Onsite recovery conserves one of the most precious resources — water. A well-engineered, closed-loop recycling system can pay dividends in avoided costs to treat and discharge wastewater
In Southern California, few businesses dispute the need for water conservation. In a naturally arid region that is also a center of industry, it is clear that every drop of water used in industrial processes comes at a cost — to the environment, as well as to the bottom line. In short, all incentives align in favor of responsible reuse. In light of these facts, closed-loop water-recycling systems can offer a cost-effective alternative to one-time water use for industrial processes. Such systems can be designed for specific process needs, and in many cases, can provide 95% or greater water recovery.
Designing the recycling system
In 2017, a manufacturer in the aerospace sector sought a way to reduce costs and wastewater at a site located in Southern California. To rinse metal parts as they are cleaned, etched and electrolytically plated with specialized metal finishes, the company’s operations require a high volume of deionized (DI) water. They therefore also produce a high volume of metals-bearing wastewater. A majority of this volume consists of rinses that can be closed-loop recycled by ion exchange in a cost-effective manner. The remainder requires specialized treatment to remove cyanide and heavy metals before discharge to sewer.
During its decades in operation before the installation of a new rinsewater recycling system, the business sourced all its water from the Metropolitan Water District of Southern California, using portable exchange deionization (PEDI) vessels to produce a limited volume of DI water, at a cost of approximately $70–80 per 1,000 gal. Given this high cost, the manufacturer only used DI water for critical process rinses. And at the end of the manufacturing process, 100% of the wastewater was discharged to the Orange County Sanitation District, after expensive chemical treatment to comply with regulatory discharge limits.
When the company decided to enlarge its metal-plating operation, they worked with Water Innovations, Inc. (San Diego, Calif.; www.waterinnovations.net) to develop an onsite system for rinsewater recycling. Utilizing a wide array of measurement and control instruments, sensors and valves supplied by GF Piping Systems (Irvine, Calif.; www.gfps.com), the HFX75d system engineered by Water Innovations (Figure 1) selectively recycles wastewater to maximize closed-loop recovery of usable water.
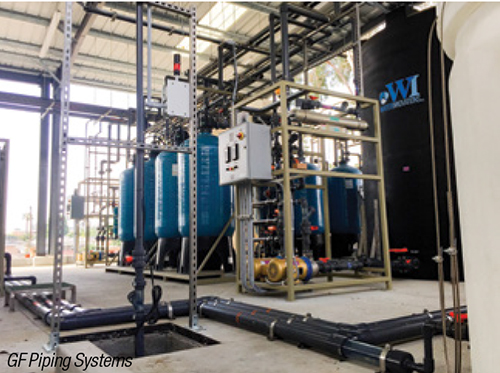
FIGURE 1. Water Innovations’ HFX75d recycling system, supported by process-automation technologies from GF Piping Systems, reduced wastewater management costs for an aerospace manufacturer by 80%
As described by Water Innovations managing partner Steven Ward: “This recycling is achieved through the use of three different resin systems: one that recycles up to 75 gal/min of select compatible rinses; one for oxidation and removal of cyanide from precious-metal plating rinses; and a polishing system with a series of specialized PEDI vessels to remove residual regulated heavy metals and cyanide from the remaining effluent prior to discharge to sewer.” Water Innovations also developed a proprietary bentonite reactant-treatment system that would allow onsite treatment of a high-volume, oily wastewater stream. In total, the volume of wastewater requiring chemical treatment before discharge has been reduced by over 60%.
Water recycling gets results
With the new system providing an abundant supply of DI water (and with the cost per gallon reduced by about 70%), the aerospace company has been able to expand the use of the system to a wider range of rinse processes, with a positive impact on product quality. Meanwhile, compared with the process of purchasing water, using it once, waste-treating and discharging to sewer, the business’ investment in closed-loop rinsewater recycling with segregated waste treatment has brought down their overall wastewater-management cost by approximately 80%, the company says. The recycling process produces DI water at a cost of $5–6 per 1,000 gal — a significant improvement over their previous cost of $70–80 for PEDI purification of potable water. Given that disposal expenditures were greatly reduced as well, the company achieved return on its Water Innovations investment in approximately two years. As of November 2022, assuming HFX75d operation at 75 gal/min, for around 100 h per week, since startup in March 2017, this aerospace supplier had recycled (and therefore avoided discharging to the publicly owned treatment works) an estimated 120 million gal of water.
For nearly two decades, Water Innovations’ water recycling and wastewater treatment systems have been engineered and manufactured exclusively with GF Piping Systems’ components (Figure 2). Critical GF components provided for the HFX75d system include: 2850 conductivity sensors, 2750 pH sensors, and 2580 flow sensors; Type 523 metering valves, which regulate the HFX75d regeneration cycles; Type 233, 285 and 288 air-actuated valves, which regulate the duplex systems that alternate between service and regeneration cycles; 582 pressure-reducing valves; 586 pressure-retaining valves; and 514 diaphragm valves, which autonomously maintain constant pressure for the blending and injection of the resin-regeneration chemistry.
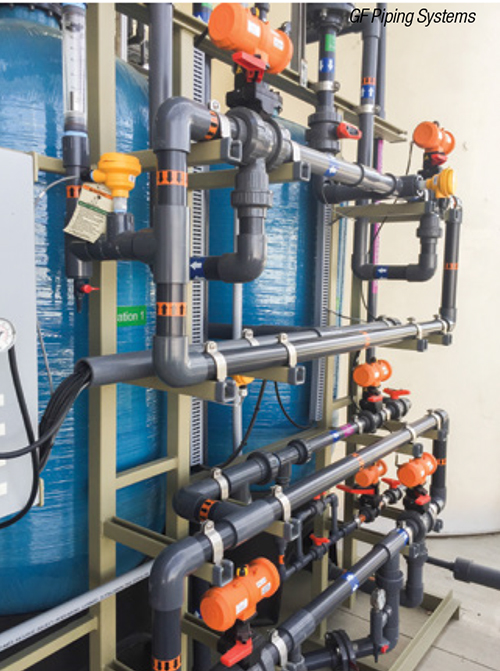
FIGURE 2. Specification of the proper components
— from pH sensors to pressure-reducing valves
— was critical to ensuring the success of the water-recycling system
As described by Ward, the results of this approach are a “win-win-win” for Water Innovations, their suppliers and their customers — as well as for a world where water scarcity is a growing concern. To operate its Orange County facility, the aerospace company needed high-quality water for rinsing and a reliable process for regulatory compliance, both at costs it could afford. The HFX75d recycling system from Water Innovations makes it possible for the business to achieve both goals. With the company’s need to draw on the finite public water supply drastically reduced, Orange County officials have reason to smile as well. Ward commented proudly: “Having been recycling water for 20 years, or literally hundreds of millions of gallons of water that have been reused by our customers — I think that’s really the epitome of sustainability.” For a business squarely founded on “leaving things cleaner than you found them,” this claim seems well justified.
Edited by Mary Page Bailey
Author
Rick Hines is the director of automation for GF Piping Systems’ U.S. Center of Excellence (9271 Jeronimo Rd., Irvine, CA 92618; Email: rick.hines@georgfischer.com). With over four decades of experience in the field of fluid handling, Hines is active in the effort to provide safe, clean and reliable water supplies to communities.