Understanding the differences among key temperature-control devices, such as heaters, coolers and heat exchangers, allows users to realize their unique benefits
When it comes to temperature control in industrial, commercial and residential settings, three key devices are often considered: heat exchangers, coolers, and heaters. Each of these units plays a crucial role in maintaining desired temperatures and ensuring efficient energy use. However, the three types of systems are not interchangeable; each device has its unique functions, design and applications. This article delves into the differences among these devices, as well as their unique roles, how they work and their respective benefits in various applications.
Heat exchangers
Heat exchangers are devices designed to transfer heat between two or more fluids without allowing them to mix. They are widely used in industries ranging from power generation and chemical processing to HVAC (heating, ventilation and air conditioning) systems. Heat exchangers can serve both heating and cooling purposes, depending on the specific application requirements.
The basic principle behind heat exchangers is thermal exchange, where heat energy is transferred from a higher-temperature fluid to a cooler one. The fluids can be gases or liquids, and they can flow in parallel, counterflow, or crossflow arrangements, depending on the design. The efficiency of a heat exchanger is determined by its ability to maximize the transfer of heat while minimizing the pressure drop and energy consumption. The three flow arrangements are outlined in the following sections.
Parallel flow. Both fluids enter the heat exchanger from the same side and flow in the same direction. This design is simpler, but less efficient, than the other two designs in terms of heat transfer.
Counterflow. The fluids enter the heat exchanger from opposite ends and flow in opposite directions. This design is more efficient than parallel flow because it maintains a larger temperature gradient between the fluids, enhancing heat transfer.
Crossflow. The fluids move perpendicular to each other, which is often used in applications where space is limited. This design can be efficient depending on the flowrates and temperature differences.
Types of heat exchangers
There are several types of heat exchangers, each suited for specific applications:
Shell-and-tube heat exchangers. Comprising a series of tubes enclosed within a shell, these exchangers are commonly used in power plants, petroleum refineries and chemical processing plants (Figure 1). They are versatile, can handle high pressures, and offer good heat transfer rates.
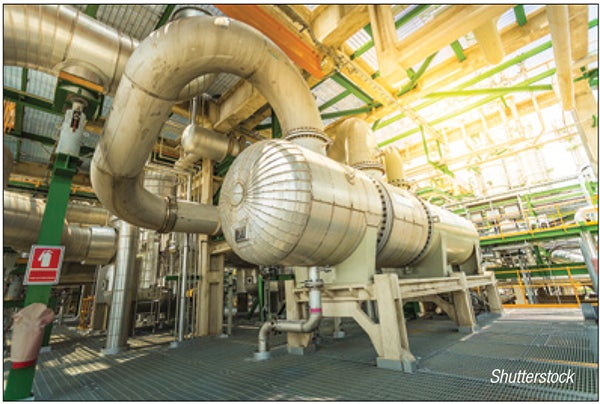
FIGURE 1. Shell-and-tube heat exchangers, common in power-generation, petroleum refining and chemical manufacturing facilities, are versatile and can handle high pressures
Plate heat exchangers. Plate heat exchangers consist of multiple thin, slightly separated plates that have large surface areas and narrow fluid-flow passages. They are compact and efficient, often used in HVAC, food-and-beverage manufacturing and pharmaceutical processes.
Air-cooled heat exchangers.These exchangers use ambient air to cool the process fluid and are often used in applications where water is scarce or in remote locations. They are commonly found in petrochemical plants and natural-gas processing facilities.
Finned-tube heat exchangers. Finned-tube heat exchangers are designed to improve heat transfer rates by increasing the exchanger surface area with fins. They are used in air conditioning, refrigeration and automotive manufacturing.
Heat exchanger applications
Heat exchangers are critical across a variety of applications, including those listed here:
Power generation. Heat exchangers are used in boilers, condensers and nuclear reactors to transfer heat efficiently.
Chemical processing. In chemical facilities, heat exchangers are essential for maintaining reaction temperatures, preheating feedstock, and condensing products.
HVAC systems. Heat exchangers help in both heating and cooling processes, making buildings more energy-efficient.
Food-and-beverage industry. Heat exchangers are used to pasteurize milk, and for heat-treatment of liquids and cooling products.
Automotive. Heat exchangers are employed in vehicle radiators and intercoolers to manage engine temperature and increase efficiency.
Coolers
Coolers are devices specifically designed to remove heat from a fluid or room space to lower its temperature. They are essential in applications where maintaining low temperatures is critical, such as in industrial processes, data centers, food storage and air-conditioning systems.
Coolers work by absorbing heat from a target area or fluid and dissipating it elsewhere. The cooling process can be achieved through various methods, including those described here:
Refrigeration cycle utilizes a refrigerant that circulates through a cycle of evaporation and condensation, absorbing heat from the surroundings and releasing it outside.
Absorption cooling uses a heat source (such as natural gas or waste heat) to drive the refrigeration cycle. It is commonly used in industrial settings where waste heat is available.
Air cooling involves blowing cool air across a surface or through a system to remove heat. This method is often used in HVAC systems and electronics cooling.
