New column internals boost efficiency and improve reliability of distillation towers
In the chemical process industries (CPI), the majority of separations are done via distillation columns. And, when the rest of the process relies upon those columns, inefficiencies, bottlenecks and shutdowns are problematic. In an effort to keep distillation processes — and the rest of the plant — chugging along, column internals are being tweaked and re-worked to help optimize efficiency and reliability of the columns.
“Whether it is in refining, chemical processing or producing plastics, most of the separation between organic chemicals is being done with distillation. At the same time, there is a constant pressure for chemical processors to make their processes more cost effective,” says Izak Nieuwoudt, chief technical officer with Koch-Glitsch (Wichita, Kan.; www.koch-glitsch.com). “Because distillation columns are a huge energy consumer and because people don’t want to spend a lot of time fixing equipment, increasing efficiency and reliability of the columns is at the forefront right now.”
Often after a process is up and running, processors find that the energy consumption is much higher than they were expecting, says Antonio Garcia, mass transfer business development manager with AMACS Process Tower Internals (Arlington, Tex.; www.amacs.com). “To obtain better energy efficiency, they must explore their options to improve the mass-transfer performance,” he says. “In addition, processors are often looking for ways to de-bottleneck the process in order to obtain better separation and capacity requirements and fouling is a common cause of bottlenecks, so finding technologies that assist with these issues is also important.”
Bottlenecks and downtime caused by fouling or mechanical issues, such as vibration or mechanisms within the columns coming apart, can become very costly. “It’s very expensive every time you have to shut down a distillation column, because it often results in the shutdown of upstream and downstream units, as well,” says Nieuwoudt. “And, these unplanned shutdowns result in large losses per day.”
For this reason, manufacturers of column internals are developing products designed to aid processors in increasing energy efficiency and reliability.
Improving efficiency & reliability
Replacing conventional trays and packings with newer, advanced solutions is often necessary for a processor who is seeking higher efficiency, capacity and reliability, so manufacturers are constantly looking to improve upon their offerings.
For instance, Raschig GmbH (Ludwigshafen, Germany; www.raschig.com) has recently released the Raschig Super-Ring Plus, a new, high-performance random packing that exceeds the performance of the previous Raschig Ring. “The optimized structure of Raschig Super-Ring Plus enables a further capacity increase at constant efficiencies,” says Micheal Schultes, technical director at Raschig. “The product is the result of design development based on many years of research. The target was to stay with all the advantages of the Super-Ring, but improve capacity and reduce pressure drop.”
The resulting product minimizes pressure drop by arranging flat sinusoidal strips into an extreme open structure, maximizes capacity by film flow preference on continuous sinusoidal-strip arrangements, increases efficiency by minimizing droplet formations inside the packing and decreases fouling tendency by reducing droplet development and offering low pressure drop. Fouling sensitivity is also reduced by generating continuous liquid films, wetting the entire packing element.
Likewise, AMACS has been doing research to improve its SuperBlend product. “Research has shown that by replacing existing random packing with our SuperBlend 2-PAC, tower efficiency can be increased by 20% or capacity by 15%,” says Moize Turkey, manager, applications engineering, with AMACS. The SuperBlend 2-PAC technology is a blend of high-performance packing sizes placed in a single bed. “We blend two sizes of the best metal random geometry and, when combined, the patented blend achieves the efficiency benefits of the smaller packing size, while retaining the capacity and pressure drop of the larger packing size,” he says. The blended bed is recommended for absorption and stripping, fine chemical distillation, refinery fractionators and retrofit opportunities in any mass- or heat-transfer tower limited by conventional or third-generation random packing.
Improvements to internals are also being developed to assist with issues such as fouling and difficult conditions.
“Reliability is extremely important for day-to-day considerations. No matter how well a device performs, if it can’t stand up to the fouling conditions in a process, it won’t be successful,” says Mark Pilling, manager of technology USA with Sulzer (Winterthur, Switzerland; www.sulzer.com). “Sulzer has spent a tremendous amount of time over the last five years developing a complete line of fouling-resistant equipment.” In trays, the company offers VG AF and anti-fouling trays, and recently launched UFM AF valves, which are both high performance for capacity and efficiency, as well as extremely fouling resistant. In packings, the company launched Mellagrid AF anti-fouling grid packings, which are suitable for highly fouling packing applications, such as vacuum tower wash sections.
