Industrial Ethernet protocols are the leading method for gathering smart instrument data and pending developments will allow improved implementation of this technique with two-wire instruments
The industrial internet of things (IIoT) uses smart instruments to enhance industrial processes through realtime analytics and requires the generation of massive amounts of big data, which are collected and stored in host systems for evaluation. Main sources of these data are the smart instruments installed throughout plants and facilities.
These instruments transmit basic process variables — along with extended data such as calibration parameters, diagnostics and other information — over digital networks. The data become valuable when analyzed by end users with the expertise to perform predictive maintenance, reduce downtime and make other operational improvements.
This description assumes every smart instrument is connected via a digital network, but in many instances the information present in the instruments is unavailable due to communication protocol limitations. Bridging the gap between smart instruments and data repositories is where industrial Ethernet protocols such as EtherNet/IP and Profinet enter the picture.
This data-gathering aspect of analytics is the focus of this article, which shows why industrial Ethernet protocols are so popular. It also explains why two-wire instruments with Power over Ethernet (PoE) are not yet available, and then discusses developments with two-wire instruments to enable connectivity.
Industrial Ethernet leads the way
Most end users prefer industrial Ethernet protocols over other traditional industrial fieldbus protocols for three main reasons:
- Ethernet protocols facilitate unification of an Ethernet infrastructure throughout a plant or facility
- Ethernet protocols provide extensive bandwidth, enabling access to more information at a faster speed
- Ethernet protocols support ease and economy of setup and use due to widespread familiarity with and availability of Ethernet
Will a plant be able to unify its operational technology (OT) and information technology (IT) networks using industrial Ethernet? Yes, but only with the proper network architecture. Smart switches or routers expressly designed to manage the information traffic from both networks are essential.
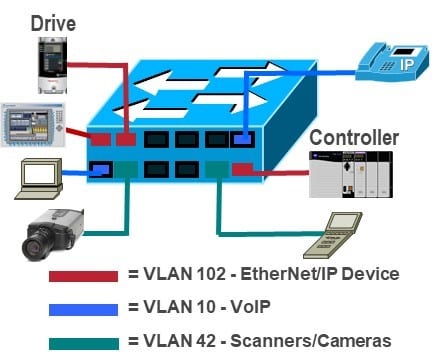
Figure 1. Ethernet switches can connect to a wide variety of industrial and commercial components
One example is the Stratix family of industrial managed Ethernet switches from Rockwell Automation. These switches separate office Ethernet TCP/IP traffic from industrial EtherNet/IP traffic by using freely assignable ports (Figure 1).
Ethernet TCP/IP is a common IT network protocol, and there are several industrial Ethernet OT network protocols. All these protocols follow the same OSI Layer Architecture model and comply with the IEEE802.3 communications specifications.
However, industrial Ethernet protocols modify the application layer. For example, with the EtherNet/IP protocol, the application layer in the OSI model is slightly different from IT protocols because it includes the common industrial protocol (CIP). CIP improves access to data used for control of network devices by separating it into implicit and explicit data packets, or messages (Figure 2).
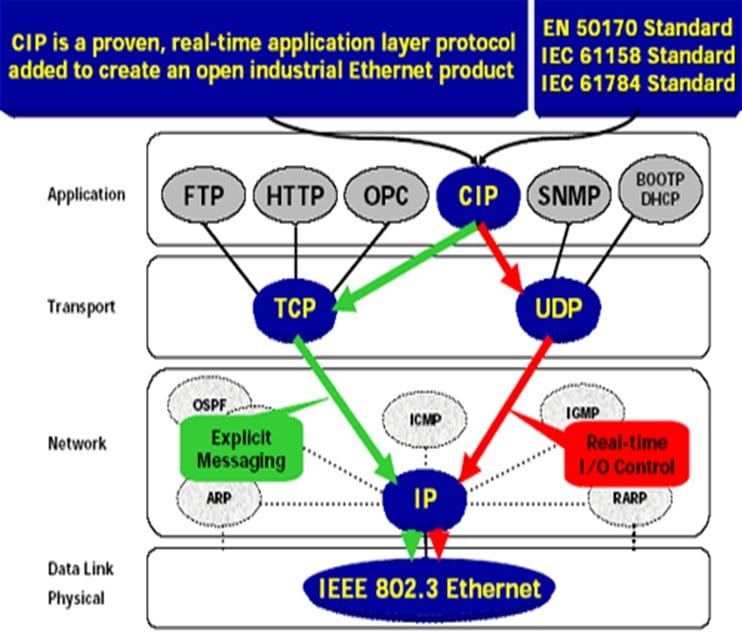
Figure 2. The common industrial protocol (CIP) improves access to data by separating packets into implicit and explicit messages
Explicit messages are for node-to-node communication and use transmission control protocol (TCP) delivery. They move large amounts of data, with variable payload sizes, only as needed. Implicit messages are for compact high-speed communication and use user datagram protocol (UDP) delivery. They are most commonly used for pre-configured high-speed input/output (I/O) messaging. EtherNet/IP adds this explicit or implicit distinction to the information packets to optimize performance for these types of transmitted data.