Liquid cooling circulates a cooled liquid (usually water or a glycol mixture) to absorb heat from hot surfaces, often used in data centers, high-performance computers and industrial machinery.
Types of coolers
Four common types of coolers are outlined below.
Air conditioners are used in residential, commercial and industrial spaces to provide a comfortable environment by lowering air temperature.
Chillers are used in industrial processes and HVAC systems to remove heat from a liquid, which is then circulated through heat exchangers to cool air or process fluids.
Refrigerators and freezers are designed to maintain low temperatures for food storage and preservation by using a refrigeration cycle.
Cooling towers remove heat from water by evaporative cooling (Figure 2), and are commonly used in power plants, refineries and manufacturing facilities.
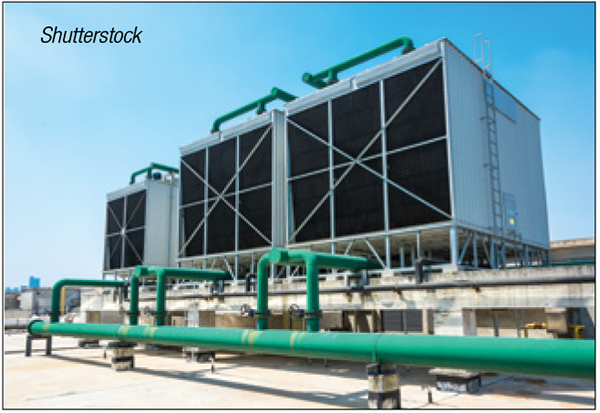
FIGURE 2. Cooling towers, like the one shown here, can remove heat from water by evaporative cooling
Applications of coolers
Coolers are critical for operations in the following areas.
Data centers. Heat exchangers maintain optimal temperatures for server operation and prevent overheating, ensuring consistent performance and preventing data loss.
Food storage and processing coolers ensure food safety and quality by keeping products at low temperatures to prevent spoilage.
Industrial processes. Coolers are used in metalworking, plastics and chemical manufacturing to remove heat generated during production.
HVAC systems provide comfort in residential and commercial buildings by controlling indoor temperatures.
Heaters
Heaters are designed to increase the temperature of a fluid, gas or room. They are used in a wide range of applications, from residential heating and hot water systems to industrial processes requiring precise temperature control.
Heaters work by converting electrical energy, fuel or steam into heat energy, which is then transferred to a target area or fluid. The method of heat generation varies depending on the type of heater. Four types are described below.
Electric heaters use electric resistance to generate heat. The electricity passes through a resistor, which converts electrical energy into heat. They are commonly used in home heating, water heating and industrial applications
Gas heaters burn natural gas, propane or other fuels to produce heat. They are efficient and commonly used in residential, commercial and industrial settings.
Steam heaters use steam generated from boilers to heat air or fluids. They are widely used in industrial processes and heating large buildings.
Infrared heaters use infrared radiation to directly heat objects and people in their path, often used in outdoor and spot heating applications.
Types of heaters
Short descriptions of the types of heaters are included here.
Space heaters are portable devices used to heat small areas, available in electric, gas, and infrared models.
Water heaters are designed to provide hot water for domestic or industrial use, including tankless, storage and solar-powered water heaters.
Industrial heaters include immersion heaters, strip heaters, band heaters and more, each designed for specific heating needs in industrial processes.
Furnaces are used to heat air in residential and commercial HVAC systems, often using natural gas, oil or electricity.
Applications for heaters
Heaters are essential in the following applications:
Residential heating units provide warmth and comfort in homes, including baseboard heaters, wall heaters and furnaces.
Water heating units are used in homes, businesses and industries for hot water supply, ranging from small electric heaters to large industrial boilers.
Industrial process heaters ensure optimal temperatures for chemical reactions, material processing, and product manufacturing.
Specialty applications heaters are used in de-icing, curing, drying and other processes where controlled heating is necessary.
Choosing the right equipment
Selecting the right equipment for your needs depends on several factors, including the purpose of the equipment, energy efficiency, application requirements and maintenance considerations. Here are six key considerations.
1. Purpose. Determine whether you need to heat, cool or transfer heat between fluids. This is the most critical factor, as it defines the type of equipment required.
2. Efficiency. Consider the energy efficiency of the equipment, as this impacts operational costs. Heat exchangers are often more energy-efficient for transferring heat, while heaters and coolers are designed for specific heating or cooling tasks.
3. Application requirements. Evaluate the specific needs of your application, such as the required temperature range, flowrates and environmental conditions. Different applications have unique requirements that will influence the choice of equipment.
4. Maintenance and durability. Consider the maintenance needs and durability of the equipment. High-maintenance equipment may have lower upfront costs but could lead to higher long-term expenses.
5. Space and design constraints. Factor in the physical space available for the equipment and any design constraints. Compact equipment like plate heat exchangers or smaller heaters might be necessary where space is limited.
6. Safety considerations. Ensure the equipment meets all relevant safety standards and regulations, especially in applications involving flammable or hazardous materials.