Pilling adds that for foaming issues, Sulzer has been working on a two-pronged approach. “While we develop equipment and designs to handle foaming applications, we also work with our customers to determine potential foaming applications,” he says. “Once you know foaming exists, you can design for it. It’s the cases where a customer will have a foaming condition and not know about it that tend to create problems. We see all sorts of foaming, such as Marangoni, Ross foams and particulate foams and work with customers to identify such situations.”
And, for applications where fouling and coking can be very severe, Koch-Glitsch developed Proflux severe-service grid packing, says Nieuwoudt (Figure 1). The new high-performance severe-service grid packing combines the efficiency of structured packing with the robustness and fouling resistance of grid packing. It is an assembly of sturdy corrugated sheets welded to heavy-gauge rods. The combination of welded rod assembly and corrugated sheets of increased material thickness provides a robust design that resists damage from tower upsets or erosion. The gaps between the sheets provide improved fouling resistance. “The packing has been installed almost 100 times now in very severe-fouling services and is really doing well compared to the products it is replacing. The longer run life and the lower pressure drop it provides results in lower operating costs for the customer,” says Nieuwoudt.
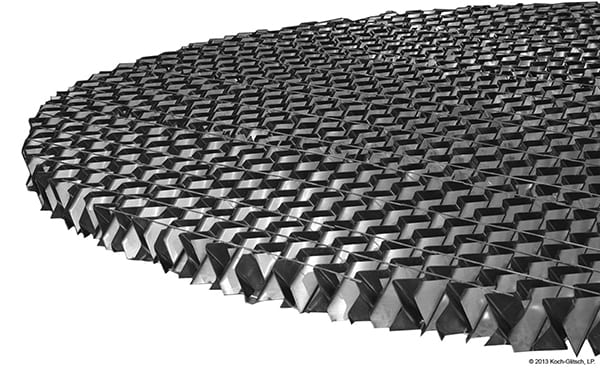
Figure 1. Proflux severe-service grid packing is a high-performance severe-service grid packing that combines the efficiency of structured packing with the robustness and fouling resistance of grid packing Koch-Glitsch
Addressing specific challenges
When it comes to distillation, there are also often challenges specific to a process that need to be addressed through special measures.
“There is a market for tailor-made solutions that are tuned to the specific process and customer needs,” says Christian Geipel, managing director, with RVT Process Equipment (Steinwiesen, Germany; www.rvtpe.com). “This is especially valid for revamps of existing plants that are modified to fulfill new demands. The challenges are various and include objectives such as longer and more predictable run lengths for fouling applications, higher capacity and lower pressure drop or wider operating ranges for more flexibility.”
To address specific needs, RVT has developed a high-capacity structured packing, the SP-Line (Figure 2). “Due to modified channel geometry, lower pressure drop and higher capacity are achieved.” Further, for very low liquid loads, another application-specific challenge, these packings can be combined with new types of liquid distributors. “An improved spray nozzle distributor that combines spray nozzles with splash plates was developed and is successfully used in applications like refinery vacuum columns,” says Geipel. “It reduces entrainment and therefore fouling in the packing sections above the distributor without sacrificing liquid distribution quality to the packing section below.”
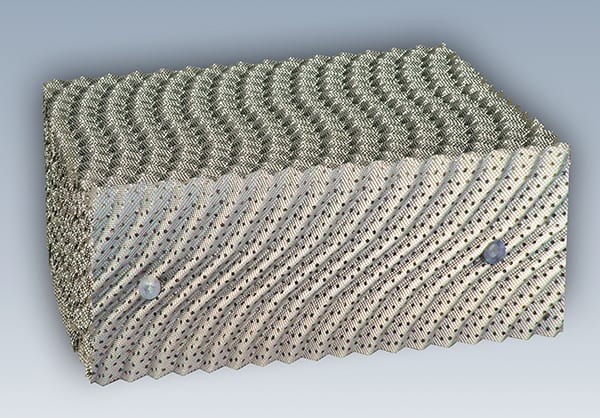
Figure 2. A new, high-capacity structured packing, the SP-Line from RVT, offers modified channel geometry, lower pressure drop and higher capacity RVT Process Equipment
Another new liquid distributor from RVT (Figure 3) is a trough-type distributor with splash plates that combines low liquid rates with a higher operating range and a robust, fouling-resistant design.
