This column is based on “Dimethyl Ether Production from Natural Gas and CO2 (Direct Method) – Cost Analysis,” a report published by Intratec. It can be found at: www.intratec.us/analysis/dimethyl-ether-production-cost.
Dimethyl ether (DME) is the simplest aliphatic ether, containing only two carbon atoms. This organic compound has been used in the production of the methylating agent dimethyl sulfate, and as an aerosol propellant, a coolant and in a number of other applications. Over the past few years, DME has been increasingly viewed as a “clean” and economical alternative fuel for diesel engines, able to achieve high performance and low emissions (CO, NOx and particulate matter) when burned as fuel.
The process
The present analysis discusses an industrial process for the production of DME from natural gas and carbon dioxide (direct method). The process comprises three major sections: (1) production of synthesis gas (syngas); (2) DME synthesis; and (3) purification (Figure 1).
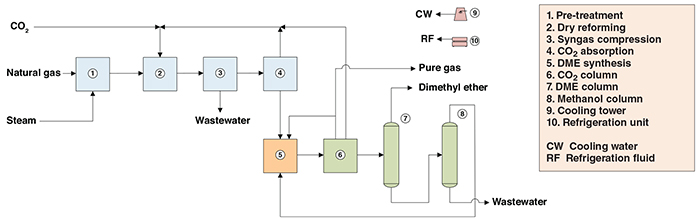
Figure 1. The diagram shows the process for production of dimethyl ether from natural gas and CO2 (direct method)
Syngas production. Natural gas feedstock is treated in zinc oxide beds for removal of sulfur compounds, and in a pre-reformer (fixed-bed-type reactor) that converts higher hydrocarbons contained in the feed gas into a gas rich in methane and hydrogen, to protect the catalysts. Then, the treated gas is fed to a dry reformer, in which the methane reacts catalytically with CO2, generating CO and H2 (syngas). The reformer outlet stream is cooled, compressed and then fed to an absorption column for the separation of unconverted CO2 using a methanol wash.
DME synthesis. The syngas is then fed to a fixed-bed synthesis reactor, in which it is directly converted to DME. Direct synthesis of DME in this way is carried out in the presence of a bifunctional zeolite-based catalyst system (Cu-Zn-Al/ZSM-5 catalyst). The reactor outlet gas mainly consists of DME, methanol, and unconverted hydrogen, CO and CO2.
Purification. The effluent from DME synthesis is cooled, and DME and methanol are separated from the gases by condensation. The separated gas is partially recycled to the DME synthesis stage, with a small purge. The DME-methanol condensate stream is then passed through distillation columns. In the CO2 column, carbon dioxide is removed from the DME and recycled to the dry reforming step. In the DME column, DME product is purified from methanol and directed to storage facilities located outside battery limits. Finally, wastewater is separated in the methanol column and the methanol obtained is recycled to the DME synthesis step.
Production pathways
Until the 1970s, DME was largely produced as a byproduct in the high-pressure production of methanol. Since this technology was phased out, different processes have been employed for DME production, including methanol dehydration, direct synthesis from syngas and others (Figure 2).
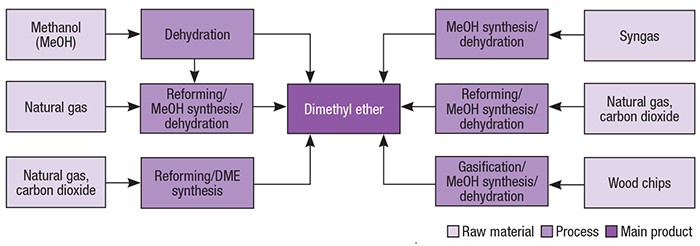
Figure 2. DME can be produced via a number of pathways, as shown here
Economic performance
The total operating cost (raw materials, utilities, fixed costs and depreciation costs) estimated to produce DME was about $500 per ton of DME in the first quarter of 2017. The analysis was based on a plant constructed in the U.S. with capacity to produce 110,000 metric tons of DME annually.
Edited by Scott Jenkins
Editor’s note: The content for this column is supplied by Intratec Solutions LLC (Houston; www.intratec.us) and edited by Chemical Engineering. The analyses and models presented are prepared on the basis of publicly available and non-confidential information. The content represents the opinions of Intratec only. More information about the methodology for preparing analysis can be found, along with terms of use, at www.intratec.us/che.