A standard IT Ethernet TCP/IP network communicates information upon request. Managing this traffic without negatively impacting the speed of the network or resulting in significant delays is relatively easy through the strategic use of the switches and routers commonly applied in IT networks.
However, OT industrial Ethernet networks are used for both I/O and control, with information broadcast continually. If a system is attempting to transmit both Ethernet TCP/IP and industrial Ethernet messages on the same network, it would quickly become overwhelmed and the speed would degrade to an unacceptable level.
Therefore, proper management of the available bandwidth through the use of special managed switches or routers is crucial. Routers can be used to segment networks, and managed switches can be used to manage traffic on each segment.
Plug and play: not yet
Industrial Ethernet protocols such as EtherNet/IP are very useful for transmitting large amounts of data quickly, making them a good fit for smart instruments. While an EtherNet/IP network is user friendly, it has not yet reached the same level of functionality most people have come to expect from a standard home or office Ethernet TCP/IP network.
Compared to the maturity of Ethernet TCP/IP, industrial Ethernet networks are still relatively young, meaning the critical mass necessary for the market to provide expected true “plug and play” functionality has not yet arrived.
If a plant has an EtherNet/IP network installed, the physical connection of four-wire smart instruments into the network is much like any other Ethernet device. The host system is also connected to this network and is capable of obtaining process data from the instruments. Hosts can include control systems, asset management systems, process historians and others.
Integration of smart instruments directly into a host system requires coordination among the smart instrument, the host system and the smart switches. For example, three main tools are needed to easily integrate smart instruments into a Rockwell Automation PlantPAx control system based on a ControlLogix hardware platform:
An Add On Profile (AOP) Level 3 is required data integration. AOPs are software packages loaded into the control system and have the following attributes:
- Specific to individual instruments
- Developed in coordination with the control system manufacturer
- Supplied to the end user or system integrator by the smart-instrument manufacturer
Add On Instructions (AOIs) are supplied as a pre-engineered function blocks, and each must be configured by the end user. AOIs are used to define data, arguments, parameters, algorithms and other functions required for processing data from the instruments.
Instrument faceplates and Global Objects are supplied to provide human-machine interface (HMI) visualization of instrument data, transparency of extended field instrument information and assistance with diagnostics. These are typically supplied by the control system manufacturer.
If multiple instruments from more than one instrument manufacturer are connected, then AOPs, AOIs and faceplate software will need to be loaded and configured for each type of smart instrument. In addition to the software requirements listed above, hardware connectivity considerations arise with two-wire instruments.
Connecting two-wire instruments with industrial Ethernet
Most users have heard of Power over Ethernet (PoE), and many question why manufacturers have not implemented this functionality into their smart two-wire instruments. A PoE standard exists in the form of IEEE802.3 AF/AT, and there are also commercially available switches on the market to manage and distribute PoE.
The main issue is that IEEE802.3 AF/AT compliant switches are rated for up to 52 V d.c. at 2.5 A. This relatively high level of power makes it very difficult to use these switches in the hazardous areas commonly found throughout process plants and facilities. This is true regardless of whether the installation is designed using an intrinsically safe or explosion-proof concept.