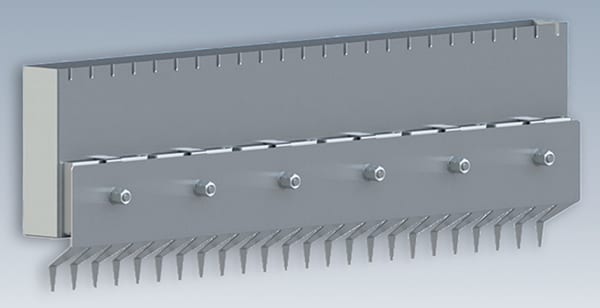
Figure 3. For very low liquid loads, another application-specific challenge, packings can be combined with new types of liquid distributors RVT Process Equipment
Similarly, GTC Technology US, LLC (Houston; www.gtctech.com) is developing new products to assist processors with improving the performance of distillation columns based on their specific needs. One of the latest developments includes GT-OPTIM high-performance trays, says Brad Fleming, general manager for GTC’s Process Equipment Technology division. Hundreds of industrial installations plus testing at Fractionation Research Inc. (FRI; Stillwater, Okla.; www.fri.org) have demonstrated that the high-performance tray achieves significant efficiency and capacity improvement over conventional trays. The cross-flow trays are customized to the end user’s needs to achieve high efficiency via a combination of patented and proprietary devices that make up each tray design. “We can provide a collection of technologies and features that can be employed in order to address specific objectives,” notes Fleming. “One processor’s objective might be to increase efficiency, while another wants to increase capacity and still another wants to minimize pressure drop, mitigate fouling or extend runtime. We have many different weapons in our equipment design arsenal, so we are able to focus on the customer’s targeted objective for their specific process improvement.”
Meanwhile, AMACS has addressed another common distillation challenge faced by petroleum refineries, petrochemical plants, gas plants and similar facilities. Often, a vertical knockout drum or separator with mist-elimination equipment installed fails to remove free liquid from a process gas stream. “Instead of trying to address or repair symptoms, we look for the root cause, which usually involves the mist-elimination equipment in the knockout drum,” says AMACS’s Garcia. To address the problem, the company developed the Maxswirl Cyclone, a high-capacity, high-efficiency mist-elimination device that uses centrifugal forces to provide state-of-the-art separation performance.
The Maxswirl Cyclone tubes consist of a fixed swirl element, which applies centrifugal force on mist-laden vapor to separate entrained liquid from gas flow. In this axial-flow cyclone, the resulting centrifugal force pushes liquid droplets outwards, where they create a liquid film on the cyclone inner wall. The liquid passes through slits in the tube wall and gets collected at the bottom of the cyclone box and drained by gravity. The dry gas concentrates in the center of the cyclone tube and exits through the cyclone.
Meanwhile, DeDietrich (Mainz, Germany; www.dedietrich.com) is focusing effort on providing columns and internals for highly corrosive processes at temperatures up to 390°F, says Edgar Steffin, head of marketing with DeDietrich. “Columns up to DN1000 are made of QVF borosilicate glass 3.3 or DeDietrich glass-lined steel. Bigger columns up to DN2400 are made of DeDietrich glass-lined steel only. The corrosion-resistant materials are made of borosilicate glass 3.3, SiC, PTFE or Tantalum” (Figure 4).
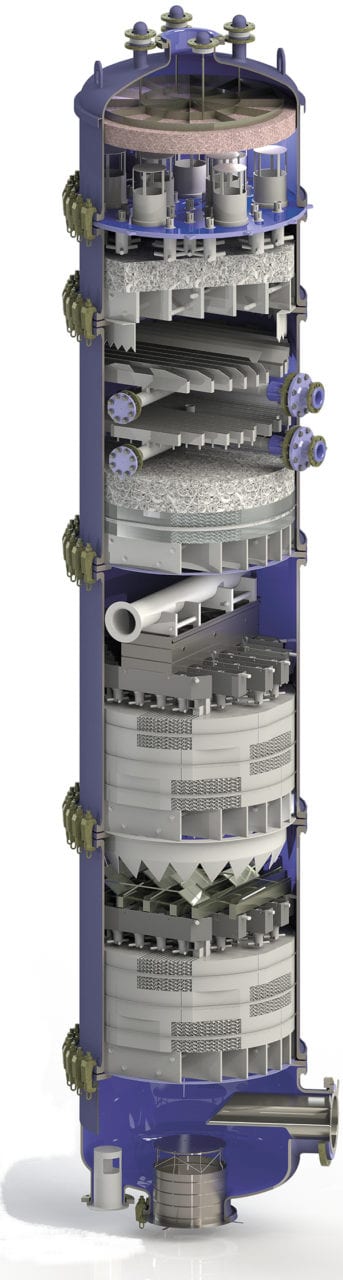
Figure 4. DeDietrich focuses on columns and internals for highly corrosive processes at temperatures up to 390°F. Columns up to DN1000 are made of QVF borosilicate glass 3.3 or DeDietrich glass-lined steel. Bigger columns up to DN2400 are made of DeDietrich glass-lined steel only. The corrosion-resistant materials are made of borosilicate glass 3.3, SiC, PTFE or tantalum DeDietrich
He adds that most processes at elevated temperatures above 300°F require the avoidance of PTFE. SiC has a higher temperature resistance and permits the design of bigger distributors and collectors that are less sensitive for feeds containing solids or those tending to foam, degas or to flash.
