Removing solids from a stream of air or other gases is an important operation across virtually all sectors of the chemical process industries (CPI). In many cases, gas-solid separation is motivated by the need to reduce environmental impact and health hazards, as in removing particulate matter from exhaust gas. In solids-processing operations, such as milling, grinding, packaging and others, it is often necessary to remove dust from air to recover product or protect equipment. This one-page reference focuses on one type of gas-solid separator: the cyclone.
Operating principles
A cyclone works on the principle of inertial separation. A stream of dust-laden air or gas is introduced tangentially to the top of a vertically oriented, cylindrical collection chamber with a conical, tapered end at the bottom. The manner by which the gas enters the chamber creates a helical airflow pattern, where the gas rotates down the chamber toward the tapered bottom (Figure 1). The swirling motion of the gas has two components — a downward-directed spiral movement for the outer stream, and a rotating, upward-moving inner stream.
Due to their greater mass, solid particles contained in the gas stream are pushed outward due to the centrifugal force that results from the rotating airflow. Since they have too much inertia to follow the path of the gas stream, particles are pushed against the interior wall of the cyclone cylinder and fall downward toward a collection device fitted at the bottom of the cyclone. The solid particles often exit the bottom through a spring-loaded flap valve or a rotary valve. Meanwhile, the solids-free gas rotates upward toward the gas outlet at the top of the chamber.
In addition to air-pollution control and dust-control applications, cyclones also serve other purposes in CPI applications. These include the recovery and recycling of catalysts in petroleum refineries, the recovery of freeze-dried coffee in food processing plants, and for capturing sawdust in a lumber mill, among others.
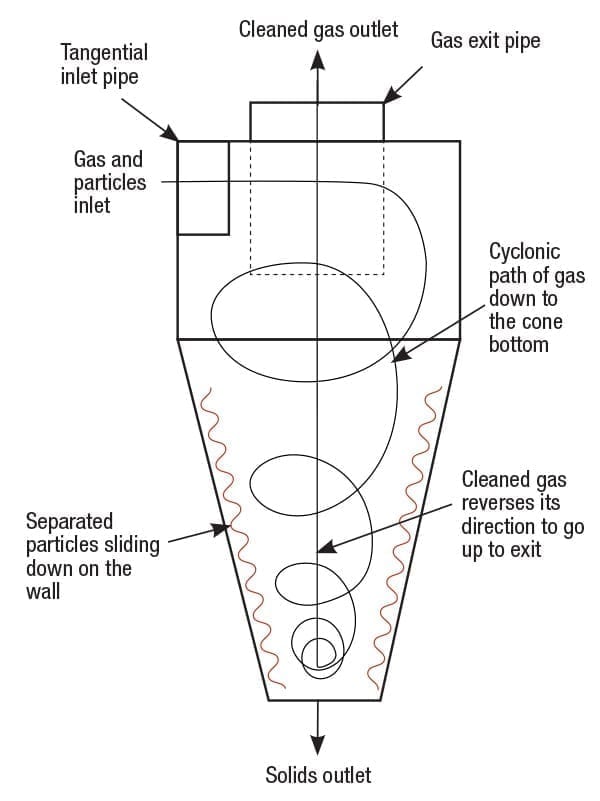
Figure 1. Cyclones have no moving parts, so the capital costs and maintenance costs are relatively low compared to other gas-solid separation approaches
Advantages and limitations
Among the reasons that the use of cyclones is so widespread are that they have no moving parts, can withstand high-temperature gases and harsh operating conditions, and are relatively inexpensive in terms of capital costs. Because of this, in air-pollution-control applications, cyclones are often used as a pre-treatment step that is followed by an electrostatic precipitator or a filter. The limitations of a cyclone can include low collection efficiencies for small particles, and relatively high operating costs due to the power required to overcome a large pressure drop. Cyclones are commonly used to separate particles greater than 5µm in size.
Standard dimensions
Standard configurations of industrial cyclones for particulate collection and removal are available as a result of empirical measurements compiled over time. All dimensions are related to the body diameter of the cyclone so that the results can be applied generally. For example, classic research suggests that the height of the inlet for a conventional cyclone is half of the body diameter and the length of the chamber is twice the diameter. Further, the length of the cone is twice the diameter and the dust outlet is one quarter of the diameter. Other important dimensions include the cleaned-gas outlet (0.5 × dia.) and the width of the dirty-gas inlet (0.25 × dia.).
Separation efficiency varies greatly depending on the particle-size distribution of the solids contained in the gas, and the cyclone geometry. Cyclones are often grouped into three categorires: high-efficiency, conventional and high throughput. Standardized dimensions have been developed for each category. In general, operating costs increase with efficiency (higher efficiency requires higher inflow pressure). A small-diameter cyclone generates greater centrifugal force than a larger-diameter device.
Design considerations
Properly designed cyclones can remove nearly every particle in the 20- to 30-µm range. Typical cyclone separators have efficiencies of 70–90%. Gas inlet velocities should be in the range of 100 to 150 ft/s, but may be limited by re-entrainment of dust particles or by unacceptable pressure drop. At the tapered end of the chamber, where the gases reverse their direction of travel, higher gas velocities are experienced, and this can re-entrain finer dust particles (reducing separation efficiency). To avoid this, cyclone design and operation should seek to prevent solids from accumulating in the cone region.
References
1. Coupler, J.R., Penney, W.R., Fair, J.R. and Walas, S.M. “Chemical Process Equipment: Selection and Design” 2nd ed., Gulf Professional Publishing, Burlington, Mass., 2005.
2. Cushman-Roisin, B., Gaseous Emissions-Control Technologies, Environmental Engineering Course Materials, Dartmouth University Thayer School of Engineering, 2019.