Therefore, only areas classified as non-hazardous are viable for PoE installations, but even here challenges exist. Per NEC500 (National Electrical Code), working on live energized parts operating with a voltage greater than or equal to 50 V is a safety issue and requires the use of personal protective equipment. In many instances, the benefits of PoE implemented in compliance with IEEE802.3 AF/AT simply do not provide sufficient value to justify the effort or expense required for design, installation and maintenance.
Addressing the two-wire instrument issue
The problem of not being able to directly use two-wire smart instruments in industrial Ethernet networks has been recognized. A consortium of organizations including FieldComm Group, ODVA, Profibus, Profinet International and manufacturers of process instrumentation and control systems have joined to build upon the work of the IEEE802.3cg Task Force. This consortium is referred to as the Ethernet Advanced Physical Layer (Ethernet-APL) group.
IEEE802.3cg (draft) is a physical layer specification and management parameter for 10 Mb/s operation and associated power delivery over a single balanced pair of conductors (Figure 3). Implementation of this draft will eventually make Industrial Ethernet protocols suitable for use in hazardous area locations.
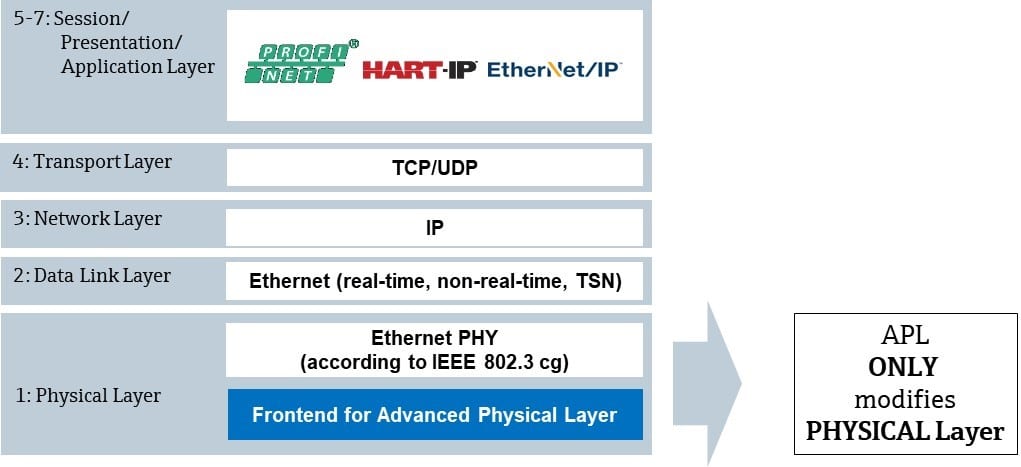
Figure 3. IEEE802.3cg (draft) is a physical layer specification and management parameter
Ethernet-APL is exactly what the name implies: a new physical architecture designed specifically for industrial Ethernet protocols (Figure 4). Ethernet-APL will not impact the protocol stack, so it will be suitable for use with Profinet, HART-IP or EtherNet/IP Industrial Ethernet protocols, and open their use to two-wire topologies.