The company’s Durapack structured packing in borosilicate glass 3.3 is suitable for corrosion-resistant glass 3.3 or glass-lined steel columns, as it has the same corrosion resistance as the glass column and keeps its thermal stability at higher temperatures compared to polymers. Borosilicate glass 3.3 is non-porous, which substantially cuts erosion and corrosion compared to equivalent ceramic packing.
And, towers that have a side cut, but are thermally inefficient, says GTC’s Fleming, may be good candidates for dividing-wall column technology. “Many distillation columns have a top and bottom product, as well as a side-draw product, but with this comes a lot of thermal inefficiency. Dividing-wall column technology — where you revamp the traditional column — is one way to increase capacity while reducing energy consumption or reducing the yield impurity of the products,” he says (Figure 5).
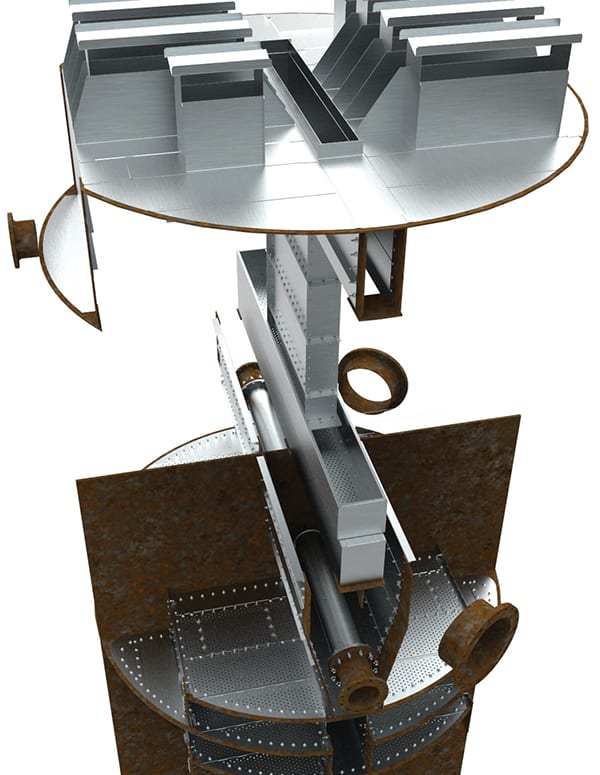
Figure 5. Towers that have a side cut, but are thermally inefficient, may be good candidates for dividing-wall column technology GTC Technologies
The dividing-wall column separates a multi-component feed into three or more purified streams within a single tower, eliminating the need for a second column. The design uses a vertical wall to divide the middle of the column into two sections. The feed is sent to one side of the column, called the pre-fractionation section. There, the light components travel up the column, where they are purified, while the heavy components travel down the column. The liquid flow from the column’s top and the vapor flow from the bottom are routed to their respective sides of the dividing wall.
From the opposite side of the wall, the side product is removed from the area where the middle-boiling components are most concentrated. This arrangement is capable of producing a much purer middle product than a conventional side-draw column of the same duty, and at higher flowrate.
“The conversion to a dividing-wall column is investigated when you’re looking at making significant improvements you couldn’t do otherwise within the constraints of a traditional tower, but if you can convert to dividing-wall technology, you will see significant decrease in energy consumption,” he says. “Generally, there is a 25 to 30% reduction in overall energy consumption for a given throughput, dramatically improved yield and purity of products and often an increase in throughput, as well.”
He adds that there is also opportunity to use a dividing-wall column to replace a traditional two-tower sequence. “You can use dividing-wall columns to perform the same operation and produce the same products, but you’re doing it in one physical tower in comparison to a two-tower scheme. In the grassroots realm, a substantial reduction in capital expenditures can be achieved with dividing-wall column technology.”