Thermal oxidizer examples
Thermal oxidizers operate by destroying chemical pollutants (VOCs/HAPs) at approximately 1,500°F. Thermal oxidizers themselves incorporate internal heat exchangers on various levels to promote highly efficient operation (air-to-air heat exchanger systems). However, there is opportunity to further process oxidizer exhaust heat for secondary applications.
An example comes from a regenerative thermal oxidizer (RTO) system to treat pentane emissions from foam processing (Figure 3). Hot air is emitted as part of the abatement process, at approximately 250–300°F, from the RTO. Utilizing air-to-air heat exchangers, fresh air can be heated to pre-condition combustion air for factory boiler burner systems. Fresh air can also be heated for product storage rooms (facilitate foam product cure). This saves energy in the process.
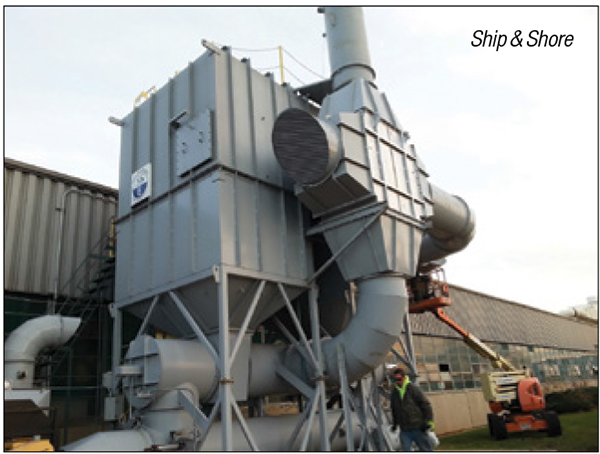
FIGURE 3. Regenerative thermal oxidizers destroy pollutants, and can also be used as a supply of heat for other applications
Condensing or cooling systems are also installed in the same facility to drive off moisture from the steam heavy exhaust of the individual foam processes. To effectively operate RTO abatement equipment, exhaust needs to be relatively moisture-free. Cold water (cooling tower operation) is utilized in plate-and-frame, and tube-and-shell type exchanger equipment to drive off water from the process exhaust to facilitate the abatement process. Recovered water can be used for cooling-tower and boiler-system makeup water.
Process heat recovery to heat loading dock areas is a more prevalent application of heat exchanger use (especially in northern climates). Energy from hot air or process fluids can be used to heat fresh air (air-to-air, fluid-to-air technology) to deliver back conditioned air into a manufacturing building. Systems can also be configured with winter/summer switch settings to introduce hot/cool conditioned air (utilizing condensing systems).
Other direct- and indirect-fired heating can be as simple as inline ductwork/pipework heaters, which are routinely used to keep process air and fluids hot or cold to satisfy process conditions.
Similar hot-air heat recovery can be used in virtually any curing operation to scavenge heat and re-introduce it into the production process. Printing, painting, coating curing operations of all types, can incorporate some type of energy exchange to fine-tune their operations, resulting in reduced energy operating costs. However, operators must be mindful of not introducing combustion byproducts (from natural-gas burners) as air makeup into operator areas for occupational safety and health reasons.
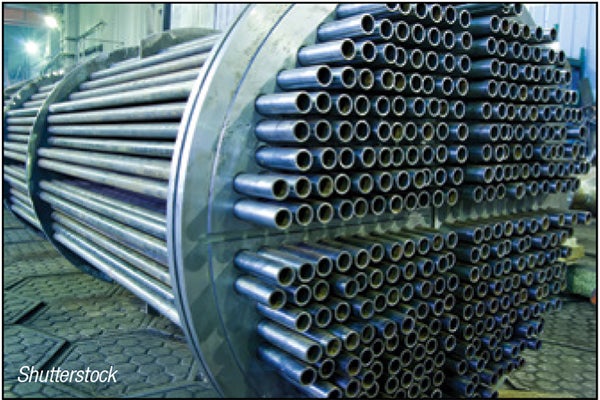
FIGURE 4. The interior of a shell-and-tube heat exchanger shows the tubes through which the process media flows
Concluding remarks
Understanding the differences between heat exchangers, coolers and heaters is vital for selecting the right solution for your thermal management needs. Heat exchangers offer versatility and energy efficiency, making them suitable for a wide range of applications, from power generation to food processing. Coolers are specialized for precise cooling tasks, essential in data centers, refrigeration and industrial cooling processes. Heaters provide dedicated heating solutions, ensuring optimal temperatures in residential, commercial, and industrial settings.
By carefully evaluating specific needs, application requirements and energy considerations, users can make informed decisions that optimize performance, enhance efficiency and ensure safety across all operational environments. Whether you need to heat, cool or simply transfer heat, there is a solution that fits your needs perfectly.
Edited by Scott Jenkins
Author
Anoosheh Oskouian is CEO of Ship & Shore Environmental, Inc. (2474 North Palm Drive, Signal Hill, CA 90755; Email: [email protected]; Phone: 562-997-0233). She spearheads innovative strategies to reduce industrial pollution and improve air quality globally. With a background in chemical engineering and a passion for sustainability, Oskouian is dedicated to advancing green technologies and advocating for environmental stewardship.