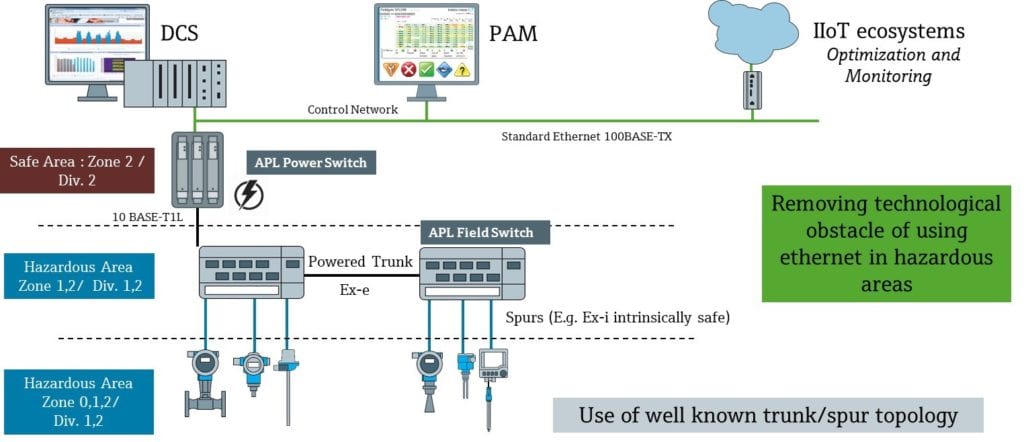
Figure 4. The advanced physical layer will allow two-wire instruments to directly connect to the industrial Ethernet
Together, Ethernet-APL and IEEE802.3cg (draft) will enable industrial Ethernet-based communication protocols for two-wire field instrumentation by doing the following:
- Allowing power and data to be carried on the same two-wire shielded cable
- Permitting installation in plant areas classified as hazardous
- Providing high bandwidth of 10 Mb/s
The work being conducted by the Ethernet-APL group and the IEEE802.3 cg Task Force is ongoing and expected to be finalized soon. Once this work is completed, instrument manufacturers and component suppliers can respond with the equipment necessary for a complete network.
Until this solution is available, the alternate method for integrating legacy two-wire instruments to an industrial Ethernet control system is through a gateway. While highly functional, this method does limit the data available from each instrument to typical primary or HART values. One example of a device with Industrial Ethernet gateway capability is shown in Figure 5.
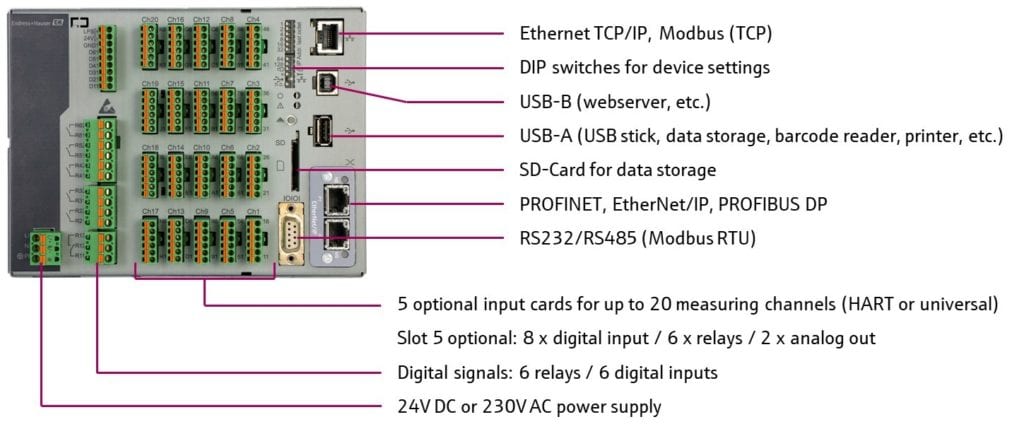
Figure 5. This industrial Ethernet gateway allows two-wire instruments to connect using the EtherNet/IP or Profinet protocol
Final words
Smart instruments are a vital component for process owners to implement IIoT strategies. However, users can only realize the full value of these devices and the subsequent potential of IIoT analytics when their systems can quickly and easily access the growing amount of available data.
Industrial Ethernet enables this digital transformation by providing simple and fast access to the required realtime instrument and process data. Today, four-wire instruments can easily connect to industrial Ethernet networks, and traditional two-wire instruments can be integrated with gateways.
In the future, two-wire instruments will be able to connect more directly as a result of Ethernet-APL and IEEE802.3cg (draft). This will enable improved operations through the use of analytics applied to data gathered using industrial Ethernet networks.
Edited by Dorothy Lozowski
Author
Keith Riley is a product business manager with Endress+Hauser (2350 Endress Place, Greenwood, IN 46143; Phone: 317-535-2169; Email: [email protected]), a position he has held since April 2008. Prior to this, he was a product manager and regional sales manager with L.J. Star Inc., as well as a product manager for Penberthy (Tyco Valves). Overall, he has over 20 years of sales, marketing and instrumentation experience in the process industries.