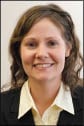
Rebekkah Marshall